Что такое фрезер и как его выбрать
Учимся «читать этикетку»: на какие опции и характеристики стоит обратить внимание при выборе фрезера? А какие особо не влияют на потребительские характеристики прибора.
На фото:
Мощность и классы
Легкие, «средние» и тяжелые фрезеры. Мощность двигателя не является критерием добротности фрезера. Есть модели, которые находятся на хорошем счету у профессионалов, несмотря на скромные ватты. Можно выделить три класса вертикальных фрезеров:
- до 1100 Вт. Такой фрезер сравнительно компактен, весит немного. Однако и высокой стойкостью к нагрузке не отличается. Большое усилие подачи к такому фрезеру лучше не прикладывать.
- 1200 — 1700 Вт — средний класс.
- 1800 — 2300 Вт. Что такое фрезер со столь мощным мотором? Это тяжелая габаритная и очень производительная машина, которая легко переносит нагрузку и уверенно справляется со съемом толстого слоя материала.
Диаметр цанги
6, 8 или 12 мм. Цанга — это втулка, в которую вставляется хвостовик фрезы. Иными словами, диаметр цанги определяет диаметр подходящего хвостовика. Наиболее распространены 8-миллиметровые цанги. Ими комплектуются фрезеры различных классов. Стандарт «6 мм» можно увидеть у машин невысокой мощности, а 12-миллиметровая цанга, наоборот, встречаются у мощных тяжелых фрезеров. Нередко в комплекте есть две или три цанги разного диаметра.
На фото: фрезер DW615 компании Black and DeWALT.
Ход фрезы
От 40 до 80 мм в зависимости от модели. Эта характеристика показывает, насколько опускается фреза при максимальном ходе «головы» вниз.
Регулировка скорости
Одна из важнейших опций. Максимальные обороты фрезеру нужны в редких случаях. При чрезмерной частоте вращения фреза перегревается и прижигает заготовку (иногда этот процесс сопровождается дымом). Есть правило: чем больше диаметр оснастки, тем меньше должна быть скорость.
Подсветка
Для хорошего обзора. При фрезеровании нередко возникают ситуации, когда обзор рабочей области затруднен. Это не страшно, если вы ведете машину по упору от края до края. Но нередко нужно контролировать продвижение фрезы, чтобы не снять лишнего. Здесь-то и выручает подсветка, которая обеспечивает прекрасный обзор линии.
Микролифт
Тонкая настройка глубины. Множество фрезеров оснащены дополнительным винтовым механизмом для регулировки глубины с точностью 0,1 мм. Стандартную настройку с ограничительным штифтом называют грубой, так как погрешности у нее довольно велики. Микролифт же пригодится там, где важно задать глубину очень точно, и к тому же он позволяет добавить необходимые доли миллиметра.
Параллельный упор
На фото: фрезер MF 1400 KE компании AEG.
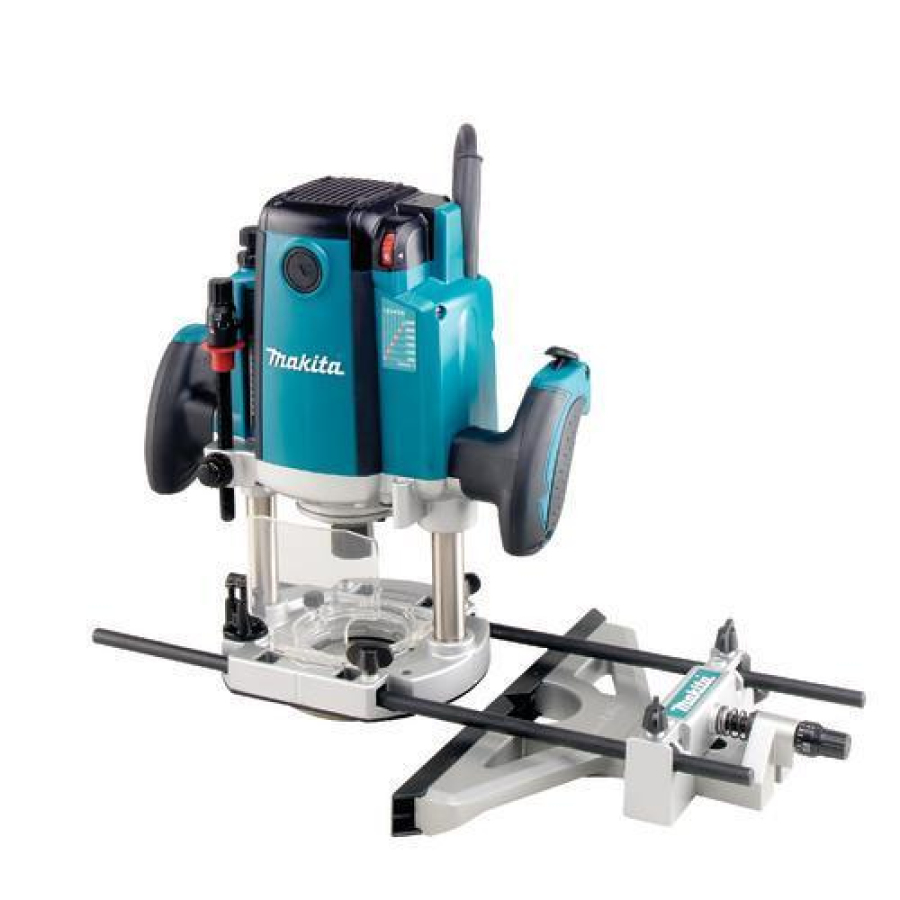
Литой или штампованный. Считается, что первый вариант предпочтительнее, так как от упора требуется хорошая жесткость (если ее нет, ждите неточностей в работе). Впрочем, иногда жесткостью отличается и штампованный упор. Проверяют так: при значительном боковом усилии на фрезер добротный упор не станет «играть» и не даст машине сместиться в сторону. Стоит добавить, что у дорогих моделей упор оснащают механизмом тонкой настройки отступа от края (наподобие микролифта) и регулируемыми башмачками. Такие усовершенствования не помешают, ведь фрезер это инструмент для точной работы.
Советы при выборе
Добротная конструкция — очень жесткая. В ней нет места люфтам и перекосам, которые негативно сказываются на точности. Осматривая понравившуюся модель, попробуйте покачать и перекосить ее «голову» неравномерными усилиями на рукоятках. Люфт или проседание хотя бы по одной из стоек — плохие признаки. Опускаться «голова» должна плавно, без рывков и чрезмерных усилий с вашей стороны.
В статье использованы изображения: blackanddecker.ru, dewalt.ru, aeg-powertools.ru
что это? Какие виды бывают и как правильно выбрать
Главная — Статьи — Фрезер — что это? Какие виды бывают и как правильно выбрать Фрезер как деревообрабатывающий электроинструмент имеется практически у каждого столяра, ведь с помощью этого оборудования можно легко вырезать пазы, производить фигурную обработку кромок и просверливать отверстия. При этом работать фрезерной машиной можно не только с чистым древесным массивом, но и с пластиком, металлом, древесностружечными, древесноволокнистыми плитами и другими материалами. Выбор любого инструмента, как правило, начинается с определения его назначения и выявления активности использования, поэтому и при выборе фрезера, изначально следует определиться с типом тех работ, в которых будет использоваться этот электроинструмент.
Типы
Фрезеры подразделяются на оборудование вертикального, кромочного, комбинированного и специального типа. Вертикальный инструмент он же погружной фрезер является универсальным оборудованием и применяется для любых видов фрезерования. Фрезерная машина кромочного или иначе окантовочного вида предназначена лишь для обработки кромок материалов. Комбинированное оборудование имеет специальный вид исполнения в него входит сразу две базы одна для снятия кромок, а вторая для погружного фрезерования.
Специальные фрезеры различаются на присадочный инструмент для выборки пазов и отверстий под дюбели, на ламельный инструмент для произведения лишь узких пазов и на триммер-оборудование рассчитанное на обработку ламината. Прежде всего, нужно определиться с назначением фрезера, ведь если он будет использоваться только для произведения каких-либо конкретных работ, совсем необязательно переплачивать и покупать оборудование универсального класса.
Технические характеристики фрезера
Фрезеры различаются по мощности, что может составлять от 600 до 2300 ватт, конечно, чем больше мощность инструмента, тем лучше, но тем он и тяжелее, поэтому работать навесу с таким оборудованием становится довольно сложно.
Также фрезерные машины классифицируются по скорости вращения шпинделя, она может составлять от 8000 до 34000 оборотов в минуту, это значение в большей мере определяется типом инструмента и его мощностью. Данное оборудование различается и по диаметру хвостовика фрезы, выбор этой характеристики, безусловно, зависит от назначения самого инструмента. Технические характеристики фрезера должны быть пропорциональны условиям, типам или иначе спецификой тех работ, которые планируется выполнять этим оборудованием, при возникновении же затруднений выбора разумнее проконсультироваться у столяров. Однако, несмотря на специфические отличия различных моделей фрезерных машин нужно уделить внимание и их общим характеристикам, так, желательно чтобы фрезер имел переключатель скорости вращения, блокиратор включателя и удобный пылевой шлюз, ведь при наличии данных функций работать фрезером будет намного удобнее.
Фрезер. Виды и устройство. Работа и применение. Как выбрать
При обработке древесины одним из самых полезных инструментов является ручной фрезер. Он применяется для широкого перечня задач, на выполнение которых вручную требуется много времени, сил и высокий уровень мастерства.
Устройство представляет собой электрический инструмент, состоящий из мотора установленного на подставку. На вал двигателя закреплена цанга для фиксации фрез и сверл. Конструкция подставки позволяет устанавливать станок на обрабатываемую поверхность под прямым углом к фрезе. При этом механизм дает возможность втягивать или выдвигать вращающиеся головку фрезы, тем самым обеспечивая регулировку глубины обработки древесины.
Инструмент применяется для выполнения следующих задач:
- Профилирование кромки доски.
- Выборка гнезд для фурнитуры.
- Выборка четверти.
- Нарезка шипов.
- Сверление отверстий.
- Обрезка.
- Гравировка и резьба по дереву.
- Подготовка пазов и шлицов.
Данное оборудование заменяет большой набор ручных инструментов, таких как рубанок, стамески, коловорот, пила и пр. Конечно, фрезер нельзя считать универсальным для любых задач, но с его помощью можно сделать действительно многое. Его по праву можно назвать инструментом, который при комплектации мастерской плотника или столяра, должен покупаться в первую очередь наряду с циркулярной пилой и электрорубанком.
По своей конструкции ручные фрезеры бывают трех видов:
- Верхний.
- Кромочный.
- Ламельный.
Верхние фрезеры устанавливаются над заготовкой. В их центральной части фиксируется вращающаяся фреза, что существенно облегчает удержание инструмента во время работы. Такое оборудование выбирают как новички, так и профессионалы. Оно считается самым универсальным для выполнения широкого спектра задач. Прибор может быть неподвижным или погружным. Если устройство погружное, то можно поднимать вращающуюся фрезу не отрывая подошву от обрабатываемой детали.
Кромочные фрезеры очень удобные для обработки кромок и снятия фасок. Такие инструменты гораздо легче верхних, поэтому для выполнения узконаправленных задач они существенно удобнее. Нужно отметить, что кромочный инструмент в основном применяется профессиональными плотниками для ускорения работы, поэтому в домашней мастерской он будет лишним, тем более что для нечастых задач вполне сгодится и более универсальный верхний фрезер.
Фрезеры для ламелей еще более редко применяемые. С их помощью осуществляется изготовление пазов и замков, которые обычно можно встретить на вагонке или напольных покрытиях. Такой инструмент является узкоспециализированным. С ним работать довольно удобно и быстро, но покупать такое оборудование для нечастого применения нецелесообразно. Эффективной заменой ламельных фрезеров могут стать верхние, установленные на фрезеровочный стол. При закреплении на столе упора, и двойном прохождении заготовки, можно сделать замок такого же качества, хотя и затратив больше времени.
Ключевые параметры при выбореПредлагаемые производителями фрезеры отличается не только по конструкции, но и по габаритам. Встречается оборудование весом от 2 до 6 и более килограмм. Легкие применяются для выполнения несложных задач. Они останавливаются при заглублении в твердую породу дерева, поэтому их обычно избегают. Тяжелые профессиональные фрезеры имеют массивный корпус и мощный электродвигатель, поэтому могут справиться с любой древесиной и крупными фрезами.
При выборе фрезера следует обращать внимание на следующие характеристики:
- Мощность.
- Скорость вращения.
- Тип цанги.
- Конструкцию подошвы.
Производительность фрезера напрямую зависит от его мощности. Оптимальными по мощности считаются приборы от 750 до 1500 Вт. Вес таких инструментом в среднем составляет около 4 кг. Бюджетные модели, мощностью до 750 Вт вполне пригодны для работы с мягкими породами древесины и гипсокартоном, но зачастую их производительность недостаточна. Слабые фрезеры часто останавливаются, особенно при резком изменении структуры волокон древесины, что бывает при обработке сучков. Тяжелые профессиональные фрезеры, мощностью свыше 2000 Вт, весят действительно много, поэтому такой инструмент сложно назвать ручным. Зачастую его мощность избыточна, поэтому если не заниматься обработкой дерева профессионально, то покупка столь функционального оборудования будет неоправданной растратой.
Выбирая фрезер следует обратить внимание на его скорость. Чем выше частота вращения фрезы, тем чище обрабатываемая поверхность. Присутствующее на рынке оборудование обычно имеет скорость от 7 до 24 тыс. оборотов в минуту. Стоит учитывать, что для очень быстрых фрезеров требуются специальные дорогостоящие фрезы, поскольку обычные не выдерживают столь интенсивной нагрузки. Также скоростные аппараты более шумные. Издаваемый ими звук при обработке древесины часто похож на свист, что сильно мешает и раздражает.
Подбирая фрезер стоит обратить внимание и на используемый тип цанги. Лучшими считаются конусные. При этом желательно чтобы цанга была сделана из закаленной стали. Данная часть фрезера является легко сменяемой. При желании всегда можно установить другую более прочную. Если пользоваться некачественной цангой, то уровень безопасности при работе фрезером снижается.
Для упора фрезера в обрабатываемую заготовку используется подошва. Она бывает литой и штампованной. Литые подошвы являются лучшими, поскольку обладают более ровными пропорциями. Кроме этого они не так подвержены деформации как штампованные. На бюджетных моделях, а также на большей части фрезеров среднего ценового сегмента, устанавливаются штампованные подошвы.
Параметры, влияющие на удобство работыПри покупке фрезера следует учитывать, что удобство его использования зависит не только от качества изготовления и мощности установленного мотора, но и возможности проведения некоторых настроек.
В связи с этим следует обратить внимание на следующие параметры:
- Рабочий ход фрезы.
- Наличие плавного пуска.
- Автоматическую защиту от перегрузок.
- Наличие параллельных упоров.
- Возможность подключения к пылесосу.
Рабочий ход фрезы является ключевым параметром при выборе. Именно от его показателя зависит глубина возможной выборки в древесине. Самые слабые модели обычно способны углубиться в заготовку на глубину от 20 до 50 мм. У профессиональных этот показатель доходит до 80 мм и выше. Глубина обработки регулируется специальным механизмом на корпусе фрезера или на его упоре, в зависимости от конструкции. Чем точнее шкала регулировки, тем лучше. Самыми удобными в использовании считаются фрезеры с делением настройки в 0,1 мм.
Более дорогие модели фрезеров оснащаются системой плавного пуска. Она позволяет электродвигателю набирать обороты медленнее. Это снижает динамическую нагрузку на отдельные узлы инструмента, что существенно увеличивает срок его эксплуатации. Также немаловажным дополнением является защита от перегрузок. Это предотвратит замыкание электрической части в случае скачков напряжения или при перегреве.
Важным параметром является и наличие дополнительных приспособлений, которые входят в комплект фрезера. В первую очередь это касается параллельного упора. С его помощью можно проводить идеально ровную выборку параллельно одной из сторон деталей. В более дорогих моделях в комплект кроме упора может входить и копировальная втулка. Она позволяет делать выборку путем копирования контура вырезанного заранее шаблона.
Также немаловажным является наличие патрубка для подключения к пылесосу. Хотя такое расширение и является довольно востребованным, патрубок есть далеко не на всех фрезерах, поэтому перед покупкой следует уточнить данный момент. Благодаря его наличию можно подключить пылесос с циклоном для отвода стружки, что обеспечит чистоту в мастерской и минимальное запыление воздуха.
Усовершенствование фрезераРучной фрезер универсальный инструмент для выполнения десятков различных задач, но он имеет и недостаток – это довольно тяжелое оборудование. При работе с ним быстро появляется усталость. Кроме этого, для того чтобы обрабатывать мелкие детали их необходимо фиксировать на столе с помощью струбцин, а также применять различные направляющие. Для решения данных проблем многие владельцы этого инструмента проводят его модернизацию, которая не влияет на целостность самого фрезера. Распространенным решением является закрепление фрезера на стол. Он прикручивается болтами к нижней стороне столешницы. При этом его фреза выводится на внешнюю часть стола, сквозь заранее подготовленное отверстие. Таким образом, инструмент можно переделать во фрезерный станок.
С помощью станка можно легко и быстро обрабатывать кромку досок, сделать соединение шип-паз, а также выполнять прочие задачи. Продуктивность при этом возрастет в разы, поскольку в таком положении проводится движение заготовки на фрезу, а не наоборот. После окончания работы фрезер можно снять и продолжить использовать его как ручной инструмент.
Похожие темы:
Что такое фрезер?
Ручной фрезер – электроинструмент, предназначение которого во фрезеровании пазов, снятии фасок, фрезерования отверстий.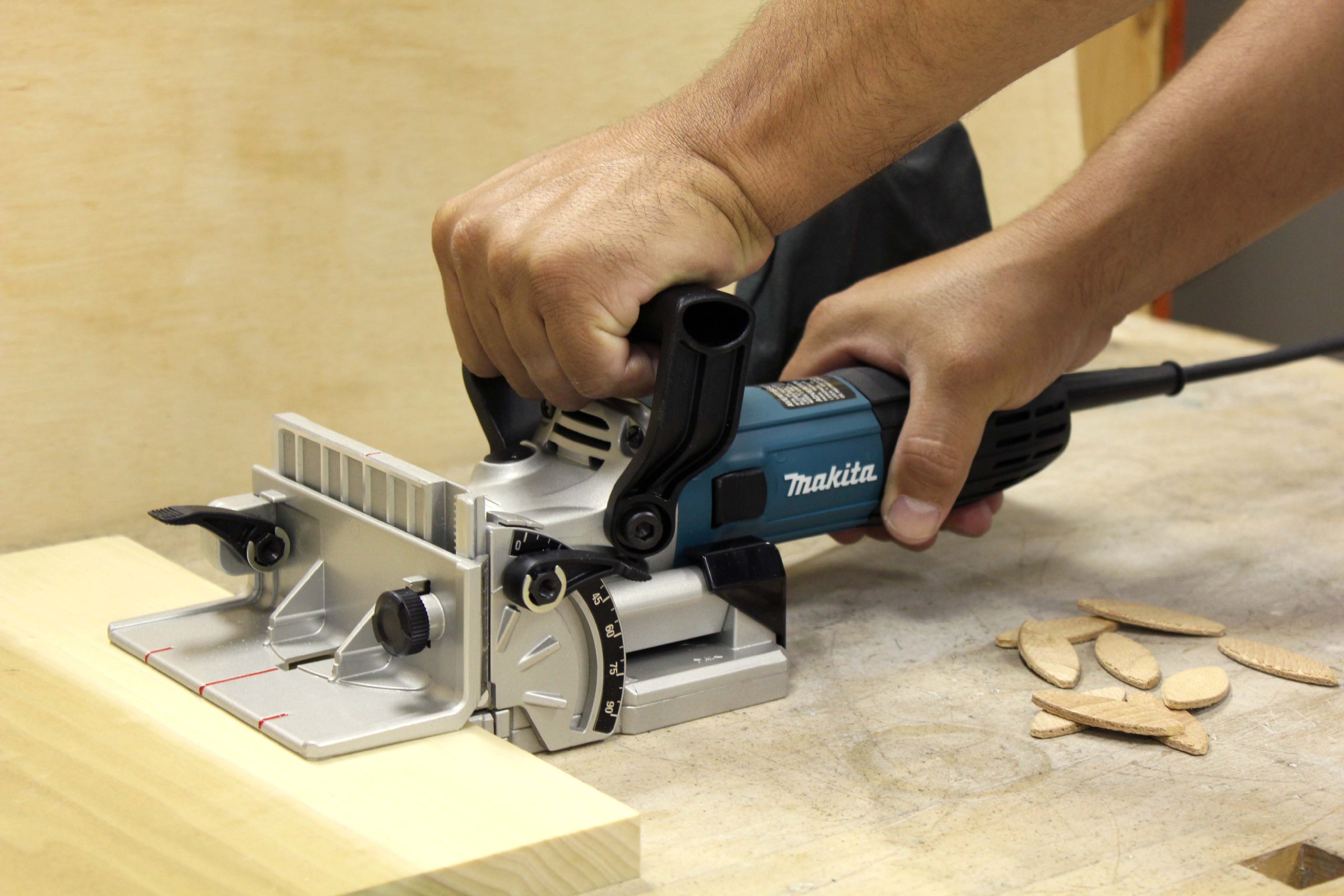
Подчеркнем при этом, что в таких случаях нужна определенная оснастка и определенный режим обработки.
Не нужно думать, что это просто деревообрабатывающий станок. Даже чисто внешне они отличаются. И принципиальное отличие в том, что этот инструмент не делает ставку на свою силу. Его преимущество – в скорости.
При обработке древесины используется фреза. Это рабочая единица фрезера, которая может быть разных видов. В зависимости от того, какая древесина попадет под обработку, будет применяться и соответствующая фреза.
В каких случаях мастер использует фрезер?
Когда необходимо вырезать паз, желоб или когда необходимо сделать ровным край заготовки; когда необходимо вырезать на нем фигурный профиль.
Можно еще перечислить немало операций, которые под силу этому электроинструменту. И все потому, что он является инструментом многофункциональным. О нем обязательно вспоминают, когда заходит речь про фрезерование отверстий, торцов, пазов.
Виды фрезеров
В настоящее время существует три вида фрезеров: верхний, кромочный, ламельный.
Верхний фрезер считается самым универсальным. Ведь ему под силу самые разные фрезеровальные работы. Верхний фрезер принято делить еще на два вида: погружной и неподвижный.
У погружного фрезера двигатель с фрезой перемещается вверх и вниз. Для этого у него две направляющие. Корпус двигателя опирается на пружины. Именно за счет этих пружин и можно вертикально опустить фрезу, которая вращается, в деталь, которая предназначена для обработки.
У неподвижных фрезеров корпус двигателя установлен жестко. И чтобы настроить глубину погружения фрезы, его необходимо передвигать вверх или вниз. Фреза выступает за плоскость базы.
Когда фрезеруешь канты обрабатываемой детали, то это не создает проблемы. А вот начало и завершение фрезерования замкнутого паза может стать проблематичным. В этом случае иногда нужно опускать и поднимать фрезер целиком и при этом не останавливать вращение рабочего инструмента.
Предназначение кромочного фрезера в обработке кромок, и потому такой вид фрезера считается инструментом узкой специализации. Предназначение ламельного фрезера в изготовлении пазов на торце изделия. У этого вида фрезера тоже узкая специализация.
Ручной фрезер: основные технологические операции — Proderevo.net
Такой инструмент состоит из двух частей: верхней, куда входят мотор, рукоятки, цанговый зажим, фиксаторы вертикального положения, и нижней — со штангами, опорной подошвой и револьверным упором. Машины этой разновидности отличаются тем, что позволяют погружаться в обрабатываемый материал на требуемую (в пределах возможностей) глубину. На примерах конкретных операций рассмотрим важные особенности конструкций современных устройств данного типа.
Готовимся к работе
1. Фрезу зажимают в цангу, пользуясь рожковым ключом и механизмом блокировки вала. Если последнего не предусмотрено, понадобится второй ключ. В данном случае установка упрощена донельзя — стопор снабжен переключаемой (отворачивание/ заворачивание) «трещоткой». Фрезу зажимают, руководствуясь разметкой на ней или исходя из общего правила (2/3-3/4 длины хвостовика).Начнем с азов — подготовки к работе. В зависимости от материала и задачи выбирают фрезу. Для мягких пород древесины, фанеры, МДФ применяют насадку с ножами из быстрорежущей стали (HSS), не возбраняется и более дорогая, точная и стойкая, с твердосплавными лезвиями (HM). В остальных случаях — ДСП, древесина твердых пород, композитные составы — использование HM обязательно. Как уже упоминалось, одна из важнейших особенностей твердосплавных лезвий — точность: они оставляют более чистую поверхность.
2. «Голову» инструмента опускают до упора фрезой в поверхность, после чего ее удобно фиксировать. Далее, исходя из вылета режущей оснастки и желаемой глубины обработки, выбирают самую низкую из подходящих «ножек» револьверного упора. Это позволяет проходить заготовки в несколько приемов, не повторяя точных регулировок. Зачастую положение каждой «ножки» можно подстроить в небольших пределах. На выбранную «подставку» опус кают опорную штангу, предварительно отпустив ее зажим. Не фиксируя ее, а лишь прижимая пальцем, перемещают по ней подвижный указатель, добиваясь его совпадения с нулем мерной линейки.В зависимости от диаметра фрезы и материала устанавливают частоту вращения. Поскольку регулировочное колесико обычно маркируют в условных единицах, придется воспользоваться инструкцией, где указывают, когда что нужно выставлять. Вообще говоря, настройка оборотов — очень ответственная процедура. Во-первых, оснастка большого диаметра может не выдержать слишком высокую скорость, во-вторых, важно подобрать режим. При завышенной частоте есть риск «прижечь» заготовку, при заниженной — падает производительность и ухудшается качество обработки.
3. Штангу поднимают до совпадения указателя с требуемым делением измерительной шкалы и зажимают ее фиксатором.Определившись с оборотами и типом фрезы, устанавливают оснастку. Сделать это верно помогут риски на хвостовике — ориентироваться нужно на них. Если требуется отступить от предписания (или его попросту не оказалось), пользуются простым правилом — фиксируют 2/3 — 3/4 от общей длины хвостовика.
Покупая «расходку», важно помнить, что диаметры зажима бывают разные. Обычно встречаются цанги под хвостовик 6,8 или 12 мм. Не отыскав оснастки нужно размера, печалиться не стоит — просто смените цангу. Она представляет собой вставку, расположенную внутри полого вала привода и зафиксированную гайкой.
Итак, пора зажимать фрезу. Делают это рожковым ключом, предварительно закрепив вал. В моделях попроще понадобиться второй ключ, в инструментах среднего уровня есть кнопка-стопор, но самый удобный фиксатор оборудован еще и «трещоткой» — в таком случае даже перехватывать не придется.
Глубина фрезерования
4. Если операция требует точности, хороший фрезер позволяет скорректировать установленное значение глубины. Его изменяют, не ослабляя (чтобы не сбить) фиксации опорной штанги, а вращая регулировочное колесико. Это можно сделать заранее, добившись точного совпадения рисок указателя и шкалы, или после пробного прохода.Следующий этап настройки — установка глубины погружения. Она задается вертикальным упором, который может иметь несколько ступеней регулировки. Наиболее ходовая — положение самого упора. Уперев его в самую низкую из ножек «револьвера» (если это возможно), ослабляют фиксаторы упора (обычно реализован барашковый зажим) и самой «головы» и опускают ее до касания фрезой поверхности. Заметим, что вовсе не обязательно использовать заготовку, лучше проделывать данную операцию на плоскости верстака, без риска повредить деталь.
5. При опускании «головы» фреза войдет в заготовку на глубину, выставленную на откалиброваннои шкале.Теперь нужно зафиксировать подвижный упор или просто придерживать его одной рукой, а другой установить подвижный указатель (он «ездит» вверх-вниз) напротив нулевого деления мерной шкалы, тем самым откалибровав линейку. Все, она готова к работе.
Перемещая упор и следы за указателем, настраивают глубину и затягивают винт подвижного упора. Если фрезер «из простых», то юстировка закончена. В ином случае глубину погружения подгоняют более точно. Положение подвижного (уже закрепленного) упора изменяют с точностью до десятых долей миллиметра, поворачивая регулировочное колесико. Оно имеет фиксаторы («перещелкивается» по делениям) или просто туго вращается. Первый вариант лучше, так как установка не собьется в процессе эксплуатации. Хорошо, когда такая регулировка реализована в широких пределах, и очень удобно, когда ее можно производить непосредственно во время работы.
Фрезерование
Не вдаваясь в особенности операций и пропустив пункт «Позиционирование машины на плоскости», расскажем, как приступать к работе. Установив максимальную глубину погружения, ее по необходимости «разбивают» на несколько ступеней — для этого предназначен револьверный упор. В подавляющем большинстве случаев он имеет три регулируемые ножки. Иногда их больше, например, восемь, что, впрочем, не считается признаком высокого класса инструмента, а скорее говорит об оригинальности. Не трогая ту ножку, по которой выставляли глубину погружения, задают ступени более высокими. Логика действий тут та же, что и в случае с оборотами, — слишком большое сечение прохода зараз приведет к медленному перемещению и «прижогу» материала, слишком маленькое — к потере производительности. Важен оптимум. Поворачивая барабан и перемещаясь от высокого упора к низкому, двигаются по заготовке до нужной глубины.
Начиная каждый проход, действуют так. Включают мотор, опускают фрезу (в материал или за пределами заготовки в зависимости от ситуации) и фиксируют «голову» стопором. Если проходов несколько или нет уверенности в том, что операция удалась, ее повторяют. Важно помнить, что двигаться по заготовке нужно в строго определенном направлении — материал навстречу вращающимся ножам. Вести фрезер «задом наперед» нельзя, так как это приведет к появлению брака. Направление движения обычно указано на подошве стрелкой; для всех моделей оно одинаково.
Несколько слов о штанговом механизме подъема/опускания «головы». Важно обратить внимание на класс изготовления. Перемещение должно быть плавным и легким, без перекосов и люфтов. Хорошо, когда стопор действует на две штанги — при такой компоновке жесткость и точность фиксации выше.
Надеемся, что читатель уже понял, что главное во фрезере — регулировки. Они обязаны обеспечить точность (это, к слову, во многом зависит от жесткости элементов конструкции) и удобство. Но если углубиться в тонкости выполнения операций, станет ясно, что не менее важно и другое — система. Под ней подразумевается ручная машина с приспособлениями для ее позиционирования на плоскости (без последних от фрезера будет мало толку, по крайней мере универсальность сильно пострадает). Рассказ о системе «фрезер + направляющий аппарат» начнем с наиболее простых случаев.
Фреза с опорным подшипником
Самым элементарным и компактным устройством, задающим положение машины, становится сама фреза, если она дополнена миниатюрным шариковым подшипником. Он располагается под или над режущими ножами и соответственно опирается на верхний или на нижний край кромки. С помощью такой оснастки получают фасонные кромки или нарезают пазы под соединение, окантовку, уплотнитель и т.д.
К достоинствам метода отнесем необременительность подготовительных операций (нужно настроить только вертикальное положение) и возможность точной обработки скругленных и криволинейных кромок (типичный пример — столешница). Недостатки вытекают из достоинств — сделать кривое ровным не удастся.
Параллельный упор
1. Для удобства и точности работы регулируют базу бокового упора. При максимальном сближении губок легче начинать и заканчивать проход. Сближая «башмаки», необходимо помнить о том, что при опускании фрезы она может встретиться с ними, если отступ от края незначителен. Максимально расширенная база облегчит длинные проходы на большом удалении от края, когда велик крутящий момент, уводящий линию упора от перпендикуляра к кромке.Все вышеперечисленное под силу и обычной фрезе без опорного подшипника (она дешевле), если использовать копировальное кольцо или параллельный упор. Начнем с упора. Им комплектуют все без исключения фрезеры, но это не значит, что он у всех одинаков.
2. Фрезер устанавливают на линию разметки, упор подводят к кромке и фиксируют. В данном случае обе штанги зажимают вращением одной рукоятки, обычно — несколькими «персональными» винтами.В самом простом случае упор представляет собой гнутую металлическую пластину на двух стальных штангах с вырезом по центру.
В подошве фрезера для них предусмотрены направляющие с фиксаторами. Для обеспечения жесткости их делают длинными (во всю плиту) или короткими, но двойными — на каждую штангу по две разнесенных.
Фиксация происходит минимум в двух точках (по одной с каждой стороны), максимум — в четырех. В «примитивном» варианте такой упор имеет существенные недостатки — низкую жесткость штампованной конструкции, сложность точной настройки положения, ограничения по диаметру используемой фрезы (она должна помещаться в центральный вырез), невозможность отрегулировать базу опорной поверхности. По мере усложнения аксессуар избавляется от этих недостатков. Для примера рассмотрим самую интересную конструкцию, опуская промежуточные.
3. Отпустив фиксатор механизма прецизионной регулировки, вращают котировочный винт, добиваясь точной установки упора.Штанги фиксируют в подошве не отдельными зажимами, а одним, действующим сразу на две стороны, — так сподручнее. После того как «штыри» зажаты, выставляют положение опорного башмака — он выполнен не заодно со штангами, а способен по ним перемещаться. У него тоже два зажима с одним (что удобнее) или двумя стопорными винтами.
4. После окончания настройки механизм фиксируют.После грубой настройки ослабляют дополнительный фиксатор и двигают опорную часть башмака, вращая юстировочное колесико. Как и в случае с вертикальной настройкой, здесь присутствуют мерные деления.
Выставив требуемое значение, дополнительный стопор фиксируют. Далее при необходимости раздвигают или сближают накладки, тем самым расширяя базу и/или подгоняя размер центрального промежутка между ними под фрезу конкретного диаметра. Заключительное и важнейшее замечание — основа механизма не стальная штампованная, а отлитая из легкого сплава.
5. Точная настройка позволяет добиться полного совпадения линии разметки и оси фрезы. Для облегчения процедуры на подошве делают «мушку-прицел», по которой легче ориентироваться.Параллельный упор пригодится при работе с кромкой или при фрезеровании в поверхности на заданном удалении от края. Работают как по ровному контуру, так и по криволинейному. «Минусы» у такого устройства позиционирования таковы: ограничение отступа от края и сложность процесса.Качественное фрезерование требует определенной сноровки и твердой руки. Например, легко «завалить» линию в начале и в конце заготовки, когда упор контактирует с кромкой не по всей длине базы. Если отступ велик, возрастает и риск уклониться от перпендикуляра с кромкой (или касательной к ней, когда она криволинейна).
Направляющая шина
Шину фиксируют относительно заготовки. Фрезер позиционируется по ней при помощи «башмака», аналогичного боковому упору, и может размещаться на разном удалении от нее. Поскольку на шину опирается лишь часть платформы, выдвигают дополнительную «ножку».Когда речь идет о прямой линии, хорошей альтернативой параллельному упору считается направляющая шина. Ее
закрепляют с произвольным отступом от края и под любым углом к нему. На штанги вместо упора устанавливают специальный башмак — он скользит по шине и задает положение фрезера. Из-за опоры на направляющую может возникнуть перепад высот, так как машина приподнимается над заготовкой. Чтобы не держать ее на весу, выдвигают опорную ножку (если она предусмотрена).
В особой комплектации подобные направляющие служат еще и для точного фрезерования отверстий, что особенно актуально при изготовлении мебели (на линейке есть отверстия со стандартным шагом, на машине — стопор; остается только выбирать нужные позиции и засверливаться).
Важное замечание: набор деталей для работы по направляющей докупают не во всех случаях; он должен присутствовать в списке аксессуаров производителя и подходить к конкретному фрезеру.
Копировальное кольцо
В некоторых случаях копировальную втулку устанавливают одним движением, центровка в таком случае не требуется.Есть и другие дополнительные приспособления, но о них позже. Сейчас же расскажем о копировальном кольце – одном из обязательных атрибутов ручного фрезера, почти всегда входящим в комплект поставки.
1. Для точной и удобной работы фрезер должен иметь гладкую подошву. Когда копировальная втулка не используется, паз, предназначенный для нее, закрывают кольцом.Приспособление очень простое, но удобное в работе и полезное.
Как правило, это штампованная стальная пластина с выступающим кольцевым бортиком вокруг центрального отверстия, который и служит упором, отслеживающим копировальный шаблон.
Втулку подбирают под конкретную фрезу. В идеале она должна проходить сквозь центральное отверстие с небольшим зазором. Иными словами, не стоит полагаться на то единственное кольцо, что прилагается к инструменту.
2. Подобная втулка с нужным диаметром опорного кольца, ее привинчивают, но крепежные винты не затягивают.Чаще всего втулка нуждается в центрировании специальным конусом. Его вставляют в цангу (до упора в копировальное кольцо), тем самым, выравнивая положение, и лишь затем окончательно затягивают крепежные винты. Иногда вместо последних используют быстрозажимные фиксаторы, тогда ничего центрировать не нужно.
3. Для точного позиционирования втулки устанавливают центрирующий корпус. Его, как обычную фрезу, зажимают в цангу (с той лишь разницей, что опорная подошва при этом прижата к корпусу)Принцип действия оснастки прост – выступающий кольцевой бортик в центре ведут вдоль шаблона. При этом фреза повторяет изгибы на заготовке. Главный «минус» у такой «приспособы» один – невозможно получить точную копию – она всегда будет больше оригинала. Подобный метод удобен в серийном производстве (естественно, речь о бытовых масштабах) или когда заготовка достаточно ценная и ради ее обработки стоит изготовить шаблон.
4. После установки конуса стопор механизма опускания освобождают, и подошва под действием подъемных пружин прижимает конус ко втулке, тем самым точно центрируя ее. Вновь зафиксировав стопор, винты крепления втулки надежно затягивают.5. Рекомендуется подбирать кольцо с наименьшим из возможных диаметром центрального отверстия, не забывая о том, что рабочая часть фрезы должна свободно проходить сквозь него.Угловой упор
Получить точную (один в один) копию с оригинала реально, установив угловой упор со щупом (как и многие другие аксессуары, его докупают отдельно). В этом случае заготовку располагают не под, а над шаблоном. Для точной подгонки размеров может быть предусмотрена настройка положения щупа.
Кстати, если установить вместо кронштейна со щупом опорную плиту или регулируемый упор для работы в горизонтальном положении, получится инструмент для фрезерования кромочных накладок заподлицо.
Циркуль
Подошву фрезера жестко привинчивают к «циркулю»; радиус задают перемещением по направляющей «центра». Центрирующий штифт вставляют в просверленное в заготовке отверстие. Существуют конструкции, в которых «циркулем» служит боковой упор или дополнительное приспособление, устанавливаемое на штангах.Частный случай криволинейной резки – по радиусу. Отдельно докупаемая линейка-циркуль поможет выполнить ее без шаблонов, а значит, точнее и с меньшими усилиями.
Пылеотсос
Об общих особенностях ручных фрезеров, пожалуй, все. Отметим только, что важное значение имеет система пылеудаления, ведь место «прописки» этого инструмента – мастерская. Стандартный вариант – кожух, закрепляемый снизу, под параллельным упором. Эффективность такого сборника средняя, как и другой разновидности – бокового «отбойника». Лучше, когда его ставят сверху, правда, лишь в том случае, если верхнее отверстие для фрезы не слишком велико.
Примеры использования
В зависимости от типа шаблона устанавливают фрезу. Регулируя глубину ее погружения, задают плотность соединения. Его можно собрать внатяг или на клею (для него необходимо предусмотреть зазор). С помощью специальных окон в шаблоне задают продольное положение упоров заготовки и поворачивают их соответствующей шаблону стороной. Далее с каждой стороны шаблона парами зажимают сопрягаемые детали. Они должны быть чисто обработаны и плотно пригнаны.Что касается наиболее известной работы для фрезера – по кромке, то здесь комментарии излишни, все и так ясно: выбирают насадку под нужный фасон и материал, способ позиционирования на плоскости (фреза с опорным роликом, копирование по шаблону с помощью втулки или углового упора, по самой заготовке с помощью бокового упора или направляющей шины) и приступают к делу. Не требуют разъяснений и действия с выборкой пазов на плоскости (декоративных или технологических). А что еще умеет фрезер?
Следующая группа типовых задач – врезка. Большинство моделей без труда справляются с подготовкой посадочных мест под накладные или мебельные петли. Более совершенные, с увеличенным вертикальным ходом, помогут с установкой врезных замков.
Обширная область применения ручных фрезеров связана с соединением деталей из древесины и ее производных. Наиболее просты (не требуют сложной оснастки) соединения типа шип-паз и переплеты. Их используют при изготовлении окон, дверей и многих других сборных столярных изделий. Как правило, применяют две парные фрезы (профиль и контрпрофиль). Как уже упоминалось, инструмент облегчает точное засверливание под нагели.
На фрезер устанавливают специальную копировальную втулку. Для повышения точности вертикального позиционирования она имеет бортик на опорном кольце, позволяющий захватить пластину шаблона с двух сторон. Руководствуясь общим правилом ведения инструмента против хода фрезы, заготовку проходят от центра к краю. Предварительно рекомендуется сделать подрезку (пройти шаблон по выступам, не «заходя» в них) — это позволит избежать сколов.Достаточно дорогое, но оправдывающее свою цену приспособление – шипорезное. По сути, это сложный и точно выполненный зажим для заготовок, дополненный копировальным шаблоном. Работают по нему со специальной копировальной втулкой. Она не только опирается на плоскость шаблона, но и «держится» за него с обратной стороны за счет небольшого бортика. Закрепляют сразу две или четыре сопрягаемые детали (с другого края, с каждой парой работают отдельно), при этом специальные упоры задают требуемое смещение заготовок друг относительно друга. Далее настраивают фрезер. Зажимают насадку специальной формы («ласточкин хвост») и в соответствии со справочной таблицей задают глубину фрезерования. От нее зависит плотность соединения, то есть зазор в паре шип-гнездо. При точной настройке несложно добиться «нулевого» зазора – после сборки внатяг конструкция будет плотно держаться без клея и других дополнительных мер фиксации. Такие соединения применяют, например, при изготовлении мебели из массива древесины ценных пород.
Несложно получить соединения и под прямой шип – потребуются другие шаблон и насадка.
В рамках нашей статьи мы кратко обрисовали основные технологические операции, на самом же деле их гораздо больше. Что и неудивительно, ведь фрезер используют даже в художественных целях для нанесения гравировок (опять-таки специальной – перьевой фрезой). Важно понимать, что этот инструмент, за редким исключением, – вещь не самодостаточная и требует всякого рода оснастки и приспособлений. Без них он едва ли раскроет и четверть своих возможностей.
Именно по этой причине к покупке стоит отнестись максимально ответственно, обратив внимание не столько на сам аппарат, сколько на перечень фирменных (иные могут и не подойти!) аксессуаров к нему.
Фрезер что такое. Изготавливаем ламельный фрезер. Что это такое?
Что такое ламельный фрезер, и как его изготовить своими руками?
В современном хозяйстве незаменимым помощником является такой инструмент, как ламельный фрезер. С ним станет возможным выполнение различных фигурных вырезок, прорезей, шлифовки поверхности.
Особенно необходимым данный инструмент будет для хозяина, занимающегося столярными работами, мебельщика или просто любителя работать с деревом и другими материалами. Ниже мы рассмотрим, что же такое ламельный фрезер, для чего он предназначен, изучим его конструктивные особенности и устройство в общих чертах. Осветим такую проблему, как изготовление ламельного фрезера своими силами в домашних условиях, какие материалы можно использовать для этого, и в какой последовательности их собирать.
Что такое ламельный фрезер
Ламельный фрезер – это инструмент, предназначенный для нарезки пазов ламельных соединений. Ламель – это пластина из дерева стандартного размера. Этот инструмент по конструкции напоминает болгарку. Основные части, из которых он состоит – это силовой агрегат, редуктор в виде конуса, непосредственно сам корпус. Закрепление фрезы на шпинделе производится с помощью гайки.
Инструмент подходит как для работы с деревом, так и для пластиковых материалов, оргстекла, камня, цветного металла, при этом требуется дополнительное оборудование. С фрезером вы можете производить следующие виды работ:
- профилирование кромки;
- выборку четверти;
- шлифовку;
- сверление технологических отверстий;
- вырезку углублений и прорезей различных форм;
- вырезку шипов.
Для разных видов работ требуются фрезеры различной мощности. Их можно разделить на три группы:
- 750 Вт – маломощные;
- 1100 Вт – средней мощности;
- 1200 Вт – мощные.
Для бытового использования будет достаточно использовать фрезер мощностью 750 или 1100 Вт.
Количество оборотов шпинделя может варьироваться в пределах от 3000 до 24000 об/мин. Выбирать режим следует, руководствуясь специальными таблицами. Глубина фрезеровки лежит в пределах 30–60 мм.
Устройство пуска в современных моделях обычно имеет защиту от «дурака», так называемый блокировщик. Кроме того, есть механизм фиксации, без которого рабочий процесс становится проблематичным.
Цанга представляет собой зажим для фрезы. Она должна быть изготовлена из закаленной стали. Конусовидная форма цанги считается лучшей среди специалистов. Для удобного удаления сора с рабочей поверхности стола предусмотрен отсос пыли. Подошва фрезера может быть выполнена из штампованного металла либо быть литой.
Как изготовить ламельный фрезер самостоятельно
В условиях кризиса сегодня не всегда домохозяин может позволить себе купить полноценный фрезер. Поэтому мы рассмотрим способ, как можно выкрутиться из этого положения с помощью обыкновенной «болгарки» с диском, нескольких листов фанеры или оргстекла, ну и, конечно же, ваших рук и смекалки.
Изготовить такой инструмент самому можно из обычной болгарки или иначе УШМ. Желательно, чтобы она имела регулируемые обороты ротора. Это необходимо для того, чтобы была возможность выставить требуемую скорость вращения диска. В исключительном случае подойдет машинка под 125 диаметр круга.
Помимо этого, нам потребуется ламельная фреза. В качестве материала для корпуса подойдет фанера или же оргстекло, которое предварительно можно отполировать. Основной корпус с боковыми пазами состоит из двух боковых и задних стенок. Верхняя и нижняя части здесь отсутствуют, сама же болгарка с ламельным диском вставляется в пазы боковых стенок вырезанными из дерева направляющими, прикрепленными к ней с двух сторон сбоку. Для регулировки высоты распила ламелей необходимо сконструировать простейшее подъемное устройство. При отсутствии необходимости в регулировке высоты, инструмент можно просто зафиксировать на определенной высоте. Оставшаяся боковая стенка фиксируется к УШМ с помощью болтов, вкручиваемых в резьбу под держатель.
Ознакомившись с данным материалом, вы сможете самостоятельно собрать себе такой инструмент, потратив время и силы, но сэкономив свои финансы. Мы искренне надеемся, что вам понравилась наша статья!
pro-instrument.com
это обработка материалов, и что такое фрезеровка лазером
Фрезерование – это вид обработки деталей с помощью фрез вручную или на станке.
В наше время фрезеровка имеет такое же распространение, как токарная обработка детали либо сверление.
Процесс фрезерования заготовки, выполненной из различного материала, заключается в обработке заготовки с помощью фрезы.
Фреза – это режущий инструмент, выполненный в виде зубчатого колеса, имеющего множество лезвий, который зажимается во фрезерном станке и, вращаясь с большой скоростью, снимает слои поверхности заготовки в нужном вам месте.
Обработка заготовки на станке
Раньше сам фрезерный станок работал лишь вручную, поэтому велик был процент брака.
С применением новых технологий и программирования появились новые фрезерные станки – с программным числовым управлением, использование которых облегчило и упростило работу фрезеровщиков.
Сейчас стал доступен и применен новый вид обработки – с помощью лазера, так на новых станках рабочий орган (фреза) полностью заменили на лазер. Лазер дает более точную обработку заготовки и соответственно меньший процент брака.
Лазерная обработка поверхности заготовки позволила совместить в один процесс обработку на токарном и фрезерном станках, и теперь появился новый термин «фрезерно-токарная обработка материала».
Классификация фрезерных работ
Четкого разделения этого вида обработки нет из-за того, что выполняемые вами работы очень разнообразны.
Существует разделение по типу станка:
- Лазерная обработка.
- Фрезерная механическая обработка.
Из основных видов можно указать следующие:
- по расположению на станине обрабатываемой заготовки – вертикальная, горизонтальная фрезеровка и фрезерование под определенным углом;
- по виду применяемой фрезы – концевая, торцевая, фасонная, периферийная;
- по направлению вращения режущего инструмента относительно движения заготовки – встречная или попутная.
Последний тип классификации используется для обработки больших заготовок, когда первичное фрезерование детали выполняется встречным видом обработки, а для окончательной доводки применяется попутный вид.
Технология процесса фрезеровки
В зависимости от типа станка, сложности обрабатываемой заготовки, материала применяемой детали различается и сама технология, по которой происходит фрезерная обработка.
Технология процесса фрезеровки на обычном станке
Вначале фрезеровщик производит подбор фрезы, которая надежно крепится на шпинделе фрезерного станка.
Обработка заготовки начинается с подготовки:
- включается небольшое вращение шпинделя, при этом деталь подводится к самой фрезе до наименьшего соприкосновения с ней;
- станина стола с закрепленной заготовкой отводится и вращающийся шпиндель останавливается;
- устанавливается необходимая глубина резки детали;
- включается вращение фрезы;
- станину стола с обрабатываемой деталью вручную перемещают до соприкосновения с вращающейся фрезой.
Фрезеровщику для работы над одной заготовкой необходим набор фрез, это позволяет увеличить производительность выполняемой им операции.
Размеры рабочего инструмента (фрез) выбираются, исходя из необходимого стандарта точности, так, для чернового вида фрезеровки необходимо достичь одиннадцатого или двенадцатого квалитета точности, а при заключительном этапе фрезеровки – 8 или 9.
В особых случаях согласно заданию точность размера может соответствовать 7 или 8 квалитетам.
Фрезерная обработка на станке с числовым программным управлением (ЧПУ)
Фрезерование с применением ЧПУ начало внедряться в производство не так давно, ее родоначальником можно считать систему рычагов, которая использовалась на обычных фрезерных станках.
С развитием электроники и вычислительной техники управление фрезерным станком было отдано компьютеру. Так фрезеровщик стал оператором ЧПУ, а для его взаимодействия со станком были написаны программы.
Обработка материала на станке ЧПУ позволяет увеличить точность, увеличить производительность, снизить процент брака, а также наладить выпуск серийных деталей со сложной геометрической поверхностью в большом количестве.
Компьютер задает станку и количество оборотов шпинделя, и параметры его движения (линейные координаты и глубина фрезеровки).
Современные ЧПУ станки могут выполнять 3D фрезеровку – это обработка детали несколькими рабочими органами одновременно, при этом находясь в разных плоскостях.
Перед началом работы, оператор предварительно на компьютере строит 3D-модель детали, станок затем воспроизводит ее с максимальной точностью.
На станке с ЧПУ к квалификации фрезеровщика предъявляются совсем иные требования.
Лазерная обработка детали на станке с ЧПУ
В современной обработке детали лазером он применяется лишь на станке с ЧПУ.
Это оборудование самое дорогостоящее, цена за работу выше, чем на фрезерном обычном станке, но лазерная обработка детали позволяет получить максимальную точность, значительно снижая при этом время на изготовление единицы детали.
Лазерным ЧПУ станкам под силу как точное фрезерование обычного материала, так и изготовление сложных объемных геометрических деталей, исключение лишь только составляют сферообразные округлые конструкции.
Лазерное фрезерование заготовки может выполняться двумя вариантами:
- В нужном месте станок с помощью теплового лазера выжигает заготовку, по окончании процесса выжигания шлифуется кромка.
- Шлифовочный лазер, снимает понемногу слои материала детали, многократно проходя по одному и тому же месту.
Лазерная обработка заготовки оставляет верхний слой гладким, без заусениц, это позволяет не производить дополнительную операцию – шлифование уже готовой вашей детали.
Фрезерование деталей выполненных из титана
Титан, как материал для деталей, все чаще используют в аэрокосмической отрасли. Титан один из самых трудных материалов для металлообработки режущей фрезой, так как он обладает низкой теплопроводностью.
То есть вовремя процесса фрезерования титана лишь небольшая часть тепла уходит со снимаемой стружкой, а это вызывает хороший нагрев как деталей фрезерного станка, так и самой заготовки.
Несмотря на все трудности с фрезерованием титана, для качественной обработки материала фрезеровщики дают немного дельных советов:
- максимально необходимо уменьшите площадь контакта заготовки из титана и фрезы;
- тщательно нужно следить за фрезой, ее режущая кромка должна быть остротой;
- применяйте фрезы с большим количеством зубьев;
- придерживайтесь позиции «только тонкая стружка»;
- начало фрезеровки производите по дуге;
- в конце прохода фрезы снимите фаску под 45°;
- применяйте фрезы с большим дополнительным задним углом;
- скрупулёзно наблюдайте за осевой вашей глубиной;
- если деталь тонкая необходимо уменьшить осевую глубину фрезерования;
- выбирать необходимо фрезу, диаметр которой не более 70% от диаметра выбираемого паза;
- для фрезеровки заготовки из титана необходимо применять высокоскоростные фрезы.
Цена на фрезеровочные работы во многом зависит от геометрии детали, вида фрезерного станка и материала вашей заготовки.
Фрезеровка материала должна производиться на исправном фрезерном оборудовании, специально прошедшем обучение персоналом.
Обращаясь за услугами фрезеровки, поинтересуйтесь, какие фрезерные станки использует фирма, уточните у знакомых или друзей репутацию исполнителя, тогда качество выполненной работы вас не разочарует, не покажется завышенной цена.
Ручной фрезер: основные технологические операции — Proderevo.net
Такой инструмент состоит из двух частей: верхней, куда входят мотор, рукоятки, цанговый зажим, фиксаторы вертикального положения, и нижней — со штангами, опорной подошвой и револьверным упором. Машины этой разновидности отличаются тем, что позволяют погружаться в обрабатываемый материал на требуемую (в пределах возможностей) глубину. На примерах конкретных операций рассмотрим важные особенности конструкций современных устройств данного типа.
Готовимся к работе
1. Фрезу зажимают в цангу, пользуясь рожковым ключом и механизмом блокировки вала. Если последнего не предусмотрено, понадобится второй ключ. В данном случае установка упрощена донельзя — стопор снабжен переключаемой (отворачивание/ заворачивание) «трещоткой». Фрезу зажимают, руководствуясь разметкой на ней или исходя из общего правила (2/3-3/4 длины хвостовика).Начнем с азов — подготовки к работе. В зависимости от материала и задачи выбирают фрезу. Для мягких пород древесины, фанеры, МДФ применяют насадку с ножами из быстрорежущей стали (HSS), не возбраняется и более дорогая, точная и стойкая, с твердосплавными лезвиями (HM). В остальных случаях — ДСП, древесина твердых пород, композитные составы — использование HM обязательно. Как уже упоминалось, одна из важнейших особенностей твердосплавных лезвий — точность: они оставляют более чистую поверхность.
2. «Голову» инструмента опускают до упора фрезой в поверхность, после чего ее удобно фиксировать. Далее, исходя из вылета режущей оснастки и желаемой глубины обработки, выбирают самую низкую из подходящих «ножек» револьверного упора. Это позволяет проходить заготовки в несколько приемов, не повторяя точных регулировок. Зачастую положение каждой «ножки» можно подстроить в небольших пределах. На выбранную «подставку» опус кают опорную штангу, предварительно отпустив ее зажим. Не фиксируя ее, а лишь прижимая пальцем, перемещают по ней подвижный указатель, добиваясь его совпадения с нулем мерной линейки.В зависимости от диаметра фрезы и материала устанавливают частоту вращения. Поскольку регулировочное колесико обычно маркируют в условных единицах, придется воспользоваться инструкцией, где указывают, когда что нужно выставлять. Вообще говоря, настройка оборотов — очень ответственная процедура. Во-первых, оснастка большого диаметра может не выдержать слишком высокую скорость, во-вторых, важно подобрать режим. При завышенной частоте есть риск «прижечь» заготовку, при заниженной — падает производительность и ухудшается качество обработки.
3. Штангу поднимают до совпадения указателя с требуемым делением измерительной шкалы и зажимают ее фиксатором.Определившись с оборотами и типом фрезы, устанавливают оснастку. Сделать это верно помогут риски на хвостовике — ориентироваться нужно на них. Если требуется отступить от предписания (или его попросту не оказалось), пользуются простым правилом — фиксируют 2/3 — 3/4 от общей длины хвостовика.
Покупая «расходку», важно помнить, что диаметры зажима бывают разные. Обычно встречаются цанги под хвостовик 6,8 или 12 мм. Не отыскав оснастки нужно размера, печалиться не стоит — просто смените цангу. Она представляет собой вставку, расположенную внутри полого вала привода и зафиксированную гайкой.
Итак, пора зажимать фрезу. Делают это рожковым ключом, предварительно закрепив вал. В моделях попроще понадобиться второй ключ, в инструментах среднего уровня есть кнопка-стопор, но самый удобный фиксатор оборудован еще и «трещоткой» — в таком случае даже перехватывать не придется.
Глубина фрезерования
4. Если операция требует точности, хороший фрезер позволяет скорректировать установленное значение глубины. Его изменяют, не ослабляя (чтобы не сбить) фиксации опорной штанги, а вращая регулировочное колесико. Это можно сделать заранее, добившись точного совпадения рисок указателя и шкалы, или после пробного прохода.Следующий этап настройки — установка глубины погружения. Она задается вертикальным упором, который может иметь несколько ступеней регулировки. Наиболее ходовая — положение самого упора. Уперев его в самую низкую из ножек «револьвера» (если это возможно), ослабляют фиксаторы упора (обычно реализован барашковый зажим) и самой «головы» и опускают ее до касания фрезой поверхности. Заметим, что вовсе не обязательно использовать заготовку, лучше проделывать данную операцию на плоскости верстака, без риска повредить деталь.
5. При опускании «головы» фреза войдет в заготовку на глубину, выставленную на откалиброваннои шкале.Теперь нужно зафиксировать подвижный упор или просто придерживать его одной рукой, а другой установить подвижный указатель (он «ездит» вверх-вниз) напротив нулевого деления мерной шкалы, тем самым откалибровав линейку. Все, она готова к работе.
Перемещая упор и следы за указателем, настраивают глубину и затягивают винт подвижного упора. Если фрезер «из простых», то юстировка закончена. В ином случае глубину погружения подгоняют более точно. Положение подвижного (уже закрепленного) упора изменяют с точностью до десятых долей миллиметра, поворачивая регулировочное колесико. Оно имеет фиксаторы («перещелкивается» по делениям) или просто туго вращается. Первый вариант лучше, так как установка не собьется в процессе эксплуатации. Хорошо, когда такая регулировка реализована в широких пределах, и очень удобно, когда ее можно производить непосредственно во время работы.
Фрезерование
Не вдаваясь в особенности операций и пропустив пункт «Позиционирование машины на плоскости», расскажем, как приступать к работе. Установив максимальную глубину погружения, ее по необходимости «разбивают» на несколько ступеней — для этого предназначен револьверный упор. В подавляющем большинстве случаев он имеет три регулируемые ножки. Иногда их больше, например, восемь, что, впрочем, не считается признаком высокого класса инструмента, а скорее говорит об оригинальности. Не трогая ту ножку, по которой выставляли глубину погружения, задают ступени более высокими. Логика действий тут та же, что и в случае с оборотами, — слишком большое сечение прохода зараз приведет к медленному перемещению и «прижогу» материала, слишком маленькое — к потере производительности. Важен оптимум. Поворачивая барабан и перемещаясь от высокого упора к низкому, двигаются по заготовке до нужной глубины.
Начиная каждый проход, действуют так. Включают мотор, опускают фрезу (в материал или за пределами заготовки в зависимости от ситуации) и фиксируют «голову» стопором. Если проходов несколько или нет уверенности в том, что операция удалась, ее повторяют. Важно помнить, что двигаться по заготовке нужно в строго определенном направлении — материал навстречу вращающимся ножам. Вести фрезер «задом наперед» нельзя, так как это приведет к появлению брака. Направление движения обычно указано на подошве стрелкой; для всех моделей оно одинаково.
Несколько слов о штанговом механизме подъема/опускания «головы». Важно обратить внимание на класс изготовления. Перемещение должно быть плавным и легким, без перекосов и люфтов. Хорошо, когда стопор действует на две штанги — при такой компоновке жесткость и точность фиксации выше.
Надеемся, что читатель уже понял, что главное во фрезере — регулировки. Они обязаны обеспечить точность (это, к слову, во многом зависит от жесткости элементов конструкции) и удобство. Но если углубиться в тонкости выполнения операций, станет ясно, что не менее важно и другое — система. Под ней подразумевается ручная машина с приспособлениями для ее позиционирования на плоскости (без последних от фрезера будет мало толку, по крайней мере универсальность сильно пострадает). Рассказ о системе «фрезер + направляющий аппарат» начнем с наиболее простых случаев.
Фреза с опорным подшипником
Самым элементарным и компактным устройством, задающим положение машины, становится сама фреза, если она дополнена миниатюрным шариковым подшипником. Он располагается под или над режущими ножами и соответственно опирается на верхний или на нижний край кромки. С помощью такой оснастки получают фасонные кромки или нарезают пазы под соединение, окантовку, уплотнитель и т.д.
К достоинствам метода отнесем необременительность подготовительных операций (нужно настроить только вертикальное положение) и возможность точной обработки скругленных и криволинейных кромок (типичный пример — столешница). Недостатки вытекают из достоинств — сделать кривое ровным не удастся.
Параллельный упор
1. Для удобства и точности работы регулируют базу бокового упора. При максимальном сближении губок легче начинать и заканчивать проход. Сближая «башмаки», необходимо помнить о том, что при опускании фрезы она может встретиться с ними, если отступ от края незначителен. Максимально расширенная база облегчит длинные проходы на большом удалении от края, когда велик крутящий момент, уводящий линию упора от перпендикуляра к кромке.Все вышеперечисленное под силу и обычной фрезе без опорного подшипника (она дешевле), если использовать копировальное кольцо или параллельный упор. Начнем с упора. Им комплектуют все без исключения фрезеры, но это не значит, что он у всех одинаков.
2. Фрезер устанавливают на линию разметки, упор подводят к кромке и фиксируют. В данном случае обе штанги зажимают вращением одной рукоятки, обычно — несколькими «персональными» винтами.В самом простом случае упор представляет собой гнутую металлическую пластину на двух стальных штангах с вырезом по центру.
В подошве фрезера для них предусмотрены направляющие с фиксаторами. Для обеспечения жесткости их делают длинными (во всю плиту) или короткими, но двойными — на каждую штангу по две разнесенных.
Фиксация происходит минимум в двух точках (по одной с каждой стороны), максимум — в четырех. В «примитивном» варианте такой упор имеет существенные недостатки — низкую жесткость штампованной конструкции, сложность точной настройки положения, ограничения по диаметру используемой фрезы (она должна помещаться в центральный вырез), невозможность отрегулировать базу опорной поверхности. По мере усложнения аксессуар избавляется от этих недостатков. Для примера рассмотрим самую интересную конструкцию, опуская промежуточные.
3. Отпустив фиксатор механизма прецизионной регулировки, вращают котировочный винт, добиваясь точной установки упора.Штанги фиксируют в подошве не отдельными зажимами, а одним, действующим сразу на две стороны, — так сподручнее. После того как «штыри» зажаты, выставляют положение опорного башмака — он выполнен не заодно со штангами, а способен по ним перемещаться. У него тоже два зажима с одним (что удобнее) или двумя стопорными винтами.
4. После окончания настройки механизм фиксируют.После грубой настройки ослабляют дополнительный фиксатор и двигают опорную часть башмака, вращая юстировочное колесико. Как и в случае с вертикальной настройкой, здесь присутствуют мерные деления.
Выставив требуемое значение, дополнительный стопор фиксируют. Далее при необходимости раздвигают или сближают накладки, тем самым расширяя базу и/или подгоняя размер центрального промежутка между ними под фрезу конкретного диаметра. Заключительное и важнейшее замечание — основа механизма не стальная штампованная, а отлитая из легкого сплава.
5. Точная настройка позволяет добиться полного совпадения линии разметки и оси фрезы. Для облегчения процедуры на подошве делают «мушку-прицел», по которой легче ориентироваться.Параллельный упор пригодится при работе с кромкой или при фрезеровании в поверхности на заданном удалении от края. Работают как по ровному контуру, так и по криволинейному. «Минусы» у такого устройства позиционирования таковы: ограничение отступа от края и сложность процесса.Качественное фрезерование требует определенной сноровки и твердой руки. Например, легко «завалить» линию в начале и в конце заготовки, когда упор контактирует с кромкой не по всей длине базы. Если отступ велик, возрастает и риск уклониться от перпендикуляра с кромкой (или касательной к ней, когда она криволинейна).
Направляющая шина
Шину фиксируют относительно заготовки. Фрезер позиционируется по ней при помощи «башмака», аналогичного боковому упору, и может размещаться на разном удалении от нее. Поскольку на шину опирается лишь часть платформы, выдвигают дополнительную «ножку».Когда речь идет о прямой линии, хорошей альтернативой параллельному упору считается направляющая шина. Ее
закрепляют с произвольным отступом от края и под любым углом к нему. На штанги вместо упора устанавливают специальный башмак — он скользит по шине и задает положение фрезера. Из-за опоры на направляющую может возникнуть перепад высот, так как машина приподнимается над заготовкой. Чтобы не держать ее на весу, выдвигают опорную ножку (если она предусмотрена).
В особой комплектации подобные направляющие служат еще и для точного фрезерования отверстий, что особенно актуально при изготовлении мебели (на линейке есть отверстия со стандартным шагом, на машине — стопор; остается только выбирать нужные позиции и засверливаться).
Важное замечание: набор деталей для работы по направляющей докупают не во всех случаях; он должен присутствовать в списке аксессуаров производителя и подходить к конкретному фрезеру.
Копировальное кольцо
В некоторых случаях копировальную втулку устанавливают одним движением, центровка в таком случае не требуется.Есть и другие дополнительные приспособления, но о них позже. Сейчас же расскажем о копировальном кольце – одном из обязательных атрибутов ручного фрезера, почти всегда входящим в комплект поставки.
1. Для точной и удобной работы фрезер должен иметь гладкую подошву. Когда копировальная втулка не используется, паз, предназначенный для нее, закрывают кольцом.Приспособление очень простое, но удобное в работе и полезное.
Как правило, это штампованная стальная пластина с выступающим кольцевым бортиком вокруг центрального отверстия, который и служит упором, отслеживающим копировальный шаблон.
Втулку подбирают под конкретную фрезу. В идеале она должна проходить сквозь центральное отверстие с небольшим зазором. Иными словами, не стоит полагаться на то единственное кольцо, что прилагается к инструменту.
2. Подобная втулка с нужным диаметром опорного кольца, ее привинчивают, но крепежные винты не затягивают.Чаще всего втулка нуждается в центрировании специальным конусом. Его вставляют в цангу (до упора в копировальное кольцо), тем самым, выравнивая положение, и лишь затем окончательно затягивают крепежные винты. Иногда вместо последних используют быстрозажимные фиксаторы, тогда ничего центрировать не нужно.
3. Для точного позиционирования втулки устанавливают центрирующий корпус. Его, как обычную фрезу, зажимают в цангу (с той лишь разницей, что опорная подошва при этом прижата к корпусу)Принцип действия оснастки прост – выступающий кольцевой бортик в центре ведут вдоль шаблона. При этом фреза повторяет изгибы на заготовке. Главный «минус» у такой «приспособы» один – невозможно получить точную копию – она всегда будет больше оригинала. Подобный метод удобен в серийном производстве (естественно, речь о бытовых масштабах) или когда заготовка достаточно ценная и ради ее обработки стоит изготовить шаблон.
4. После установки конуса стопор механизма опускания освобождают, и подошва под действием подъемных пружин прижимает конус ко втулке, тем самым точно центрируя ее. Вновь зафиксировав стопор, винты крепления втулки надежно затягивают.5. Рекомендуется подбирать кольцо с наименьшим из возможных диаметром центрального отверстия, не забывая о том, что рабочая часть фрезы должна свободно проходить сквозь него.Угловой упор
Получить точную (один в один) копию с оригинала реально, установив угловой упор со щупом (как и многие другие аксессуары, его докупают отдельно). В этом случае заготовку располагают не под, а над шаблоном. Для точной подгонки размеров может быть предусмотрена настройка положения щупа.
Кстати, если установить вместо кронштейна со щупом опорную плиту или регулируемый упор для работы в горизонтальном положении, получится инструмент для фрезерования кромочных накладок заподлицо.
Циркуль
Подошву фрезера жестко привинчивают к «циркулю»; радиус задают перемещением по направляющей «центра». Центрирующий штифт вставляют в просверленное в заготовке отверстие. Существуют конструкции, в которых «циркулем» служит боковой упор или дополнительное приспособление, устанавливаемое на штангах.Частный случай криволинейной резки – по радиусу. Отдельно докупаемая линейка-циркуль поможет выполнить ее без шаблонов, а значит, точнее и с меньшими усилиями.
Пылеотсос
Об общих особенностях ручных фрезеров, пожалуй, все. Отметим только, что важное значение имеет система пылеудаления, ведь место «прописки» этого инструмента – мастерская. Стандартный вариант – кожух, закрепляемый снизу, под параллельным упором. Эффективность такого сборника средняя, как и другой разновидности – бокового «отбойника». Лучше, когда его ставят сверху, правда, лишь в том случае, если верхнее отверстие для фрезы не слишком велико.
Примеры использования
В зависимости от типа шаблона устанавливают фрезу. Регулируя глубину ее погружения, задают плотность соединения. Его можно собрать внатяг или на клею (для него необходимо предусмотреть зазор). С помощью специальных окон в шаблоне задают продольное положение упоров заготовки и поворачивают их соответствующей шаблону стороной. Далее с каждой стороны шаблона парами зажимают сопрягаемые детали. Они должны быть чисто обработаны и плотно пригнаны.Что касается наиболее известной работы для фрезера – по кромке, то здесь комментарии излишни, все и так ясно: выбирают насадку под нужный фасон и материал, способ позиционирования на плоскости (фреза с опорным роликом, копирование по шаблону с помощью втулки или углового упора, по самой заготовке с помощью бокового упора или направляющей шины) и приступают к делу. Не требуют разъяснений и действия с выборкой пазов на плоскости (декоративных или технологических). А что еще умеет фрезер?
Следующая группа типовых задач – врезка. Большинство моделей без труда справляются с подготовкой посадочных мест под накладные или мебельные петли. Более совершенные, с увеличенным вертикальным ходом, помогут с установкой врезных замков.
Обширная область применения ручных фрезеров связана с соединением деталей из древесины и ее производных. Наиболее просты (не требуют сложной оснастки) соединения типа шип-паз и переплеты. Их используют при изготовлении окон, дверей и многих других сборных столярных изделий. Как правило, применяют две парные фрезы (профиль и контрпрофиль). Как уже упоминалось, инструмент облегчает точное засверливание под нагели.
На фрезер устанавливают специальную копировальную втулку. Для повышения точности вертикального позиционирования она имеет бортик на опорном кольце, позволяющий захватить пластину шаблона с двух сторон. Руководствуясь общим правилом ведения инструмента против хода фрезы, заготовку проходят от центра к краю. Предварительно рекомендуется сделать подрезку (пройти шаблон по выступам, не «заходя» в них) — это позволит избежать сколов.Достаточно дорогое, но оправдывающее свою цену приспособление – шипорезное. По сути, это сложный и точно выполненный зажим для заготовок, дополненный копировальным шаблоном. Работают по нему со специальной копировальной втулкой. Она не только опирается на плоскость шаблона, но и «держится» за него с обратной стороны за счет небольшого бортика. Закрепляют сразу две или четыре сопрягаемые детали (с другого края, с каждой парой работают отдельно), при этом специальные упоры задают требуемое смещение заготовок друг относительно друга. Далее настраивают фрезер. Зажимают насадку специальной формы («ласточкин хвост») и в соответствии со справочной таблицей задают глубину фрезерования. От нее зависит плотность соединения, то есть зазор в паре шип-гнездо. При точной настройке несложно добиться «нулевого» зазора – после сборки внатяг конструкция будет плотно держаться без клея и других дополнительных мер фиксации. Такие соединения применяют, например, при изготовлении мебели из массива древесины ценных пород.
Несложно получить соединения и под прямой шип – потребуются другие шаблон и насадка.
В рамках нашей статьи мы кратко обрисовали основные технологические операции, на самом же деле их гораздо больше. Что и неудивительно, ведь фрезер используют даже в художественных целях для нанесения гравировок (опять-таки специальной – перьевой фрезой). Важно понимать, что этот инструмент, за редким исключением, – вещь не самодостаточная и требует всякого рода оснастки и приспособлений. Без них он едва ли раскроет и четверть своих возможностей.
Именно по этой причине к покупке стоит отнестись максимально ответственно, обратив внимание не столько на сам аппарат, сколько на перечень фирменных (иные могут и не подойти!) аксессуаров к нему.
Фрезер что такое. Изготавливаем ламельный фрезер. Что это такое?
Что такое ламельный фрезер, и как его изготовить своими руками?
В современном хозяйстве незаменимым помощником является такой инструмент, как ламельный фрезер. С ним станет возможным выполнение различных фигурных вырезок, прорезей, шлифовки поверхности.
Особенно необходимым данный инструмент будет для хозяина, занимающегося столярными работами, мебельщика или просто любителя работать с деревом и другими материалами. Ниже мы рассмотрим, что же такое ламельный фрезер, для чего он предназначен, изучим его конструктивные особенности и устройство в общих чертах. Осветим такую проблему, как изготовление ламельного фрезера своими силами в домашних условиях, какие материалы можно использовать для этого, и в какой последовательности их собирать.
Что такое ламельный фрезер
Ламельный фрезер – это инструмент, предназначенный для нарезки пазов ламельных соединений. Ламель – это пластина из дерева стандартного размера. Этот инструмент по конструкции напоминает болгарку. Основные части, из которых он состоит – это силовой агрегат, редуктор в виде конуса, непосредственно сам корпус. Закрепление фрезы на шпинделе производится с помощью гайки.
Инструмент подходит как для работы с деревом, так и для пластиковых материалов, оргстекла, камня, цветного металла, при этом требуется дополнительное оборудование. С фрезером вы можете производить следующие виды работ:
- профилирование кромки;
- выборку четверти;
- шлифовку;
- сверление технологических отверстий;
- вырезку углублений и прорезей различных форм;
- вырезку шипов.
Для разных видов работ требуются фрезеры различной мощности. Их можно разделить на три группы:
- 750 Вт – маломощные;
- 1100 Вт – средней мощности;
- 1200 Вт – мощные.
Для бытового использования будет достаточно использовать фрезер мощностью 750 или 1100 Вт.
Количество оборотов шпинделя может варьироваться в пределах от 3000 до 24000 об/мин. Выбирать режим следует, руководствуясь специальными таблицами. Глубина фрезеровки лежит в пределах 30–60 мм.
Устройство пуска в современных моделях обычно имеет защиту от «дурака», так называемый блокировщик. Кроме того, есть механизм фиксации, без которого рабочий процесс становится проблематичным.
Цанга представляет собой зажим для фрезы. Она должна быть изготовлена из закаленной стали. Конусовидная форма цанги считается лучшей среди специалистов. Для удобного удаления сора с рабочей поверхности стола предусмотрен отсос пыли. Подошва фрезера может быть выполнена из штампованного металла либо быть литой.
Как изготовить ламельный фрезер самостоятельно
В условиях кризиса сегодня не всегда домохозяин может позволить себе купить полноценный фрезер. Поэтому мы рассмотрим способ, как можно выкрутиться из этого положения с помощью обыкновенной «болгарки» с диском, нескольких листов фанеры или оргстекла, ну и, конечно же, ваших рук и смекалки.
Изготовить такой инструмент самому можно из обычной болгарки или иначе УШМ. Желательно, чтобы она имела регулируемые обороты ротора. Это необходимо для того, чтобы была возможность выставить требуемую скорость вращения диска. В исключительном случае подойдет машинка под 125 диаметр круга.
Помимо этого, нам потребуется ламельная фреза. В качестве материала для корпуса подойдет фанера или же оргстекло, которое предварительно можно отполировать. Основной корпус с боковыми пазами состоит из двух боковых и задних стенок. Верхняя и нижняя части здесь отсутствуют, сама же болгарка с ламельным диском вставляется в пазы боковых стенок вырезанными из дерева направляющими, прикрепленными к ней с двух сторон сбоку. Для регулировки высоты распила ламелей необходимо сконструировать простейшее подъемное устройство. При отсутствии необходимости в регулировке высоты, инструмент можно просто зафиксировать на определенной высоте. Оставшаяся боковая стенка фиксируется к УШМ с помощью болтов, вкручиваемых в резьбу под держатель.
Ознакомившись с данным материалом, вы сможете самостоятельно собрать себе такой инструмент, потратив время и силы, но сэкономив свои финансы. Мы искренне надеемся, что вам понравилась наша статья!
pro-instrument.com
это обработка материалов, и что такое фрезеровка лазером
Фрезерование – это вид обработки деталей с помощью фрез вручную или на станке.
В наше время фрезеровка имеет такое же распространение, как токарная обработка детали либо сверление.
Процесс фрезерования заготовки, выполненной из различного материала, заключается в обработке заготовки с помощью фрезы.
Фреза – это режущий инструмент, выполненный в виде зубчатого колеса, имеющего множество лезвий, который зажимается во фрезерном станке и, вращаясь с большой скоростью, снимает слои поверхности заготовки в нужном вам месте.
Обработка заготовки на станке
Раньше сам фрезерный станок работал лишь вручную, поэтому велик был процент брака.
С применением новых технологий и программирования появились новые фрезерные станки – с программным числовым управлением, использование которых облегчило и упростило работу фрезеровщиков.
Сейчас стал доступен и применен новый вид обработки – с помощью лазера, так на новых станках рабочий орган (фреза) полностью заменили на лазер. Лазер дает более точную обработку заготовки и соответственно меньший процент брака.
Лазерная обработка поверхности заготовки позволила совместить в один процесс обработку на токарном и фрезерном станках, и теперь появился новый термин «фрезерно-токарная обработка материала».
Классификация фрезерных работ
Четкого разделения этого вида обработки нет из-за того, что выполняемые вами работы очень разнообразны.
Существует разделение по типу станка:
- Лазерная обработка.
- Фрезерная механическая обработка.
Из основных видов можно указать следующие:
- по расположению на станине обрабатываемой заготовки – вертикальная, горизонтальная фрезеровка и фрезерование под определенным углом;
- по виду применяемой фрезы – концевая, торцевая, фасонная, периферийная;
- по направлению вращения режущего инструмента относительно движения заготовки – встречная или попутная.
Последний тип классификации используется для обработки больших заготовок, когда первичное фрезерование детали выполняется встречным видом обработки, а для окончательной доводки применяется попутный вид.
Технология процесса фрезеровки
В зависимости от типа станка, сложности обрабатываемой заготовки, материала применяемой детали различается и сама технология, по которой происходит фрезерная обработка.
Технология процесса фрезеровки на обычном станке
Вначале фрезеровщик производит подбор фрезы, которая надежно крепится на шпинделе фрезерного станка.
Обработка заготовки начинается с подготовки:
- включается небольшое вращение шпинделя, при этом деталь подводится к самой фрезе до наименьшего соприкосновения с ней;
- станина стола с закрепленной заготовкой отводится и вращающийся шпиндель останавливается;
- устанавливается необходимая глубина резки детали;
- включается вращение фрезы;
- станину стола с обрабатываемой деталью вручную перемещают до соприкосновения с вращающейся фрезой.
Фрезеровщику для работы над одной заготовкой необходим набор фрез, это позволяет увеличить производительность выполняемой им операции.
Размеры рабочего инструмента (фрез) выбираются, исходя из необходимого стандарта точности, так, для чернового вида фрезеровки необходимо достичь одиннадцатого или двенадцатого квалитета точности, а при заключительном этапе фрезеровки – 8 или 9.
В особых случаях согласно заданию точность размера может соответствовать 7 или 8 квалитетам.
Фрезерная обработка на станке с числовым программным управлением (ЧПУ)
Фрезерование с применением ЧПУ начало внедряться в производство не так давно, ее родоначальником можно считать систему рычагов, которая использовалась на обычных фрезерных станках.
С развитием электроники и вычислительной техники управление фрезерным станком было отдано компьютеру. Так фрезеровщик стал оператором ЧПУ, а для его взаимодействия со станком были написаны программы.
Обработка материала на станке ЧПУ позволяет увеличить точность, увеличить производительность, снизить процент брака, а также наладить выпуск серийных деталей со сложной геометрической поверхностью в большом количестве.
Компьютер задает станку и количество оборотов шпинделя, и параметры его движения (линейные координаты и глубина фрезеровки).
Современные ЧПУ станки могут выполнять 3D фрезеровку – это обработка детали несколькими рабочими органами одновременно, при этом находясь в разных плоскостях.
Перед началом работы, оператор предварительно на компьютере строит 3D-модель детали, станок затем воспроизводит ее с максимальной точностью.
На станке с ЧПУ к квалификации фрезеровщика предъявляются совсем иные требования.
Лазерная обработка детали на станке с ЧПУ
В современной обработке детали лазером он применяется лишь на станке с ЧПУ.
Это оборудование самое дорогостоящее, цена за работу выше, чем на фрезерном обычном станке, но лазерная обработка детали позволяет получить максимальную точность, значительно снижая при этом время на изготовление единицы детали.
Лазерным ЧПУ станкам под силу как точное фрезерование обычного материала, так и изготовление сложных объемных геометрических деталей, исключение лишь только составляют сферообразные округлые конструкции.
Лазерное фрезерование заготовки может выполняться двумя вариантами:
- В нужном месте станок с помощью теплового лазера выжигает заготовку, по окончании процесса выжигания шлифуется кромка.
- Шлифовочный лазер, снимает понемногу слои материала детали, многократно проходя по одному и тому же месту.
Лазерная обработка заготовки оставляет верхний слой гладким, без заусениц, это позволяет не производить дополнительную операцию – шлифование уже готовой вашей детали.
Фрезерование деталей выполненных из титана
Титан, как материал для деталей, все чаще используют в аэрокосмической отрасли. Титан один из самых трудных материалов для металлообработки режущей фрезой, так как он обладает низкой теплопроводностью.
То есть вовремя процесса фрезерования титана лишь небольшая часть тепла уходит со снимаемой стружкой, а это вызывает хороший нагрев как деталей фрезерного станка, так и самой заготовки.
Несмотря на все трудности с фрезерованием титана, для качественной обработки материала фрезеровщики дают немного дельных советов:
- максимально необходимо уменьшите площадь контакта заготовки из титана и фрезы;
- тщательно нужно следить за фрезой, ее режущая кромка должна быть остротой;
- применяйте фрезы с большим количеством зубьев;
- придерживайтесь позиции «только тонкая стружка»;
- начало фрезеровки производите по дуге;
- в конце прохода фрезы снимите фаску под 45°;
- применяйте фрезы с большим дополнительным задним углом;
- скрупулёзно наблюдайте за осевой вашей глубиной;
- если деталь тонкая необходимо уменьшить осевую глубину фрезерования;
- выбирать необходимо фрезу, диаметр которой не более 70% от диаметра выбираемого паза;
- для фрезеровки заготовки из титана необходимо применять высокоскоростные фрезы.
Цена на фрезеровочные работы во многом зависит от геометрии детали, вида фрезерного станка и материала вашей заготовки.
Фрезеровка материала должна производиться на исправном фрезерном оборудовании, специально прошедшем обучение персоналом.
Обращаясь за услугами фрезеровки, поинтересуйтесь, какие фрезерные станки использует фирма, уточните у знакомых или друзей репутацию исполнителя, тогда качество выполненной работы вас не разочарует, не покажется завышенной цена.
Оцените статью: Поделитесь с друзьями!stanok.guru
Слово ФРЕЗЕР — Что такое ФРЕЗЕР?
Слово фрезер английскими буквами(транслитом) — frezer
Слово фрезер состоит из 6 букв: е е з р р ф
Значения слова фрезер. Что такое фрезер?
Фрезер
Фрезер, фрезерная машина — ручной деревообрабатывающий электроинструмент для фрезерования — фигурной обработки кромок, вырезания пазов и сверления отверстий. Вертикальный (погружной) — используется для любых видов фрезеровок.
ru.wikipedia.orgФРЕЗЕР — инструмент с вращательным движением, по образующим или по торцам к-рого расположены режущие ребра — зубцы. Ф. служит для обработки всякого рода поверхностей, нарезки зубьев, шестерен разных профилей и т. п.
Технический железнодорожный словарь. — 1941Фрезер торфяной
Фрезер торфяной (a. peat miller; н. Frastorf; ф. outil de fraisage de la tourbe; и. fresadora de turba) — машина для поверхностно-послойного измельчения торфяной залежи.
Геологический словарь. — 1978ФРЕЗЕРА ДИАГРАММА
ФРЕЗЕРА ДИАГРАММА — способ получения интерполяционных формул по узлам х 0, x0+h, х 0-h, x0+2h, x0-2h,… в точке x=x0+th, основанный на соотношении. где -конечные разности функции f(х), а -биномиальные коэффициенты.
Математическая энциклопедия. — 1977-1985Фрезер (платформа)
Фре́зер — пассажирская железнодорожная платформа Казанского направления Московско-Рязанского отделения Московской железной дороги на территории Москвы.
ru.wikipedia.orgШоссе Фрезер
Шоссе́ Фре́зер (название с 1930 года) — шоссе в Москве, на территории района «Нижегородский» (исторический район Карачарово) Юго-Восточного административного округа. Проходит параллельно Малому кольцу Московской железной дороги…
ru.wikipedia.orgПроезд Фрезер
Прое́зд Фре́зер — проезд, расположенный в Восточном административном округе города Москвы на территории района Перово. Проезд получил своё название в 1996 году по близости к платформе Фрезер Рязанского направления Московской железной дороги.
ru.wikipedia.orgМосковский завод режущих инструментов «Фрезер»
Московский завод режущих инструментов «Фрезер» им. М. И. Калинина, крупнейшее предприятие инструментальной промышленности СССР. Специализируется на крупносерийном производстве стандартного и специального режущего инструмента…
БСЭ. — 1969—1978Русский язык
Фре́зер, -а.
Орфографический словарь. — 2004Фре́з/ер/.
Морфемно-орфографический словарь. — 2002- фрезеруется
- фрезеруются
- фрезерующий
- фрезер
- фрезия
- фрезование
- фрейдизм
wordhelp.ru
Для чего нужен фрезер
Для начала, рассмотрим, что же представляет из себя фрезер. Это электроинструмент, который предназначен для фрезерования различных пазов. Также применяется в снятии фаски, очень удобен для фрезерования отверстий. В основном, фрезер используется при работе с различными породами древесины.
Однако, если прибор оборудовать дополнительными специальными фрезами, то есть режущими частями, то его можно использовать и резки металла, а также различного пластика. По сути, фрезер это достаточно много функциональный прибор, который используется для выполнения очень большого списка различных операций.
Для чего нужен фрезер, как его использовать?
В большинстве случаев, фрезер используют в обрабатывающей промышленности. Он нашел применение при монтаже различной мебели, такой как шкафы, комоды и т.д. Прибор часто используется для фрезерования разного диаметра отверстий под установку петли,применяется и при подготовке мебельных изделий под стяжку. Фрезер также используют для создания отверстий в межкомнатных дверях, в которые вставляются дверные ручки и петли.
Использовать прибор в дизайне интерьера очень удобно и практично. Например, такая работа, как обшивка деревом стен помещения, работа по облицовке фасада здания, а также иные работы такого типа, практически не возможны без применения фрезера. При установке дверей, им необходимо придать аккуратный вид. Края дверей, которые примыкают к стене, необходимо обработать, и тут на помощь приходит фрезер. Именно с его помощью можно создать достаточно эстетический вид устанавливаемых дверей.
Использование фрезера для декоративных целей.
Если необходимо выполнить работы по фрезерованию поверхности некоторых декоративных изделий, то вопрос, для чего нужен фрезер, автоматически отпадает. Прибор просто незаменим, если необходимо создание различных рисунков и узоров на двери шкафа, и т.д. Также, прибор применяют для декорирования поверхности различных пород дерева, изделий из металла, есть возможность нанесении разных рисунков на отделочную поверхность.
Если Вы решили приобрести фрезер, лучше всего, для начинающих, купить высококачественный погружной прибор. Именно такая модель, способна охватить самый разнообразный спектр фрезерных работ, а это практически 80% всех возможных операций фрезера. Современные фрезеры оснащены защитой от попадания щепок, позволяют регулировать скорость работы, очень просты в эксплуатации.
steelserie.ru
Какой ручной фрезер выбрать, на что обратить внимание?
Любой домашний мастер в комплекте своих инструментов обязательно должен иметь ручной фрезер. Большинство людей считает, что с помощью этого инструмента можно работать только по дереву, но это не так. Есть разная оснастка, установка которой на фрезер позволяет им работать с такими материалами, как пластик, цветной металл, искусственный камень и другими. В зависимости от задач, что вы планируете выполнять этим инструментом, будет зависеть то, какой ручной фрезер надо выбрать.
Ручным фрезером можно обрабатывать детали из дерева, пластика, искусственного камня, цветного металла.
Возможности ручного фрезера
Этот инструмент имеет достаточно широкий перечень возможностей, и перед тем как выбрать фрезер ручной, необходимо с ними ознакомиться:
Ручным фрезером можно выполнять фигурную резьбу по дереву.
- профилирование кромки, оно может быть как прямым, так и фигурным;
- выполнение посадочных мест для разных замков, навесов и любой фурнитуры;
- проведение выборки четверти;
- выполнение шлифования;
- сверление отверстий и нарезание шипов;
- отрезание необходимой длины заготовки;
- проведение чернового выравнивания;
- резьба по дереву и гравировка;
- проделывание канавок вдоль или по спирали на ножках, балясинах;
- выполнение различных пазов, шлицов.
Это незаменимый инструмент для людей, занимающихся изготовлением мебели, столяров, строителей, выполняющих отделочные работы, он нужен как любителю, так и профессионалу.
Вернуться к оглавлению
Какие бывают виды ручных фрезеров?
Перед тем как выбирать фрезер, необходимо знать, что они делятся на верхние, кромочные и ламельные.
Кромочный фрезер можно использовать для снятия фасок и выполнения кромок.
Верхний фрезер. Этот вид указанного инструмента может быть неподвижным или погружным. Первый вариант выполнен в виде двигателя, в котором имеются настройки глубины фрезерования, что выполняется за счет перемещения инструмента по вертикали. Использовать такой фрезер сложно, это объясняется тем, что положение фрезы вам придется менять, не проводя ее выключение.
В погружном варианте перемещение двигателя выполняется по направляющей. Инструмент опускается или поднимается за счет действия пружин, при этом вам не надо отрывать его от заготовки. Таким инструментом намного удобнее работать, и он подойдет как профессионалам, так и новичкам.
Кромочный фрезер. Данный тип инструмента обычно используют для выполнения кромок и снятия фасок.
Ламельный фрезер применяется для изготовления пазов.
Ламельный фрезер. Имеет более узкую специализацию и в основном применяется для изготовления пазов.
Независимо от того, какой ручной фрезер вы решили приобрести, все они в комплекте имеют различные вспомогательные приспособления. Это позволяет более производительно выполнять работу, для более точной подачи используются упоры, зажимы, также для этих целей применяются шаблоны и направляющие.
Вернуться к оглавлению
На что обращать внимание во время выбора фрезера?
При совершении выбора фрезера необходимо обращать внимание на многие его параметры и характеристики, только в таком случае вы выберете качественный инструмент, который будет работать долго и надежно.
Мощность инструмента. Этот показатель будет зависеть от того, в каких целях вы планируете использовать фрезер. Чтобы им было удобно работать, надо подобрать оптимальное соотношение между его весом и мощностью.
Правильное направление при работе фрезером.
Легкие фрезеры имеют минимальный вес, но и мощность их всего до 750 Вт. Средние фрезеры имеют мощность уже до 1100 Вт. Тяжелые фрезеры имеют большой вес, но и мощность у них больше 1200 Вт. Поэтому вес инструмента будет напрямую зависеть от его мощности, чем он мощнее, тем будет тяжелее.
Если вы планируете использовать этот инструмент дома, то вам будет достаточно легких или средних моделей, если же вы профессионал, то сразу приобретайте тяжелую и мощную модель.
Скорость. От указанного показателя будет зависеть материал, с которым можно работать этим инструментом, будет это только дерево или другие материалы. Скорость фрезера может быть 7-24 тысячи оборотов в минуту. Для бытового использования достаточно глубины работы 30 мм, у профессиональных моделей она может достигать 60 мм.
Включатель. Этому устройству многие люди при совершении выбора ручного электрического инструмента не уделяют внимания, но делают это зря. Данное устройство обязательно должно иметь фиксирующий механизм, а также защиту от его случайного включения. Наличие таких функций не только намного облегчит работу, но обеспечит безопасность оператора во время выполнения им работы.
Для разных работ используются разные виды фрез.
Цанга. Самыми лучшими считаются конусовидные стальные цанги, это объясняется тем, что вал двигателя имеет конусообразную форму, и они идеально подходят друг другу. Это устройство должно быть сделано из закаленной стали, если была использована обыкновенная сталь, то во время работы она быстро изнашивается, и появляется дребезжание, что усложняет работу.
Удаление пыли. Почти все современные фрезеры имеют шлюз для отсоса пыли, что возникает во время работы. Чтобы обеспечить максимальное удаление пыли, указанный механизм должен быть встроенным. Наличие шлюза может немного ухудшать видимость, но если работать на специальном столе, то он не мешает, и рабочее место постоянно остается чистым.
Если говорить о столе, на котором проводятся работы, то он должен быть прочным, иметь точки крепежа, на нем должна быть система регулировки высоты, и его конструкция должна обеспечивать максимальную видимость.
Подошва фрезера. Одним из основных элементов указанного инструмента является подошва. На большинстве моделей она штампованная, более дорогие модели имеют литую подошву. Чтобы работа выполнялась легко, подошва должна иметь правильную форму и хорошо прилегать к основе. Базовая опора является местом, где находятся проушины направляющих деталей. Подошва закрывается накладкой, которая может быть пластиковой или деревянной. Большое значение имеет размер отверстия, так как от этого зависит размер фрезы, что можно использовать.
Штанговый механизм. Производительность и функциональность этого инструмента будет зависеть от того, как будет перемещаться «голова», она движется по штангам. Исправная работа данного механизма обеспечивает плавное и легкое перемещение фрезы. Для регулирования глубины погружения фрезы может быть использован рычаг или винт. Качество инструмента будет зависеть от точности указанной регулировки.
Револьверный упор помогает выполнять несколько оборотов с изменением глубины. Для перенастройки глубины погружения используется ответная часть упора. Удобно, когда она сделана в виде болтов, при вкручивании которых и происходит изменение высоты.
Вспомогательные детали. Мы рассмотрели основные моменты, на которые надо обращать внимание при выборе фрезера, но также необходимо обратить внимание и на дополнительные детали.
Для того чтобы была возможность максимально точно выполнять работу, используются различные направляющие, они входят в комплектацию инструмента.
Для того чтобы вести фрезер на равном удалении, используют параллельный упор. Он должен быть изготовлен из качественной стали, может состоять из 2 элементов или занимать всю опорную площадку, между упором и заготовкой должна быть пластиковая накладка.
Копировальное кольцо представляет собой пластину, на которой есть бортик, оно вставляется в специальный проем подошвы. Фиксация конструкции должна быть быстрозажимной, чтобы исключить дополнительные движения детали при ее позиционировании.
Угловой упор позволяет выполнять копирование заготовки. Деталь размещают над шаблоном, а фреза опирается на щуп. Более удобно, когда есть возможность его регулировки.
Вернуться к оглавлению
Некоторые советы для совершения правильного выбора
Если вы планируете применять фрезер в домашних условиях и при ручном использовании, то не стоит брать инструмент большой мощности. Очень удобно, когда в выбранной вами модели есть возможность регулировать скорость. Чтобы исключить случайное перемещение колесика, оно должно двигаться с усилием и ступенчато.
Оптимальным вариантом при определении глубины погружения является тот, когда цанга не выходит за основную конструкцию, максимум она может доходить до низа подошвы.
Выполнение пазов некоторыми видами фрез.
Большое значение имеет эргономика инструмента. Рукоятка должна быть удобной для вас, короткий шнур предусматривает обязательное использование удлинителя, что не совсем удобно.
При совершении покупки попробуйте работу цангового механизма. Головка должна перемещаться легко, без люфта и перекоса. Надо, чтобы вертикальный упор надежно фиксировался в необходимом положении.
Проверьте, как устанавливаются дополнительные компоненты, насколько жестко и надежно они крепятся, есть ли зазоры. Если вы предпочитаете работать без направляющих, то выберите модель, которая имеет максимальный обзор. При этом надо обращать внимание на размещение пылеотсоса, наличие подсветки и другие элементы, что могут ухудшать обзор.
Во время проверки работы прибора наличие вибрации или посторонних шумов как на холостом ходу, так и при нагрузке, будет указывать на плохое качество его сборки.
Некоторые пользователи считают, что профессиональный инструмент сделан очень качественно, а бытовой только так, чтобы мог включаться и работать, но они неправы. И те и другие могут быть как качественными, так и не очень высокого качества, все зависит от производителя.
Основным отличием профессионального инструмента является наличие большого количества различных приспособлений. Если в бытовых инструментах втулки могут быть полимерными, то в профессиональных моделях они сделаны из цветного металла, что значительно увеличивает их срок службы.
В профессиональном инструменте подшипники не устанавливают в пластмассу, они ставятся в металлические гильзы, поэтому после нагрева в них не появляется люфт.
Еще один момент: если профессиональным фрезером можно работать на протяжении 8 часов, то при использовании бытового инструмента надо 15 минут работать, а затем на такое же время давать ему отдохнуть.
Вы ознакомились с основными параметрами и характеристиками фрезера, на которые необходимо обращать внимание, чтобы выбрать качественный и надежный инструмент.
moiinstrumenty.ru
Фрезерование. Основные виды и методы данной обработки металла
Привет! Вот и новая статья которая называется фрезерование и его основные виды потому, что с нее мы начнем изучение этого не простого метода обработки металла.Что такое фрезерование?
Фрезерование — это обработка создающая плоские и фасонные поверхности , путем применения такого режущего инструмента как фреза. Можно много сказать еще про этот вид механической обработки но я думаю, что мы с вами поэтапно будем рассматривать все его составляющие. И когда закончим (что очень не скоро:)) вы будете знать про него практически все.
Фрезерование.Основные виды и методы.
Я не хочу грузить вас теорией и скучными определениями которых и так полно во всякой литературе посвященной резанию металлов. Просто хочу пока рассказать про основные виды фрезерования. И так…
Фрезерование цилиндрической фрезой. Ну как уже понятно из названия для данного метода применяется цилиндрическая фреза. Суть метода заключается в обработке плоских поверхностей правильной формы (квадраты,прямоугольники и др.) Углубляться не будем, пока:).
Фрезерование торцевой фрезой. Этот метод в принципе аналогичен предыдущему но разница в том, что тут для получения таких же поверхностей применяется торцевая фреза. В чем их различие разберемся в следующих постах. Так, что не забываем подписываться на обновления блога.
Фрезерование зубчатого колеса. Что качается изготовления зубчатого венца методом фрезерования на горизонтально-фрезерном станке, то скажу вам сразу, что данный метод давно устарел и применяется разве, что в ремонтных цехах так как он не имеет необходимой производительности и качества получения шестерни. К стати получение зубчатых колес мы тоже будем рассматривать:)
Фрезерование уступа дисковой трехсторонней фрезой. Как уже понятно с названия снятие припуска производится трехсторонней дисковой фрезой. Которая называется так потому, что имеет сразу три режущие кромки — по наружному диаметру и сразу с двух торцев. Это позволяет ей фрезеровать уступы как показано на рисунке.
Фрезерование набором двух трехсторонних дисковых фрез. Этот метод похож на предыдущий но разница в том, что в данном случае производится одновременная обработка двумя фрезами, что очень удобно для изготовления лысок на цилиндрических поверхностях.
Фрезерование паза концевой фрезой. Используется данный вид для получения прямобочных пазов различных размеров и конфигураций как на плоских так и цилиндрических деталях.
Фрезерование пазов шлицевой фрезой. Ну тут скажу, что под шлицевыми пазами подразумеваются шлицы. Данный методом тоже устарел так как является низко производительным и не дает достаточной точности получения детали. Деление осуществляется с помощью делительной головки.
Фрезерование фасонной поверхности. Под фасонными поверхностями как вы уже поняли из моего предыдущего поста про токарную обработку. Это поверхности которые имеют не совсем правильные «фасонные» формы (эллипсы, сферы и др.). И как следствие для их получения необходимы специальные фрезы которые и называют фасонные (имеющие форму которую необходимо получить после фрезеровки).
Фрезеровка наклонной плоскости. Угловые фрезы тоже работаю по принципу копирования, а именно получаемая наклонная поверхность обеспечивается точностью изготовления режущего инструмента. Этот метод применяется для изготовления направляющих скольжения металлорежущих станков.
Фрезеровка криволинейного контура. С помощью концевой фрезы мы сможем получить практически любой сложный криволинейный контур. Тут фреза описывает обрабатываемую деталь по кривой линии которую нам необходимо получить.
Фрезеровка винтовых канавок. С помощью данного способа фрезерования как видно из предлагаемого эскиза изготавливают сверла, зенкера и другой инструмент имеющий винтовые стружкоотводящие канавки. В основном эти операции выполняются на станках с ЧПУ (в настоящее время).
Разрезание отрезной фрезой. Ну в данном случае название говорит само за себя. С помощью отрезной фрезы можно нарезать металлические бруски различных размеров.
Ну все на сегодня информации пожалуй хватит. Я думаю, что не плохо расписал про фрезерование и его основные виды. Если у вас есть какие то предложения чем можно дополнить данный пост ПИШИТЕ!!!
С вами был Андрей!
mextexnologii.ru
Что такое кромочный фрезер?
Во-многих статьях журналов и на сайтах, посвященных столярному делу, упоминаются кромачные фрезеры. В наших интернет-магазинах можно встретить только фрезеры брендов Bosch, Makita, AEG, RYOBI, DeWALT, ВИХРЬ и др., но менее известен инструмент под брендом Virutex.
Этот инструмент решает задачи по обработке кромок, устройству пазов, узоров и декоративных элементов. Выбор среди множества моделей осуществляется с учетом технических характеристик инструмента и индивидуальных потребностей покупателя. Рассмотрим подробнее на примере фрезеров Virutex моделей: FR156N, FR192N, AS93, FR256N, FR256S и FR292R.
Фрезеры кромочные
Кромочные фрезеры Virutex FR156N, Virutex FR192N, Virutex AS93 оснащены мощными двигателями и удобными конструкциями. Их отличие между собой заключается в мощности двигателя, толщине обрабатываемых кромок, наличии дополнительных возможностей. Например, FR192N способен удалять свесы толщиной в 1 мм, а FR156N может обработать прямоугольные кромки за один подход и сохранять настройки при смене фрезы. Кромочный фрезер AS93 отличается от представленных моделей повышенной мощностью двигателя, габаритами конструкции и возможностью интенсивной и долгой работы.
Фрезеры универсальные
Фрезеры для снятия свесов представлены моделями Virutex FR256N и Virutex FR256S. Стандартный кромочный фрезер FR156N, при сочетании его со специальной насадкой CA56U, становится универсальной моделью фрезера FR256N с увеличенной площадью основания. Использование данного фрезера удобно возможностью менять положение инструмента относительно обрабатываемой детали и качеством обкатки углов.
Фрезер FR256S способен при работе материалами разной плотности стабилизировать и контролировать обороты. Кромочный фрезер обрабатывает свесы на прямолинейной и криволинейной поверхности, фрезирует свесы за один проход со всех сторон.
Фрезер универсальный, представленный моделью Virutex FR292R, укомплектован наклонной базой, позволяющей использовать его и в качестве обыкновенного вертикального механизма, и для работы с кромками. Преимущество инструмента в его многофункциональности и возможности подгонки фрезы по вертикальной или торцевой плоскости. Нет необходимости в перенастройке инструмента для выполнения различных задач.
Какой лучше?
При интенсивном и разнообразном использовании фрезера лучше приобретать универсальную модель. Но если столярные работы производятся на высокопрофессиональном уровне и в больших объемах, включая специфические работы, стоит подумать о приобретении нескольких инструментов.
Оцените:
Загрузка…Сообщите друзьям:
Обратите внимание
www.stroitelstvo-domov.net
Как и какой выбрать фрезер и что им можно сделать | Своими руками
Общее представление об электрических лобзиках, дрелях и шуруповертах, пожалуй, есть у всех.
А вот вопрос «Что умеет фрезер?» порой ставит в тупик даже продвинутых пользователей обычных бытовых инструментов». И в этом нет ничего удивительного. До недавнего времени фрезеры были представлены только в профессиональных линейках инструментальной продукции. Между тем вещь эта — весьма полезная, а зачастую и совершенно необходимая в арсенале домашнего мастера.
Зачем нужен фрезер
Без фрезера невозможно качественно изготовить мебель по авторским эскизам или замысловатую поделку из дерева. Конечно, опытный мастер обойдется и неспециализированным инструментом, но в таком случае потребуется гораздо больше труда и времени при непредсказуемом конечном результате.
Наиболее востребованные в любительской среде вертикальные фрезеры способны выполнять множество различных операций. Они вырезают в деревянных изделиях и деталях пазы, кромки, шлицы, снимают фаску, выбирают четверти. К тому же вертикальные фрезеры используют для изготовления продольных кромок и формирования сложных соединений на шипах (прямых или типа «ласточкин хвост» – о нем мы упоминали в статье “Каркас своими руками”) и шпунтах.
«Спецы» по фрезеровке
Универсальность имеет и обратную сторону. Бесспорно, вертикальные фрезеровочные машины умеют многое, но ими неудобно пользоваться в стесненных условиях. Тут нужны компактные кромочные фрезеры.
Подобные инструменты легко держать даже одной рукой. При этом они обеспечивают высокую точность обработки — снимают кромку без сучка и задоринки и строго под заданный размер. Положение фрезы изменяется с помощью масштабной шкалы и регулировочного колесика.
Если нет уверенности, что для кромочного фрезера найдется много работы, то следует присмотреться к комбинированным фрезерам. Подобные машины комплектуются двумя базами — для погружного фрезерования и обработки кромок. Правда, в сложной обстановке кромочный фрезер все-таки удобнее.
Мебельщику
Также в продаже имеются дюбельные фрезерные машины, которые еще называют присадочными или ламельными. Подобные инструменты используют для фрезерования пазов под плоские дюбели для угловых и кромочных соединений (ламельные фрезеры), а также выборки отверстий под мебельные шканты и дюбели (присадочные фрезеры).
Это стандартная операция при изготовлении мебели. Надо сказать, что выполнение пазов обычным инструментом — весьма утомительное занятие. А с присадочным фрезером все решается в кратчайшие сроки и к тому же с безупречным качеством.
Ссылка по теме: Работ с ламельным фрезером – что им можно сделать
Паркетчику
На производственных площадках и в строительстве используют специализированные фрезеры для обработки ламината, и паркетной доски. Их называют триммеры. В быту подобные устройства вряд ли пригодятся. Что делать, если все-таки по какой-либо исключительной причине домашний мастер никак не может обойтись без такого «экзотического» фрезера? Взять его в аренду, конечно же!
Для каких бы целей вы ни выбирали себе машину, покупаете ее или берете напрокат, прежде чем принимать окончательное решение, примеритесь к приглянувшейся модели. Подержите ее в руках, оцените эргономичность рукоятки, а также удобство расположения выключателя и других элементов управления.
О здравом смысле
Серьезные модели фрезеров стоят недешево. Нет далеко идущих планов — стоит ли вообще приобретать такую машину? Другое дело, если вы собираетесь обставить дом предметами мебели ручной работы. Начинать этот масштабный проект разумно именно с приобретения удобного, надежного и практичного фрезера.
Конечно, новичку следует осваивать основы мастерства на небольших изделиях — тумбах, маленьких столиках, декоративных ящичках и шкатулках. Однако, как известно, аппетит приходит во время еды, и эта французская поговорка как нельзя лучше подходит к столярному ремеслу. Тому, кто чувствует в себе потенциал творца, и модель нужна с большим техническим и креативным потенциалом.
Как выбрать фрезер – критерии
Мощность машины. Чем больше этот показатель, тем выше производительность фрезера и тем шире его возможности. Но в отношении мощности следует проявлять чувство меры и не увлекаться «тяжелыми» моделями на 2 кВт и более.
Число оборотов.
При покупке стоит отдавать предпочтение моделям с электронной регулировкой частоты оборотов. Эта опция позволяет точно подобрать режим работы инструмента в зависимости от типа операции и вида материала.
Читайте также: Ленточно-шлифовальный станок своими руками
Глубина погружения фрезы.
У профессиональной техники этот показатель достигает 60 мм и более. Глубина реза «завязана» на мощности и, как следствие, тяжеловесности инструмента. Если фреза погружается на разную глубину, значит, пользователь может более точно выполнять обработку материала (этому способствует фиксатор глубины и упор глубины опускания фрезы).
Параллельный упор.
Он упрощает выполнение операции по снятию кромки. (Фиксатор и упоры входят в основную комплектацию инструмента.)
Возможность безопасной и легкой смены фрез разного диаметра (6 и 8 или 12 мм).
В качественных ручных фрезерах обязательно предусмотрена такая замена. Реализуется она посредством цангового патрона или других фирменных приспособлений (например, встроенной блокировки шпинделя в моделях от компании Bosch).
Револьверная головка.
Она позволяет быстро изменить высоту опускания фрезы, что помогает качественно и быстро выполнить обработку в несколько проходов.
Набор
В комплект профессиональных фрезеров нередко входят вспомогательные детали и изделия. Вместе с тем многие мастера предпочитают собирать оснастку самостоятельно, по своему вкусу и опыту. Применение фрез разной конфигурации и назначения позволяет создавать подлинные шедевры — предметы с ажурной резьбой и изысканным рельефом. Постепенно вокруг универсального вертикального фрезера собирается целое семейство «помощников» — инструментов и приспособлений (направляющих, шаблонов и т. д.) для специфических операций и эксклюзивной обработки.
На заметку:
Желательно, чтобы фрезер имел специальные противоскользящие мягкие накладки. При выполнении большого объема работ удобнее, когда выключатель встроен в рукоятку. Полезная деталь — патрубок для подсоединения пылесоса для сбора опилок и стружки. И, наконец, подсветка зоны фрезерования. Локальное освещение повышает комфортность работы и положительно влияет на настроение мастера.
Свое название вертикальные фрезеры получили из-за расположения двигателя и фрезы. В таких машинах двигатель установлен сверху — над основанием инструмента. Эти два узла соединены между собой особым подъемным механизмом, посредством которого производится регулировка глубины погружения фрезы в материал.
Если ручную фрезеровочную машину закрепить в столярном верстаке или хотя бы стойке для электродрели, то получится полустационарный деревообрабатывающий станок. При определенной сноровке с его помощью можно делать потрясающие вещи.
Читайте также: Усовершенствование циркулярки – делаем пилу удобнее
Виды фрез
Главная деталь
Рабочим органом фрезеровочной машины или станка служит фреза — приспособление с несколькими режущими лезвиями или зубьями. Существует множество разновидностей фрез:
Виды фрез для фрезера (наиболее часто используемые в работе) | |
№ | Название |
1. | дисковые; |
2. | конические; |
3. | торцевые; |
4. | угловые |
5. | червячные; |
6. | цилиндрические; |
7. | шпоночные и др. |
Изготавливают их из стали, твердых сплавов, металлокерамики, алмаза, массива кардной проволоки. Есть устройства, с помощью которых обрабатывают не только дерево, но и материалы куда как потверже, например алюминий, сталь, чугун. Применяются они в серьезных промышленных станках. В домашних же условиях обычно используют ручные электроинструменты для обработки именно древесины.
Наиболее популярные марки фрезеров: Makita (Макита), AEG, Bosch (Бош), Metabo (Метабо), Black and Decker (Блэк энд Дэкер), DeWalt
Ручная фрезерная машинка, или фрезер: виды фрез ,устройство, приемы работы и оснастка
Ручная фрезерная машинка, или фрезер, как её называют многие умельцы, расширяет технологические возможности домашнего мастера. При наличии такого инструмента профессионально выполнить сложнейшие столярные операции гораздо проще.
Фрезерная машинка со штатным комплектом вспомогательной оснастки, набором концевых фрез и дополнительных приспособлений, в том числе и самодельных, позволит владельцу выбрать в деревянных заготовках пазы и шлицы разных размеров и конфигураций, снять фаску, придать сложный профиль кромкам по контуру, изготовить декоративные фасонные планки и нанести гравировку, с высокой точностью врезать дверные петли и замки.
Фрезерную машинку можно применять даже для обработки пластика, оргстекла, композитных материалов и цветных металлов, используя предназначенные для этих целей фрезы и правильно выбрав режим обработки. Рекомендуемые режимы для тех или иных материалов и рекомендации производителя, как правило, содержит инструкция, прилагаемая к инструменту.
Устройство фрезера
Несмотря на внешние различия, фрезерные машинки принципиально устроены одинаково и состоят из двух конструктивных узлов — электропривода с цанговым зажимом и основания с механизмом подъёма-опускания привода.
Цанги для зажимов (и хвостовики концевых фрез) выпускают трёх основных модификаций — 0 6, 8 и 12 мм. Это следует иметь в виду при покупке инструмента и фрез к нему. В комплект машинки обычно включают боковой упор, роликовый упор, пластмассовую или металлическую копировальную втулку, насадку для подключения пылесоса, фиксатор вала и гаечный ключ.
Мощность двигателя — одна из важнейших характеристик фрезерной машинки. В разных моделях она варьируется от 600 до 2 300 Вт.
Чем больше мощность, тем шире возможности машинки. В частности, это позволяет использовать фрезы большого диаметра — например, для профилирования филёнок.
От мощности во многом зависит и стоимость инструмента.
Скорость вращения двигателя, а значит, и фрезы, закреплённой на конце его вала с помощью цангового зажима, у многих моделей регулируется в широком диапазоне. При этом максимальная скорость может достигать 20, а у некоторых моделей даже 35 тыс. об./мин.
Нужно иметь в виду, что при завышенной скорости обработки есть риск перегреть фрезу и «прижечь» ею заготовку, а при заниженной скорости существенно уменьшаются производительность и качество обработки.
Функция плавного пуска позволяет избежать резкой отдачи инструмента при включении. Особенно это ощутимо при использовании фрез большого диаметра.
Ещё одна важная характеристика инструмента — диапазон регулировки глубины фрезерования (рабочий ход фрезы). У разных моделей он составляет от 30 до 76 мм.
Разновидности фрез
Ассортимент фрез к фрезерным машинкам широк и разнообразен. Их продают в розницу и в наборах.
Основные их разновидности: пазовая фреза, фреза для выборки желобка (галтель), фасонная фреза, многорадиусная фасонная фреза, дисковая пазовая фреза, фреза для сращивания заготовок и ещё целая гамма специализированных фрез.
Конструктивно фрезы можно поделить на несколько групп: пазовые погружные; кромочные с направляющей цапфой или подшипником; комбинированные; филёночные; комплекты для формирования рамных соединений. Изготавливают фрезы целиком из быстрорежущей стали или с напаянными режущими элементами из твёрдого сплава. Первые хорошо себя зарекомендовали при обработке заготовок из древесины мягких пород.
Для обработки же древесины твёрдых пород, древесных материалов (ДСП, MDF, фанеры), а также ламинированных заготовок желательно пользоваться фрезами с режущими элементами из твёрдого сплава. Режущие кромки фрез из твёрдых сплавов чувствительны к механическим воздействиям. Поэтому хранить их нужно ни в коем случае не навалом в общем инструментальном ящике. Проще всего работать с фрезами, имеющими направляющую цапфу или подшипник
При этом легко контролировать движение инструмента. Никаких дополнительных приспособлений не нужно — достаточно установить нужную глубину фрезерования. Цапфа или подшипник опирается на ровную кромку заготовки или шаблона — и фреза точно копирует заданную траекторию. Однако на кромке не должно быть никаких изъянов, иначе они в точности повторятся на обработанной поверхности.
Приёмы работы с фрезером
Древесину обрабатывают фрезой из быстрорежущей стали или твердосплавной на высоких оборотах. Обработанные поверхности получаются при этом очень чистыми, но образуется большое количество стружки. Поэтому работать желательно с системой удаления стружки. Револьверный упор каретки механизма регулировки глубины фрезерования, смонтированный на основании фрезерной машинки, позволяет делать несколько повторных проходов одного участка, каждый раз на большую глубину. Качество обрабатываемой поверхности зависит от нескольких факторов. Во-первых, от заточки фрезы — она должна быть острой. Свою роль играет и направление прохода. С наибольшими сложностями связана обработка торцов, а наилучший результат даёт продольное фрезерование вдоль волокон.
Качество поверхности улучшается, если отрегулировать револьверный упор так, чтобы при последнем проходе съём материала был минимальным.
Фрезеровать паз параллельно прямолинейной кромке заготовки или начисто обработанной пласти можно с помощью бокового упора входящего в комплект принадлежностей, или пластиковой накладки на подошву основания машинки в случаях, когда глубина фрезерования не превышает толщины накладки. Но лучше всего пользоваться
фирменной шиной с кареткой, перемещаемой по ней. В крайнем случае годится и самодельная направляющая подходящей длины Роликовый же упор из комплекта принадлежностей гарантирует точное повторение профиля криволинейной кромки. Все эти приспособления обеспечат сохранение фиксированного расстояния паза от базового торца или в соответствии с разметкой, если в процессе обработки постоянно поджимать упор к кромке или основание машинки — к направляющей. Нужно иметь в виду, что все регулировочные и установочные винты должны быть туго затянуты, иначе от высокочастотной вибрации работающего привода первоначальная настройка фрезерной машинки может сбиться, а деревянная заготовка будет загублена.
При фрезеровании пазов и выборок сложной конфигурации выручит копировальная втулка Правда, для выполнения такой операции сначала нужно изготовить точный шаблон с учётом наружного диаметра копировальной втулки. Приспособление-циркуль понадобится при осуществлении криволинейного фрезерования по дуге или окружности.
Дополнительная оснастка фрезера
Применение дополнительной оснастки, в том числе изготовленной самостоятельно, позволит выполнить и другие операции деревообработки быстро и очень качественно.
Так, при изготовлении мебели чаще всего выполняют угловые соединения на шпонках и шкантах, хотя прочнее и солиднее — сделать их на шипах прямых или «ласточкин хвост». А всё потому, что вырезать шипы на ответных деталях вручную — занятие кропотливое и трудоёмкое. Другое дело — фрезерование шипов. Правда, здесь не обойтись без комбинированного приспособления-шаблона
Производители, выпускающие фрезерные машинки, делают такие шаблоны.
Назначение у них — одно и то же, а конструкции отличаются. Поэтому приобретать шаблон нужно той же фирмы, что и машинка в вашей мастерской.
Такие шаблоны кроме направляющей металлической пластины включают в себя кронштейны-зажимы, в которых фиксируются одновременно обе сопрягаемые детали. Очень удобное приспособление, соединившее в себе функции направляющей шины и параллельного упора, — направляющие салазки. Основание фрезерной машинки легко и без поперечного люфта перемещается между брусками по тонким планкам из фанеры
Если натереть боковые ограничивающие бруски воском, основание машинки будет скользить по ним ещё легче.
Фрезер вместо лобзика
Когда требуется сделать в детали круглый вырез, рука сразу тянется к лобзику. Но если нужно сделать много одинаковых вырезов, лучше использовать ручную фрезерную машину. Лобзик тоже понадобится — всего лишь для изготовления шаблона.
Начертим циркулем окружность или нужную часть дуги на листе тонкой фанеры.
С таким материалом лобзик легко справится. А далее за дело возьмётся фрезер с копировальной втулкой.
Закрепив заготовку струбцинами к столу, а шаблон к заготовке — выполняем рез фрезером. Мощный фрезер со спиральной фрезой — это не слабосильный лобзик. Работает быстро, только успевай шаблон двигать! Поверхность вырезов — ровная, нигде ничего не завалено, сколов нет.
Текст: М. Филатова
ИНСТРУМЕНТ ДЛЯ МАСТЕРОВ И МАСТЕРИЦ, И ТОВАРЫ ДЛЯ ДОМА ОЧЕНЬ ДЕШЕВО. БЕСПЛАТНАЯ ДОСТАВКА. ЕСТЬ ОТЗЫВЫ.Ниже другие записи по теме «Как сделать своими руками — домохозяину!»
Подпишитесь на обновления в наших группах и поделитесь.
Будем друзьями!
Что такое фреза?
Фреза — важный компонент фрезерного станка. Как следует из названия, именно режущий инструмент отвечает за соскабливание материала с заготовки. Все фрезерные станки имеют фрезу. Во время типичной операции фрезерования фреза движется перпендикулярно своей оси, позволяя снимать материал с заготовки по окружности фрезы. Чтобы узнать больше о фрезах и о том, как они работают, продолжайте читать.
Обзор фрез
Назначение фрезы — удаление материала с заготовки.При этом фрезы не состоят из одного лезвия. В то время как токарные операции, выполняемые на токарном станке, обычно имеют однолезвийный режущий инструмент, фрезы состоят из нескольких лезвий. Когда фреза вращается относительно неподвижной заготовки, она соскабливает материал.
Фрезы часто изготавливаются из твердых, прочных материалов, которые могут выдерживать значительные нагрузки, не ломаясь или не подвергаясь иным повреждениям. Например, фрезы нередко имеют покрытие из поликристаллического алмаза (PCD).Согласно Википедии, фрезы с покрытием PCD служат до 100 раз дольше, чем их аналоги без покрытия. Загрузка фрез с покрытием из PCD заключается в том, что их нельзя использовать в приложениях, где температура превышает 1112 градусов по Фаренгейту.
Различные типы фрез
Все фрезы характеризуются наличием множества канавок, каждая из которых действует как лезвие, соскабливающее материал с заготовки. При этом существуют разные типы фрез.Режущий инструмент концевой фрезы, например, представляет собой тип фрезы с зубьями на конце и по бокам. Доступные из стали и карбида цемента, они обычно используются при вертикальном фрезеровании.
Другой распространенный тип фрезы — это фреза с черновым концом. Фрезы с грубым концом имеют глубокие канавки на конце, которые позволяют удалить излишки материала с заготовки. Фрезы с черновым концом, также известные как рыхлители, обычно используются в крупносерийном производстве.
Третий вид фрезы — это шаровые фрезы. Шаровая фреза, также известная как фреза со сферическим концом, имеет полусферическую конструкцию, которая сводит к минимуму нагрузку на заготовку.
Наконец, боковая фреза — это тип фрезы, у которой есть зубья по бокам и спереди. Бокорезы существуют с начала 1800-х годов. Фактически, тогда это были самые распространенные фрезы.
Фреза — важный компонент фрезерного станка.Состоящий из нескольких лезвий, он отвечает за соскабливание материала с заготовки, тем самым изменяя форму заготовки.
Фрезы и инструменты — типы и их назначение (с изображениями)
Обработка с ЧПУ — это широко применяемая субтрактивная технология производства. Системы числового программного управления обеспечивают меньшую потребность в рабочей силе и более высокий уровень автоматизации.
Одним из таких автоматизированных методов изготовления является фрезерование с ЧПУ. Это процесс, при котором роторные фрезы удаляют материал, что делает его противоположным токарным станкам с ЧПУ.
Фрезерные центры автоматически выполняют не только резку, но и смену инструмента. В среднем процессе создания готового изделия, например, из металлической глыбы, используются различные инструменты.
Итак, давайте посмотрим, какие фрезерные инструменты используются на станках и для чего они предназначены.
Какие бывают типы фрез?
Наиболее распространенные типы фрез:
- Концевая фреза
- Торцевая фреза
- Шаровой нож
- Слябовый стан
- Фреза боковая
- Эвольвентная зуборезка
- Мухорезка
- Полый стан
- Корпусная фреза
- Концевая фреза для черновой обработки
- Фреза в форме ласточкиного хвоста
- Устройство для обрезки ершей
Во-первых, мы должны начать с одного из основных вопросов.
В чем разница между концевым и торцевым фрезерованием?
Это две наиболее распространенные операции фрезерования, в каждой из которых используются разные типы фрез — фреза и торцевая фреза. Разница между концевым фрезерованием и торцевым фрезерованием заключается в том, что концевая фреза использует как конец, так и стороны фрезы, тогда как торцевое фрезерование используется для горизонтальной резки.
Концевая фреза
У этих инструментов обычно плоское дно, но не всегда.Также доступны круглые и закругленные фрезы. Концевые фрезы похожи на сверла в том смысле, что они могут резать в осевом направлении. Но преимущество фрезерования заключается в возможности поперечной резки.
Торцевая фреза
Торцевое фрезерование
Торцевые фрезы не режут в осевом направлении. Вместо этого режущие кромки всегда расположены по бокам режущей головки. Режущие зубья представляют собой сменные твердосплавные пластины.
Это увеличивает срок службы инструмента при сохранении хорошего качества резки.
Шарорез
Шаровые фрезы, также известные как шаровые мельницы, имеют полусферический режущий наконечник. Цель состоит в том, чтобы поддерживать радиус угла для перпендикулярных граней.
Слябовый стан
Слябовые фрезы не так уж часто используются в современных обрабатывающих центрах. Скорее, они все еще используются с ручными фрезерными станками для быстрой обработки больших поверхностей. Вот почему фрезерование слябов часто называют фрезерованием поверхности.
Сама плита вращается в горизонтальном положении между шпинделем и опорой.
Фреза боковая
Предшественник концевой фрезы. Бокорезы имеют зубья по окружности и с одной стороны. Это делает функциональность очень похожей на концевые фрезы, но их популярность с годами пошла на убыль с развитием других технологий.
Эвольвентная зуборезка
Есть специальный режущий инструмент для фрезерования эвольвентных шестерен. Существуют различные фрезы для изготовления шестерен с определенным количеством зубьев.
Мухорезка
Эти инструменты выполняют ту же функцию, что и торцевые фрезы. Они состоят из центрального корпуса, вмещающего одну или две насадки (двусторонние фрезы).
Торцевые фрезы лучше подходят для качественной резки. Фрезы для мух просто дешевле, и режущие насадки часто изготавливаются в магазине машинистом, а не покупаются в магазинах.
Полый стан
Полое фрезерование
Пустотные фрезы в основном противоположны торцевым фрезам.Здесь заготовка подается во внутреннюю часть фрезы для получения цилиндрической формы.
Концевая фреза для черновой обработки
Как следует из названия, это в значительной степени концевые фрезы с небольшой разницей. Концевая фреза для черновой обработки имеет зазубрины. Это ускоряет процесс резки по сравнению с обычной концевой фрезой.
Обрезанные кусочки металла меньше обычных, поэтому их легче очистить. С заготовкой одновременно контактируют несколько зубцов. Это уменьшает стук и вибрацию, которые в противном случае могли бы быть больше из-за неровностей зубьев.
Фреза по дереву
Woodruff или фрезы для шпоночных пазов и пазов используются для разрезания пазов на детали, например, валы. Режущие инструменты имеют зубья, перпендикулярные внешнему диаметру, для создания подходящих пазов для шлифовальных шпонок.
Резьбовая фреза
Название этого инструмента говорит все, что вам нужно знать о его назначении. Для изготовления резьбовых отверстий используются резьбовые фрезы.
Нарезание резьбы обычно выполняется на буровом оборудовании.Однако использование резьбовой фрезы более стабильно и имеет меньше ограничений для окружающей среды.
Какие материалы используются для режущих инструментов?
Как видите, существует множество различных станков для самых разных целей. То же самое и с материалами, из которых изготовлены эти инструменты.
Давайте копнем глубже и рассмотрим наиболее распространенные материалы для фрезерных бит.
Углеродистая сталь
Самый дешевый из всех. И именно поэтому он до сих пор находит применение.Поскольку углеродистая сталь не очень долговечна, она подходит только для низкоскоростных операций.
Углеродистая стальтеряет твердость при 200 ° C. Это является причиной более низких скоростей — для сохранения низкого теплового эффекта.
Быстрорежущая сталь
Быстрорежущая сталь, марка инструментальной стали, содержит несколько легирующих элементов, которые обеспечивают лучшую реакцию на нагрев и износ, чем обычная углеродистая сталь. По мере того, как жизненный цикл такого инструмента увеличивается, увеличивается и его стоимость.
Теряет твердость при 600 ° С.Поэтому для этих инструментальных сталей подходят более высокие скорости фрезерования.
Твердые сплавы
Этот материал тверже, чем быстрорежущая сталь, но его прочность не так впечатляет. Более высокая твердость обеспечивает лучшую защиту от износа, но более низкие уровни вязкости делают его немного более восприимчивым к растрескиванию и выкрашиванию.
Верхняя температура использования составляет 900 ° C.
Резка керамики
Режущая керамика даже тверже, чем твердый сплав, но проигрывает в отношении прочности.И оксид алюминия, и нитрид кремния используются для производства этих инструментов с различными свойствами.
Режущие керамические инструменты склонны к растрескиванию при работе с твердыми материалами и при высоких температурах. Поэтому, например, они не подходят для обработки стали. В противном случае следует ожидать короткого срока службы инструмента.
Выбор подходящего станка
Как правило, в производстве выбор метода или инструмента сводится к достижению баланса между скоростью, стоимостью и качеством.Стоимость зависит как от цены инструмента, результата механической обработки износа, так и от времени, необходимого (скорости) для изготовления деталей.
Выбор материала инструмента
Обычные углеродистые стали обычно исключаются из списка опций из-за их ограниченных возможностей. Поэтому HSS (быстрорежущая сталь) является наиболее дешевым материалом для выполнения работы. В то же время скорость его износа означает, что в долгосрочной перспективе есть варианты получше.
Кобальтсодержащая быстрорежущая сталь, например, подходит для еще более быстрого фрезерования.Это делает их достаточно подходящими для большинства работ.
Твердый сплав — это еще один шаг к высокопроизводительному фрезерованию благодаря вышеупомянутым свойствам таких фрезерных станков. В конечном итоге они являются более экономичным выбором, в то время как первоначальные затраты выше.
Диаметр
Это довольно просто. Инструмент большого диаметра может быстрее фрезеровать деталь. Ограничения применяются в зависимости от геометрии конечной детали.
Например, если необходимы определенные внутренние радиусы, инструмент не может отклоняться от них.В то же время вы можете использовать большой инструмент для фрезерования основной части и применить меньший инструмент для обработки внутренних углов.
Покрытие инструмента
Существуют различные покрытия для защиты инструментов от износа. Например, покрытие из нитрида титана увеличивает срок службы инструмента, но также увеличивает его стоимость.
Такое покрытие снижает липкость режущего материала, что может быть проблемой для алюминия. Следовательно, во время резки требуется меньше смазки.
Количество канавок
Канавки — это каналы на фрезерной коронке. Чем больше канавок, тем выше скорость подачи, потому что удаляется меньше материала.
В то же время это увеличивает общий диаметр фрезы. Это оставляет меньше места для стружки.
Угол винтовой линии
Угол наклона спирали вместе со скоростью вращения шпинделя определяет скорость резания или скорость подачи. Более крутой угол подходит для более мягких материалов и металлов.
Чтобы выбрать подходящие фрезы для вашей работы, необходимо понимание материалов, параметров и определенно некоторый опыт.Конечный результат зависит от этого выбора, и машинист должен понимать, какие фрезы подходят для резки различных материалов.
Хороший выбор ведет к высокой подаче и, следовательно, к сокращению времени резки, а также к снижению затрат.
При выборе службы обработки с ЧПУ убедитесь, что у них есть все необходимые инструменты для изготовления ваших деталей.
Глава 12: Фрезы и операции | Применение режущего инструмента
В металлообработке используются два основных типа режущего инструмента: одноточечный и многоточечный.По сути, они похожи. Фрезу можно создать, сгруппировав несколько одноточечных инструментов в круглом держателе.
Фрезерование — это процесс создания обработанных поверхностей путем постепенного удаления заданного количества материала с заготовки, который продвигается с относительно низкой скоростью подачи к фрезу, вращающейся со сравнительно высокой скоростью. Характерной особенностью процесса фрезерования является то, что каждый зуб фрезы снимает свою долю припуска в виде мелких отдельных стружек.
Типы фрез
Разнообразие доступных фрез делает фрезерование универсальным процессом обработки. Фрезы производятся в большом размере. Фрезы изготавливаются из быстрорежущей стали (HSS), другие имеют твердосплавные пластины, а многие из них являются сменными или индексируемыми пластинами.
Периферийные фрезы — Периферийные фрезы обычно устанавливаются на оправку для выполнения различных операций. Обычные фрезы для высокоскоростной стали включают фрезу со ступенчатым зубом, боковую фрезу, плоскую фрезу, одноугловую фрезу, двухугловую фрезу, выпуклую фрезу, вогнутую фрезу и фрезу с закругленными углами.
Плоская фреза для легких режимов работы — Фреза общего назначения для периферийного фрезерования. Узкие фрезы имеют прямые зубья, а широкие — винтовые.
Плоская фреза для тяжелых условий эксплуатации — Аналогичная фреза для легких режимов работы, за исключением того, что она используется для более высоких скоростей съема металла. Чтобы помочь ему в этой функции, зубцы расположены шире, а угол наклона спирали увеличен примерно до 45 градусов.
Боковая фреза — Имеет режущие кромки по бокам и по периферии.Это позволяет фрезу фрезеровать пазы.
Фреза половинная — То же, что и описанная ранее, за исключением того, что режущие кромки имеются на одной стороне. Используется для фрезерования уступов. Две фрезы этого типа часто устанавливаются на одной оправке для двухкоординатного фрезерования.
Боковая фреза со смещенными зубьями — То же, что и боковая фреза, за исключением того, что зубья расположены со смещением, так что каждый второй зуб режет на заданной стороне паза. Это позволяет выполнять глубокие и тяжелые пропилы.
Угловые фрезы — Периферийные режущие кромки лежат на конусе, а не на цилиндре. Может быть предусмотрен одинарный или двойной угол.
Концевая фреза — Имеет периферийные режущие кромки плюс торцевые режущие кромки на одном конце. В нем есть отверстие для болта, чтобы прикрепить его к шпинделю.
Формовочная фреза — Периферийная фреза, кромка которой имеет форму, позволяющую придать поверхности особую форму. Одним из примеров является фреза для зубьев шестерни.На поверхности заготовки воспроизводится точный контур режущей кромки формовочной фрезы.
Концевые фрезы — Концевые фрезы могут использоваться на вертикальных и горизонтальных фрезерных станках для выполнения различных операций торцевания, обработки пазов и профилирования. Цельнотянутые концевые фрезы изготавливаются из быстрорежущей стали или спеченного карбида. Другие типы, такие как концевые фрезы и фрезы, состоят из режущих инструментов, которые прикручены болтами или иным образом прикреплены к адаптерам.
Фрезы сплошные — Фрезы сплошные концевые имеют две, три, четыре или более канавок и режущие кромки на торце и периферии.Две концевые фрезы с канавками можно подавать прямо вдоль их продольной оси в твердый материал, поскольку режущие поверхности на концах встречаются. Фрезы с тремя и четырьмя канавками с одной торцевой режущей кромкой, выступающей за центр фрезы, также можно подавать непосредственно в твердый материал.
Цельнотянутые концевые фрезы бывают двухсторонние или односторонние, с прямым или коническим хвостовиком. Концевая фреза может быть короткой с короткими режущими канавками или очень длинной для проникновения в глубокие полости. На концевых фрезах, предназначенных для эффективной резки алюминия, угол наклона спирали увеличен для улучшения режущего действия и удаления стружки, а канавки можно полировать.
Специальные концевые фрезы — Шаровые концевые фрезы доступны в диаметрах от 1/32 до 2-1 / 2 дюйма, одностороннего и двустороннего типов. Одноцелевые концевые фрезы, такие как фрезы Woodruff со шпоночным шлицем, фрезы для закругления углов и фрезы «ласточкин хвост», используются как на вертикальных, так и на горизонтальных фрезерных станках. Обычно они изготавливаются из быстрорежущей стали и могут иметь прямой или конический хвостовик.
Номенклатура фрезы — Что касается режущего действия по металлу, подходящие углы на зубе — это те, которые определяют конфигурацию режущей кромки, ориентацию поверхности зуба и рельеф для предотвращения трения о землю .
Внешний диаметр — Диаметр окружности, проходящей через периферийные режущие кромки. Это размер, используемый вместе со скоростью шпинделя для определения скорости резания (SFPM).
Диаметр корня — Этот диаметр измеряется по окружности, проходящей через нижнюю часть галтели зуба.
Зуб — Зуб — это часть фрезы, начинающаяся от корпуса и заканчивающаяся периферийной режущей кромкой. Сменные зубы называют вкладышами.
Лицевая поверхность зуба — Лицевая поверхность зуба — это поверхность между галтелем и режущей кромкой, по которой стружка скользит во время ее формирования.
Фаска — Область за режущей кромкой зуба, которая очищена во избежание столкновения, называется фаской.
Канавка — Канавка — это пространство, предназначенное для прохождения стружки между зубьями.
Угол зазора — Угол зазора измеряется между лицевой стороной зуба и задней частью зуба непосредственно впереди.
Скругление — Скругление — это радиус в нижней части канавки, предназначенный для обеспечения стекания стружки и ее скручивания.
Вышеуказанные термины применимы в первую очередь к фрезам, в частности к гладким фрезам. При определении конфигурации зубьев фрезы важны следующие термины.
Периферийная режущая кромка — Режущая кромка, выровненная в основном в направлении оси фрезы, называется периферийной режущей кромкой.При периферийном фрезеровании именно эта кромка удаляет металл.
Лицевая режущая кромка — Лицевая режущая кромка — это кромка для удаления металла, ориентированная в основном в радиальном направлении. При боковом и торцевом фрезеровании эта кромка фактически образует новую поверхность, хотя периферийная режущая кромка все еще может снимать большую часть металла. Это соответствует торцевой режущей кромке одноточечных инструментов.
Угол спуска — Этот угол измеряется между площадкой и касательной к режущей кромке на периферии.
Свободный угол — Предназначен для стружки и образования канавки.
Радиальный передний угол — Угол между поверхностью зуба и радиусом фрезы, измеренный в плоскости, перпендикулярной оси фрезы.
Осевой передний угол — Измеряется между периферийной режущей кромкой и осью фрезы, если смотреть радиально на точку пересечения.
Угол установки лезвия — Когда в корпусе резака имеется паз для лезвия, угол между основанием паза и осью резака называется углом установки лезвия.
Сменные фрезы
Существует множество зажимных систем для сменных пластин в корпусах фрез.
Клиновой зажим — Фрезерные пластины уже много лет зажимаются с помощью клиньев в индустрии режущего инструмента. Этот принцип обычно применяется одним из следующих способов: либо клин спроектирован и ориентирован так, чтобы поддерживать пластину во время зажима, либо клин зажимает режущую поверхность пластины, прижимая пластину к корпусу фрезы.Когда клин используется для поддержки пластины, он должен поглощать всю силу, возникающую во время резания. Вот почему предпочтение отдается зажиму клина на режущей поверхности пластины, поскольку этот метод передает нагрузки, возникающие при прорезании пластины, на корпус резца.
Однако система клинового зажима имеет два явных недостатка. Во-первых, клин покрывает почти половину режущей поверхности пластины, препятствуя нормальному потоку стружки и вызывая преждевременный износ корпуса фрезы, а во-вторых, высокие зажимные усилия, вызывающие деформацию зажимного элемента и корпуса фрезы, могут и часто будут результатом.Чрезмерное усилие зажима может вызвать достаточную деформацию корпуса фрезы, так что в некоторых случаях при загрузке пластин в корпус фрезы последний паз пластины будет сужен до точки, в которой последняя пластина не войдет в корпус. Когда это происходит, несколько уже загруженных пластин удаляются и сбрасываются. Клиновой зажим можно использовать для зажима отдельных пластин или сменных и сменных картриджей фрез.
Винтовой зажим — Этот метод зажима используется в сочетании со вставкой с запрессованной зенковкой или зенковкой.Динамометрический винт часто используется для эксцентрической установки и прижатия пластины к стенкам гнезда для пластины.
Винтовой зажим отлично подходит для концевых фрез малого диаметра, где пространство ограничено. Он также обеспечивает свободный беспрепятственный путь для стружки без клиньев или любого другого препятствующего оборудования. Винтовой зажим обеспечивает меньшее зажимное усилие, чем при использовании клиновой зажимной системы. Однако, когда температура режущей кромки значительно повышается, пластина часто расширяется и вызывает нежелательный эффект повторной затяжки, увеличивая крутящий момент, необходимый для разблокировки винта пластины.Метод винтового зажима может использоваться на шаровых фрезах со сменными пластинами или на фрезах со сменными пластинами и торцевых фрезах.
Геометрия фрезы
Существует три стандартных геометрии фрезы: двойное отрицательное, двойное положительное и положительное / отрицательное. Каждый из них имеет определенные преимущества и недостатки, которые необходимо учитывать при выборе правильной фрезы для работы.
Двойная отрицательная геометрия — Двойная отрицательная фреза использует только отрицательные пластины, удерживаемые в отрицательном кармане.Это обеспечивает прочность режущей кромки для черновой обработки и прерывистого резания. При определении геометрии фрезы важно помнить, что отрицательная пластина имеет тенденцию отталкивать фрезу, оказывая значительное усилие на заготовку. Это может быть проблемой при обработке слегка удерживаемых деталей или при использовании легких станков. Однако эта тенденция толкать обрабатываемую деталь или отталкивать фрезу от обрабатываемой детали может быть полезной в некоторых случаях, потому что сила прекращается, чтобы «нагружать» систему, что часто снижает вибрацию.
Двойная положительная геометрия — Двойные положительные фрезы используют положительные пластины, удерживаемые в положительных карманах. Это необходимо для обеспечения необходимого зазора для резки. Двойная положительная геометрия фрезы обеспечивает резку с низким усилием, но пластины контактируют с заготовкой в их самом слабом месте — режущей кромке. При фрезеровании с положительным передним углом силы резания стремятся поднять заготовку или втягивать фрезу в работу. Самым большим преимуществом двойного положительного фрезерования является свободное резание. К заготовке прилагается меньшее усилие, поэтому требуется меньшая мощность.
Положительная / отрицательная геометрия — Положительная / отрицательная геометрия фрезы объединяет положительные пластины, удерживаемые в отрицательных карманах. Это обеспечивает положительный осевой прием и отрицательный радиальный передний угол, а также, как и в случае с двойными положительными пластинами, необходимый зазор для резания. В случае фрез с положительным / отрицательным наклоном заготовка контактирует с режущей кромкой в радиальном направлении и с режущей кромкой в осевом направлении. Резак положительного / отрицательного типа может считаться резаком с низким усилием.При положительном / отрицательном фрезеровании доступны некоторые из преимуществ как положительного, так и отрицательного фрезерования.
Угол подъема — Угол подъема — это угол между пластиной и осью фрезы. Чтобы определить, какой угол подъема лучше всего подходит для конкретной операции, необходимо учитывать несколько факторов. Во-первых, угол подъема должен быть достаточно небольшим, чтобы покрывать глубину резания. Чем больше угол подъема, тем меньшую глубину резания можно выполнить для пластины данного размера. Кроме того, для обрабатываемой детали может потребоваться небольшой угол подъема, чтобы очистить часть или сформировать определенную форму на детали.
Угол подъема также определяет толщину стружки. Чем больше угол подъема для одинаковой скорости подачи или нагрузки стружки на зуб, тем тоньше стружка становится. Как и в одноточечной оснастке, глубина резания распределяется по более длинной поверхности контакта. Следовательно, рекомендуется использовать фрезы с углом подъема, когда целью является максимальное удаление материала. Утончение стружки позволяет увеличить скорость подачи.
Углы подъема могут составлять от нуля до 85 градусов. Наиболее распространенные углы подъема, доступные для стандартных фрез, составляют 0, 15, 30 и 45 градусов.Углы подъема более 45 градусов обычно считаются особыми.
Фрезы с большим углом в плане также обладают большей теплоотдачей. Однако, если при резке можно использовать больше инструмента, как в случае с большими углами подъема, способность инструмента рассеивать тепло будет улучшена. Кроме того, увеличивается осевая сила и уменьшается радиальная сила, что является важным фактором в борьбе с вибрацией.
Геометрия углов фрезерной пластины
Форма и размер индексируемых пластин обсуждались в главе 2.Выбор правильной угловой геометрии, вероятно, является наиболее сложным элементом выбора пластины. Доступны самые разные стили углов. Выбранный стиль углов существенно повлияет на качество поверхности и стоимость вставки.
Радиус при вершине — Пластина с радиусом при вершине обычно дешевле, чем аналогичная пластина с любой другой угловой геометрией. Радиус при вершине также является самой сильной угловой геометрией, потому что у него нет острых углов на стыке двух плоскостей.Только по этим двум причинам пластина с радиусом при вершине должна быть лучшим выбором для любого применения, где ее можно использовать.
Пластины с радиусом при вершине могут повысить стойкость инструмента, если они используются в фрезах с углом упора от 0 до 15 градусов.
Фаска — Существует два основных способа применения пластин с угловой фаской. В зависимости от угла фаски и угла подъема корпуса фрезы, в которой используется пластина, площадка фаски будет либо параллельной, либо угловой (наклонной) по отношению к направлению подачи.
Пластины, на которые нанесена фаска под углом к направлению подачи, обычно имеют только одну фаску. Эти пластины обычно не такие прочные, и их стоимость обычно выше, чем у пластин с большим радиусом при вершине. Пластины для снятия фаски с угловой фаской часто используются для обработки общего назначения с использованием двойных отрицательных фрез.
Пластины, предназначенные для использования с фаской, параллельной направлению подачи, могут иметь одинарную фаску, одинарную фаску и угловой разрыв, двойную фаску или двойную фаску и угловой разрыв.Более крупные участки называются первичными гранями, а участки меньшего размера — вторичными гранями. Стоимость фасок по сравнению с другими типами углов геометрии зависит от количества фасок. Однофасетная пластина является наименее дорогой, а многогранная пластина стоит дороже из-за дополнительных затрат на шлифование.
Самым большим преимуществом использования пластин с фаской, параллельной направлению подачи, является то, что при правильном использовании они обеспечивают отличное качество поверхности.Когда ширина площадки больше, чем продвижение на оборот, одна пластина образует поверхность. Это означает, что обычно достигается отличное качество поверхности независимо от биения торца пластины.
Стеклоочистители — Стеклоочистители уникальны как по внешнему виду, так и по применению. Эти пластины имеют только одну или две очень длинные чистящие площадки. В корпусе фрезы, заполненной другими пластинами (обычно пластинами для черновой обработки), используется одинарный очиститель, который устанавливается приблизительно от 0,003 до 0.На 005 дюймов выше, чем у других пластин, так что только очиститель образует готовую поверхность.
Чистовая обработка, полученная с помощью протирочной машины, даже лучше, чем превосходная чистовая обработка, достигаемая с помощью пластины для снятия фаски с параллельной площадкой.
Основные операции фрезерования Перед тем, как будет предпринята какая-либо операция по фрезерованию, необходимо принять несколько решений. Помимо выбора наилучших средств удержания работы и наиболее подходящих фрез, необходимо установить скорость резания и скорость подачи, чтобы обеспечить хороший баланс между быстрым съемом металла и длительным сроком службы инструмента.
Правильное определение скорости резания и скорости подачи возможно только в том случае, если известны следующие шесть факторов:
• Тип обрабатываемого материала для стяжки
• Жесткость установки
• Физическая прочность фрезы
• Режущий инструмент материал
• Доступная мощность на шпинделе
• Требуемый тип чистовой обработки
Направление подачи фрезерования Применение фрезерного инструмента с точки зрения направления его обработки имеет решающее значение для производительности и срока службы инструмента в течение всей операции.Два варианта направления фрезерования описываются как обычное фрезерование или фрезерование с подъемом. Обычное фрезерование и фрезерование с подъемом также влияют на стружкообразование и стойкость инструмента.
Обычное фрезерование — Термин, часто ассоциируемый с этой техникой фрезерования, — это фрезерование под прямым углом. Фреза вращается против направления подачи, когда заготовка продвигается к ней со стороны, где зубья движутся вверх. Разделительные силы, возникающие между резцом и заготовкой, препятствуют движению заготовки.Толщина стружки в начале реза минимальна, постепенно увеличиваясь до максимальной в конце реза.
Фрезерование с подъемом — Термин, часто связанный с этой техникой фрезерования, — это фрезерование «снизу». Фреза вращается в направлении подачи и заготовки, поэтому продвигается к фрезу со стороны, где зубья движутся вниз. Когда зубья фрезы начинают резать, возникают силы значительной интенсивности, которые способствуют движению заготовки и стремятся втягивать ее под фрезу.Стружка имеет максимальную толщину в начале реза, уменьшаясь до минимума на выходе. Как правило, рекомендуется везде, где это возможно, фрезерование с подъемом. Подъемное фрезерование обеспечивает лучшую чистовую обработку и продлевает срок службы фрезы.
Преимущества и недостатки — Если обрабатываемая деталь имеет сильно абразивную поверхность, обычное фрезерование обычно обеспечивает больший срок службы резца, поскольку режущая кромка входит в контакт с обрабатываемой поверхностью ниже абразивной поверхности. Обычное фрезерование также защищает кромку за счет скалывания поверхности перед режущей кромкой.
Ограничения на использование подъемного фрезерования в основном связаны с состоянием станка и жесткостью, с которой заготовка закреплена и поддерживается. Поскольку резец имеет тенденцию взбираться на работу, оправка фрезерного станка и опора оправки должны быть достаточно жесткими, чтобы преодолеть эту тенденцию. Подача должна быть равномерной, и если на станке нет привода глушителя люфта, упоры стола должны быть затянуты, чтобы предотвратить втягивание заготовки в резак.Большинство современных машин построено достаточно жестко. Старые станки обычно можно подтянуть, чтобы можно было использовать подъемное фрезерование.
Давление вниз, вызванное подъемным фрезерованием, имеет неотъемлемое преимущество в том, что оно имеет тенденцию удерживать изделие и приспособление напротив стола, а стол — напротив путей. При обычном фрезеровании происходит обратное, и заготовка имеет тенденцию подниматься со стола.
Джордж Шнайдер-младший является автором Cutting Tool Applications, справочника по материалам, принципам и конструкциям станков.Он является почетным профессором инженерных технологий Технологического университета Лоуренса и бывшим председателем Детройтского отделения Общества инженеров-технологов.Что такое типы фрез и фрез — Советы по выбору правильных режущих инструментов с ЧПУ
Фреза — необходимый инструмент для обработки на фрезерных станках с ЧПУ. Рекомендуется выяснить типы и особенности различных режущих инструментов и выбрать подходящий для экономии затрат и повышения эффективности.CNClathing.com представляет фрезу, ее типы и советы по выбору режущего инструмента с ЧПУ.
Что такое фреза?Фреза — это фреза с одним или несколькими зубьями для фрезерования. В процессе фрезерования зубья фрезы срезают припуск заготовки по очереди и с перерывами. Он имеет цилиндрическую форму с режущей кромкой по окружности и снизу для резки заготовки вращением. Фреза в основном используется для обработки плоскости, ступени, канавки, формующей поверхности и резки заготовки на фрезерных станках и фрезерных станках с ЧПУ (числовое программное управление).
Типы фрез и концевые фрезыЕсть много видов фрез. Далее мы в первую очередь представим концевую фрезу. Фрезы общего назначения ( CNC-фрезы ) можно разделить на следующие типы:
1) Цилиндрическая фреза: используется для обработки плоскости на горизонтальном фрезерном станке. Зубья фрезы распределены по окружности фрезы.По форме зуба они делятся на прямые и спиральные. Спиральная фреза с широкими зубьями имеет меньше зубьев, высокую прочность, пространство для удержания стружки большое, подходит для черновой обработки. Боковая фреза также является цилиндрической фрезой.
2) Торцевая фреза: используется для обработки плоскости на вертикальном фрезерном станке, торцевом фрезерном станке или портальном фрезерном станке. На торце и по окружности имеются зубья фрезы, в ее состав входят цельные, вставные и поворотные.
3) Концевая фреза: используется для обработки канавок, ступенчатых поверхностей и т. Д., Когда зубья фрезы находятся на окружности и торцевой поверхности, ее нельзя подавать в осевом направлении. Когда концевой фрезер имеет концевой зуб, проходящий через центр, он может подаваться в осевом направлении.
4) Плоская фреза: также называемая плоской фрезой или фрезой для слябов, используется для фрезерования плоских поверхностей, причем ее ось параллельна фрезеруемой поверхности.
5) Угловая фреза: включая одноугловую фрезу и двухугловую фрезу
6) Пильная фреза: много зубьев фрезы по окружности глубокой канавки и обрабатываемой детали, углы вторичного отклонения 15 ‘~ 1 ° с обеих сторон зубьев фрезы.
7) Фреза для Т-образных пазов: используется для фрезерования Т-образных пазов
Существуют также фасонные фрезы, фрезы для мух, фрезы со вставными зубьями, полые фрезы, шаровые фрезы, эвольвентные зуборезные фрезы, фрезы для деревянных ерш, резьбовые фрезы, зубофрезерные фрезы и другие различные типы фрез с ЧПУ.
Концевые фрезы могут иметь прямые или спиральные канавки. Концевые фрезы со спиральными канавками подразделяются на правые и левые, в зависимости от направления вращения канавок.Левая фреза, как правило, является разновидностью фрезы, выбранной с учетом требований высокоточной обработки, обычно используемой для изготовления клавиши телефона, панели мембранного переключателя, ЖК-панели, акриловой линзы и другой отделочной обработки. Но есть некоторые приложения с высокими требованиями к точности и отделке, например, изготовление и обработка некоторых кнопок мобильных телефонов или электрических панелей, необходимо выбрать обрезку нижнего ряда и повернуть налево, чтобы избежать побеления режущей кромки и кромки. чип.
Советы по выбору режущего инструмента с ЧПУ Выбор режущего инструмента должен основываться на обрабатывающей способности станков, характеристиках обрабатываемых материалов, процедурах обработки, параметрах резания и других факторах. Общий принцип выбора фрезы с ЧПУ: удобство установки и регулировки, хорошая жесткость, высокая прочность и точность. Постарайтесь выбрать более короткую рукоятку инструмента, чтобы повысить жесткость обработки.
1) Размер режущего инструмента должен соответствовать размеру поверхности обрабатываемых деталей
2) Концевая фреза часто используется для обработки периферийного контура плоских деталей
3) Можно использовать твердосплавную фрезу для фрезерования плоскости
4) Концевая фреза из быстрорежущей стали может использоваться для обработки выпуклостей и выпуклостей
5) Винтовая фреза — идеальный вариант для обработки заготовок или черновых отверстий
6) Для обработки цельного профиля и различных Угловой профиль, фреза со сферическим концом, кольцевая фреза, коническая фреза и дисковая фреза часто используются
Как профессиональный поставщик прецизионных станков, компания Junying предлагает надежные и подходящие режущие инструменты для предоставления более эффективных услуг фрезерования с ЧПУ .
Выбор подходящей конструкции зубофрезерной фрезы для обработки высококачественных параллельных осей, цилиндрических зубчатых колес и шлицев
Инженер-технолог должен принять ряд решений при планировании необходимых процессов для производства параллельных осей, цилиндрических прямозубых или косозубых шестерен и шлицев. Зуборезание, конечно, является наиболее распространенным процессом удаления металла для создания надлежащего зазора между зубьями, необходимого для изготовления этих шестерен. Этот процесс существует уже более 100 лет и доказал свою эффективность.Это процесс формирования формы посредством последовательных и пошаговых разрезов, которые создают правильную форму с помощью ряда режущих зубьев реечного типа с прямым профилем. В процессе фрезерования зубчатое колесо вращается по мере вращения варочной панели и продвигается в осевом направлении по своей поверхности.
Рис. 1: Зубофрезерование — типичная схема создания последовательных зубьев червячной фрезыНо есть и другой способ выполнить эту задачу. Также эффективны зубофрезерные фрезы, которые фрезеруют все пространство между зубьями при неподвижном зубчатом колесе.Многие инженеры задают следующие вопросы: когда зубофрезерование предпочтительнее зубофрезерования? Какой тип станка нужен для зубофрезерования? Как выбрать подходящий инструмент для зубофрезерования? Как оценивается время цикла? Какие у меня должны быть проблемы с качеством? А как насчет зажима, крепления инструмента, скорости и подачи?
Вооружившись необходимой информацией, продуманным планированием, а также необходимыми инструментами и оборудованием, можно будет найти ответы на эти вопросы. При необходимости могут применяться стабильные и экономичные процессы зубофрезерования или заделки зубьев.Эта статья предназначена для инженеров-технологов, которые, возможно, плохо знакомы с производством шестерен. Это не научный анализ высокого уровня. Он носит практический характер и призван служить ценным руководством для разработки процесса изготовления зубчатых передач.
Основы процесса зубофрезерования
Инженер-технолог должен сначала понять основы фрезерования, чтобы принять рациональное технологическое решение о зарезке по сравнению с фрезерованием. Как уже говорилось, зубофрезерование — это порождающий процесс.Зубофрезерование требует сложной кинематики резания. Лучший способ понять это — наблюдать за образующимися рисунками, возникающими при фрезеровании (см. Рисунок 1). Обратите внимание на узор трохоидных петель, как показано.
Рисунок 2: Изменение расстояния между зубьями в зависимости от количества зубьевКак показано, каждый зуб червячной фрезы режет в разном положении в пространстве между зубьями и имеет разные характеристики стружкообразования. По мере того, как шестерня становится меньше в диаметре и имеет меньше зубьев для заданного диаметрального шага (DP) или модуля, пространство между зубьями увеличивается.(См. Рисунок 2.)
По мере увеличения зазора между зубьями и уменьшения диаметра шестерни меньшее количество зубьев червячной фрезы участвует в процессе резания, поскольку длина хорды фрезы уменьшается; следовательно, толщина стружки увеличивается при заданной скорости подачи на оборот шестерни. Кроме того, по мере увеличения зазора каждый зуб фрезы теперь должен принимать больший кусок. Площадь поперечного сечения чипа больше.
Рис. 3. Поднутрение корня, образованное выступом. Это означает, что шестерни с меньшим количеством зубьев и большими зазорами, чем их сопряженная шестерня, могут быть весьма требовательными.Именно тогда зубофрезерные фрезы становятся лучшей технологической альтернативой зубофрезерованию.
Другой фактор, который следует учитывать при зубофрезеровании, — это конфигурация корня и любой необходимый подрез. Поднутрения требуются, когда требуется последующая чистовая операция, например, шлифование. Поднутрения корня достигаются с помощью выступа на кончике зуба фрезы. Эта функция выпуклости создает поднутрение корня с широким трохоидальным рисунком режущего действия.(См. Рисунок 3.)
Величину поднутрения из-за фрезерования небольшого числа зубьев или шага можно контролировать с помощью фрезерных фрез с коротким шагом. Конструкции варочных панелей особой конструкции считаются нестандартными, возможно, с более длительным сроком изготовления и более высокой стоимостью, чем у обычных варочных панелей. Это был успешный метод борьбы с чрезмерным подрезом на протяжении многих лет, но подробный анализ этих варочных панелей выходит за рамки данной статьи.
Рис. 4: Пример зубчато-фрезерного профиля с заготовкой для шлифования по боковой поверхности, но с обработанной корневой частьюОсновы процесса зубофрезерования или зарезки
При зарезании зубчатое колесо удерживается неподвижно, в то время как фреза продвигается в осевом направлении по ширине торца заготовки зубчатого колеса.Этот процесс можно использовать для черновой или получистовой обработки пространства между зубьями с дополнительным припуском для последующих операций фрезерования, шлифования, бритья или хонингования. Или он может довести пространство между зубами до окончательной формы. Это можно сделать за один или несколько проходов. Зубофрезерные фрезы могут быть установлены тандемом для создания двух или более пространств, и они могут быть сконструированы из стальных корпусов со съемными твердосплавными пластинами. В некоторых редких случаях их заставляют использовать повторно шлифованные твердосплавные лезвия, но с современными технологиями прецизионного шлифования твердосплавных пластин для таких инструментов нет (если вообще есть) оправдания.Иногда используются твердосплавные инструменты, но из-за высокой стоимости и ограничений по размеру твердосплавных инструментов они также становятся менее популярными. Фрезы из быстрорежущей стали можно изготавливать по относительно низкой цене, но они обладают ограниченными скоростными характеристиками и лучше всего подходят для зубчатых колес очень малого объема и модулей меньшего размера, поскольку высокая стоимость материала из быстрорежущей стали делает резцы большего размера непрактичными. (Примеры различных конструкций зубофрезерных фрез показаны на рисунках 5, 6, 7 и 8.)
Рис. 5: Зубофрезерование твердым инструментом (быстрорежущая сталь или твердый сплав)Зубофрезерные фрезы с тангенциально установленными пластинами довольно распространены.Они отличаются хорошей экономичностью, так как большинство из них имеют твердосплавные пластины с несколькими кромками. Большинство из них предназначены для модулей размером более 8 (DP 3). Требования к мощности и крутящему моменту выше, поскольку их режущая геометрия традиционно подразумевает отрицательные осевые и радиальные передние углы. Некоторые новые конструкции имеют пластины с положительной геометрией резания, но обычно это ограничивается инструментами для черновой и получистовой обработки, для которых не требуются точные полнопрофильные пластины. Такие пластины отшлифованы в соответствии с требованиями производителя зубчатых колес; поэтому дорогостоящие прессовые инструменты со вставками обычно не производятся, если это не оправдано очень большим объемом.
Внешний шлицевой фрезерный инструмент и пластины показаны на Рис. 9 и Рис. 10. В прошлом, независимо от того, были ли шлицы эвольвентными или прямолинейными, зубофрезерование было почти исключительным методом обработки. Благодаря усовершенствованию станков с ЧПУ с точной индексацией 4-й оси, теперь предпочтительным процессом становится зарезка.
Разгрузка шлифования (чистовая фрезеровка) в корневой зоне для предотвращения ступенек в активном профиле (см. Рисунок 4) также может быть выполнена с помощью зубофрезерных фрез. Поскольку процесс зубофрезеровки приводит к более выраженному подрезу по мере уменьшения числа зубьев шестерни и уменьшения диаметра делительной окружности, площадь поперечного сечения корня становится тоньше (см. Рисунок 3).Более толстая корня по сравнению с зубофрезерованием дает преимущество в прочности конструкции при зарезании по сравнению с зубофрезерованием.
На Рисунке 4 компоненты с 1 по 6 представляют собой сменные пластины, расположенные по периферии корпуса фрезы. Огибающая прорезей, сделанных каждой пластиной, дает полуфабрикат боковой поверхности и завершает фрезерованную форму корня с выступом.
Рис. 6: Инструмент для зарезки со сменными пластинами полной формыВыбор зарезки поверх зубофрезеровки
Если доступны отдельные индексирующие станки, будь то специальные зубофрезерные станки или оборудование с ЧПУ с возможностью точного индексирования, возможно зарезание / зубофрезерование.При выборе зубофрезерования или зарезки необходимо учитывать следующие факторы:
- Число зубьев шестерни . В шестернях и шестернях с небольшим количеством зубьев (с учетом их модуля или размера DP) зазор между зубьями увеличивается по мере уменьшения дуги делительной окружности. Длина хорды зацепления червячного инструмента будет меньше, чем у шестерни большего диаметра с большим количеством зубьев и большей дугой делительной окружности. Это означает, что меньше зубьев фрезы задействовано для создания необходимого зазора.Это ограничивает подачу варочной панели, так как зубья варочной панели быстро перегружаются. Разрезание может завершать форму за один или несколько проходов, в зависимости от жесткости машины и настройки, мощности и крутящего момента. Время индексации фрезы от одного промежутка зуба к другому сокращается вместе с количеством зубьев. Это работает в пользу продолжительности цикла измельчения.
- Требования к филе корня . Филе корня получают в процессе зубофрезерования и несколько ограничены из-за ранее описанной трохоидальной петли.Если при последующей операции требуется шлифовка, стачивание или хонингование боковых сторон, то необходим соответствующий припуск в области корня. Степень гибкости важна. Зубцевание может создать настоящий поднутрение, как показано на рисунке 3. Зарезание приведет к прямому рельефу в корне. Это является предпочтительным во многих случаях из-за увеличения толщины поперечного сечения зуба в области корня ниже начала активного профиля. При малозубчатых шестернях трохиодальная петля может образовывать очень большое поднутрение при зубофрезеровании.В таких случаях для прочности предпочтительнее зарезание.
- Только с обычным оборудованием с ЧПУ. Если в наличии нет зубофрезерного станка, но есть станок с ЧПУ с возможностью индексации, часто хорошим вариантом является зарезка. Здесь необходимо учитывать, что станок имеет очень качественный индексирующий стол (4-я или 5-я оси), который может обеспечить допуск на погрешность расстояния между зубьями в соответствии с требованиями. Современные многоцелевые токарно-фрезерные станки набирают популярность и обладают огромным потенциалом.Также необходимо учитывать мощность шпинделя и жесткость. Необходимо учитывать качественные интерфейсы между инструментом и шпинделем. Конус № 50 ISO, Coromant Capto или HSK — хорошие варианты интерфейса между шпинделем и инструментом для повышения точности и жесткости. Станки с ЧПУ не будут иметь подвесной оправки, как у традиционных зуборезных станков; поэтому может потребоваться выполнить несколько проходов для уменьшения усилий. С другой стороны, шлицевое фрезерование обычно гораздо менее требовательно, поскольку общая глубина часто составляет половину одного и того же размера зубчатого колеса.При шлицевом фрезеровании время цикла часто на 50 процентов меньше, чем при традиционном горизонтальном фрезеровании HSS, особенно если выбранный станок с ЧПУ имеет высокую скорость быстрого хода. Это может быть меньше одной секунды на зуб.
Комбинация зарезки и зубофрезерования
Инструменты для резки и зубофрезерования можно комбинировать на одном станке. Многие современные зубофрезерные станки имеют функцию управления, позволяющую резаку, установленному на той же оправке, что и варочная панель, выполнять единичную индексацию и черновую или получистовую обработку промежутков между зубцами.Затем фрезерная головка может сместиться — без потери положения зуба на заготовке и местоположения червячной фрезы — для завершения фрезерования зубчатого колеса. Этот метод полезен при использовании резца со сменными пластинами из твердого сплава для удаления большей части заготовки, когда рабочий материал трудно обрабатывать с помощью традиционной фрезерной фрезы из быстрорежущей стали. Инструмент для варочной поверхности обрабатывает шестерню только за счет удаления минимального количества материала. Длину варочной панели можно уменьшить, а время между переточками можно увеличить. (См. Рисунок 11.)
Определение толщины стружки при зазоре
Наиболее важным фактором при правильном применении зубофрезерных фрез является определение толщины стружки. Поскольку дуга зацепления зуборезной фрезы обычно очень короткая, часть фрезы, задействованная в работе, очень мала по отношению к общей окружности (см. Рисунок 12). Скорость подачи при фрезеровании часто выражается в единицах подачи на зуб. Из-за этой небольшой дуги зацепления фактическая толщина стружки будет значительно меньше подачи на зуб.
Рис. 8: Чистовая, дуплексная, тангенциальная зубофрезерная фрезаПри этом необходимо рассчитать фактическую толщину стружки. Фактическая толщина стружки обозначается как H ex . Необходимо определить расчет коэффициента модификации fz. Этот коэффициент указывается как множитель фактической подачи на зуб, обозначаемый как f z . Первым делом необходимо определить диаметр фрезы или D c . Затем определите фактическую всю глубину пространства между зубьями или глубину фрезерования (если требуется несколько проходов), которая обозначается как A e .Конечно, правильное значение H ex должно определяться в соответствии с рекомендациями производителя инструмента.
Формула для f z , коэффициент модификации:
Уравнение 1
Примером может служить фреза диаметром 8 дюймов, D c = 8
Однопроходное фрезерование до глубины зазора между зубьями 0,7 дюйма, A e = 0,7
Таким образом, fz , коэффициент модификации = 5.7143 / 3,229 = 1,769
Следовательно, если требуется H ex 0,008, тогда f z 0,008 x 1,769 = 0,014.
Рисунок 9: Инструмент для зарезания шлицевых шлицовУтончение стружки на боковой поверхности по сравнению с корнем
Предыдущий раздел о толщине стружки относится к корневой зоне. В корневой зоне рассчитывается максимальная толщина стружки. Стружка, образующаяся на боковой поверхности зуба, намного тоньше. Простой способ взглянуть на это — рассмотреть базовую V-образную форму стойки.В случае редуктора с углом сжатия 20 градусов вы просто берете тангенс угла 20 градусов, который составляет 0,364. Используя этот коэффициент, толщина стружки, рассчитанная на основе корня 0,008, будет умножена на 0,364. Это будет означать, что толщина боковой стружки составляет около 0,003 дюйма.
Поскольку боковые поверхности не имеют прямой V-образной формы (за исключением фрезерования прямой зубчатой рейки) с типичной конструкцией эвольвентной кривой, нецелесообразно рассчитывать точную толщину стружки на боковой поверхности. Этот метод использования тангенса угла давления приемлем для целей планирования процесса.Этот фактор более тонкой стружки на боковой поверхности также является причиной более легкой подготовки режущей кромки на боковых пластинах. Слишком большая заточка кромки может привести к трению и смазыванию металла из-за слишком большого давления и недостаточного срезающего действия.
Рис. 10: Различные профили пластин для шлицев одинакового размера с 45, 39 и 32 зубьямиПо этой причине, когда инструменты изготавливаются с отдельными корневыми и боковыми пластинами, конструкторы часто увеличивают количество корневых пластин по сравнению с боковыми пластинами. Отношение корней к боковым сторонам составляет 2: 1 и 3: 1.Корневые пластины производят примерно в три раза больше работы, чем боковые пластины, поэтому эта концепция имеет смысл для балансировки износа инструмента всех задействованных пластин.
Полноформатный разрыв
Возвращаясь к рисунку 6, полноразмерные режущие инструменты во многих случаях имеют свои достоинства. При полном зарезании твердосплавные пластины шлифуются по всей форме производимого пространства зуба (корень и боковые поверхности). Это наиболее точный вариант благодаря универсальной конструкции. В случае отдельных пластин с корнем, левой и правой боковыми поверхностями каждая пластина имеет допуск, плюс гнезда под пластину в корпусе инструмента имеют допуски; следовательно, наложение больше, чем у полноразмерной вставки, где требуются одна вставка и один карман.
Рис. 11: Комбинация зубофрезеровки и зарезкиЕще одним преимуществом полноформатной конструкции является простота и эффективность удаления стружки. Конструкции тангенциальных пластин с множеством различных корневых и боковых пластин создают различные образования стружки, которые изгибаются в разных направлениях. Прогнозирование этих схем формирования стружки и последующего удаления стружки может оказаться сложной задачей даже для самых опытных разработчиков инструментов. Иногда встречается смазывание стружки и повторная резка. Цельнозубчатые фрезы имеют до двух раз более эффективные зубья, чем тангенциальные фрезы; следовательно, они более производительны.
Незначительным недостатком полноразмерной конструкции является то, что отношение корневой части к боковой поверхности составляет 1: 1, что, как упоминалось в предыдущем разделе, не является идеальным балансом для износа инструмента. Улучшения производительности, качества и удаления стружки обычно перевешивают эти проблемы. По мере увеличения зубчатого модуля или размера DP размер требуемой твердосплавной заготовки становится больше, и в конечном итоге ее производство становится непрактичным как с технической, так и с экономической точки зрения.
Если технические требования AGMA, DIN или другие требования к качеству зубчатой передачи вызывают озабоченность у разработчика инструмента или инженера-технолога, следует рассмотреть вариант полной формы.
Фрезерование с подъемом и обычным фрезерованием
Распространенной передовой практикой фрезерования является использование подъемного фрезерования для зарезания зубчатых колес. Иногда используется другой процесс, обычно называемый обычным измельчением. Визуализация этих двух методов показана на рисунке 13.
Рис. 12: Малая дуга зацепленияФрезерование с подъемом позволяет режущей пластине вступать в работу с некоторым немедленным стружкообразованием и выходить из зоны резания без толщины стружки.Поскольку карбид лучше всего работает при сжимающей нагрузке, этот метод доказал свою лучшую стойкость инструмента. Разгрузка на выходе менее опасна для инструмента, так как выходной удар минимален.
При обычном фрезеровании инструмент входит в резку без толщины стружки, а затем постепенно формирует стружку по мере продвижения в работу. Он выходит из резания с некоторой толщиной стружки, поэтому разгрузка происходит внезапно и снижает стойкость инструмента. Кроме того, трение при входе инструмента в работу вызывает большее тепловыделение и тепловой эффект.При использовании этого метода также значительно увеличивается давление инструмента. Одним из ощутимых преимуществ является то, что качество обработки поверхности обычно лучше при обычном фрезеровании из-за сжимающего и полирующего действия, когда инструмент начинает формировать стружку. Лабораторные результаты Sandvik Coromant показали снижение Ra на 20-30% при использовании обычного фрезерования по сравнению с резанием с подъемом.
Рисунок 13: Фрезерование с подъемом и обычное фрезерованиеФрезерование со смазочно-охлаждающей жидкостью и сухое резание
Лучшая практика фрезерования твердосплавными инструментами — это, за некоторыми исключениями, резание всухую.При резке жидкостью твердосплавный инструмент подвергнется термическому удару при выходе из резания. Эффект теплового удара обычно отрицательно сказывается на сроке службы инструмента. Пример этого механизма разрушения показан на рисунке 14. Здесь повторяющиеся циклы нагрева и охлаждения в конечном итоге приводят к перпендикулярным краевым трещинам, которые в конечном итоге позволяют материалу вставки высвободиться, что приводит к быстрому разрушению. Водорастворимые смазочно-охлаждающие жидкости оказывают наиболее вредное воздействие на тепловой удар, поскольку вода быстро охлаждает инструмент. Смазочно-охлаждающие масла также обладают значительным охлаждающим эффектом, но они не удаляют БТЕ так быстро, как вода.Следовательно, они несколько лучше воды по стойкости инструмента. Конечно, при использовании жидкостей как на нефтяной, так и на водной основе возникают экологические издержки, и цель должна заключаться в их устранении, когда это возможно.
Применение сжатого производственного воздуха или даже вихревое охлаждение сжатого воздуха может способствовать удалению стружки и охлаждению инструмента и работы. Пример этого метода охлаждения показан на рисунке 15. Это проверенный метод обеспечения охлаждения. Устранение тепловыделения и удаление стружки — основная причина, по которой все еще используются смазочно-охлаждающие жидкости.
Рисунок 14: Термическое растрескивание Инструментымогут иметь внутренние воздушные каналы, как показано на Рисунке 16. Такая конструкция способствует удалению стружки и охлаждению инструмента. Однако такие функции значительно увеличивают сложность и стоимость инструмента. Этот метод подачи внутреннего воздуха следует тщательно продумать, так как необходимы модификации шпинделя и оправки станка, а также стоимость инструмента и проблемы сложности прохождения воздуха через инструмент. При правильной конструкции инструмента для свободного отвода стружки в сочетании с правильной стратегией резания, вероятно, можно избежать внутренних воздушных отверстий.
Рисунок 15: Система охлаждения сжатым воздухом VortexСила резания
Требования к мощности и крутящему моменту должны быть определены для эффективного применения зубофрезерных фрез для стабильного процесса обработки. Чтобы правильно оценить усилия обработки, необходимо определить площадь поперечного сечения стружки и удельную силу резания для данного материала. Вычислить точную площадь поперечного сечения для данного пространства зуба довольно сложно, и лучше всего это сделать с помощью компьютерного программного обеспечения, способного создать точный профиль боковой поверхности и конфигурацию корня.Подобные расчеты выходят за рамки данной статьи. Вместо этого цель состоит в том, чтобы найти близкое, пригодное для использования приближение. Для этого можно изучить базовую конфигурацию стойки (V-образную форму) для заданного угла давления без сложного профиля эвольвентной кривой на боковых сторонах. Примечание. При использовании этого метода оценки для фрезерных шестерен или шестерен с малым числом зубьев, как обсуждалось ранее, зазор будет открываться по мере уменьшения делительной окружности. В таких случаях может потребоваться дополнить результаты расчета силы в сторону высоких значений.
Первым шагом в вычислении поперечного сечения микросхемы является определение базовой стойки. (См. Рисунок 17.)
Рисунок 16: Зубофрезерная фреза с внутренним воздухомНоменклатура
- H = Общая глубина зазора между зубьями (мм)
- a = Угол давления (градусы)
- V = смещение боковой поверхности от основания (мм)
- B = толщина стружки на боковой поверхности (мм)
- D = ширина основания (мм)
- A = Площадь межзубного промежутка (мм 2 )
- f z = Подача на зуб (мм)
- h ex = максимальная толщина стружки (мм)
- h м = Средняя толщина стружки (мм)
- v c = Скорость резания (м / мин.)
- M c = крутящий момент (Нм)
- P c = Полезная мощность (кВт)
- a e = рабочее зацепление (мм)
- D c = Диаметр фрезы (мм)
- k c1 = Удельная сила резания для данного материала (Н / мм 2 )
- м c = коэффициент удельного увеличения силы резания относительно толщины стружки
- kc = Удельная сила резания при м c с учетом
- n = об / мин
- z c = Общее количество эффективных зубьев фрезы
- M n = Размер модуля (мм)
- v f = Скорость подачи (мм / мин.)
В следующем примере показано, как рассчитать мощность и силы резания. Первым шагом является определение частоты вращения фрезы ( n ) на основе рекомендованной скорости резания ( v c ).
Формула:
Уравнение 2
Для этого примера:
Затем необходимо определить v f (подача мм / мин). Формула:
Уравнение 3
В этом примере мы предполагаем, что:
Далее необходимо определить k c .Формула:
Уравнение 4
В этом примере мы используем:
Этот коэффициент доступен в разделах материалов каталогов Sandvik Coromant и в технической литературе в печатном виде и в Интернете. (См. Рисунок 18.)
Средняя толщина стружки, или h м , определяется по формуле:
Уравнение 5
В этом примере мы используем полную глубину ( H ) 36 мм. Мы предполагаем однопроходную операцию, поэтому a e = H и f z (подача на зуб в мм) 0.04 мм:
Уменьшено до:
Это может быть уменьшено до:
Таким образом, для удельной силы резания мы имеем k c = 1900 / (0,130,25) = 3188,93
Далее необходимо определить площадь зубного промежутка. Возвращаясь к рисунку 17, мы должны сначала определить C . Формула для этого:
Уравнение 6
В этом примере предполагается размер модуля: M n = 16 и a = 20:
Далее, из рисунка 17 необходимо определить D .Формула:
Уравнение 7
В этом примере:
Снова из рисунка 17 необходимо определить V . Формула:
Уравнение 8
В этом примере:
Затем, как показано на рисунке 17, необходимо определить A , поэтому формула:
Уравнение 9
В этом примере это:
Выполнив эти шаги, мы можем рассчитать мощность на шпинделе, или P c .Формула:
Уравнение 10
В этом примере:
Следующий важный расчет — крутящий момент, или M c . Формула для этого расчета:
Уравнение 11
В этом примере:
Таким образом, модульная фреза 16 мм, диаметром 350 мм с восемью эффективными зубьями, работающая со скоростью 180 м / мин. скорость резки, подача со скоростью 524 мм / мин. Скорость подачи, резка нормальной низколегированной стали с твердостью 300 BHN потребует приблизительно 24 кВт на шпинделе с требуемым крутящим моментом 1392 Нм.
Можно написать простую компьютерную программу для работы с электронными таблицами, чтобы автоматизировать эти вычисления, чтобы сэкономить время и предотвратить ошибки вычислений. Это очень поможет инженеру-производителю зубчатых колес при планировании процесса. Та же самая таблица может быть интегрирована с расчетами времени цикла.
Рис. 18: Информация от Sandvik Coromant с конкретными данными о силе резанияЗаключение
Зубофрезерование или зарезание зубцов при обработке зубчатых колес — это хорошо зарекомендовавший себя, эффективный и стабильный метод изготовления зубчатых колес.Возможности повышения производительности, снижения затрат и создания качественных шестерен очевидны. Помощь квалифицированных поставщиков инструментов поможет направить инженера в правильном направлении. Новые концепции инструментов, прогрессивные концепции станков, методы термообработки и материалы для зубчатых колес постоянно меняют производственную среду. И новое поколение профессионалов в области оборудования, приходящих на рабочее место, привносит свежие идеи и готовность использовать новые методы от молодых инженеров, которые руководят технологическим сдвигом.
Наряду с этими факторами, все больше и больше используются многозадачные станки с ЧПУ для изготовления зубчатых колес. У производства зубчатых колес светлое будущее, и ближайшие годы обещают стать захватывающим временем для тех, кто работает в этой отрасли.
Список литературы
- Антониадис, А., Видакис, Н., и Билалис, Н. «Исследование усталостного разрушения твердосплавных инструментов при зубофрезеровании, Часть 1: Моделирование зубофрезерования с помощью МКЭ и вычислительная интерпретация экспериментальных результатов.”Журнал производственной науки и техники, ASME, Vol. 124, ноябрь 2002 г.
- Антониадис А., Видакис Н. и Билалис Н. «Исследование усталостного разрушения твердосплавных инструментов при зубофрезеровании, Часть 2: Влияние параметров резания на уровень напряжений инструмента — количественный параметрический анализ». Журнал производственной науки и техники, ASME, Vol. 124, ноябрь 2002 г.
- Исаков Эдмунд, канд. «Расчетная сила», Разработка режущего инструмента — Плюс, Вып. 64, выпуск 5, май 2012 г.
- «Техническое руководство Sandvik Coromant — токарная обработка, фрезерование, сверление, растачивание, крепление инструмента». AB Sandvik Coromant, 2010.
- Абуд, Али М. «Динамический анализ режущих сил при зубофрезеровании». Школа механики и системотехники, Университет Ньюкасл-апон-Тайн, Великобритания, декабрь 2002 г.
* Напечатано с разрешения правообладателя, Американской ассоциации производителей оборудования, 1001 N. Fairfax Street, Suite 500, Alexandria, Virginia 22314. Заявления, представленные в этом документе, принадлежат авторам и могут не отражать позицию или мнение Американская ассоциация производителей шестерен (AGMA).Этот документ был представлен в октябре 2015 года на осеннем техническом совещании AGMA в Детройте, штат Мичиган. 15ФТМ11.
Введение, особенности и типы фрез
Фреза — это вращающийся инструмент с одним или несколькими зубьями, который используется для фрезерных операций. Он в основном используется для обработки плоскостей, ступеней, канавок, формования поверхностей и резки деталей на фрезерных станках.Введение в фрезы
Фрезы — это многозубые роторные фрезы, каждая из которых эквивалентна токарному инструменту, закрепленному на вращающейся поверхности фрезы.Режущая кромка длиннее, нет холостого хода, а Vc выше, поэтому производительность выше. Существует множество видов фрез разной конструкции и широкого спектра применения. В зависимости от использования их можно разделить на три основные категории: фрезы для обработки плоских поверхностей, фрезы для обработки канавок и фрезы для обработки поверхностей.
Фрезерный инструмент — это высокоэффективный метод резки заготовок с помощью вращающегося многолезвийного инструмента. Инструмент вращается во время работы (для основного движения), заготовка перемещается (для движения подачи), и заготовка может быть зафиксирована, но вращающийся инструмент также должен двигаться (как основное движение, так и движение подачи).Инструментальные станки для фрезерования — это горизонтальные или вертикальные фрезерные станки или большие портальные фрезерные станки. Это могут быть обычные инструментальные станки или станки с числовым программным управлением. Обработка вращающейся фрезой в качестве режущего инструмента. Фрезерование обычно выполняется на фрезерном или расточном станке и подходит для обработки плоскостей, канавок, различных формующих поверхностей (например, шпонок для фрезерования цветов, шестерен и резьбы) и специальных форм форм.
Характеристики фрезы
1.Каждый зуб фрезы периодически задействуется в прерывистой резке.
2. Толщина реза каждого зуба в процессе резания варьируется.
3. Подача на зуб αf (мм / зуб), которая указывает относительное смещение заготовки за время, когда фреза поворачивается на один зуб.
Тип фрезы
1. Фрезы концевые цилиндрические Используется для обработки плоскостей на горизонтально-фрезерных станках.Зубья фрезы распределены по окружности фрезы и по форме делятся на прямые и спиральные. Зубы бывают двух типов: грубые и мелкозубые по количеству зубов. Фрезы со спиральными зубьями и крупными зубьями подходят для черновой обработки из-за небольшого количества зубьев, высокой прочности зубьев и большой устойчивости к стружке; Фрезы с мелкими зубьями подходят для чистовой обработки.
2. Торцевая фреза Используется в вертикальных фрезерных станках, торцевых фрезерных станках или портальных фрезерных станках для обработки плоскостей с резцами на торце и окружности, а также с крупными и мелкими зубьями.Его конструкция бывает трех типов: цельная, зубчатая и индексируемая.
3. Цельнотвердосплавные концевые фрезы Используется для обработки канавок, ступенчатых поверхностей и т. Д., Где зубья находятся на периферийных и торцевых поверхностях и не могут подаваться вдоль оси при работе. Осевая подача возможна, когда концевые зубья проходят через центр концевой фрезы.
4. Твердосплавные концевые фрезы с тремя канавками Применяется для обработки всех видов канавок и поверхностей ступеней с зубьями по бокам и по окружности.
5. Твердосплавные концевые фрезы с разным углом наклона спирали Для фрезерования канавок под определенным углом существуют фрезы двух типов: одно- и двухугловые.
6. Пильный диск фрезерный Он используется для обработки глубоких канавок и обработки деталей с большим количеством зубьев по окружности. Чтобы уменьшить трение во время фрезерования, с обеих сторон зубьев имеется угол малого отклонения 15 ‘~ 1 °. Кроме того, существуют концевые фрезы с канавкой под ключ, концевые фрезы с канавкой типа «ласточкин хвост», концевые фрезы с Т-образной канавкой и различные концевые фрезы для формовки.
7. Фреза Т-образная Используется для фрезерования Т-образных пазов.
Основные требования к режущей части материала фрезы
(1) Высокая твердость и устойчивость к истиранию:
При комнатной температуре режущая часть материала должна иметь твердость, достаточную для врезания в заготовку; с высокой стойкостью к истиранию инструмент не изнашивается, продлевая срок службы.
(2) Хорошая термостойкость:
Инструмент будет выделять много тепла во время процесса резания, особенно при высокой скорости резания температура будет очень высокой, поэтому материал инструмента должен иметь хорошую термостойкость, оба при высокой температуре могут сохранять более высокую твердость. , может продолжать резать, он обладает свойством высокотемпературной твердости, также известной как термическая твердость или красная твердость.
(3) Высокая прочность и хорошая ударная вязкость:
В процессе резания инструмент должен выдерживать сильные удары, поэтому материал инструмента должен иметь более высокую прочность, иначе его легко сломать и повредить. Поскольку резак подвержен ударам и вибрации, материал резца также должен иметь хорошую вязкость, чтобы предотвратить выкрашивание и растрескивание.
Общие материалы, используемые для фрез
1. Быстрорежущая инструментальная сталь (HSS, FSS и др.)) Он разделен на HSS общего и специального назначения. Он имеет следующие характеристики.
(1) Легирующие элементы вольфрам, хром, молибден и ванадий имеют более высокое содержание, а твердость при закалке может достигать HRC62-70, что позволяет поддерживать более высокую твердость при 6000 ° C.
(2) Хорошая прочность и ударная вязкость режущей кромки, высокая устойчивость к вибрации, может использоваться при производстве режущих инструментов со средней скоростью резания, для станков с меньшим количеством стали, использование высокоскоростного стального резака, все еще может резать плавно .
(3) Хорошая производительность процесса, ковка, обработка и заточка относительно просты, также можно изготавливать инструменты более сложной формы.
(4) По сравнению с твердосплавными материалами все еще существуют недостатки, такие как более низкая твердость и более низкая твердость и износостойкость.
2. Карбид: Он изготовлен из карбида металла, карбида вольфрама, карбида титана и металлического связующего на основе кобальта с помощью порошкового и неметаллургического процесса.Его основные особенности заключаются в следующем.
Он может выдерживать высокие температуры и поддерживать хорошую производительность резки при температуре около 800-10000 ° C. При резке он может выбрать в 4-8 раз более высокую скорость резания, чем HSS. Хорошая стойкость к истиранию при комнатной температуре и твердость. Низкая прочность на изгиб, плохая ударная вязкость, нелегко заточить лезвие, очень острое.
Обычно используемые карбиды можно разделить на три основные категории:
(1) Карбид вольфрама и кобальта (YG) Обычно используемые числа YG3, YG6, YG8, где числа указывают процентное содержание кобальта, чем больше содержание кобальта, тем выше ударная вязкость, тем выше устойчивость к ударам и вибрации, но снижается твердость и износостойкость.Таким образом, этот сплав подходит для резки чугуна и цветных металлов, а также может использоваться для резки ударопрочных заготовок и деталей из закаленной и нержавеющей стали.
(2) Карбид титана и кобальта (YT) Обычно используются марки YT5, YT15, YT30, а числа указывают процентное содержание карбида титана. Карбидные сплавы, содержащие карбид титана и выше, повышают температуру соединения стали, снижают коэффициент трения и обеспечивают небольшое увеличение твердости и износостойкости, но снижают прочность на изгиб и вязкость, что делает свойства хрупкими, поэтому этот тип сплава является приспособлен для резки стальных деталей.
(3) Карбид общего назначения В указанные выше два типа твердых сплавов добавлено нужное количество карбидов редких металлов, таких как карбид тантала и карбид ниобия и т. Д., Для утонения штампа, повышения твердости при комнатной температуре и высокотемпературной твердости, износостойкости, связывания. температура и стойкость к окислению, которые могут повысить ударную вязкость сплава, поэтому этот тип твердосплавного инструмента имеет лучшие характеристики резания и универсальность.
Типы концевых фрез
1. По режущей части материала фрезы. (1) Концевые фрезы из быстрорежущей стали: используются для более сложных инструментов.
(2) Твердосплавные концевые фрезы: большинство из них приварены или механически закреплены на корпусе фрезы.
2. По использованию фрезы. (1) Фрезы для обработки плоскости: цилиндрические фрезы, концевые фрезы и т. Д.
(2) Фрезы для обработки пазов (или ступеней): вертикальные фрезы, дисковые фрезы, фрезы для пильных полотен и т. Д.
(3) Фрезы для специальных поверхностей: Формовочные фрезы и т. Д.
3. По конструкции фрезы (1) Остроконечные зубчатые фрезы: усеченная форма задней части зуба прямая или сложенная, простая в изготовлении и заточке, с более острым краем.
(2) Фреза с зубьями лопаты: усеченная форма задней части зуба представляет собой спираль Архимеда. После заточки фрезы этого типа, если передний угол остается неизменным, а форма зуба остается неизменной, она подходит для формирования фрезы.
Основные геометрические параметры и функции фрезы.
1. Название каждой детали фрезы Базовая поверхность:
Плоскость, проходящая через любую точку резца и перпендикулярная скорости резания этой точки.
Рубанок:
Плоскость, проходящая через режущую кромку и перпендикулярная основанию.
Поверхность переднего лезвия:
плоскость, откуда стружка вытекает.
Задняя поверхность инструмента:
грань, противоположная обрабатываемой поверхности
2.Главный геометрический угол и функция фрезы цилиндрической (1) Передний угол γ0:
Угол между передней поверхностью лезвия и базовой поверхностью. Цель состоит в том, чтобы сделать режущую кромку острой, уменьшить деформацию металла во время резания и уменьшить удаление стружки, тем самым экономя усилия резания.
(2) Задний угол α0:
Угол между задней режущей поверхностью и режущей плоскостью. Его основная функция — уменьшить трение между задней поверхностью инструмента и режущей плоскостью и уменьшить шероховатость поверхности заготовки.
(3) Угол поворота 0:
Угол между касательной на режущей кромке спирального зуба и осью фрезерного инструмента. Функция состоит в том, чтобы позволить зубьям постепенно врезаться в заготовку и выходить из нее для повышения стабильности резания. Кроме того, для цилиндрических концевых фрез он позволяет стружке плавно стекать с торцевой поверхности.
3. Главный геометрический угол и назначение концевых фрез Концевая фреза имеет дополнительную вторичную режущую кромку, поэтому помимо переднего и заднего углов есть.
(1) Главный угол отклонения Kr:
Угол между основной режущей кромкой и обрабатываемой поверхностью. Изменение влияет на длину основной режущей кромки, участвующей в резке, изменяя ширину и толщину стружки.
(2) Угол дополнительного отклонения Krˊ:
Угол между подрезной кромкой и обработанной поверхностью. Эффект состоит в том, чтобы уменьшить трение между вторичной режущей кромкой и обрабатываемой поверхностью и повлиять на полировальный эффект вторичной режущей кромки на обрабатываемой поверхности.
(3) Угол наклона режущей кромки λs:
Угол между основной режущей кромкой и базовой поверхностью. В основном он служит для резки под углом.
4. Формовочная фреза Формовочные концевые фрезы — это специальные концевые фрезы для обработки формованных поверхностей, где профиль режущей кромки рассчитывается в соответствии с контуром обрабатываемой детали.
(1) Формовочные фрезы можно разделить на два типа: острые зубья и лопаточные зубья. Для фрезерования и переточки фрез с острыми краями требуются специальные плашки, которые сложнее изготавливать и затачивать.Задняя часть фрезы, образующей зубья лопаты, затачивается и затачивается на станине лопаты, при переточке затачивается только передняя поверхность фрезы. Должны быть соблюдены два условия: ① форма режущей кромки остается неизменной после переточки; и ②получен желаемый угол наклона спинки.
(2) Дорсальные кривые и уравнения Концевой профиль, перпендикулярный оси концевой фрезы, создается в любой точке на режущей кромке концевой фрезы, а его пересечение с задней поверхностью зуба называется обратной кривой зуба концевой фрезы.
Задний изгиб зуба должен удовлетворять двум основным условиям: первое состоит в том, что задний угол фрезы остается практически неизменным после каждой переточки; другой прост в изготовлении.
Кривые, удовлетворяющие неизменному заднему углу, представляют собой всего лишь логарифмические спирали, но их сложно построить. Спираль Архимеда удовлетворяет тому, что задний угол практически не изменился, прост в изготовлении и прост в использовании. Вот почему спирали Архимеда широко используются в производстве в качестве обратной кривой для формирования фрез.
Согласно геометрическим знаниям, значение радиуса вектора ρ в точках на линии архимедовой спирали увеличивается и уменьшается пропорционально значению угла θ радиуса вектора.
Таким образом, спираль Архимеда может быть получена, если она состоит из комбинации двусмысленного вращательного движения и двусмысленного прямолинейного движения по радиусу.
Выражается в полярных координатах: когда θ = 00, ρ = R, (R — радиус фрезы), когда θ> 00, ρ
Общее уравнение для задней части зуба фрезы: ρ = R-CQ
Предполагая, что лопата не возвращается, концевая фреза должна иметь межзубный угол ε = 2π / z для каждого поворота лопаты, и количество зубьев лопаты должно быть К.Чтобы лопата могла двигаться с одинаковой скоростью, кривая на кулачке должна быть архимедовой спиралью, и поэтому ее легко сделать. Кроме того, размер кулачка определяется только значением K объема продаж лопаты и не связан с количеством зубьев в диаметре фрезы и задним углом. Пока производство и продажи равны, кулачок универсален. Это причина, по которой спираль Архимеда теперь широко используется на задней части зубьев фрезерных фрез, образующих лопату.
Если известны радиус фрезы R и величина проходки лопаты K, можно получить C.
Когда θ = 2π / z ρ = R-K
тогда R-K = R-2πC / z ∴ C = Kz / 2π
5. Явления, возникающие после пассивации фрез (1) Из-за формы хлопьев они становятся крупными и чешуйчатыми.
(2) Шероховатость поверхности заготовки очень плохая, поверхность заготовки имеет яркие пятна и следы от ножа или рябь.
(3) В процессе фрезерования возникают очень сильные вибрации и аномальный шум.
(4) Если посмотреть на форму лезвия, на нем есть блестящие белые пятна.
(5) При фрезеровании стальных деталей твердосплавными фрезами часто вылетает большое количество огненного тумана.
(6) При фрезеровании стальных деталей на станах из быстрорежущей стали образуется много дыма, если они охлаждаются масляной смазкой.
Выше представлены описание, характеристики, тип и тип фрезы. В реальном производственном применении, когда пассивация фрезы, мы должны остановиться вовремя, чтобы проверить износ фрезы, если износ относительно небольшой, можно использовать для ремонта режущей кромки с помощью масляного камня, а затем использовать; если износ более сильный, необходимо заточить, чтобы предотвратить чрезмерный износ фрезы.
Типы фрезерных фрез, преимущества и применения — виртуальные события и потоки
Задача фрезы — удалить материал с заготовки. Имея это в виду, фрезы не состоят из одного лезвия. В то время как токарные операции, выполняемые на токарном станке, обычно включают однолезвийный режущий инструмент, резцы состоят из множества лезвий.
Когда фреза вращается относительно неподвижной заготовки, она удаляет материал.фрезы часто изготавливаются из твердых, прочных материалов, которые могут выдерживать значительные нагрузки без поломок или других повреждений. Например, резцы нередко имеют поликристаллическое алмазное покрытие. Фрезы с покрытием PCD служат в сто раз дольше, чем их аналоги без покрытия.
Обратной стороной использования фрез с покрытием PCD является то, что они не могут использоваться в приложениях, где температура превышает 600 градусов Цельсия. В этой статье мы научим вас всему, что вам нужно знать о фрезах и их свойствах.
Материалы, используемые для фрез
Самыми популярными материалами, используемыми для фрез, являются сталь и твердые сплавы:
Сталь (HSS, FSS)
Быстрорежущая сталь, марка инструментальной стали, содержит несколько легирующих добавок, которые обеспечивают лучшую реакцию на нагрев и износ, чем обычная углеродистая сталь. По мере увеличения срока службы такой фрезы стоимость увеличивается. Он делится на HSS общего и специального назначения.
Он имеет следующие особенности. Легирующие элементы вольфрама, хрома, молибдена и ванадия имеют более высокое содержание, а твердость при закалке может достигать HRC62-70, что позволяет сохранять более высокую твердость при 6000 ° C.
Хорошая прочность и ударная вязкость режущей кромки фрезы, высокая устойчивость к вибрациям, может использоваться для изготовления режущих станков со средней скоростью резания, в случае станков с меньшим количеством стали, использование высокоскоростной фрезы, по-прежнему может плавно резать.
Высокая эффективность процесса, ковка, обработка и заточка относительно просты, и можно изготавливать инструменты более сложной формы. По сравнению с твердосплавными материалами все еще существуют недостатки, такие как более низкая твердость и более низкая твердость и износостойкость.
Карбид
Твердосплавные фрезы прочнее, чем из быстрорежущей стали, но их прочность не так хороша. Более высокая твердость обеспечивает лучшую защиту от износа, но более низкая прочность делает его немного более уязвимым к растрескиванию и сколам.
Изготавливается из карбида металла, карбида вольфрама, карбида титана и металлических связующих на основе кобальта в порошковых и неметаллургических процессах. Его основные особенности заключаются в следующем. Он может выдерживать высокие температуры и поддерживать хорошую эффективность резки при температуре около 800-10000 ° C.
При резании твердосплавной фрезой скорость резания может быть в 4-8 раз выше, чем скорость резания из быстрорежущей стали. Хорошая стойкость к истиранию и твердость при комнатной температуре. Низкая прочность на изгиб, низкая вязкость, нелегко затачивать лезвие, очень острый.
Типы фрез
Все фрезы характеризуются наличием множества канавок, каждая из которых действует как лезвие для соскабливания материала с заготовки. Имея это в виду, существуют разные типы фрез. Например, концевая фреза — это фреза с зубьями на конце и по бокам.
Применяются для обработки стали и твердого сплава, они обычно используются при вертикальном фрезеровании. Черновой нож — еще одна распространенная форма фрезы. Вверху черновые фрезы имеют глубокие пазы, способные удалять излишки материала из заготовки.
Черновые фрезы, также известные как фрезы-рыхлители, широко используются в крупномасштабном производстве. Третий тип фрез — фрезы шаровых мельниц. Фреза с шаровой мельницей, также известная как фреза со сферическим концом, имеет полусферическую конструкцию, которая сводит к минимуму нагрузку на заготовку.
Наконец, боковые фрезы — это фрезы с зубьями с обеих сторон и вперед. Боковые и торцевые фрезы используются более 200 лет.
Фактически, тогда они были самым распространенным типом фрез. Фреза — неотъемлемая часть фрезерного станка. Он состоит из нескольких ножей и отвечает за соскабливание материала заготовки, тем самым изменяя ее форму.
Различия между торцевыми фрезами и концевыми фрезами
Это два наиболее распространенных инструмента для фрезерных операций, каждый из которых использует разные типы фрез: концевые фрезы и торцевые фрезы.Различие между торцевым фрезерованием и торцевым фрезерованием заключается в том, что торцевая фреза использует как конец, так и стороны фрезы, в то время как торцевое фрезерование используется для горизонтального фрезерования.
Концевая фреза
Обычно у этих инструментов плоское дно, но не всегда. Также доступны круглые фрезы. Концевые фрезы похожи на сверла тем, что их можно разрезать в осевом направлении. Но преимущество фрезерования — возможность обрезать края.
Торцевая фреза
Торцевые фрезы не режут в осевом направлении.Вместо этого режущие кромки всегда находятся на кромках режущей головки. Режущие зубья представляют собой сменные твердосплавные пластины, которые продлевают срок службы инструмента при сохранении высокой эффективности резания.
Какой тип фрезы выбрать?
Выбор подходящей фрезы должен основываться на обрабатывающих возможностях станков, свойствах обрабатываемых материалов, процедурах обработки, параметрах резания и других факторах. Основное правило выбора фрез с ЧПУ — удобство сборки и регулировки, хорошая жесткость, долговечность и точность.
Попробуйте выбрать более короткий держатель инструмента, чтобы повысить жесткость обработки. Размер режущего инструмента должен соответствовать размеру поверхностей обрабатываемых деталей. Кроме того, концевую фрезу часто используют для обработки периферийного контура плоских деталей, а концевую фрезу из твердого сплава можно использовать для фрезерования плоских поверхностей.
Если вы выберете высокоскоростную фрезу, вы сможете обрабатывать неровности и вогнутости. Спиральная фреза — идеальный вариант для обработки черновой поверхности или обработки отверстий.Наконец, шаровые фрезы, кольцевые фрезы, конические фрезы и дисковые фрезы часто используются для обработки полного профиля и профиля с переменным углом.
Производители фрезерных станков на IMTS-Exhibition.com
Вы можете найти множество поставщиков фрезерных фрез на imts-exhibition.