Осмысленный выбор бюджетного плазмореза для станка с ЧПУ — Оборудование для плазменной и газовой резки
Ну и последний в этой группе, заслуживающий внимания Сварог CUT70
Произведение Китайской фирмы Jasic. Весьма достойный аппарат с жесткой характеристикой резки.
Неплохо, что нижний предел тока — 20 ампер. Плохо, что обычно уже закомплектован резаком с 6-и метровым шлангом.
Пользовали такие достаточно часто. Следует заметить, что изредка встречаются экземпляры с некачественной сборкой (китай, однако).
С родным резаком CS-81 режет в машинном режиме до 16мм стали на пробой. После замены резака на 141-й с неплохой скоростью (около 10мм/сек) резали аллюминий 16мм. Что соответствует стали 20мм. Для сравнения ElmaCUT 70 (профессиональный трансформаторный плазморез) с аналогичным резаком с такой задачей не справился.
Расход воздуха достаточно большой — на 6 атм где то более 250 литров/мин. Что видимо и обеспечивает слегка большие возможности. Компрессора с производительностью по входу менее 500 л/мин явно не хватит.
Касаемо потребности в фильтрах влаго-масло отделения.
У Трафиметовских резаков внутри воздушного шланга идет силовой кабель в виде медной плетенки. Компрессор, особенно поршневой, полюбому гонит масло и влагу в воздухе. Эта масло-водяная смесь постепенно накапливается в плетенке-кабеле, как в губке и спустя время начинает выдавливаться в зазор катод-сопло.
При запуске начинается чехарда с чиханиями и внезапными погасаниями плазмы. У ЧПУ при этом частенько «сносит голову». Уровень помех возрастает лавинообразно.
Лечится достаточно просто.
Откручиваем разъем и разбираем резак, подсоединяем к ВАЗовскому топливному насосу подходяшим шлангом. Опускаем второй конец и насос в банку со………СПИРТОМ (чистым). И гоняем минут 30-40. По степени пожелтения спирта понимаем, что фильтр был нужен. Затем — продуваем воздухом. Собираем и радуемся.
Изменено 12.2014 12:35 » data-short=»6 г»>10 декабря, 2014 пользователем Sergey-BТипичные ошибки оператора при плазменной резке и способы их избежания
Все знают что простои в работе из-за выхода оборудования из строя несут большие убытки для производства, тогда как их можно было бы избежать при правильном использовании оборудования.
Обращая внимание на вещи описанные ниже в статье и проводя своевременные процедуры можно избежать простоев и крупных поломок, сэкономив деньги на ремонте, не потерять оборудование на время его ремонта (или же не потерять вовсе из-за неремонтопригодности) и в целом увеличить ресурс его работы.
Особое внимание, естественно, стоит уделить износу расходных материалов поскольку они со временем изнашиваются, а качество и точность реза уменьшается. Увеличенный краевой скос и деформация края являются важными признаками для оператора, что требуется замена непригодной детали.
Чтобы устранить эти проблемы, оператор нередко заменяет весь набор расходных материалов сразу — электрод, сопло и защитную крышку, вместо того, чтобы оценивать каждый компонент по отдельности. Это приводит к чрезмерному использованию расходных материалов, что отрицательно сказывается на общей стоимости эксплуатации и увеличивает стоимость производства.
Эта статья поможет вам избежать лишних трат и своевременно реагировать на проблемы, а также заблаговременно предупредить их.
Итак, вот список ошибок, которые стоит избегать.
Использование расходных материалов до тех пор, пока они не выйдут из строя
Если посмотреть на ряд деталей одного типа, которые были вырезаны при таком подходе, можно безошибочно определить те детали, на которых сопло или электрод были уже «на подходе». Использование сильно изношенных сопел и электродов может не только привести к браку при вырезке детали, но и стать причиной дорогостоящего ремонта пламенного резака и даже аппарата плазменной резки, во время которого машина плазменной резки будет простаивать.
Новая деталь | Изношенная деталь | |
Защитная насадка Её следует заменять только при наличии видимых повреждений, таких как образование шлака, вмятины или ожоги, или если его трудно надеть на горелку или защитная крышка не может быть ровно установлена из-за повреждений. |
||
Защитная крышка
Как следует из его названия, защитный колпачок заглушает защитный газ с целью дополнительного охлаждения сопел и улучшения края режущей кромки. Отверстие в защитной крышке имеет решающее значение для качества реза, поэтому его следует заменить, когда оно становится сожженным, согнутым, когда на него попадает шлак и оно становится не круглым. Для удаления брызг (шлака), который застрял на защитной крышке, можно использовать абразивную щётку. Всегда проверяйте уплотнительные кольца на предмет возможных повреждений, таких как трещины и разрывы. Убедитесь, что уплотнительные кольца правильно смазаны с использованием рекомендованной производителем смазки. Инструкции по смазке см. в руководстве изготовителя. |
||
Внутреннее защитное кольцо Эта деталь имеет медный корпус с нажимным изоляционным кольцом для размещения в защитной крышке. Цель внутреннего удерживающего колпачка состоит в том, чтобы циркулировать охлаждающую жидкость вокруг внешней части сопла и распределять газ на защитный колпачок через крошечные отверстия в изоляторном кольце. Эта деталь не изнашивается плазменной дугой и может легко выдерживать до 30 или более замен электродов. Заменяйте только в том случае, если отверстие сожжено, согнуто или повреждено и не является круглым, или если повреждено изоляционное кольцо или отверстия по периметру. |
||
Сопло Сопло – один из важнейших элементов плазмотрона. Сопло формирует струю плазмы, которая, проходя через отверстие, осуществляет рез. Когда оно новое, это отверстие будет идеально круглым с четко определенным острым краем. Сопло должно быть заменено, когда отверстие начинает изнашиваться во внешнем или внутреннем отверстии, делая края менее острыми и ухудшая качество реза. На внутренней стороне сопла могут возникать более светлые участки, вызванные пуском дуги, но это не является причиной замены. Для наивысшего качества резки следует заменять сопло в два раза чаще, чем электрод. |
||
Завихрительное кольцо (шазовый диффузор) Вихревое кольцо изготовливается из высокотемпературного материала, такого как Vespel или керамики, и поэтому не изнашивается плазменной дугой. Оно служит для завихрения плазмообразующего газа вокруг электрода и направления его в сопло. Вихревое кольцо также изолирует отрицательно заряженный электрод от положительно заряженного сопла. Диффузор влияет на множество факторов, и без него вы получите гораздо более короткий срок службы всех остальных расходных частей и плохое качество реза. Необходимо следить за тем, чтобы маленькие отверстия не содержали грязи и мусора, и их следует заменять, если обнаружены трещины или сколы, так как даже микроскопическая трещина может нарушить газовый поток. Всегда проверяйте уплотнительные кольца на предмет возможных повреждений, таких как трещины и разрывы. Убедитесь, что уплотнительные кольца правильно смазаны с использованием рекомендованной производителем смазки. Инструкции по смазке см. в руководстве изготовителя. В среднем 1 диффузор способен пережить более 50 замен электрода. |
||
Электрод Электрод является основным и расходным материаом в плазменной резке и требует наиболее частой замены. Электрод может быть изготовлен из меди или серебра или их комбинации и содержит отдельную вставку из эмиттерного стержня, изготовленную из гафния или вольфрама. Эмиттерный стержень обладает меньшим сопротивлением току, чем медь, что предотвращает сжигание электрода при генерировании большого тока дуги. Медь обладает низким электрическим сопротивлением, из-за чего электрическая дуга может пройти на корпус, что повлечёт повреждение других элементов — сопла, защитной крышки, а также самого плазмотрона. Чтобы этого не допустить, электрод следует менять в тот момент, когда на вставке появится ямка по размерам равная диаметру самой вставки. |
||
Безопасное значение глубины износа эмиттера составляет примерно 0,040 дюйма (1,02 мм) для медных электродов и 0,1 дюйма (2,54 мм) для серебряных электродов. |
Слишком частая замена сопел и электродов
Среди использованных сопел и электродов достаточно часто можно встретить такие, которые еще можно использовать при резке. Излишне частая замена расходников также очень распространена среди операторов металлорежущих станков с ЧПУ, и в особенности, машин плазменной резки. При замене сопла или электрода оператор должен четко знать, на что обращать внимание. Сопло требует замены в следующих ситуациях:
1. Если сопло имеет деформации снаружи или изнутри. Это часто бывает при слишком маленькой высоте пробивки и при непрорезе металла. Расплавленный металл попадает на внешнюю поверхность сопла или защитного колпака и деформирует ее.
2. Если выходное отверстие сопла по форме отличается от окружности. При большой высоте пробивки, если движение начинается до прореза металла, то дуга отклоняется от перпендикуляра к листу и проходит через край отверстия сопла. Чтобы определить, изношен ли электрод, нужно посмотреть на вставку из металла серебристого цвета на торце медного электрода (как правило, используется сплав циркония, гафния или вольфрама). В общем случае, электрод считается работоспособным, если этот металл вообще есть и глубина лунки на его месте не превышает 2 мм для воздушно-плазменной или кислородно-плазменной резки. Для резки плазмой в среде защитного газа (азота или аргона) глубина лунки может достигать 2,2 мм. Завихритель нуждается в замене лишь в том случае, если при тщательном осмотре можно выявить забитые отверстия, трещины, следы вызванные попаданием дуги, или сильный износ. Завихрители особенно часто заменяются преждевременно. То же самое касается и защитных колпаков которые нуждаются в замене только в случае физического повреждения. Очень часто защитные колпачки могут быть очищены наждачной бумагой и использованы вновь.
Использование неправильных настроек параметров плазменной резки и расходных материалов
Выбор расходников при плазменной резке зависит от вида разрезаемого металла (сталь, медь, латунь, нержавейка и т.д.), от его толщины, выставленного тока дуги на аппарате плазменной резки, плазмообразующего и защитного газов и т.д. Справочное руководство оператора машины плазменной резки описывает, какие расходные материалы использовать в случае разных режимов процесса резки. Указанные в инструкции оператора режимы, рекомендации относительно настроек плазменной резки следует соблюдать. Использование расходных материалов (сопел, электродов) несоответствующих текущему режиму плазменной
резки обычно приводит к ускоренному выходу расходников из строя и к значительному ухудшению качества пламенного реза. Очень важно выполнять плазменную резку металла именно с тем током дуги, на который рассчитаны используемые расходные материалы. Например, не стоит резать металл плазмой на 100 амперах, если в плазменном резаке стоит сопло на 40 ампер, и т.д. Самое высокое качество реза достигается, когда ток на аппарате плазменной резки выставлен на 95% от номинального тока резки, на который рассчитано сопло. Если установлен режим плазменной резки с заниженным током дуги, то рез будет зашлакованный, и на обратной стороне вырезаемых деталей будет значительное количество грата, пламенный рез будет неудовлетворительного качества. Если установленный на установке плазменной резки ток слишком высок, то срок службы сопла значительно сокращается.
Неправильная сборка плазменного резака
Пламенный резак должен быть собран таким образом, чтобы все его детали плотно прилегали друг к другу, и не было бы впечатления «разболтанности». Плотность прилегания деталей плазмотрона обеспечивает хороший электрический контакт и нормальную циркуляцию воздуха и охлаждающей жидкости через плазменный резак. Во время замены расходных материалов нужно стараться разбирать плазменный резак на чистой поверхности, чтобы грязь и металлическая пыль, образующиеся при плазменной резке, не загрязнили плазмотрон. Чистота при сборке/разборке плазменного резака очень важна и, тем не менее, это требование часто не соблюдается.
Невыполнение регулярного планового обслуживания плазмотрона
Плазменный резак может работать в течение многих месяцев, и даже лет без должного обслуживания. И, тем не менее, газовые каналы и каналы охлаждающей жидкости внутри плазменного резака должны содержаться в чистоте, посадочные места сопел и электродов должны проверяться на предмет загрязнения или повреждений. Грязь, металлическая пыль должны удаляться из плазменного резака. Для чистки плазмотрона следует использовать чистую хлопчатобумажную тряпочку и жидкость для чистки электрических контактов либо перекись водорода.
Резка металла без проверки давления плазмообразующего газа или подачи охлаждающей жидкости в плазморез
Расход и давление плазмообразующего газа и охлаждающей жидкости нужно проверять ежедневно. Если расход недостаточный, детали резака не будут в должной степени охлаждаться и их срок службы будет снижен. Недостаточный проток охлаждающей жидкости из-за изношенного насоса, забитых фильтров, недостаточного количества охлаждающей жидкости, является распространенной причиной поломок плазменных резаков. Постоянное давление плазмообразующего газа очень важно для поддержания режущей дуги и для качественного реза. Избыточное давление плазмообразующего газа является распространенной причиной затрудненного поджига плазменной дуги, притом, что все остальные требования к настройкам, параметрам и процессу плазменной резки полностью удовлетворены. Слишком высокое давление плазмообразующего газа является причиной быстрого выхода из строя электродов. Плазмообразующий газ обязательно должен быть очищен от примесей, т. к. его чистота оказывает сильное влияние на срок службы расходных материалов и плазмотрона в целом. Компрессоры, подающие воздух в аппараты плазменной резки имеют тенденцию к загрязнению воздуха маслами, влагой и мелкими частицами пыли.
Пробивка при малой высоте плазмотрона над металлом
Расстояние между заготовкой и срезом сопла плазмотрона оказывает огромное влияние, как на качество реза, так и на срок службы расходных материалов. Даже небольшие изменения в высоте плазменного резака над металлом могут значительно повлиять на скосы на кромках вырезаемых деталей. Высота плазменного резака над металлом во время пробивки особенно важна. Распространенной ошибкой является пробивка при недостаточной высоте плазмотрона над металлом. Это приводит к тому, что расплавленный металл выплескивается из лунки, образованной при пробивке и попадает на сопла и защитные колпачки, разрушая эти детали. Тем самым существенно ухудшается качество реза. Если пробивка происходит, когда плазменный
резак касается металла, то может произойти «втягивание» дуги. Если дуга «втягивается» в плазмотрон, то электрод, сопло, завихритель, а иногда, и резак целиком — разрушаются. Рекомендуемая высота пробивки равна 1.5-2 величины толщины разрезаемого плазмой металла. Следует отметить, что при пробивке достаточно толстого металла рекомендуемая высота получается слишком большой, дежурная дуга не достает до поверхности листа металла, следовательно, процесс резки на рекомендуемой высоте начать невозможно. Однако если пробивка будет производиться на высоте, на которой плазморез может зажечь дугу, то брызги расплавленного металла могут попасть на плазмотрон. Решением этой проблемы может быть применение технологического приема под названием «подпрыжка». При отработке команды на включение резки, плазменная резка включается на небольшой высоте, затем резак поднимается вверх на заданную высоту подпрыжки, на которой брызги металла не достают до резака. После отработки пробивки резак опускается на высоту врезки и начинается движение по контуру.
Плазменная резка металла на слишком большой, либо слишком малой скорости
Несоответствие скорости плазменной резки выбранному режиму существенно сказывается на качестве реза. Если установленная скорость резки слишком низкая, на вырезаемых деталях будет большое количество облоя и разнообразных наплывов металла по всей длине реза на нижней части кромки деталей. Низкие скорости резки могут стать причиной увеличения ширины реза и большого количества брызг металла на верхней поверхности деталей. Если установлена слишком высокая скорость резки, дуга будет загибаться назад, вызывая деформацию кромок вырезаемой детали, будет узкий рез, и небольшие бусинки грата и облоя в нижней части кромки реза. Грат образованный при высокой скорости резки тяжело удаляется. При правильно выбранной скорости резки количество грата, облоя и наплывов металла будет минимальным. Поверхность кромки пламенного реза при правильно выбранной скорости должна быть чистой и механическая обработка должна быть минимальной. В начале и конце реза может произойти «отклонение» дуги от перпендикуляра. Это происходит из-за того, что дуга не успевает за резаком. Отклонение дуги приводит к тому, что она врезается в боковую поверхность сопла, нарушая тем самым его геометрию. Если выполняется врезка с кромки, центр отверстия сопла должен находиться точно на линии кромки детали. Это особенно важно в комбинированных станках, в которых применяется и дыропробивная головка и плазморез. Отклонение дуги может произойти и когда плазмотрон при включенной резке проходит через край листа, или если линия выхода из контура с резкой (lead out) пересекает старый рез. Необходима точная настройка параметров времени, чтобы уменьшить проявления этого эффекта.
Механическое повреждение или поломка плазменного резака
Столкновения резака с листом, вырезанными деталями или ребрами раскроечного стола могут полностью вывести резак из строя. Столкновений резака с вырезаемыми деталями можно избежать, если в управляющей программе задавать холостые проходы вокруг, а не над вырезанными деталями. Например, в программе оптимального раскроя ProNest производства MTC-Software присутствует такая возможность, что позволяет свести риск поломки плазмотрона к минимуму и сэкономить значительные средства. Стабилизаторы высоты резака также обеспечивают некоторую защиту от столкновений с металлом. Однако, если используется только лишь датчик высоты резака по напряжению дуги, то в конце реза могут происходить «клевки», т.к. напряжение дуги меняется в результате ее «отклонения» и резак опускается вниз чтобы его компенсировать. В системах ЧПУ применяется многоуровневая система защиты от столкновения с металлом. Используется как датчик касания, измеряющий сопротивление между антенной вокруг резака и листом, емкостной датчик и датчик
напряжения дуги. Это позволяет в полной мере использовать преимущества каждого из типов датчиков. Также, для защиты резака можно применять «ломкие» кронштейны, которые при столкновении сломаются быстрее, чем плазменный резак. Таким образом, грамотный оператор машины плазменной резки может сэкономить своему предприятию огромные деньги, время и накладные расходы на плазменную резку. Результатом работы хорошего оператора МТР будет возросшая рентабельность плазменной резки и увеличение прибыли предприятия в целом. Надеемся, что изложенные в этой статье рекомендации по плазменной резке металла позволят выполнить настройку плазменной резки и подобрать режимы реза для каждого конкретного случая.
Преимущества и недостатки плазменной резки
Преимущества и недостатки плазменной резки по сравнению с другими методами резки металлов?
Резка металлов — проблема, с которой приходится сталкиваться и в цеху, и на стройплощадке, и в мастерской. Простые решения вроде автогена устроят многих, но не всех. Если объем работ по резке металла большой, а требования к качеству реза высоки, то стоит подумать об использовании аппарата плазменной резки (плазмореза).
Первые установки и аппараты плазменной резки появились более полувека назад, но широкому кругу мастеров они стали доступны только в последние два десятилетия.
ПРЕИМУЩЕСТВА:
Какие преимущества в работе дает аппарат или станок плазменной резки металла в работе?
1. При правильном подборе мощности он позволит в 4-10 раз (по сравнению кислородной горелкой) повысить производительность. По этому параметру плазморез уступит лишь промышленной лазерной установке, зато намного выиграет в себестоимости. Экономически целесообразно использовать плазменную резку на толщинах металла до 50-60мм. Кислородная же резка более предпочтительна при раскрое стальных листов толщиной свыше 50 мм.
2. УНИВЕРСАЛЬНОСТЬ. Плазменная резка позволяет обрабатывать и сталь, и чугун, и алюминий, и медь, и титан, и любой другой металл, причем работы выполняются с использованием одного и того же оборудования: достаточно выбрать оптимальный режим по мощности и выставить необходимое давление воздуха. Важно отметить и то, что качество подготовки поверхности материала особого значения не имеет: ржавчина, краска или грязь помехой не станут.
3. ТОЧНОСТЬ и ВЫСОКОЕ КАЧЕСТВО РЕЗА. Современные плазморезы обеспечивают минимальную ширину реза и «чистые» без наплывов, перекаливания и грата кромки, почти не требующие дополнительной обработки. Немаловажно и то, что зона нагрева обрабатываемого материала намного меньше, чем при использовании автогена, а поскольку термическое воздействие на участке реза минимально, то и тепловые деформации вырезанных деталей незначительны, даже если они небольшой толщины.
4. БЕЗОПАСНОСТЬ, обусловленная отсутствием взрывоопасных газовых баллонов.
5. НИЗКИЙ уровень загрязнения окружающей среды. Касательно экономической стороны вопроса, то совершенно очевидно, что при больших объемах работ плазменная резка выгоднее той же кислородной или, например, механической. В остальных же случаях нужно учитывать не материалы, а трудоемкость использования. Например, сделать фигурный рез в толстом листе недолго и автогеном, но может потребоваться продолжительная шлифовка краев.
НЕДОСТАТКИ:
Ну а теперь поговорим о недостатках. Первый из них — относительно скромная максимально допустимая толщина реза, которая даже у мощных аппаратов редко превышает 80-100 мм. В случае же с кислородной резкой максимально допустимая толщина реза для стали и чугуна может достигать 500 мм.
Следующий недостаток метода — довольно жесткие требования к отклонению от перпендикулярности реза. В зависимости от толщины детали угол отклонения не должен превышать 10-50°. При выходе за эти пределы наблюдается значительное расширение реза и, как одно из следствий, быстрый износ расходных материалов.
Наконец, сложность рабочего оборудования делает практически невозможным одновременное использование двух резаков, подключенных к одному аппарату, что с успехом применяется при резке штучным электродом.
Процесс плазменной резки (принцип работы плазмореза)
Для начала определим, что же есть плазма. В данном случае это нагретый электрической дугой до высокой температуры (порядка 25000 °C) воздух в ионизированном состоянии. Последнее означает, что он утрачивает свойства диэлектрика и приобретает способность проводить электрический ток. В процессе резки плазменный поток становится проводником для тока, расплавляющего металл, и сам же его выдувает.
Для начала определим, что же есть плазма. В данном случае это нагретый электрической дугой до высокой температуры (порядка 25000 °C) воздух в ионизированном состоянии. Последнее означает, что он утрачивает свойства диэлектрика и приобретает способность проводить электрический ток. В процессе резки плазменный поток становится проводником для тока, расплавляющего металл, и сам же его выдувает.
Рабочий орган аппарата называется плазмотрон. Под этим словом подразумевается плазменный резак с кабель-шланговым пакетом, подключаемый к аппарату. Иногда плазмотроном ошибочно называют аппарат плазменной резки целиком. Разновидностей плазмотронов достаточно много. Но наиболее распространены и более всего пригодны для резки металлов плазмотроны постоянного тока прямой полярности. По виду дуги различают плазмотроны прямого и косвенного действия. В первом случае разрезаемое изделие включено в электрическую цепь, и дуговой разряд возникает между металлической деталью и электродом плазматрона. Именно такие плазмотроны применяются в устройствах, предназначенных для обработки металлов, включая и аппараты воздушно-плазменной резки. Плазматроны косвенного действия применяются, в основном, для обработки неэлектропроводных материалов (у них электрическая дуга возникает в самом резаке).
Сопло — важнейший элемент, определяющий возможности плазмотрона. При плазменной резке применяются сопла небольшого (до 3 мм) диаметра и большой (9-12 мм) длины. От размера диаметра сопла плазмотрона зависит количество воздуха, которое способен пропустить плазмотрон, этот параметр необходимо учитывать при подборе компрессора. Это также влияет на ширину реза и охлаждение плазмотрона. Что касается длины, то чем она больше, тем выше качество реза. Однако чрезмерное увеличение этого параметра ведет к снижению надежности работы и быстрому разрушению сопла. Считается, что длина канала должна быть больше диаметра в 1,5-1,8 раза.
Электродом (катодом) внутри плазматрона служит металлический стержень — другие конструкции в недорогих аппаратах не применяются. То же можно сказать и о материале: разновидностей изобилие, но массово используется лишь электрод из гафния.
Теперь пару слов о рабочих газах, используемых при плазменной резке. Их можно разделить на плазмообразующие и защитные (транспортирующие). Для резки в обычных плазменных системах бытового назначения (сила тока дуги — ниже 200 А, максимальная толщина реза — до 50 мм) сжатый воздух применяют и как плазмообразующий, и как защитный газ. При этом достигается удовлетворительное качество реза, хотя и наблюдается некоторое азотирование и окисление обрабатываемой поверхности. В более сложных системах применяются иные газовые смеси, содержащие кислород, азот, водород, гелий, аргон.
Выбор аппарата плазменной резки
Даже самые доступные аппараты плазменной резки сложны и довольно дороги в сравнении, например, со сварочными, поэтому к выбору недешевой техники нужно подходить осознанно. Прежде всего необходимо определиться, как обычно, с целями и задачами.
Первый параметр, без учета которого бесполезно учитывать остальные, — это максимально допустимая толщина реза. Данная величина обычно приводится для углеродистой стали, реже — для нержавеющей, еще реже — для алюминия и очень редко — для меди. Поскольку на максимально допустимую глубину реза сильно влияет теплопроводность материала, то для сплавов на основе меди этот показатель примерно на 30% ниже, чем для сплавов на основе железа. И если в технических характеристиках аппарата заявлена максимально допустимая толщина реза стали в 10 мм, это будет означать, что максимальная глубина реза медных сплавов составит 7 мм. Таким образом, вторым по важности показателем станет тип сплава, с которым предстоит работать.
Следующий фактор — планируемый режим эксплуатации плазмореза. Как и в случае со сварочными аппаратами, он определяется параметром «ПВ» (продолжительность включения), который определяет отношение времени работы аппарата ко времени, необходимому для его охлаждения. В некоторых промышленных аппаратах плазменной резки ПВ может приближаться к 100%, для ручной же резки металла вполне достаточно 40-50%.
На практике это выглядит следующим образом. Если ПВ плазмореза составляет 50%, то в течение часа эксплуатации он должен 30 минут работать и 30 минут остывать. При ручной резке приходится время от времени перемещаться или перемещать изделие и периодически выключать кнопку поджига на плазмотроне. Это время как раз и идет в зачет охлаждения, и поэтому работа кажется непрерывной. Такая формула дает сбой при работе с толстыми листами металла или при автоматической плазменной резке с ЧПУ, когда время реза может быть значительным. Дело в том, что параметр ПВ определяется для 10-минутного цикла, поэтому в начале смены, пока аппарат холодный, он будет отработать без перерыва и 15 минут даже при низком ПВ, а вот при цикличной работе может отключиться и после 5 минут непрерывной резки.
Когда ключевые параметры, определяющие принципиальную возможность использования аппарата, определены, следует уделить внимание такому аспекту, как удобство использования. Тут первостепенное значение приобретает мобильность, точнее, радиус действия, на который можно свободно удаляться от малоподвижного аппарата, «прикованного» к своему месту компрессором. Так, длина кабель-шлангового пакета плазмотрона может варьироваться до десятков метров. Кстати, важна не только длина: некоторые производители заявляют ее на уровне 30 м и более, но «забывают» сообщить о том, имеются ли евроразъемы на плазмотроне и источнике. Если таких разъемов нет, то укоротить или удлинить плазмотрон вряд ли получится, и всякий раз разматывать его для того, чтобы резать небольшие по размерам листы, будет утомительно. Главный же минус длинного плазматрона не в этом, а в том (и производители об этом, как правило, тоже умалчивают!), что при его длине свыше 20 метров наблюдается потеря мощности, причем довольно ощутимая. Поэтому разумнее всего выбирать плазмотрон небольшой (6-12 м) длины, оснащенный евроразъемом, чтобы при необходимости была возможность удлинить конструкцию, используя быстронаращиванмый удлинитель плазмотрона. Это будет, кстати, удобно и при работе на открытом воздухе в неблагоприятных условиях, когда выносить из помещения аппарат нежелательно. Однако, как уже отмечалось, использовать удлинитель нужно лишь в случае действительной необходимости.
Очень важный вопрос — проблема расходных материалов: электродов (катодов) и сопел. Важно, чтобы они были доступны и недороги. Как правило, износ этих деталей происходит или одновременно или с небольшим «разбросом» (один катод на два сопла). Одного сопла в среднем хватает на целую рабочую смену (при работе с деталями, толщиной до 10 мм).
Момент, не относящийся напрямую к плазматрону, но требующий обязательного учета, — это система подачи воздуха. Если отбросить самые маломощные модели, оборудованные встроенным компрессором и воспринимаемые многими профессионалами как малополезные игрушки, то следует помнить, что для работы плазматрону нужен мощный компрессор. И не он один: при достаточно большом расходе воздуха (100-250 л/мин при 0,4-0,6 МПа) жесткие требования предъявляются и к его качеству, а значит не обойтись без вспомогательных устройств — таких как влаго- и маслоотделители, фильтры. Поступать в аппарат воздух должен равномерно, без пульсаций, поскольку они серьезно влияют на стойкость сопел и электродов, на стабильность поджига дуги и, как следствие, на качество реза, а значит, нужен объемный ресивер.
ПРЕДЛОЖЕНИЕ ДЛЯ ЛЮБИТЕЛЯ
Среди современных устройств плазменной резки можно выделить отдельную и наиболее интересную для рядового потребителя категорию — переносные инверторные источники плазмы, применяемые при ручной резке. Их основные достоинства: низкое энергопотребление, компактность, небольшой вес, эргономичный дизайн. Недостатки: ограничение по максимальной мощности (не более 70 А), и, как следствие, по максимальной толщине реза (до 15-20 мм). Также придется мириться с невысокой продолжительностью включения и чувствительностью к перепадам напряжения. Оборудование, выходящие за рамки этого типа, как правило, рассчитано на промышленное применение.
Большинство аппаратов с плазмотронами воздушного охлаждения пригодны для резки металлических деталей толщиной до 50 мм. Для резки деталей толщиной свыше 50 мм или для увеличения производительности применяют более сложные и дорогие аппараты с плазмотронами водяного охлаждения
Максимальная глубина реза определяет толщину материала, которая может быть разрезана данным аппаратом в принципе. Скорость работы при этом в расчет не берется. Чтобы комфортно и быстро работать с деталями толщиной 3-4 мм, следует выбирать аппарат, максимально допустимая глубина реза которого — 8-10 мм.
Унифицированные разъемы для плазмотронов производятся в соответствии с европейскими стандартами и состоят из розеток (со стороны источника плазмы) и вилок (со стороны резака). Преимущество подобной системы заключается в возможности при необходимости удлинить или укоротить конструкцию без ощутимой потери мощности, прочности и электрического контакта.
Износ сопла заключается в нарушении его геометрической формы, что негативно влияет на качество реза. Износ же катода приводит к выработке стержня (допустимая глубина выработки — не более 1,5 мм), в результате чего может произойти пригорание катода к головке плазмотрона и его (плазмотрона) перегрев.
При минусовых температурах необходимо соблюдать определенные меры предосторожности. Поскольку в ресивере и шлангах образуется конденсат, который в случае замерзания может вывести из строя оборудование, то после окончания работ шланги обязательно продувают, а сам компрессор хранят в помещении с плюсовой температурой.
как выбрать и 10 лучших моделей, рейтинг 2021
Не все металлы можно резать газо-кислородным пламенем. Если Вам необходимо работать с нержавейкой, медью или алюминием, то понадобится плазморез. Даже при крое черных металлов этот аппарат оставляет меньше капель шлака, а сам рез гораздо тоньше, что сокращает последующую обработку и экономит материалы. Подробное описание устройства оборудования и рейтинг лучших моделей помогут вам разобраться, как выбрать плазморез для разных сфер применения.
Подборка товаров осуществлена на основе отзывов, мнений и оценок пользователей, размещенных на различных ресурсах в сети интернет. Вся информация взята из открытых источников. Мы не сотрудничаем с производителями и торговыми марками и не призываем к покупке тех или иных изделий. Статья носит информационный характер.
Устройство и принцип работы плазмореза
Оборудование для плазменной резки состоит из:
- источника питания;
- горелки;
- кабеля массы;
- компрессора или баллона со жатым воздухом.
Источником питания выступает инвертор, выдающий постоянный ток, который до этого был преобразован несколько раз с повышением частоты. Для подключения необходимо 220 или 380 V, в зависимости от характеристик прибора. На выходе аппарат выдает напряжение до 400 V и силу тока от 25 до 125 А. Горелка в таком оборудовании называется плазмотроном. На ней есть сопло и кнопка для запуска питания. Плазмотрон бывает ручной или автоматического типа на кронштейне с рельсами.
Составные элементы плазмореза.
Устройство плазмотрона.
Принцип работы плазмореза заключается в возбуждении электрической дуги, в которую подается сжатый воздух. От нагрева он переходит в плазму, которой осуществляется резка всех видов металлов и даже керамики. Температура плазмы составляет около 20000 градусов, что превосходит показатель кислородной резки в 6 раз.
Еще плазма обладает высокой скоростью иссечения 1500 м/с, которой нет у газо-кислородного пламени, режущего за счет давления в 10 атм. из баллона. Такие характеристики дуги обеспечивают чистый рез, узкую кромку и минимум шлака на обратной стороне детали.
Для резки плазмотроном в оборудовании осуществляются следующие процессы:
1. Источник тока подает напряжение на катод и анод, расположенные в сопле плазмотрона. Между ними возникает электрическая дуга. Одновременно от компрессора поступает сжатый воздух, пропущенный через фильтр-осушитель. Воздух, проходя через дугу, ионизируется и превращается в плазму. Эта дуга называется дежурной и горит только на плазмотроне.
Работа плазменной горелки.
2. Затем сварщик подносит горелку к заготовке. Благодаря кабелю массы, несущему положительный заряд и подключенному к изделию, дуга замыкается на материале. Дежурная дуга становится режущей. Сварщик управляет горелкой и ведет резку по намеченному контуру. Длину плазмы и ширину можно регулировать силой тока и диаметрами устанавливаемых сопел.
3. Когда резка выполнена, сварщик убирает горелку от изделия и снова горит дежурная дуга. Отпуская кнопку, она гасится и еще какое-то время подается воздух для охлаждения сопла.
Схема работы плазмореза.
Сфера применения, плюсы и минусы плазменной резки
Оборудование для плазменной резки металлов используется на заводах и в частных мастерских. С его помощью ведется крой листового железа с толщиной от 1 до 100 мм (зависит от мощности аппарата). Плазмой можно вырезать сложные узоры, прожигать отверстия, срезать кромку. Последующие заготовки используются для приваривания к другим конструкциям или подвергаются токарной обработке, штамповке. В отличие от кислородного пламени, плазма режет все виды металлов и керамику, поэтому ее функционал и зона применения шире.
Чтобы определиться, нужен ли Вам плазморез, рассмотрите преимущества и недостатки такого оборудования.
К главным плюсам этого метода кроя относятся:
Высокая скорость реза
Благодаря температуре 20000 градусов плазморезом можно кроить заготовки гораздо быстрее, чем другими методами. Например, лист с сечением 25 мм получится резать на скорости 1000 мм/мин.
Быстрый сквозной прожиг
Если требуется начать резку не с края листа, а в центре, то плазма прожжет толщину 15 мм за 2 с, а газопламенному резаку потребуется на это около 30 с.
Минимальный нагрев соседних участков
Плазма точечно воздействует на металл, не нагревая поверхность вокруг. Это снижает количество деформаций и позволяет держаться за крупные заготовки руками в перчатках, поворачивая их по необходимости.
Высокое качество реза
После плазмы почти не остается потекших капель шлака на обратной стороне заготовки. Кромки содержат минимум рельефности, поэтому не нуждаются в обработке — сразу можно производить последующую сварку конструкций. Если требуется порезать тонкие листы 1-2 мм, то их можно сгруппировать друг на друге и выполнить все за один раз — заготовки не прилипнут между собой на краях.
Пример металла разрезанного плазморезом.
Безопасность
В этом оборудовании не используются горючие газы. Применение сжатого воздуха или инертных газов делает процесс более безопасным — взрыва точно не будет, как в случае обратного удара пламени в кислородном резаке.
Простота использования
В отличие от газопламенной резки, здесь не нужно настраивать подачу по-отдельности горючего газа и кислорода, а затем регулировать еще и струю режущего кислорода. Все включается одной кнопкой и доступно для быстрого освоения даже новичку.
Возможность автоматизации
Плазморез легко доукомплектовать кронштейном (портальный или консольный тип), чтобы он автоматически передвигался над изделием. Управление ведется с ЧПУ. В нем оператор задает конфигурацию и скорость кроя, одновременно один человек может следить за процессами на пяти установках.
Минимум подготовки перед процессом
Плазма способна кроить любой металл без предварительной очистки от грязи или ржавчины. При работе нет разбрызгивания металла и воздушных хлопков.
Но у этого метода резки есть и недостатки, которые нужно знать, чтобы грамотно выбрать плазморез и не разочароваться.
Вот самые основные минусы аппаратов и самого метода:
- Лучшее качество реза достигается за счет удержания горелки под углом 90 градусов к поверхности. Резать фаску под косым углом могут только дорогие модели.
- Этим оборудованием сложно нагреть металл, чтобы выполнить гиб или ковку.
- Максимальная толщина реза составляет 100 мм, тогда как газопламенной резкой можно прорезать 200-300 мм.
- Само оборудование стоит дороже. Понадобиться еще компрессор. Цена аргона выше, чем пропана или кислорода.
- Аппараты зависят от электрической сети. Для работы в полевых условиях необходим бензогенератор. Его мощность должна быть достаточно высокой, чтобы покрыть потребности плазмореза и компрессора.
Смотрите на что способен плазморез:
Виды плазморезов
Понимая принцип работы плазмореза и его устройство, рассмотрим разновидности оборудования. Это поможет определиться с деталями выбора под конкретные задачи на производстве.
Плазморезы по типу резки
Плазморезы бывают ручными и автоматическими. Это важно учесть при выборе, чтобы оборудование подходило под предстоящие процессы.
Плазморезы для ручной резки
Применяются для работы с небольшими сечениями 1-10 мм. Это актуально для гаража и небольшой мастерской, где изготавливаются двери, ворота, калитки, мангалы. Им удобно прорезать скважины, вырезы под замки и петли, кроить заготовки под полотна и гнутые короба. Оборудование подороже способно прорезать 10-30 мм.
Это расширяет сферу использования и подходит для вырезания заготовок под последующую механическую обработку на производстве (изготовление фланцев, валов, порезка труб и т. д.). Такие установки мобильны и удобны.
Плазморез для ручной резки.
Плазморез для автоматической резки
Используются с режущими головками, перемещаемыми на кронштейнах портального или консольного типа. Управляются с ЧПУ. Могут одновременно вести резку сразу 2-4 головками. Подходят для кроя деталей, габаритами от 1х1 до 3х30 м. Нуждаются в достаточном месте и сложны при транспортировке.
Станок для плазменной резки.
Плазморезы по типу используемого газа
Для работы плазмореза необходим воздух, чтобы ионизироваться в электрической дуге. Здесь различаются два типа оборудования:
Плазморезы на сжатом воздухе
Бытовой и полупрофессиональный класс. Стоят дешевле, просты в управлении (регулируется только сила тока), универсальны. Совсем маленькие аппараты рассчитаны на крой сечения до 10 мм. Более мощные справятся с 12-25 мм. Главным плюсом является недорогое обслуживание (цена сопел, единоразовая покупка компрессора). В последствии ничего дорогостоящего докупать не придется.
Плазморезы на аргоне, кислороде, азоте или их смесях
Применяются на крупных станках по плазменной резке. Нуждаются в продолжительных настройках, зато способны выполнять рез быстрее, точнее и сложнее. Необходимо регулярно тратиться на закупку баллонов с газом. Такой тип подходит для крупных предприятий с большим объемом выпускаемой продукции.
Станок для плазменной резки на аргоне.
Плазморезы по типу поджига дуги
Еще плазморезы делятся по способу возбуждения электрической дуги:
- Контактные. Этот тип поджига встречается в бытовых инверторах. Соплом плазмотрона необходимо коснуться изделия, к которому подсоединена масса. Простая конструкция горелки реже ломается, но сопло быстрее покрывается окалинами.
- Пневматические. Образуют дугу самостоятельно при подаче газа (без касания об изделие). Это удобно для частого перемещения и выполнения мелких резов. Экономит ресурс сопла и повышает производительность.
- Высокочастотные (HF). Самый комфортный тип поджига, достигаемый за счет осциллятора. Дуга возбуждается высокочастотным импульсом, между катодом и анодом в сопле. При подносе к изделию автоматически переходит в режущую. Тип поджига подходит для точного начала реза, чтобы на заготовке не осталось электрических следов.
Плазморезы по типу охлаждения
Воздушное
Применяется в бытовых и полупрофессиональны моделях. Тепло с горелки удаляется естественным путем в окружающий воздух. Внутри каналы остужаются благодаря подаче кислорода или инертного газа. В самом корпусе расположен вентилятор, обдувающий трансформатор и выпрямляющий блок. При работе потребуются периодические перерывы, чтобы не расплавить сопло.
Плазморез с воздушным охлаждением.
Жидкостное
Используется на промышленных версиях оборудования. В плазмотроне есть каналы, по котором, при помощи водяного насоса, циркулирует дистиллированная вода с этиловым спиртом. Это быстро забирает тепло и позволяет работать аппаратом без перерывов. Подходит для объемных задач или эксплуатации установки в две смены.
Как выбрать плазморез
При выборе плазмореза нужно учесть несколько ключевых характеристик.
Толщина разрезаемого металла
Этот параметр напрямую зависит от силы тока (количества ампер), вырабатываемой инвертором. Если Вам требуется резать черный металл, то на каждый 1 мм толщины понадобиться 4 А мощности. Например, чтобы кроить листовое железо 7 мм, ищите аппарат с силой тока не менее 30 А. Для цветных сплавов расчетное значение 1 мм=1.5 А.
Существует еще понятие чистового реза и максимального. Например, первое значение в характеристиках может быть 12 мм, а второе — 18 мм. Это означает, что при толщине до 12 мм вообще не понадобится последующая механическая обработка. Лучше брать плазморез с запасом по мощности, чтобы он не работал постоянно в полную силу. Это продлит его ресурс.
Вид металла | Сила тока, необходимая для резки заготовки толщиной в 1 мм |
---|---|
Медь, латунь, алюминий, медные сплавы | 6 А |
Нержавеющая сталь, черные металлы | 4 А |
Продолжительность включения
Подразумевает, как долго аппарат сможет работать без перерыва. Зависит от мощности и типа охлаждения. Для гаража и небольшой мастерской подойдут установки с ПВ 40%. Для производства, где часто требуется плазменная резка заготовок, выбирайте ПВ 60-80%.
Необходимая мощность компрессора
Чтобы плазменная резка была качественной, необходима стабильная подача воздуха от компрессора. Его производительность должна быть на 20-30% выше, чем требуется по паспорту инвертора. Покупайте компрессор с фильтром-осушителем и маслоотделителем, чтобы примеси не влияли на качество плазмы.
Длина шлангпакета
У плазмотрона длина кабелей может быть 1.5-8 м. При выборе учитывайте, с какими по габаритам конструкциями Вам придется работать. Чем короче шлангпакет, тем чаще придется переставлять аппарат. Но если он требуется для выреза небольших деталей над столом, то можно сэкономить и купить плазмотрон с коротким кабелем.
Видео. Как выбрать плазморез
Лучшие плазморезы
Изучив характеристики оборудования и советы по выбору, перейдем к рейтингу лучших плазморезов, основанному на отзывах сварщиков. Возможно, здесь Вы найдете подходящий для себя аппарат и отправитесь в магазин за уже конкретным товаром.
Aurora PRO AIRHOLD 42 Mosfet
Возглавил рейтинг аппарат плазменной резки с доступной ценой. Его габариты составляют 40х16х30 см. Он работает от однофазной сети 220 В и потребляет 6.6 кВт. Максимальная сила тока 40 А разрешает резать без последующей зачистки толщину до 12 мм. ПВ на максимуме до 60%. Инвертор подходит для кроя чугуна, легированной и углеродистой стали, меди. Для поджига необходимо коснуться соплом о поверхность детали. Весит оборудование 9 кг, поэтому его не сложно транспортировать.
Плюсы Aurora PRO AIRHOLD 42 Mosfet 16337
- Удобный аппарат с хорошим качеством сборки.
- Доступная цена.
- Сопло долго не изнашивается (только чернеет).
- Понятная панель управления.
- Легко купить расходники.
- Жесткая рукоятка на крышке.
- Железные углы закрыты пластиком.
Минусы Aurora PRO AIRHOLD 42 Mosfet 16337
- Контактный тип поджига.
- Если купить отдельно горелку с осциллятором, то нет штатного разъема для подключения.
- Чувствителен при падении напряжения сети до 190-200 В.
- Свыше толщины 10 мм значительно падает скорость резки.
- Нужен компрессор с производительностью не менее 350 л/мин (иначе хватит на 5 см реза и воздух закончится).
Вывод. Этот плазморез выделяется длинной штатной горелкой с кабельканалом 5 м. Отлично подходит для работы с крупными заготовками на производстве и в гараже. Судя по отзывам сварщиков, аппарат легко зажигает дугу на морозе до -20 градусов. Если Вам часто приходится резать металл на улице, то это оптимальный выбор.
BRIMA CUT-40
Еще один профессиональный плазморез в рейтинге по доступной цене. Имеет максимальную силу тока 40 А, чего хватает для чистого реза 12 мм. Относится к полупрофессиональному классу. Питается от 220 В с потреблением мощности 5 кВт. По паспорту требуется производительность компрессора 170 литров воздуха в минуту. ПВ на максимуме достигает 60%. Чтобы возбудить дугу, потребуется касание по изделию. Хранить и перевозить инвертор не сложно ввиду габаритов 44х16х31 см. В аппарате применяется воздушный тип охлаждения. На корпусе имеются многочисленные отверстия и встроен вентилятор.
Плюсы BRIMA CUT-40
- Небольшая масса 10 кг и жесткая ручка.
- Прочный стальной корпус.
- Понятная панель управления.
- Расходники в наличии.
- В комплекте уже есть три сопла и три электрода.
- Хорошо пробивает отверстия сквозь краску.
- Толщину до 3 мм режет очень быстро.
- На «десятке» почти нет подтеков шлака.
Минусы BRIMA CUT-40
- Нет Евро разъема для замены горелки на модель более высокого класса.
- Контактный розжиг электрической дуги.
- Быстро портится сопло.
- Слив из встроенного осушителя расположен рядом с вентилятором охлаждения (в него попадают брызги).
Вывод. Этот плазморез обладает очень компактным плазмотроном. Если Вам нужно демонтировать металлические конструкции и подлазить в узкие места для среза стоек, полок или других элементов, то эта горелка подойдет. Головка оснащена коротким керамическим соплом с наклоном 100 градусов. Держать резак удобно.
Ресанта ИПР 40
Далее в рейтинге товар от латвийского бренда, собираемый в Китае. Плазморез инверторного типа выполнен в стальном корпусе и снабжен воздушным охлаждением. На переднюю сторону вынесен манометр, благодаря чему сварщику не требуется смотреть за показателями на компрессоре. На плазмотроне есть мягкий зажим, облегчающий удержание кнопки пуска в нажатом состоянии при долгих резах. Прибор питается от однофазной сети и выдает до 40 А. ПВ при этом разрешено 35%. Потребуется давление 5000 бар для качественного кроя. Толщина чистого реза составляет 12 мм.
Плюсы Ресанта ИПР 40
- Петли для намотки шлангпакета.
Рельефности на ручке плазмотрона, облегчающие удержание и манипуляции.
Плавная регулировка тока от 15 до 40 А.
Встроенный манометр для контроля давления в системе — не нужно смотреть на компрессор.
При толщине стали до 5 мм, режет очень уверенно.
В любом сервисном центре есть к нему запчасти.
Минусы Ресанта ИПР 40
- Сравнительно высокая стоимость.
Отсутствует Евро разъем.
Качество реза хуже при падении напряжения в сети.
Нужен мощный компрессор.
Иногда плохо фиксируется зажим массы на изделии.
Вывод. Этот плазморез отличается функцией включения/выключения дуги с интервалом 5 секунд. Такой режим пригодится для быстрой резки сетки. Сварщику не нужно часто нажимать на кнопку, что экономит ее ресурс. Скорость резки подобных материалов прерывистой дугой значительно выше, чем если бы приходилось поджигать ее каждый раз, попадая по тонким прутикам сетки.
BlueWeld Prestige Plasma 54 Kompressor
Продолжает рейтинг товар от итальянского бренда. Плазморез имеет диапазон силы тока 7-40 А и способен чисто резать сечение металла до 10 мм. Он потребляет 4.5 кВт, но сварщики в отзывах делятся, что аппарат сможет функционировать даже от генератора с производительностью 3 кВт. Весит источник питания 16 кг. Длина кабеля плазмотрона — 4м. Работает агрегат не очень шумно и легко транспортируется. На приборной панели есть индикация массы, сети и перегрева.
Плюсы BlueWeld Prestige Plasma 54 Kompressor 815725
- Эргономичная ручка горелки.
- Есть прорези для присоединения плечевого ремня — можно резать на высоте.
- Органы управления защищены от случайного изменения настроек.
- Фиксатор кнопки пуска в зажатом положении.
- Можно опускать силу тока до 7 А, чтобы резать аккуратно жесть 0.6-0.8 мм толщиной.
- Длина кабель-пакета 4 м.
- Бесщеточный двигатель компрессора прослужит долго.
Минусы BlueWeld Prestige Plasma 54 Kompressor 815725
- Сопло горелки длиннее, чем у других моделей.
- Отсутствует жесткая рукоятка.
- Высокая стоимость.
- Нет EURO разъема.
- ПВ 30% — после прорезания 1.5 м, приходится давать остывать до 20 минут.
- Более крупные размеры 51х17х34 см.
Вывод. Особенность этого плазмореза видна уже из названия. В него встроен компрессор, рассчитанный специально под дугу. Купив его, Вы получаете все необходимое в одном корпусе для плазменной резки. Это упрощает транспортировку и пригодится при мобильном образе работы (выездные бригады по монтажу/демонтажу на месте, строительство металлоконструкций). С ним даже получится отрезать что-то на высоте, ведь за собой не нужно тащить отдельно компрессор или длинный шланг.
Сварог REAL CUT 45 L207
Завершает рейтинг модель от производителя «Сварог». Это качественный аппарат для плазменной резки с мощностью 4.3 кВт, выдающий 20-45 А. Для оптимальной работы достаточно компрессора, вырабатывающего 100 л воздуха в минуту. В инверторе используется давление 4 бар для ионизации дуги. Максимальное сечение металла для чистого реза допустимо 12 мм, но сварщики в отзывах делятся, что им получится прорезать и 15 мм. Товар укомплектован плазмотроном с рукавом 5 м и кабелем массы 3 м.
Плюсы Сварог REAL CUT 45 L207 93557
- Может подключаться к небольшому бензогенератору ввиду потребления 4.3 кВт.
- Высокие ножки содействуют устойчивости аппарат и проходу воздуха снизу для лучшего охлаждения.
- Углы корпуса защищены резиновыми накладками.
- Есть встроенный манометр для слежения за давлением.
- Четкая и ровная линия реза.
- Высокочастотный поджиг для легкости начала реза.
- Редко уходит в защиту.
Минусы Сварог REAL CUT 45 L207 93557
- Нет прорезей для плечевого ремня.
- Сначала могут быть проблемы с розжигом.
- Без трафарета страдает ровность линии.
- Хлипкий диффузор на плазмотроне.
Вывод. У этого плазмореза есть две особенности: малый вес по отношению к мощности. Масса аппарата составляет 8 кг, что пригодится при частой перевозке с объекта на объект. Есть и более легкие модели, но здесь максимальная сила тока 45 А, чем могут похвастаться далеко не все компактные плазморезы. Это лучший аппарат для стройки.
Если вы заметили ошибку, не рабочее видео или ссылку, пожалуйста, выделите фрагмент текста и нажмите Ctrl+Enter.
как выбрать плазменный резак, какое оборудование лучше и рейтинг моделей
Для разрезания листового металла удобно использовать плазморез. Качество получаемого реза значительно выше, чем при работе болгаркой. На поверхности отсутствуют заусенцы, и это место не требует финишной доводки. Раскаленная плазма, которая подается из прибора, воздействует только на место реза, не затрагивая остальную часть заготовки. Работа не связана с приложением усилий.
Виды и назначение плазморезов
Прежде чем понять, как выбрать плазморез, необходимо изучить существующие виды приборов. В зависимости от области применения они подразделяются:
- Инверторные. Обладают способностью резать металл толщиной 30 мм.
- Трансформаторные. Разрезают металл толщиной 80 мм.
Существует классификация в зависимости от контакта резака с деталью.
Они подразделяются:
- Контактные. При работе необходим контакт плазмы с металлом. Толщина его может быть до 18 мм.
- Бесконтактные. В этом случае металл может быть большой толщины и контакта с ним не требуется.
В зависимости от потребляемой энергии также есть свои разновидности. Это приборы:
- Бытовые. Работают от сети 220 Вт.
- Плазморез промышленный. Работает от трехфазной сети 380 Вт.
Принцип работы устройства
Выбор плазмореза нужно начинать с изучения его устройства. Электрическая дуга нагревает ионизированный воздух до температуры 30000 градусов. Через него проходит электрический ток. Он направляется на металл. В области среза происходит его выдувание. Состоит прибор из следующих элементов:
- Плазмотрон. Это плазменный резак, который с помощью кабеля и шланга подключен к аппарату. При разрезании металла дуга возникает между заготовкой и резаком. Такие плазматроны называются прямого действия. Если разрезается неметаллическая поверхность, то дуга образуется непосредственно в резаке. Это плазматроны косвенного действия.
- Сопло. Это элемент, через который проходит воздух. В зависимости от его размера изменяется величина реза и скорость проведения работы. Наименьшие диаметры сопла составляют 3 мм, а максимальные 9−12 мм. Длина сопла выбирается в 1,5—1,8 раза больше диаметра. Чем оно длиннее, тем выше скорость. Но если эта величина слишком большая, то сопло быстро разрушается.
- Электрод. Это металлический стержень из гафния, расположенный внутри плазматрона.
Другое его название — катод.
В процессе резки используется воздух. Однако в некоторых случаях идет добавление кислорода, гелия или водорода. Связано это с тем, что поверхность материала может окисляться, а эти газы выступают в качестве защитных сред.
Преимущества и недостатки агрегатов
Чтобы понять, какой плазморез лучше, нужно знать преимущества и недостатки приборов. К преимуществам относятся:
- кроме обычного металла, можно резать алюминий, нержавейку или чугун;
- не требуется подготовки поверхности. Допускается присутствие ржавчины и краски;
- срез получается ровный без окалины;
- даже при небольшой толщине заготовки отсутствует тепловая деформация поверхности;
- безопасность в эксплуатации;
- возможность формирования сложных резов.
Однако при всех достоинствах у плазмореза есть и недостатки. К ним относятся:
- ограничение по толщине реза. Максимальная величина составляет 100 мм;
- заготовка должна располагаться четко перпендикулярно резу;
- нельзя работать двумя резаками, подключенными к одному аппарату.
Факторы, влияющие на выбор
При выборе плазмореза нужно учитывать некоторые факторы. К ним относятся:
- Сила тока. В зависимости от этой величины увеличивается мощность дуги и быстрее расплавляется металл. Если предстоит работа с алюминием, медью или ее сплавами, то сила токам выбирается 6А. Для нержавейки и черных металлов — 4А.
- Продолжительность включения. Некоторые аппараты могут работать 50% времени, а потом столько же должны отдыхать. Этого достаточно, чтобы нарезать определенное количество заготовок. Для промышленных целей выбирается прибор с 100% временем работы.
- Встроенный или внешний компрессор. Если компрессор встроенный, то такие приборы не обладают большой мощностью и относятся к бытовым устройствам.
При наличии внешнего компрессора имеется возможность работать непрерывно. Давление в плазморезе не должно быть выше выдаваемого компрессором.
- Частота замены сопла и электрода. Это зависит от длительности работы и толщины разрезаемого материала. При работе с металлом толщиной 10 мм некоторые расходники выдерживают 150 резов, другие 500−600, а промышленные работают всю смену.
- Длина кабеля и шланга не должна превышать 20 м иначе создадутся неудобства при их раскручивании.
Рейтинговые аппараты для резки
При выборе прибора нужно ориентироваться на рейтинг плазморезов. К наилучшим моделям относятся:
- Сварог CUT 40B (R34). Обладает мощностью 3,84 кВт. Работает от напряжения 220 Вт. Размеры составляют 425 x 205 x 355 мм. Аппарат рассчитан на работу с тонким листовым металлом; легкий и удобный в управлении.
- AURORA PRO AIRFORCE 60 IGBT. Подключается к напряжению 380 Вт. Максимальная толщина режущей поверхности 20 мм. Можно работать с любыми марками материала, проводящими ток. Режущая сила тока составляет 60 А.
- BRIMA CUT 120. Работает от напряжения 380 Вт. Имеет возможность разрезать листы толщиной 35 мм. Мощность аппарата составляет 20 кВт. Размеры: 475 x 330 x 370 мм.
- КЕДР CUT-40B. Потребляемое напряжение — 220 Вт. Разрезает листы металла толщиной 12 мм.
- Lincoln Electric Tomahawk 1538. Питается напряжением 380 Вт. Имеет угольный электрод. Ток резки составляет 30−100 А. Размеры — 455 x 301 x 640 мм.
При выборе плазмореза нужно ориентироваться на его параметры. В домашних условиях нет смысла приобретать промышленный аппарат, вполне достаточно бытового. Устройство будет работать 50% времени и столько же отдыхать. За этот период можно провести значительную часть работы.
Также плазменный резак можно собрать самостоятельно, как – читайте здесь.
Резка металла с помощью плазмореза — Плазменная резка
Плазменная резка получила широкое распространение в различных отраслях производства, ведь с ее помощью можно разрезать практически любые токопроводящие металлы: от алюминия и нержавейки до углеродистой стали и титана. Этот метод используют как на крупных предприятиях, так и в небольших частных мастерских. Овладев основными приемами плазменной резки, Вы сможете легко выполнять прямые и фигурные резы, делать проемы и отверстия в металлических заготовках, выравнивать кромки листов и выполнять более сложные работы. Впервые работая с плазморезом, хочется, чтобы результат оправдал ожидания. Но, к сожалению, не у всех начинающих резчиков это получается. Для примера приведем наиболее распространенный случай из практики. Пользователь работает с купленным недавно плазморезом. Но почему-то возникают проблемы: то дуга нестабильная, то пламя гаснет, то аппарат вовсе отключается. Возникает подозрение – некачественный ток в центральной электросети. Пока время уходит на поиск и устранение неполадок, работа стоит. А на самом деле причина может быть в другом. Сколько раз случалось, когда пользователи во всем винили центральную проводку, а на деле оказывалось, что было неправильно выставлено давление воздуха или сила тока. Чтобы такого не случилось, при работе с плазморезом нужно учесть множество нюансов.
Освоить азы технологии плазменной резки не так сложно, главное – детально во всем разобраться. Мы расскажем обо всем по порядку. А начать нужно с вопроса безопасности проведения работ. Ведь от соблюдения правил зависит Ваше здоровье.
Что нужно знать о безопасности?
Сначала перечислим факторы, которые представляют опасность при работе с аппаратом плазменной резки: электрический ток, высокая температура, ультрафиолетовое излучение, раскаленный металл. Чтобы защитить себя, нужно работать в специальной экипировке. Глаза должны быть защищены очками или щитком сварщика (стекла 4 или 5 класса затемнения), руки – перчатками, ноги – штанами из плотной ткани и закрытой обувью. Стоит отметить, что при работе с резаком образуется газ с примесями озона, водорода и частиц металла. Наиболее опасными являются окислы марганца, соединения кремния и хрома, окись титана, которые представляют угрозу не только для легких, но и для других внутренних органов. Чтобы не вдыхать эти вредные пары, нужно обеспечить в помещении хорошую вентиляцию, а на лицо надевать защитную маску.
Что касается электробезопасности, то нужно соблюдать несколько обязательных требований:
- Плазменная резка должна подключаться в сеть с предохранителем или автоматическим выключателем.
- Параметры тока в электросети должны соответствовать характеристикам устройства.
- Обязательно убедитесь в том, что обеспечено хорошее заземление розеток, а также рабочей подставки аппарата и находящихся поблизости металлических предметов.
- Проверьте электрические и силовые кабели на предмет повреждений. Не используйте их, если изоляция повреждена.
Ответственный подход и соблюдение мер безопасности помогут Вам избежать травм, а также снизить риск получения профессиональных заболеваний.
Как подготовить аппарат к работе?
Подробный алгоритм подключения плазмореза к электросети и источнику сжатого воздуха Вы найдете в инструкции, поэтому мы не будем заострять внимание на этом этапе. Лучше обозначим наиболее важные аспекты, которые напрямую влияют на качество выполнения работ.
Аспект 1. Установите аппарат таким образом, чтобы к его корпусу был обеспечен доступ воздуха для охлаждения. Это позволит трудиться продолжительное время и избежать отключений оборудования в связи с перегревом. При этом на него не должны попадать капли расплавленного металла и какие-либо жидкости.
Аспект 2. Позаботьтесь о подаче качественного воздуха от пневмосети или компрессора. Установите влагомаслоотделитель, чтобы частицы масла и воды не попали в резак. В противном случае увеличится износ расходных материалов, а также может прийти в негодность сам плазмотрон. Убедитесь, что давление подаваемого воздуха соответствует параметрам аппарата плазменной резки. При недостаточном давлении дуга будет нестабильна (появятся наплывы и шлак в месте реза), а при избыточном могут прийти в негодность важные рабочие элементы.
Аспект 3. Тщательно подготовьте заготовку перед тем, как ее резать. Если на поверхности есть краска или ржавчина, нужно ее счистить, чтобы при нагреве металла не выделялись ядовитые пары. Кроме того, не рекомендуется резать без предварительной очистки резервуары и емкости, в которых были горючие вещества.
Помните, что правильно проведенные подготовительные работы являются гарантией эффективности использования плазменной резки. Теперь перейдем к рассмотрению самого процесса резки металла.
Как правильно подобрать силу тока?
Чтобы получить ровный и аккуратный рез, без окалины, наплывов и шлака, нужно грамотно выставить на аппарате силу тока, необходимую для разрезания конкретной заготовки. Для этого нужно знать, какая сила тока приходится на расплавление 1 мм материала. Для разных видов металла будет свое значение:
- При работе с чугуном и сталью – 4 А.
- При работе с цветными металлами и их сплавами – 6 А.
К примеру, для обработки стального листа толщиной 20 мм на аппарате нужно выставить силу тока не менее 80 А, а для работы с алюминиевым листом такой же толщины – 120 А. Но это еще не все, что нужно учесть при работе. Чтобы металл успел расплавиться в месте реза, но при этом не деформировался при тепловом воздействии плазмы, важно подобрать оптимальную скорость ведения резака. Она может быть от 0,2 до 2 м/мин. в зависимости от выставленной силы тока, толщины заготовки и вида металла, Конечно, первое время новичку будет сложно измерить скорость и подобрать наиболее подходящую, это придет с опытом. А на первое время запомните простое правило: ведите горелку так, чтобы искры были видны с обратной стороны разрезаемой заготовки. Если их не видно – металл разрезан не насквозь, скорость большая. Но слишком медленное ведение резака, особенно при высокой силе тока, может стать причиной образования окалины, угасания дуги и ухудшению качества реза.
Как разжигать плазменную дугу?
Прежде чем приступать к резке, нужно сделать продувку резака газом. Для этого нажмите и отпустите кнопку поджига на резаке, плазмотрон перейдет в режим продувки. Выждите не меньше 30 секунд, прежде чем зажигать дугу, за это время из резака должен удалиться конденсат и инородные частицы. После этого можно нажимать на кнопку розжига – появится дежурная или, как ее называют, пилотная дуга. Как правило, пилотная дуга горит не более 2 секунд. Поэтому за это время должна зажечься рабочая дуга. У разных моделей плазморезов это происходит по-разному, в зависимости от типа поджига. Различают:
- Контактный – для получения рабочей дуги необходимо короткое замыкание, которое возникает следующим образом: после того, как зажглась дежурная дуга, при нажатии на кнопку блокируется подача воздуха – контакт замыкается. После автоматического открытия воздушного клапана контакт размыкается, а поток воздуха выводит искру из сопла. Между электродом с отрицательной полярностью и металлом с положительной полярностью возникает плазменная дуга. Помните, что контактный поджиг не значит, что нужно прислонять сопло к металлу.
- Бесконтактный – такой тип розжига используется в аппаратах, сила тока которых превышает 50 А (его еще называют осциллятором или высокочастотным зажиганием). Дежурная дуга имеет высокую частоту тока и высокое напряжение, она возникает между электродом и соплом. При приближении сопла к поверхности разрезаемой заготовки образуется рабочая дуга.
После зажигания рабочей дуги, пилотная гаснет. Если Вам не удалось с первого раза получить рабочую дугу, то нужно отпустить кнопку на резаке и вновь нажать ее – это будет новый цикл. Дуга может не разжигаться из-за недостаточного давления воздуха в пневмосистеме, неправильной сборки плазмотрона или неполадок в работе электроэлементов. Выключите аппарат, проверьте правильность подключения и давление на входе. Еще раз попробуйте осуществить розжиг.
Также стоит помнить, что в процессе резки рабочая дуга может гаснуть. Это может случиться по причине износа электрода, но чаще всего проблемы возникают при несоблюдении расстояния между резаком и деталью. Естественно, это сказывается на скорости выполнения работ и на качестве реза.
Как поддерживать расстояние между горелкой и металлом?
Бывают аппараты плазменной резки, которые рассчитаны на разрезание металла с упором на сопло, то есть, вплотную к заготовке – соблюдать расстояние не нужно. Но большинство моделей оборудования для этого не предназначено – сопло будет быстро изнашиваться, резак будет отключаться. Для них оптимальным расстоянием между заготовкой и соплом будет 1,6-3 мм. Если превысить его, то дуга будет затухать, придется поджигать ее снова – аккуратного реза не получится. Особенно важно поддерживать одинаковое расстояние при выполнении кропотливых работ, например, фигурной резки. Чтобы удерживать зазор, многие пользователи устанавливают на резак специальную дистанционную направляющую. и опираются ею на заготовку, а не соплом.
Не забывайте, что держать резак нужно таким образом, чтобы сопло было перпендикулярно заготовке. Угол отклонения не должен превышать 10-50 градусов, иначе рез будет неаккуратным. Если Вы режете металлическую заготовку, толщина которой не превышает 25% от максимально допустимой производителем, держите горелку не перпендикулярно поверхности, а под небольшим углом. Так Вы сможете избежать сильной деформации тонкого металла. При этом следите, чтобы расплавленный металл не попадал на сопло резака.
Помните, что сопло и электрод являются оснасткой, которая подвержена наибольшему износу при выполнении работ. Своевременно заменяйте эти элементы, согласно требованиям инструкции. Тогда во время плазменной резки будет обеспечена стабильная дуга, не будет наплывов и шлака на обрабатываемой поверхности – рез будет аккуратным и ровным.
купить плазморез горыныч
как выбрать плазморез
ручной аппарат для плазменной резки
ручная плазменная резка
плазморез из инвертора своими руками подробно
Рекомендации. Типичные ошибки оператора МТР при плазменной резке и способы их избежания
Использование расходных материалов до тех пор, пока они не выйдут из строя
Если посмотреть на ряд деталей одного типа, которые были вырезаны при таком подходе, можно безошибочно определить те детали, на которых сопло или электрод были уже «на подходе». Использование сильно изношенных сопел и электродов может не только привести к браку при вырезке детали, но и стать причиной дорогостоящего ремонта пламенного резака и даже аппарата плазменной резки, во время которого машина плазменной резки будет простаивать. Выход из строя сопел и электродов можно легко предупредить по нескольким признакам, которые выдают изношенные расходники. Опытный оператор по звуку резки и цвету пламени дуги (при выгорании циркониевой вставки оно приобретает зеленоватый оттенок), а также по необходимости уменьшать высоту плазмотрона при пробивке, всегда скажет Вам, когда пора менять электрод. Также, одним из лучших способов оценки состояния деталей резака является качество реза. Если качество реза внезапно начинает ухудшаться, то это повод проверить состояние сопла и электрода. Разумным подходом является ведение журнала со средним временем работы электрода или сопла от замены до замены. Сопло и электрод могут выдерживать разное количество пробивок в зависимости от тока резки, типа и толщины материала. Например, при резке нержавеющей стали требуется более частая замена расходников.
Однажды определив по такому журналу среднее время жизни электрода для каждого конкретного вида вырезаемых деталей, можно выполнять плановую замену сопел и электродов, не доводя до появления брака в вырезаемых деталях или до поломки пламенного резака.
Слишком частая замена сопел и электродов
Среди использованных сопел и электродов достаточно часто можно встретить такие, которые еще можно использовать при резке. Излишне частая замена расходников также очень распространена среди операторов металлорежущих станков с ЧПУ, и в особенности, машин плазменной резки. При замене сопла или электрода оператор должен четко знать, на что обращать внимание. Сопло требует замены в следующих ситуациях:
1. Если сопло имеет деформации снаружи или изнутри. Это часто бывает при слишком маленькой высоте пробивки и при непрорезе металла. Расплавленный металл попадает на внешнюю поверхность сопла или защитного колпака и деформирует ее.
2. Если выходное отверстие сопла по форме отличается от окружности. При большой высоте пробивки, если движение начинается до прореза металла, то дуга отклоняется от перпендикуляра к листу и проходит через край отверстия сопла. Чтобы определить, изношен ли электрод, нужно посмотреть на вставку из металла серебристого цвета на торце медного электрода (как правило, используется сплав циркония, гафния или вольфрама). В общем случае, электрод считается работоспособным, если этот металл вообще есть и глубина лунки на его месте не превышает 2 мм для воздушно-плазменной или кислородно-плазменной резки. Для резки плазмой в среде защитного газа (азота или аргона) глубина лунки может достигать 2,2 мм. Завихритель нуждается в замене лишь в том случае, если при тщательном осмотре можно выявить забитые отверстия, трещины, следы вызванные попаданием дуги, или сильный износ. Завихрители особенно часто заменяются преждевременно. То же самое касается и защитных колпаков которые нуждаются в замене только в случае физического повреждения. Очень часто защитные колпачки могут быть очищены наждачной бумагой и использованы вновь.
Использование неправильных настроек параметров плазменной резки и расходных материалов
Выбор расходников при плазменной резке зависит от вида разрезаемого металла (сталь, медь, латунь, нержавейка и т.д.), от его толщины, выставленного тока дуги на аппарате плазменной резки, плазмообразующего и защитного газов и т.д. Справочное руководство оператора машины плазменной резки описывает, какие расходные материалы использовать в случае разных режимов процесса резки. Указанные в инструкции оператора режимы, рекомендации относительно настроек плазменной резки следует соблюдать. Использование расходных материалов (сопел, электродов) несоответствующих текущему режиму плазменной резки обычно приводит к ускоренному выходу расходников из строя и к значительному ухудшению качества пламенного реза. Очень важно выполнять плазменную резку металла именно с тем током дуги, на который рассчитаны используемые расходные материалы. Например, не стоит резать металл плазмой на 100 амперах, если в плазменном резаке стоит сопло на 40 ампер, и т.д. Самое высокое качество реза достигается, когда ток на аппарате плазменной резки выставлен на 95% от номинального тока резки, на который рассчитано сопло. Если установлен режим плазменной резки с заниженным током дуги, то рез будет зашлакованный, и на обратной стороне вырезаемых деталей будет значительное количество грата, пламенный рез будет неудовлетворительного качества. Если установленный на установке плазменной резки ток слишком высок, то срок службы сопла значительно сокращается.
Неправильная сборка плазменного резака
Пламенный резак должен быть собран таким образом, чтобы все его детали плотно прилегали друг к другу, и не было бы впечатления «разболтанности». Плотность прилегания деталей плазмотрона обеспечивает хороший электрический контакт и нормальную циркуляцию воздуха и охлаждающей жидкости через плазменный резак. Во время замены расходных материалов нужно стараться разбирать плазменный резак на чистой поверхности, чтобы грязь и металлическая пыль, образующиеся при плазменной резке, не загрязнили плазмотрон. Чистота при сборке/разборке плазменного резака очень важна и, тем не менее, это требование часто не соблюдается.
Невыполнение регулярного планового обслуживания плазмотрона
Плазменный резак может работать в течение многих месяцев, и даже лет без должного обслуживания. И, тем не менее, газовые каналы и каналы охлаждающей жидкости внутри плазменного резака должны содержаться в чистоте, посадочные места сопел и электродов должны проверяться на предмет загрязнения или повреждений. Грязь, металлическая пыль должны удаляться из плазменного резака. Для чистки плазмотрона следует использовать чистую хлопчатобумажную тряпочку и жидкость для чистки электрических контактов либо перекись водорода.
Резка металла без проверки давления плазмообразующего газа или подачи охлаждающей жидкости в плазморез
Расход и давление плазмообразующего газа и охлаждающей жидкости нужно проверять ежедневно. Если расход недостаточный, детали резака не будут в должной степени охлаждаться и их срок службы будет снижен. Недостаточный проток охлаждающей жидкости из-за изношенного насоса, забитых фильтров, недостаточного количества охлаждающей жидкости, является распространенной причиной поломок плазменных резаков. Постоянное давление плазмообразующего газа очень важно для поддержания режущей дуги и для качественного реза. Избыточное давление плазмообразующего газа является распространенной причиной затрудненного поджига плазменной дуги, притом, что все остальные требования к настройкам, параметрам и процессу плазменной резки полностью удовлетворены. Слишком высокое давление плазмообразующего газа является причиной быстрого выхода из строя электродов. Плазмообразующий газ обязательно должен быть очищен от примесей, т.к. его чистота оказывает сильное влияние на срок службы расходных материалов и плазмотрона в целом. Компрессоры, подающие воздух в аппараты плазменной резки имеют тенденцию к загрязнению воздуха маслами, влагой и мелкими частицами пыли.
Пробивка при малой высоте плазмотрона над металлом
Расстояние между заготовкой и срезом сопла плазмотрона оказывает огромное влияние, как на качество реза, так и на срок службы расходных материалов. Даже небольшие изменения в высоте плазменного резака над металлом могут значительно повлиять на скосы на кромках вырезаемых деталей. Высота плазменного резака над металлом во время пробивки особенно важна. Распространенной ошибкой является пробивка при недостаточной высоте плазмотрона над металлом. Это приводит к тому, что расплавленный металл выплескивается из лунки, образованной при пробивке и попадает на сопла и защитные колпачки, разрушая эти детали. Тем самым существенно ухудшается качество реза. Если пробивка происходит, когда плазменный резак касается металла, то может произойти «втягивание» дуги. Если дуга «втягивается» в плазмотрон, то электрод, сопло, завихритель, а иногда, и резак целиком — разрушаются. Рекомендуемая высота пробивки равна 1.5-2 величины толщины разрезаемого плазмой металла. Следует отметить, что при пробивке достаточно толстого металла рекомендуемая высота получается слишком большой, дежурная дуга не достает до поверхности листа металла, следовательно, процесс резки на рекомендуемой высоте начать невозможно. Однако если пробивка будет производиться на высоте, на которой плазморез может зажечь дугу, то брызги расплавленного металла могут попасть на плазмотрон. Решением этой проблемы может быть применение технологического приема под названием «подпрыжка». При отработке команды на включение резки, плазменная резка включается на небольшой высоте, затем резак поднимается вверх на заданную высоту подпрыжки, на которой брызги металла не достают до резака. После отработки пробивки резак опускается на высоту врезки и начинается движение по контуру.
Плазменная резка металла на слишком большой либо слишком малой скорости
Несоответствие скорости плазменной резки выбранному режиму существенно сказывается на качестве реза. Если установленная скорость резки слишком низкая, на вырезаемых деталях будет большое количество облоя и разнообразных наплывов металла по всей длине реза на нижней части кромки деталей. Низкие скорости резки могут стать причиной увеличения ширины реза и большого количества брызг металла на верхней поверхности деталей. Если установлена слишком высокая скорость резки, дуга будет загибаться назад, вызывая деформацию кромок вырезаемой детали, будет узкий рез, и небольшие бусинки грата и облоя в нижней части кромки реза. Грат образованный при высокой скорости резки тяжело удаляется. При правильно выбранной скорости резки количество грата, облоя и наплывов металла будет минимальным. Поверхность кромки пламенного реза при правильно выбранной скорости должна быть чистой и механическая обработка должна быть минимальной. В начале и конце реза может произойти «отклонение» дуги от перпендикуляра. Это происходит из-за того, что дуга не успевает за резаком. Отклонение дуги приводит к тому, что она врезается в боковую поверхность сопла, нарушая тем самым его геометрию. Если выполняется врезка с кромки, центр отверстия сопла должен находиться точно на линии кромки детали. Это особенно важно в комбинированных станках, в которых применяется и дыропробивная головка и плазморез. Отклонение дуги может произойти и когда плазмотрон при включенной резке проходит через край листа, или если линия выхода из контура с резкой (lead out) пересекает старый рез. Необходима точная настройка параметров времени, чтобы уменьшить проявления этого эффекта.
Механическое повреждение или поломка плазменного резака
Столкновения резака с листом, вырезанными деталями или ребрами раскроечного стола могут полностью вывести резак из строя. Столкновений резака с вырезаемыми деталями можно избежать, если в управляющей программе задавать холостые проходы вокруг, а не над вырезанными деталями. Например, в программе оптимального раскроя ProNest производства MTC-Software присутствует такая возможность, что позволяет свести риск поломки плазмотрона к минимуму и сэкономить значительные средства. Стабилизаторы высоты резака также обеспечивают некоторую защиту от столкновений с металлом. Однако, если используется только лишь датчик высоты резака по напряжению дуги, то в конце реза могут происходить «клевки», т.к. напряжение дуги меняется в результате ее «отклонения» и резак опускается вниз чтобы его компенсировать. В системах ЧПУ применяется многоуровневая система защиты от столкновения с металлом. Используется как датчик касания, измеряющий сопротивление между антенной вокруг резака и листом, емкостной датчик и датчик напряжения дуги. Это позволяет в полной мере использовать преимущества каждого из типов датчиков. Также, для защиты резака можно применять «ломкие» кронштейны, которые при столкновении сломаются быстрее, чем плазменный резак. Таким образом, грамотный оператор машины плазменной резки может сэкономить своему предприятию огромные деньги, время и накладные расходы на плазменную резку. Результатом работы хорошего оператора МТР будет возросшая рентабельность плазменной резки и увеличение прибыли предприятия в целом.
Надеемся, что изложенные в этой статье рекомендации по плазменной резке металла позволят выполнить настройку плазменной резки и подобрать режимы реза для каждого конкретного случая.
лучших плазменных резаков до 1000 долларов США
Сварка — важный навык, но чтобы стать отличным производителем, вам понадобится плазменный резак.
Плазменные резаки— это экономичный способ пополнить свой арсенал удивительными навыками.
Они не занимают много места и не требуют много тепла, затрат на техническое обслуживание или уборку.
Их также легко освоить и быстро запустить в производство.
Мы исследовали рынок, чтобы предложить вам эти плазменные резаки стоимостью менее 1000 долларов США
Быстрое сравнение
Товар | |||
---|---|---|---|
Изображение | Товар | Подробности | |
Иствуд Versa-Cut 60 | Режет пластину 7/8 дюйма 20-футовый фонарь Trafimet Высокочастотная дуга начинается | ||
Сварочный аппарат Yeswelder CUT-55DS | Доступная мощность Пилотный фонарь ВЧ Гарантия 1 год | ||
Hobart Airforce 12ci | Легкий Запуск дуги без касания Работает от 120 В | ||
PrimeWeld CUT60 | с ЧПУ Горелка с обратным затвором Фиксатор спускового крючка для длинных резов | ||
Forney 250P Plus | Работает на мощности 120 Бортовой компрессор Простые настройки | ||
PowerPlasma 52i | готово к ЧПУ Таймер постпотока 120 или 240 вольт |
Лучшие плазменные резаки до 1000 долларов с отзывами
Вот список лучших плазменных резаков, которые вы можете купить менее чем за 1000 долларов:
1.

- Выходная мощность 20-60 ампер
- Лист 28 калибра на сталь 7/8 дюйма
- 60-процентный рабочий цикл при 60 ампер
- 20-футовый разъем резака
- Горелка Trafimet CB70
Плюсы
- Стандартные расходные материалы, легко найти
- Гарантия 3 года
- Весит всего 45 фунтов
- Внутренний воздухо-водоотделитель
- 30-дневная гарантия возврата денег
Минусы
- Не подходит для плазменных столов с ЧПУ
- Цепь на 50 А — высокий уровень для магазинов DIY
Обзор
Плазменный резак Eastwood Versa-Cut на 60 ампер — это доступный и мощный аппарат. Выходная мощность от 20 до 60 ампер позволяет резать металл толщиной от 1/64 дюйма (24 калибра) до стального листа толщиной 7/8 дюйма. Эта машина работает от 240 вольт и требует автоматического выключателя на 50 ампер, что выше, чем обычные 20-30 ампер в большинстве домашних мастерских. Eastwood также предлагает плазменный резак Versa-Cut 40 с двойным напряжением, если вы предпочитаете выбирать между 120 и 240 мощностями.
Одной из замечательных особенностей плазменного резака Eastwood Versa-Cut 60 Amp является 20-футовое соединение резака, позволяющее легко добраться до вашей работы и перемещать более крупные детали, такие как проекты автомобилей и ремонт оборудования.Более того, Иствуд включил выдающийся резак
Trafimet CB70.
Плазменный резак Eastwood Versa-Cut 60 А оснащен внутренним водоотделителем. Хотя высокочастотный запуск дуги очень удобен при работе вручную, он будет мешать работе цифровой электроники, такой как сотовые телефоны и компьютеры. Это делает Versa-Cut 60 непригодным для использования на столе плазменной резки с ЧПУ. На Versa-Cut 60 предоставляется трехлетняя гарантия Eastwood «без проблем» и 30-дневная гарантия возврата денег.
2. Плазменный резак Yeswelder CUT-55DS
- Двойное входное напряжение 120/240
- Может резать пластину 1/2 дюйма
- Горелка высокочастотная
- Включает резак AG60
- Пусковой механизм с блокировкой 2T / 4T
Плюсы
- Соединение резака 13 футов
- Время продувки 20 секунд
- Алюминиевая ручка
- Включает воздушный фильтр.
- Поставляется с запасными расходными материалами
Минусы
- Внешний воздух, необходимый для тяжелых резов
- Не совместим со столом с ЧПУ
Обзор
Плазменный резак YesWelder CUT-55DS использует резак Longevity AG60 для надежной и точной резки.Некоторые владельцы считали, что воздушный поток ограничен дешевым шлангом подачи воздуха, возможно, из-за дешевого воздушного шланга. YesWelder имеет откидной экран, закрывающий панель управления. Мощность резки в 55 ампер является хорошей серединой между машинами на 50 и 60 ампер, обеспечивая достаточную мощность для резки стали толщиной 1/2 дюйма по доступной цене.
Высокочастотная вспомогательная дуга увеличивает срок службы расходных материалов. Однако такая система запуска не работает со столом с ЧПУ из-за высокочастотных помех цифровой электронике.Плазменный резак YesWelder CUT-55DS поставляется с основным соединением на 120 вольт и адаптером на 240 вольт. YesWelder предоставляет на этот аппарат как годовую гарантию, так и 30-дневную гарантию возврата денег.
3.
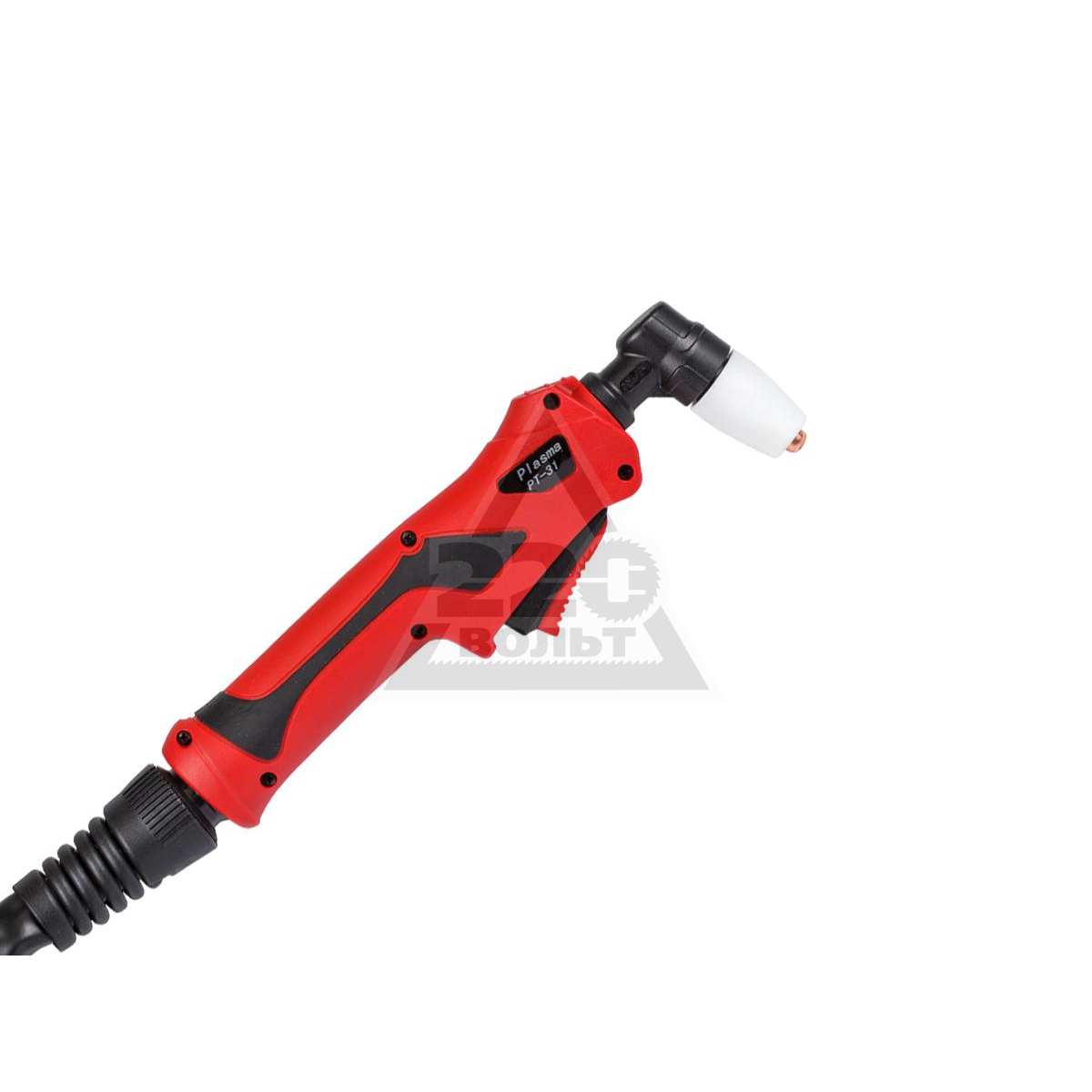
- 120 вольт мощность
- 5-летняя гарантия
- Fan-On-Demand экономит электроэнергию
- Режет сталь 3/16 дюйма
- Выходная мощность 12 А
Плюсы
- Легкий плазменный резак
- Эргономичный дизайн фонарика
- 12-футовый шланг горелки
- Бесконтактный запуск дуги
- Пост-поточное охлаждение
Минусы
- Жалобы на низкое давление воздуха
- Низкая режущая способность
Обзор
Плазменный резак Hobart Airforce 12ci предлагает расширенные профессиональные функции. Постпоточное воздушное охлаждение поддерживает поток воздуха после завершения резки. Функция AirForce 12ci Fan-On-Demand помогает защитить корпус от пыли и мусора, а также сэкономить электроэнергию. Он спроектирован таким образом, чтобы быть легким, прочным и легко переносимым.
Этот аппарат плазменной резки работает от напряжения 120 вольт, мощности которого достаточно для резки стали толщиной 3/16 дюйма при входном напряжении 120 вольт. Этой мощности достаточно, чтобы провести крупный ремонт бытовой техники, ворот, ограждений и гаражных ворот. Профессиональные специалисты по кондиционированию воздуха и обогреву могут пронести этот плазменный резак в дом и подключить его к электросети домовладельца без продувки цепей.Встроенный воздушный компрессор — еще один приятный штрих, устраняющий расходы, беспорядок и проблемы отдельного компрессора, чтобы обеспечить необходимое давление резки.
Бесконтактный запуск пилотной дуги и эргономичный резак в сочетании с системой автоматической настройки упрощают освоение станка для начинающих. Хобарт предоставляет на плазменный резак AirForce 12ci 5-летнюю гарантию, подчеркивая его статус серьезного профессионального инструмента, созданного в соответствии с промышленными стандартами.
4.Плазменный резак PrimeWeld CUT60
- Непрерывная пилотная дуга
- Двойной вход 120/240 вольт
- Совместимость с ЧПУ
- Горелка с обратным затвором PT60
- Таймер продувки воздуха
Плюсы
- Блокировка спускового крючка 2T / 4T
- Центральный разъем европейского типа
- Длина резака 20 футов
- Бесконтактный запуск дуги
- Гарантия 3 года
Минусы
- Выключатель находится сзади
- Шнур питания немного короткий
Обзор
Плазменный резак PrimeWeld CUT60 обладает большой мощностью. Максимальный ток 60 А позволяет резать сталь толщиной до 7/8 дюймов. Нижний предел в 20 ампер подходит для листового металла 26 калибра. Он имеет вход двойного напряжения с входным напряжением 120 и 240 вольт. Есть стандартный 3-полюсный шнур питания 240 и кабель-адаптер для подключения к 120 розеткам.
Если вам нужен плазменный резак для использования на станке плазменной резки с ЧПУ с компьютерным управлением, плазменный резак PrimeWeld CUT60 полностью совместим с ЧПУ. Машины, которые используют высокочастотный запуск дуги, будут мешать работе цифровой электроники в компьютерах.В этом аппарате используется 20-футовый резак с обратным затвором PT60, который использует давление воздуха для зажигания дуги при нажатии на спусковой крючок.
Плазменный резак PrimeWeld CUT60 оснащен непрерывной вспомогательной дугой, которая позволяет резать такие материалы, как просечно-вытяжной металл, соты и решетки. Когда дуга пересекает пространство, резак выключается, пока он не коснется следующего твердого пятна и не зажжет дугу снова. Владельцы PrimeWeld очень лояльны и высоко ценят качество сборки, производительность и обслуживание клиентов.
5.Машина для плазменной резки Forney 250 P Plus
- Источник входного напряжения 120 В
- Гарантия 3 года
- 15-футовый шнур питания
- Режет сталь 1/8 дюйма
- Номинальный ток 12 А
Плюсы
- Элементы управления просты в использовании
- Работает от генератора
- 15-футовый фонарь
- Старт перетаскивания
- Встроенный склад расходных материалов
Минусы
- Не подходит для объемных работ
- Компрессор не самый сильный
Обзор
Созданный в соответствии с профессиональными стандартами, Forney 250P Plus имеет функцию зажигания дуги с торможением. Плазменные резаки без резака могут быть трудными в использовании, потому что резак должен находиться на определенном расстоянии от режущей поверхности, чтобы обеспечить высокое качество резки. Благодаря способности перетаскивания резака головку резака можно поместить прямо на металл и буквально тащить, чтобы сделать рез.
Еще одна приятная особенность легкого автомобиля Forney 250P Plus — это встроенный воздушный компрессор. Некоторых пользователей не устраивает давление воздуха, поддерживаемое бортовым компрессором. Это легкий плазменный резак весом 43 фунта.Источник питания на 120 вольт означает, что этот плазменный резак можно подключать где угодно.
Хотя он отлично подходит для случайных сокращений, например, для ремонта на дому, для начала резки требуется слишком много времени, чтобы его можно было использовать для производственных работ. Между зажиганием дуги и началом резки существует задержка в несколько секунд, которая складывается при выполнении нескольких отдельных разрезов в день. Forney 250P Plus имеет трехлетнюю гарантию и имеет встроенное хранилище расходных материалов.
6.Плазменный резак Everlast PowerPlasma 52i
- Питание от двух напряжений 120/240
- Резак PT60, 14 футов
- Выбираемые режимы вспомогательной дуги
- Пуск дуги с обратным током
- Выход от 20 до 50 ампер
Плюсы
- Совместимость с ЧПУ
- Таймер продувки воздуха
- Центральный разъем резака европейского типа
- Руководство по настройке светодиодного дисплея
- Гарантия 5 лет
Минусы
- Качество сборки несовместимо
- Плохо написанное руководство
Обзор
Плазменный резак Everlast PowerPlasma 52i — это новая версия аппарата PowerPlasma 50S, производимого в течение длительного времени. Одна из новых функций, разработанных в PowerPlasma 52i, — это встроенное руководство по настройке цифровых светодиодов для давления воздуха. Everlast также добавил функцию продувки воздуха, чтобы воздух продолжал поступать до 60 секунд после остановки резака, чтобы улучшить качество резки и обеспечить быстрое охлаждение.
Пилотный механизм с обратной продувкой имеет отдельные режимы для нормальной резки, резки строжки и для плазменных столов с ЧПУ. Плазменный резак Everlast PowerPlasma 52i оснащен двухрежимным резаком. Для стандартных резов он ограничивает продолжительность работы вспомогательной дуги для экономии наконечников и расходных материалов.Существует также непрерывный пилотный режим, который повторно зажигает дугу после того, как головка резака проходит через пространство, такое как режущие решетки или расширенная металлическая сетка.
Плазменный резак Everlast PowerPlasma 52i имеет 14-футовый резак PT60 и диапазон выходной мощности 20-50 ампер. Некоторые владельцы сообщают о проблемах при первоначальном использовании, чаще всего это компьютерный код, указывающий на отсутствие воздушного потока. Everlast предоставляет на эту машину 5-летнюю гарантию.
Плазменные резаки | Langmuir Systems
Выбор плазменного резака для CrossFire
Плазменный стол CrossFire ™ с ЧПУ был спроектирован как машина для хобби, чтобы принять широкий спектр доступных плазменных резаков, имеющихся сегодня на рынке. Единственным жестким требованием является то, что плазменный резак не должен использовать высокочастотный пусковой механизм для зажигания плазменной дуги. Плазменные резаки такого типа строго запрещены для использования на аппарате CrossFire ™, поскольку высокочастотная дуга может вызвать необратимое повреждение электронных компонентов аппарата.
К счастью, сегодня в большинстве современных плазменных резаков для создания пилотной дуги используется так называемый пусковой механизм с обратной продувкой.Ниже мы составили список устройств плазменной резки, которые компания Langmuir Systems сочла совместимыми с машиной CrossFire ™, в которой используется метод пуска с продувкой. Этот список никоим образом не является исчерпывающим для всей совместимости на рынке, поэтому, если вы не уверены в своем плазменном резаке, мы рекомендуем вам проконсультироваться с вашим производителем и узнать о методе зажигания дуги для вашей конкретной модели.
Каждый аппарат CrossFire ™ стандартно поставляется с универсальным держателем резака, который подходит как для ручных, так и для машинных резаков.
Плазменные резаки RAZORWELD
Наша миссия с самого начала заключалась в том, чтобы довести плазменную резку с ЧПУ до уровня хобби, предложив недорогое и индивидуальное решение для домашнего потребителя. Хотя сегодня на рынке представлено множество высококачественных аппаратов плазменной резки, многие из этих моделей намного дороже, чем сам аппарат CrossFire ™. После оценки качества, совместимости и доступности нескольких аппаратов плазменной резки мы решили сотрудничать с RAZORWELD, чтобы объединить действительно мощную линейку аппаратов плазменной резки с аппаратом CrossFire ™ по невероятной цене.Воспользуйтесь преимуществами сниженной цены при оформлении заказа, связав свой аппарат CrossFire ™ с аппаратом плазменной резки RAZORWELD.
Гарантия и меры безопасности
Соединение проводов пускового курка резака может нарушить или не нарушить гарантию на ваш плазменный резак. Вы обязаны проконсультироваться с производителем плазменного резака относительно условий гарантии и того, нарушает ли выполнение процедуры сварки эти условия. Langmuir Systems не несет ответственности за нарушение гарантии.
Для завершения процедуры необходимо открыть шкаф источника питания плазменного резака, который подвергнет вас воздействию высокого напряжения и высоких электрических компонентов. Вы несете ответственность за то, чтобы все работы выполнялись безопасно и с отключенным питанием. Если у вас есть какие-либо сомнения относительно вашей способности безопасно выполнять эту работу, мы настоятельно рекомендуем вам обратиться к услугам профессионального электрика. Langmuir Systems не несет ответственности за травмы или смерть, возникшие в результате неправильного или небезопасного выполнения этой процедуры.
После сращивания проводов очень важно никогда не оставлять кабель зажигания резака подключенным к корпусу электроники CrossFire, если резак не установлен в держателе резака и не готов к резке. Если резак требуется для ручной резки, обязательно сначала отсоедините кабель зажигания, прежде чем снимать резак. В противном случае электронная система CrossFire может включить фонарик, когда он физически находится в небезопасном месте; например, в присутствии летучих или взрывоопасных веществ.Если не отсоединить кабель зажигания резака от корпуса электроники, когда резак не установлен, это может привести к серьезным травмам или смерти. Langmuir Systems не несет ответственности за травмы или смерть в результате несоблюдения этого важного требования безопасности.
Уведомление о плазменном резаке CrossFire PRO — 21.09.19
Те же устройства плазменной резки с обратным пуском, которые совместимы с CrossFire, совместимы с PRO. Длина кабеля резака должна составлять не менее 16 футов для использования на аппарате.Если длина провода резака меньше 16 футов, обратитесь к производителю плазменной резака, чтобы узнать, могут ли они поставить резак с более длинным проводом. Примечание. Все аппараты Vipercut 30i стандартно поставляются с 13-дюймовым кабелем резака и не могут использоваться с PRO без приобретения более длинного провода резака.
Уведомление о плазменном резаке— 04.09.18
Мы больше не можем рекомендовать следующие плазменные резаки, совместимые с CrossFire.
- Lotos Supreme Cut 60D
- Lotos Supreme LTP5500D
- Харбор Фрахт / Чикаго Электрик, версия 1
- AHP AlphaCut 60
Известно, что помехи, создаваемые источниками питания этих резаков, вызывают проблемы с электроникой CrossFire. Владельцы этих моделей, которые хотят использовать свой резак с CrossFire, должны предпринять дальнейшие шаги для обеспечения надлежащего заземления и устойчивости к электромагнитным помехам в своих системах.
Использование этих резаков не поддерживается компанией Langmuir Systems и на ваш страх и риск.
Плазменные резаки, совместимые с CrossFire ™
Плазменные резаки | Линкольн Электрик
Выберите 3 продукта для сравнения Плазменный резак Tomahawk® 1500 — K2809-1, K3477-1, -2
Основные функции
Входная мощность
Процессы Плазменная резка, строжка | Начиная от: 4366 долл. США.00 |
Выберите 3 продукта для сравнения Плазменный резак Tomahawk® 375 — K2806-1
Основные функции
Входная мощность Процессы Плазменная резка низкоуглеродистой стали, нержавеющей стали, алюминия, латуни, меди | Начиная от: & nbsp $ 1 750,00 |
Выберите 3 продукта для сравнения Плазменный резак Tomahawk® 625 — K2807-1
Основные функции
Входная мощность Процессы Плазменная резка низкоуглеродистой стали, нержавеющей стали, алюминия, латуни, меди | Начиная от: & nbsp $ 2 368,00 |
Выберите 3 продукта для сравнения Плазменный резак Tomahawk® 1000 — K2808-1
Основные функции
Входная мощность Процессы Плазменная резка низкоуглеродистой стали, нержавеющей стали, алюминия, латуни, меди | Начиная от: 3089,00 $ |
Выберите 3 продукта для сравнения Система плазменной резки Spirit® II 400A, автоматическая — BK1111-000043-000049
Основные функции
Входная мощность Процессы Плазменная резка, маркировка |
Выберите 3 продукта для сравнения Система плазменной резки Spirit® II 275A, автоматическая INOVA — BK1111-000120 — 000129
Основные функции
Входная мощность Процессы Плазменная резка, маркировка |
Выберите 3 продукта для сравнения Система плазменной резки Spirit® II 400A, автоматическая INOVA — BK1111-000143 — 000149
Основные функции
Входная мощность Процессы Плазменная резка, маркировка |
Выберите 3 продукта для сравнения Burny 10LCD Plus
Основные функции
Входная мощность
Процессы Плазменная резка, кислородная резка и гидроабразивная резка |
Выберите 3 продукта для сравнения Фантом II
Основные функции
Входная мощность Процессы Плазменная резка, фигурная резка с ЧПУ, кислородное топливо |
Как работает плазменный резак
Что такое плазма?
Чтобы правильно объяснить, как работает плазменный резак, мы должны начать с ответа на основной вопрос: «Что такое плазма? Проще говоря, плазма — это четвертое состояние вещества.Обычно мы думаем, что материя имеет три состояния: твердое, жидкое и газообразное. Материя переходит из одного состояния в другое за счет введения энергии, например тепла. Например, вода переходит из твердого (лед) в жидкое состояние при приложении определенного количества тепла. Если уровень тепла увеличится, он снова изменится с жидкости на газ (пар). Теперь, если уровень тепла снова увеличится, газы, составляющие пар, станут ионизированными и электропроводящими, превратившись в плазму.Плазменный резак будет использовать этот электропроводящий газ для передачи энергии от источника питания к любому проводящему материалу, в результате чего процесс резки будет более чистым и быстрым, чем при использовании кислородного топлива.
Формирование плазменной дуги начинается, когда газ, такой как кислород, азот, аргон или даже производственный воздух, пропускается через небольшое отверстие сопла внутри горелки. Электрическая дуга, генерируемая от внешнего источника питания, затем вводится в этот поток газа под высоким давлением, в результате чего возникает то, что обычно называют «плазменной струей».Плазменная струя сразу достигает температуры до 40000 ° F, быстро пробивая заготовку и сдувая расплавленный материал.
Компоненты плазменной системы
Источник питания — Источник питания для плазменной резки преобразует одно- или трехфазное сетевое напряжение переменного тока в плавное постоянное напряжение постоянного тока в диапазоне от 200 до 400 В постоянного тока. Это постоянное напряжение отвечает за поддержание плазменной дуги на всем протяжении резки. Он также регулирует требуемый выходной ток в зависимости от типа и толщины обрабатываемого материала.
- Консоль зажигания дуги
— Схема ASC вырабатывает переменное напряжение приблизительно 5000 В переменного тока на частоте 2 МГц, которое создает искру внутри плазменной горелки для создания плазменной дуги.
- Плазменный резак
— Плазменный резак предназначен для обеспечения правильного выравнивания и охлаждения расходных деталей. Основными расходными деталями, необходимыми для генерации плазменной дуги, являются электрод, завихритель и сопло. Дополнительный защитный колпачок может использоваться для дальнейшего улучшения качества резки, а все части удерживаются вместе внутренними и внешними удерживающими колпачками.
Подавляющее большинство систем плазменной резки сегодня можно сгруппировать как в обычные, так и в прецизионные категории.
В обычных плазменных системах в качестве плазменного газа обычно используется производственный воздух, а форма плазменной дуги в основном определяется отверстием сопла. Приблизительная сила тока плазменной дуги этого типа составляет 12-20K ампер на квадратный дюйм.Во всех портативных системах используется обычная плазма, и она все еще используется в некоторых механизированных приложениях, где допуски деталей более приемлемы. | ||
Системы прецизионной плазменной резки (с высокой плотностью тока) спроектированы и спроектированы так, чтобы производить резку с максимальной резкостью и высочайшим качеством, достижимую с помощью плазмы. Конструкции резака и расходных деталей более сложны, и в комплект входят дополнительные детали для дальнейшего сужения и формы дуги.Прецизионная плазменная дуга составляет примерно 40-50 кОм на квадратный дюйм. Несколько газов, таких как кислород, воздух высокой чистоты, азот и смесь водорода / аргона / азота, используются в качестве плазменного газа для получения оптимальных результатов на множестве проводящих материалов. |
Ручной режим В типичной ручной плазменной системе, такой как наша Tomahawk® Air Plasma, расходные части электрода и сопла контактируют друг с другом внутри резака в выключенном состоянии.При нажатии на спусковой крючок источник питания вырабатывает постоянный ток, который течет через это соединение, а также инициирует поток плазменного газа. Как только плазменный газ (сжатый воздух) создает достаточное давление, электрод и сопло раздвигаются, что вызывает электрическую искру, которая превращает воздух в плазменную струю. Затем поток постоянного тока переключается от электрода к соплу на путь между электродом и заготовкой. |
Прецизионная плазменная установка
Внутри прецизионного плазменного резака электрод и сопло не соприкасаются, а изолированы друг от друга закручивающим кольцом с небольшими вентиляционными отверстиями, которые превращают предварительный поток / плазменный газ в закрученный вихрь. Когда на источник питания подается команда пуска, он генерирует до 400 В постоянного тока напряжения холостого хода и запускает предварительную подачу газа через шланг, подсоединенный к горелке.Сопло временно подключается к положительному потенциалу источника питания через цепь вспомогательной дуги, а электрод находится на отрицательном полюсе.
Затем из пульта запуска дуги генерируется высокочастотная искра, которая заставляет плазменный газ становиться ионизированным и электрически проводящим, в результате чего возникает путь тока от электрода к соплу, и создается пилотная плазменная дуга.
Как только вспомогательная дуга контактирует с заготовкой (которая подключается к заземлению через планки стола для резки), путь тока смещается от электрода к заготовке, высокочастотная дуга отключается, и цепь вспомогательной дуги размыкается. .
Затем источник питания нарастает постоянный ток до значения силы тока резки, выбранного оператором, и заменяет газ предварительной продувки оптимальным плазменным газом для разрезаемого материала. Также используется вторичный защитный газ, который выходит за пределы сопла через защитный колпачок.
Форма защитного колпачка и диаметр его отверстия заставляют защитный газ еще больше сжимать плазменную дугу, что приводит к более чистому сечению с очень малыми углами скоса и меньшим пропилом.
Руководство по лучшим плазменным резакам для 2021 года и обзоры плазменных резаков
Плазменные резаки— чрезвычайно популярный инструмент для резки металлов и автомобильных работ. Они режут быстро, точно и могут резать любой токопроводящий металл.Ниже приводится руководство для покупателей, сравнительная таблица и наши лучшие решения для плазменных резаков различной толщины, включая лучшие со встроенными воздушными компрессорами.
Щелкните любую из ссылок ниже, чтобы найти сварочный аппарат, который лучше всего подходит для ваших нужд.
Сравнительная таблица лучших плазменных резаков
1. Лотос LTP5000D
Лучшее за деньги
Лучшее до 500 $
Lotos LTP5000D, пожалуй, самый популярный аппарат плазменной резки на рынке.Это отличный выбор для любителей, которым нужен универсальный резак, но которые не хотят тратить слишком много денег. У него есть вспомогательная дуга, поэтому он будет аккуратно прорезать ржавый или окрашенный металл и позволяет резать, не касаясь металла, в отличие от других дешевых машин. Он поддерживает двойное напряжение, но если вы хотите использовать 110 В, вам нужно будет купить переходник на 110 В. Он действительно быстро проходит через расходные материалы и не выдерживает частого использования, как плазменные резаки крупных брендов, но расходные материалы относительно недорогие.Он аккуратно прорежет сталь 1/2 дюйма. Вам нужно не торопиться с 1/2 ″ и 1/4 ″, но он пройдет через 1/8 ″ быстро и быстро. Он режет довольно толстый слой, поэтому он не идеален для более точной резки.
В целом мы считаем, что это лучшая цена для вашего устройства плазменной резки. Он идеально подходит, если вы ищете небольшой плазменный резак по доступной цене для домашних хобби-проектов. Если вы ищете что-то еще более дешевое, обратите внимание на LT5000D, аналогичную модель, но без вспомогательной дуги.На это устройство предоставляется гарантия сроком 1 год, чтобы защитить вас в краткосрочной перспективе, но, возможно, вам лучше взглянуть на устройство Hypertherm, если вам нужна более долговечная машина.
Технические характеристики
| Плюсы
Минусы
|
2.Hypertherm Powermax 30XP
Лучшее до 1500 $
Лучшее для 1/4 ″
Hypertherm Powermax 30 XP — исключительный аппарат плазменной резки. Hypertherm проявляет огромную осторожность при проектировании своих устройств и собирает их с непревзойденной тщательностью (прямо здесь, в США). Вы знаете, что получите отличные результаты с Hypertherm и что он выдержит испытание временем. Они созданы для интенсивного использования в профессиональной среде и имеют 3-летнюю гарантию.
В нем есть все необходимое для резки (кроме воздуха), в том числе действительно хороший жесткий футляр для переноски, в котором вы можете хранить все свое оборудование, например, запасные расходные материалы, которые поставляются с устройством.
Модель 30XP очень компактна и легка, весит всего 21 фунт, и включает в себя расходные детали FineCut для более тонкой и детальной резки. Он идеально подходит для стали толщиной 1/4 дюйма, но также может резать 3/8 дюйма при скорости 20 дюймов в минуту. Качество резки чистое и резкое, можно подключить до 110 или 220 В.
В целом это один из самых надежных устройств плазменной резки на рынке, обеспечивающий качественные результаты при длительном сроке службы расходных деталей.
Технические характеристики
| Плюсы
Минусы |
3.
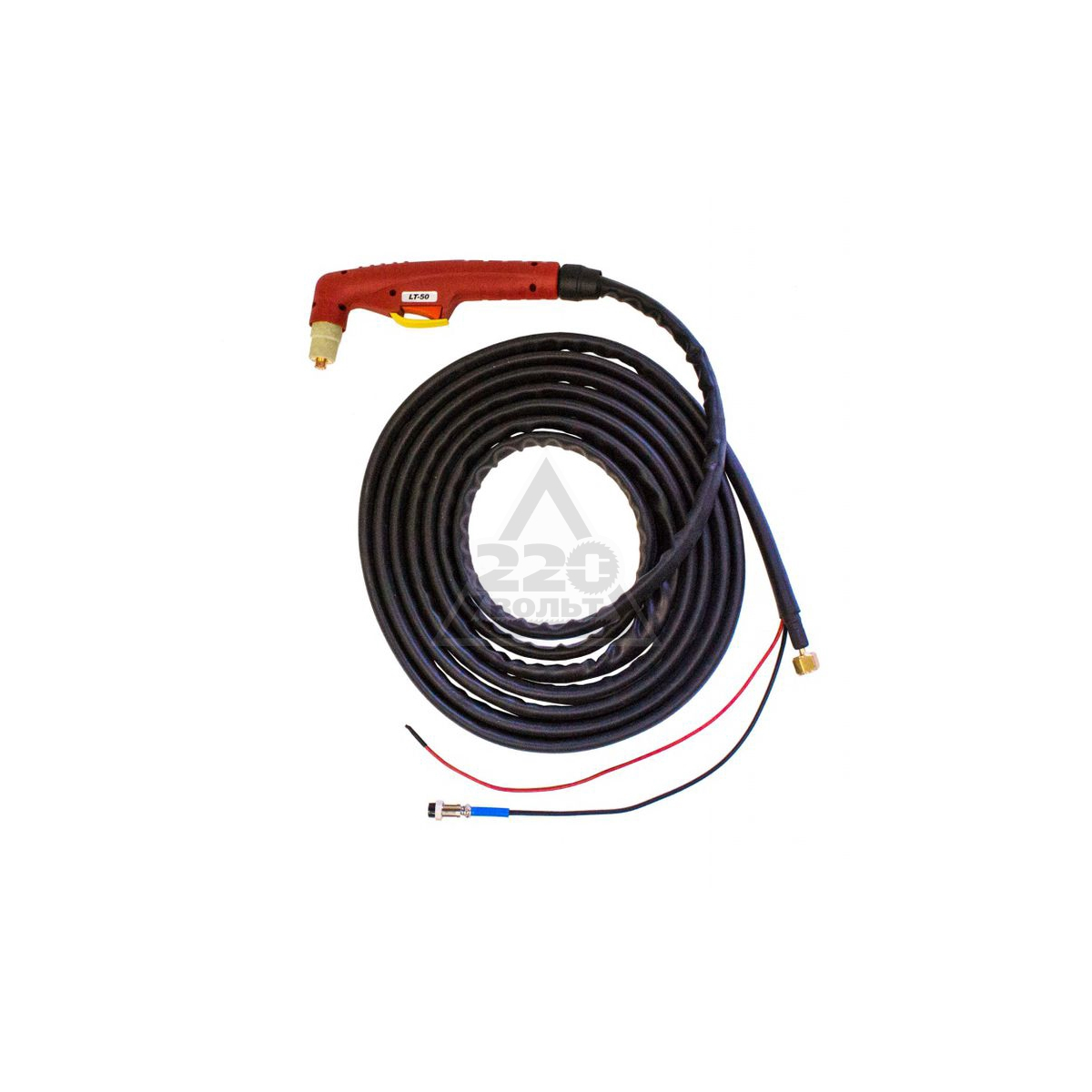
Best со встроенным воздушным компрессором
Это еще один превосходный аппарат плазменной резки от Hypertherm, на этот раз он оснащен встроенным воздушным компрессором, что делает его более универсальным. Это, безусловно, лучший аппарат плазменной резки со встроенным воздушным компрессором на рынке. Hypertherm производит только устройства плазменной резки, и они вкладывают много энергии в проектирование и производство станков самого высокого качества. Он обладает такими же превосходными характеристиками, как Powermax 30 XP, и позволяет довольно комфортно резать 1/2 дюйма, при этом 3/8 дюйма являются идеальным срезом.Hypertherm также создает лучшие в отрасли расходные материалы, которые действительно долговечны, поэтому в долгосрочной перспективе они вам не будут стоить. В целом он легкий, портативный, простой в использовании и дает отличные результаты — вы не ошибетесь.
Технические характеристики
| Плюсы
Минусы |
Лучший плазменный резак до $ 1000
Hobart Airforce 12ci
1. Фирменное наименование: Hobart
2. Модель: Airforce 12ci
3. Высота: 10 дюймов
4. Длина: 13 дюймов
5. Ширина: 8,25 дюймов
6. Рабочий цикл: 35 % При 12 В
7. Входное напряжение: 110 В
8. Вес продукта: 25,1 фунта
9. Идеальная резка: 1/8 дюйма
10. Разрезная резка: 1/4 дюйма
11. Максимальный ток: 12A
12. Воздушный компрессор: Да
Наш любимый плазменный резак стоимостью менее 1000 долларов — Hobart Airforce 12ci.Лучшая особенность этого — то, что он имеет встроенный воздушный компрессор. Это означает, что вам никогда не придется беспокоиться о подключении его к воздушному компрессору, и вы сможете использовать его, когда захотите. Он не такой мощный, как некоторые другие резаки, потому что работает только от 110 В, но все же дает хорошие результаты на более тонком металле. Это отличное маленькое устройство, изготовленное в соответствии с качеством Хобарта, является отличным выбором для людей, которым не требуется такая большая мощность, но которые хотят иметь качественный плазменный резак.
Узнать цену
Hobart Airforce 40ci
1.Фирменное наименование: Hobart
2. Модель: Airforce 40i
3. Высота: 11,25 дюйма
4. Длина: 14,25 дюйма
5. Ширина: 8,25 дюйма
6. Рабочий цикл: 50 % @ 40A
7. Входное напряжение: 240 В
8. Вес продукта: 30,6 фунта
9. Ideal Cut: 5/8 дюйма
10. Sever Cut: 7/8 дюйма
11. Максимальный ток: 40A
12. Воздушный компрессор: №
Это еще один отличный юнит, построенный Хобартом. Он способен аккуратно резать сталь 5/8 дюйма и отрезать до 7/8 дюйма, поэтому обладает большой мощностью. Он работает только от 240 В, поэтому вы не сможете использовать его с домашним блоком питания. Он имеет очень хороший рабочий цикл с максимальной мощностью 50% при 40 А. Эта машина создана для длительных промышленных проектов и не подведет.
Узнать цену
Что такое плазменный резак?
Плазменный резак — это машина, которая позволяет легко резать любой токопроводящий металл, включая алюминий, нержавеющую сталь, медь, латунь, сталь и другие.Плазменная струя формируется путем пропускания газа через сопло в горелке и объединения его с электрической дугой, генерируемой источником питания. Он достигает температуры до 40000 ° F и может мгновенно расплавлять и резать металл.
Зачем нужен плазменный резак?
Плазменные резаки — лучший способ резать металл. Они резают намного быстрее, чем кислородно-топливные, и более точны из-за меньшей ширины реза. Это означает, что окружающая область не подвержена воздействию тепла, и вы можете уточнить область разреза.Плазменная резка также позволяет резать любой токопроводящий металл, включая нержавеющую сталь или алюминий, поэтому это универсальный вариант.
Как настроить плазменный резак?
- Соблюдайте все инструкции по технике безопасности, приведенные в руководстве, включая использование шлема для защиты глаз от излучения и сварочных перчаток.
- Подсоедините воздушный компрессор к аппарату плазменной резки (см. Инструкции, как это сделать). Если ваш плазменный резак имеет встроенный воздушный компрессор, в этом нет необходимости.
- Подключите резак к аппарату плазменной резки
- Подсоедините зажим заземления к плазменной резке и надежно прикрепите его к заготовке. Убедитесь, что на стыке зажима с заготовкой нет ржавчины или краски.
- Убедитесь, что все разъемы надежно закреплены
- Задайте правильные настройки для толщины металла, который вы режете.
- Проверьте резак, чтобы увидеть, есть ли поток воздуха, кратковременно нажав на спусковой крючок на резаке.
- Если есть поток воздуха — переместите головку резака на металлическую заготовку, чтобы разрезать металл.
Что искать в аппарате плазменной резки
Ideal Cut
Первое, на что следует обратить внимание при выборе устройства плазменной резки, — это толщина металла, который он разрезает. Вам следует подумать о том, с какой толщиной металла вы будете работать чаще всего, и подыскать идеальный срез этой толщины. Рассмотрим толщину мягкого металла, которую машина может резать со скоростью 10 дюймов в минуту. Разделительный разрез не даст столь хороших результатов, и вам лучше использовать эту максимальную толщину только изредка и там, где вы не против окалины.Если вам требуется качественная стрижка, вам следует выбрать идеальную стрижку.
Толщина разрыва
Толщина разделения — это максимальная толщина, которую плазменный резак может разрезать металл, однако для эффективной резки металла требуется начало кромки. При такой толщине резание будет очень медленным, и машина не будет вырабатывать достаточно тепла для чистого реза и будет шероховатой и заполненной окалиной. Резка металла необходимой толщины не рекомендуется для регулярной резки или достижения наилучших результатов.
Встроенный воздушный компрессор
Большинство аппаратов плазменной резки потребуют от вас использования дополнительного воздушного компресса, прежде чем вы сможете с ним резать. Но есть некоторые аппараты плазменной резки со встроенным воздушным компрессором. Это более дорогой, но более удобный вариант, поскольку, если вы находитесь в поле, вам не понадобится отдельный воздушный компрессор с собой. Вам не нужно подключать воздушный шланг или что-то еще, вы можете просто подключить его и начать резку. Это определенно то, что стоит рассмотреть за небольшие дополнительные деньги.
Pilot Arc
Лучшие аппараты плазменной резки будут иметь вспомогательную дугу в качестве функции резки, что означает, что вы можете выполнять рез без соприкосновения наконечника резака с металлом. Пилотная дуга помогает прорезать окрашенные и ржавые поверхности. Помните, что если вы режете ржавые или окрашенные поверхности, вам необходимо очистить место, где вы подключаете заземляющий зажим. Кроме того, если вы идете по металлу с зазорами между металлом, например, с сеткой, вам не нужно останавливать и запускать горелку, потому что она горит непрерывной дугой.У большинства сварщиков, кроме дешевых китайских, есть запальная дуга.
Расходные материалы
После того, как вы приобрели плазменный резак, в текущую стоимость будет входить замена расходных материалов. Расходными материалами считаются 5 частей: удерживающий колпачок, электрод, сопло, защитный колпачок и завихритель. Все они имеют разную продолжительность жизни в зависимости от ряда переменных, но когда вы пробиваете металл, и расплавленный металл дует обратно в факел, они обязательно получают некоторые повреждения. Отверстие в насадке должно быть идеально круглым, иначе разрез будет поврежден.Кроме того, увеличение глубины укладки приведет к увеличению окалины и ухудшению качества реза. Более дорогие сварщики обычно имеют более долговечные расходные материалы. Несмотря на то, что машины Hypertherm дороги, они имеют низкие эксплуатационные расходы благодаря превосходному качеству расходных материалов.
Цена
Цена очень важна при покупке плазменного резака. Купить дешевый плазменный резак китайского производства несложно, но убедитесь, что вы знаете о рисках. Срок службы недорогого аппарата будет намного короче, чем у сварочного аппарата, сделанного в США или от надежного производителя.Hypertherm, Hobart и Miller надежны, имеют отличное качество и могут легко прослужить в 3 или 4 раза дольше, чем дешевые устройства плазменной резки, что является одной из причин их дороговизны.
Напряжение
Плазменные резаки с входным напряжением 110/115/120 В совместимы с обычным внутренним источником питания. Они отлично подходят для начинающих или если вы используете их дома, но их мощность ограничена. Если вам нужно немного больше мощности, вам понадобится один с входом 220 В, который совместим только с генераторами.Если вы приобретете плазменный резак с входным напряжением 110 В и 220 В, тогда у вас будет выбор источников питания, так что это мои любимые типы из-за их универсальности.
Сила тока
Сила тока плазменного резака указывает толщину металла, который он может резать. например выходной ток 30 А должен удобно резать металл толщиной 3/8 дюйма. но выходная мощность 12 А может сократить только приблизительно 1/8 дюйма. Если вы используете входное напряжение 220 В, вы сможете увеличить силу тока и резать более толстый металл.
Рабочий цикл
Рабочий цикл означает время, в течение которого машина может непрерывно работать до того, как ей потребуется охлаждение. Например, рабочий цикл 35% при установленной силе тока и напряжении будет означать, что при этих настройках плазменный резак может оставаться включенным в течение 3,5 минут из 10 минут без перегрева. Продолжительность включения увеличится при понижении силы тока. Более длительный рабочий цикл при более высокой силе тока лучше для выполнения длинных и глубоких разрезов в металле.
Вес
Вес всегда нужно учитывать при покупке оборудования, так как вы не хотите таскать с собой слишком много тяжелого оборудования.К счастью, большинство устройств плазменной резки в наши дни относительно легкие благодаря инверторной технологии. Если вы покупаете установку для плазменной резки со встроенным воздушным компрессором, она может быть немного тяжелее, но все же будет намного более портативной, поскольку вам понадобится только плазменная резка, и вы готовы к работе.
Безопасность
И последнее, но не менее важное: безопасность — это приоритет номер один. Прочтите все инструкции по технике безопасности, содержащиеся в буклете с инструкциями для выбранного вами устройства плазменной резки.Убедитесь, что у вас есть хорошие защитные очки, чтобы защитить глаза. Несмотря на то, что дуга не такая интенсивная, как сварочная дуга, она может повредить глаза, поэтому попробуйте надеть очки с оттенком 3 или 5. Вы также должны носить перчатки. Мне нравится носить перчатки MIG или TIG, которые не слишком громоздки и позволяют вам чувствовать, что вы делаете, одновременно защищая себя. Не используйте перчатки из синтетического материала, потому что они могут плавиться и прилипать к вашей коже. Всегда используйте кожу. Накройте свое тело, ноги и руки прочным хлопковым материалом, чтобы защитить его от искр и дуги.Наконец, пока вы будете рубить металл, наденьте ботинки со стальной защитой, чтобы не пораниться падающим металлом.
Заключение
Надеюсь, это руководство поможет вам выбрать лучший плазменный резак для ваших нужд. Если я что-то пропустил, не стесняйтесь оставлять вопросы в комментариях ниже.
Надеемся, вам понравилась наша статья «Лучшие установки для плазменной резки в 2021 году». Если да, то мы были бы очень признательны, если бы вы оценили ее и поделились ею.
Большая экономия на плазменных резаках и оборудовании для резки металла, скидка 10% при первом заказе
Longevity производит профессиональное оборудование для плазменной резки для энтузиастов и профессионалов уже более десяти лет.Наши машины плазменной резки мощные, портативные и надежные. Машины плазменной резки серии ForceCut прошли испытание на рынке сварки на станках с ЧПУ и доказали, что они обеспечивают качественную резку при толщине более 2 дюймов. Плазменные резаки долговечности имеют диапазон от 40 до 100 ампер и обеспечивают функцию Pilot Arc для резки расширенных металлов, а также позволяют пользователю легко зажигать дугу.
С оборудованием для плазменной резки Longevity ForceCut вы получите высокую производительность резки, стабильную и сильную дугу, а также меньшее количество шлака от вырезанной металлической детали.Плазменные резаки долговечности способны вырезать, протыкать, а также серьезно резать любые металлические части, включая алюминий, и работать от любого воздушного компрессора с минимальным давлением 70 фунтов на квадратный дюйм и 3,0 куб. Это означает, что вы можете использовать любой воздушный компрессор, от малогабаритного портативного до большого заводского компрессора, для управления нашими станками плазменной резки.
Longevity были протестированы против некоторых более крупных брендов с премиальной ценой, и результаты независимых испытаний показали превосходство во всех аспектах, включая срок службы расходных материалов плазменных резаков, производительность резки, скорость резки и цену.
Плазменные резакисчитаются самым чистым способом резки металла. С плазменным резаком скорость резки намного выше, очистка намного меньше по сравнению с газовым резаком с ацетиленом кислородом, а эффективность значительно повышается. Помимо лучшего инструмента для резки металла, плазменная резка значительно снижает эксплуатационные расходы не только на срок службы расходных материалов плазменной резки, но и на время, которое вы экономите, не занимаясь очисткой конечного продукта.
Еще одним преимуществом плазменных резаков является тот факт, что они способны создавать нестандартные детали и выводить ваше производство на более высокий уровень изготовления при подключении к столам с ЧПУ. Плазменные резаки Longevity полностью совместимы со столами с ЧПУ и обеспечивают беспроблемную интеграцию с портом ЧПУ на задней панели большинства моделей. При подключении к столу с ЧПУ резка выполняется точно и плавно. Если вы хотите добавить наш станок плазменной резки к столу с ЧПУ, мы предлагаем приобрести станок плазменной резки большей мощности, способный резать более толстые материалы, поскольку он будет резать более тонкие материалы с большей скоростью.
Плазменные резаки Longevity также используют функцию запуска вспомогательной дуги обратной продувки на большинстве моделей. Для конечного пользователя это означает, что наша технология плазменной резки не будет мешать работе каких-либо столов с ЧПУ или любого частотно-чувствительного оборудования или аппаратов. С функцией Blow Back start вы можете безопасно запускать плазменный резак вокруг чувствительного оборудования, включая компьютеры, кардиостимуляторы, и работать в зонах, подверженных электронной чувствительности, не опасаясь повредить какое-либо оборудование.
Хотите испытать долговечный плазменный резак? Долголетие предлагает 30-дневную 100% гарантию удовлетворения. Если заказываемый вами плазменный резак не соответствует вашим потребностям или не превосходит ваши ожидания, мы заберем его обратно! Плазменные резаки Longevity производятся более десяти лет, и тысячи довольных клиентов!
Плазменные резаки Eastwood Versa-Cut, расходные материалы для домашнего использования
Независимо от того, занимаетесь ли вы проектом реставрации или производите детали и панели для нестандартной сборки, вам понадобится плазменный резак.Плазменный резак позволяет быстро делать чистые пропилы в металле от толщины листового металла до толстого листа.
Линия плазменных резаков Versa-Cut® компании Eastwood — это инструменты профессионального качества, предназначенные для помощи в изготовлении прецизионных металлических изделий в точном соответствии со спецификациями, необходимыми для проекта.
Eastwood Плазменный резак для продажи
Хороший сварной шов начинается с того, что нужно соединить два хороших куска металла. Плазменные резаки Eastwood Versa-Cut разработаны для легкой резки черных и цветных металлов, поэтому вы можете изготавливать их по мере необходимости.Эти резаки используют электрическую дугу для нагрева высокоскоростного режущего газа, превращая его в плазменную форму, которая быстро и чисто режет расплавленный металл. Для прецизионных металлических работ по прямым линиям, углам или кривым, покупайте Eastwood, чтобы получить профессиональное качество по цене DIY.
Плазменный резак Versa-Cut для любой работы
Мы знаем, что существуют производители разных уровней, поэтому специалисты по исследованиям и разработкам предложили несколько решений для резки металла. Versa-Cut 20 110V — наш базовый вариант для точной резки листового металла и патч-панелей.Для средних нагрузок Versa-Cut 40 с двумя входами может работать с любым металлом толщиной до 3/8 дюйма. С плазменным резаком Versa-Cut 60 вы получаете резку металла промышленного уровня с размером блока и ценой, которые подходят для вашего магазина. Все наши аппараты плазменной резки разработаны для получения резких результатов на небольших участках с незначительным образованием шлака или без него.
Наборы сварочного аппарата и плазменной резки Eastwood
Доверьтесь компании Eastwood на каждом этапе работы с кузовом автомобиля, используя набор сварочного аппарата / плазменной резки.Совместите один из наших сварочных аппаратов MIG, TIG или Multi-Process с Versa-Cut того же класса, чтобы получить комплексное решение для резки и соединения металлов. Полная профессиональная резка также включает в себя многофункциональную тележку на колесиках, которая удерживает сварщика, резак и принадлежности и катит их в любом месте, где необходимо выполнить работу.
Гарантированное качество и производительность
С плазменными резаками Eastwood у вас будет незаменимый инструмент для формования кузовных панелей на восстановленных автомобилях, гоночных автомобилях, ремонте аварий и других профессиональных или любительских проектах.Если вы не уверены, какой Versa-Cut вам подходит, ознакомьтесь с нашей сравнительной таблицей или посмотрите видео с руководством покупателя в Eastwood Garage. Все наши системы плазменной резки имеют полную 3-летнюю гарантию и 100-процентную гарантию удовлетворенности клиентов.
Плазменные резаки Eastwood Versa-Cut могут резать тонкий листовой металл толщиной до 7/8 дюймов. Eastwood Versa-Cut 20 может резать металл толщиной до 1/8 дюйма и отлично подходит для работы с патч-панелями и листовым металлом. Vera-Cut 40 режет до 3/8 дюйма и идеально подходит для изготовления изделий средней тяжести.Vera-Cut 60 может прорезать лист толщиной до 7/8 дюйма и незаменим при тяжелых производственных работах.
Какой плазменный резак Eastwood вам подходит?
Видео ниже поможет вам решить, какой плазменный резак Eastwood Versa-Cut лучше всего подойдет для ваших нужд.