Силикаты – это что за минералы? Основные свойства и виды силикатов :: SYL.ru
Силикаты – это сложные вещества, которые широко распространены в пределах нашей планеты. Больше всего они представлены в земной коре, в которой по разным подсчетам составляют от 75 до 90% объема. В природе они существуют в виде минералов, но человек нашел способ получать их искусственным путем. Что такое силикаты? Где они применяются и чем отличаются от других веществ? Обо всем этом вы узнаете из нашей статьи.
Суть и значение слова «силикат»
Силикаты представляют собой разнообразные по внешнему виду и свойствам минералы, которые образованы соединениями кремнезема. На нашей планете они присутствуют преимущественно в земной коре, а также в верхней и нижней частях мантии. Термин silikat, значение которого с латинского языка переводится как «кремень», возник по аналогии с названием химического элемента Silicium (кремний), который обязательно присутствует в каждом силикате.
В мире существует больше 800 видов этих веществ. Они образуются под действием сложных магматических процессов, метаморфизма или же в результате выветривания и первичных изменений пород.
Силикаты – это самая обширная группа минералов. Многие из них формируют горные породы и являются важными полезными ископаемыми. Ряд силикатов присутствует в составе никелевых, бериллиевых, литиевых, циркониевых, цинковых и других металлических руд. Там они часто образуют пустую породу, которая обычно не находит практического применения. Большинство силикатов, наоборот, являются довольно полезными и используются в промышленности, строительстве, дизайне и ювелирном деле.

Структура и разновидности
Силикаты – это, как правило, твердые и тугоплавкие вещества. Чтобы расплавить, их нужно нагреть до температур от 1000 до 2000 градусов Цельсия. Они не разлагаются под действием кислот и обычно не растворяются в воде. Многие из них склонны к полиморфизму и образуют две или больше аллотропные модификации.
Природные силикаты – минералы, такие как глина, асбест, слюда, роговая обманка, титанит, турмалин, гранат. Наиболее распространенными являются кварц и группа полевых шпатов. Стекло, цемент, керамика, плавленые флюсы, кирпичи тоже являются силикатами, но характеризуются искусственным происхождением. Их изготавливают на основе глины, кварцевого песка, известняка, соды и других веществ, подвергая их различным способам обработки.
Природные силикаты обладают сложным строением, в основе которого лежат разнообразные вариации связей кремния и кислорода, к которым присоединяются и другие элементы, например, Mg, Ca, Al, Fe2+, Mn, K, Na, Li, B, Zr, F, H. Их кристаллические решетки состоят из тетраэдров, где на один атом Si приходится четыре атома O, в зависимости от того, как они комбинируются между собой, выделяют такие виды силикатов:
- островные;
- поясные;
- цепочные;
- каркасные;
- листовые.
Островные
Островные силикаты – это наиболее многочисленные представители класса. Их решетки представляют собой изолированные тетраэдры или группы тетраэдров, в которых атомы кислорода не пересекаются или практически не пересекаются. Связь между двумя разными тетраэдрами (или двумя группами) происходит через катионы, а атомы кислорода у них не могут быть общими.
Как правило, это светлые или бесцветные минералы, с плотной структурой, благодаря чему они обладают большим удельным весом. Их состав нередко включает катионы железа, магния, тория, алюминия, ниобия, марганца и других металлов.
Минералы гранат, аквамарин, турмалин, топаз, изумруд, везувиан, хризолит – полудрагоценные и драгоценные камни. Их собирают в музейные и выставочное коллекции, используют в украшениях и декоративных поделках. Из распространенного недрагоценного минерала форстерита делают огнеупорные кирпичи. Циркон применяется как в ювелирном деле, так и для производства огнеупоров. Он также является источником циркония, гафния и урана.
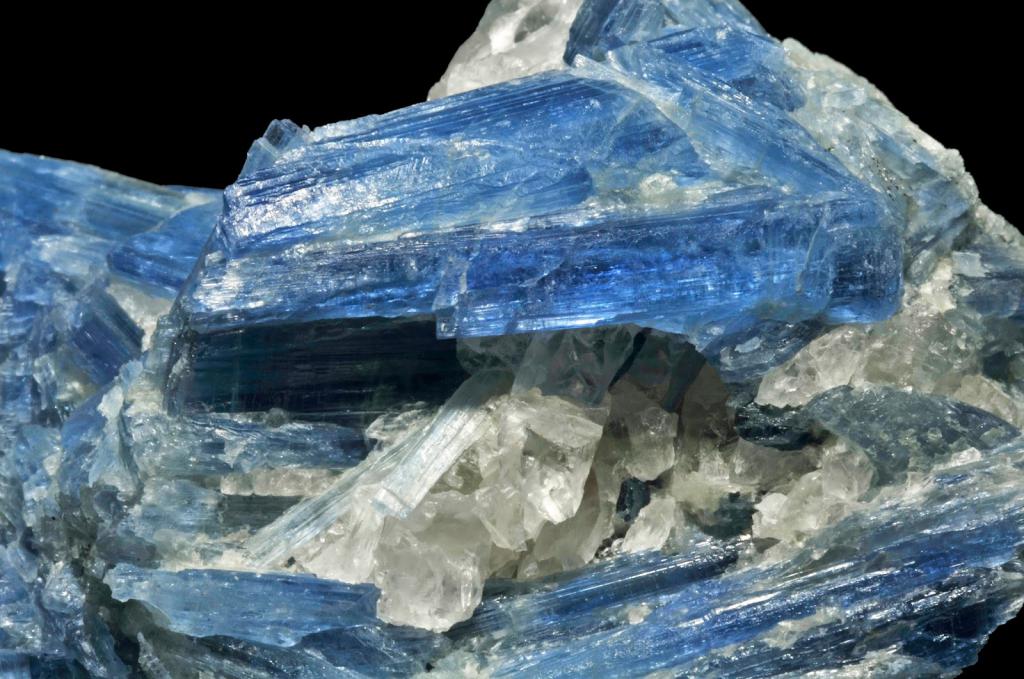
Поясные
Атомы поясных силикатов выстроены в длинные двойные ленты из обособленных тетраэдров. Благодаря такой структуре их также называют «ленточными». Они обладают меньшей плотностью, чем островные, но характеризуются более четкой спайностью.
Одним из распространенных представителей группы является роговая обманка, состоящая из магния, железа и алюмосиликата кальция. Сюда относятся различные амфиболовые минералы, например, антофиллит, куммингтонит, грюнерит, тремолит.

Цепочечные
К этому виду относятся представители большой группы пироксенов, такие как жадеит, энстатит, авгит, эгрин. Цепочечные имеют много общего с группой ленточных силикатов. Они тоже обладают средней плотностью и хорошо заметной спайностью. Их кристаллическая структура имеет вид тетраэдров, соединенных друг с другом в длинные непрерывные цепочки. Однако, в отличие от поясных силикатов, их цепочки не двойные.

Листовые
Структура листовых силикатов представляет собой сетки тетраэдров из кремния и кислорода, которые чередуются с плоскими сетками катионов, образуя слои. Их цвет определяется наличием окрашивающих элементов, без которых они являются белыми или бесцветными. С двухвалентным железом в составе они приобретают различные зеленые оттенки, с одновалентным – становятся коричневыми, бурыми, зеленовато-черными. Марганец делает их розовыми или сиреневыми, алюминий – оранжевыми или рыжеватыми.

Слоистая структура характерна для талька, асбеста, каолинита, мурманита, серпентина, для различных слюд, таких как мусковит, биотит, лепидолит, флогопит. Они входят в состав глин, гнейсов, мергелей, пегматитов, сланцев, гранитов. Многие из них находятся в составе осадочных пород и магматических пород коры выветривания. Слоистые силикаты используются как диэлектрики в промышленности, а также в строительстве в виде смазочных, отделочных и огнеупорных строительных материалов.
Каркасные
Атомы каркасных силикатов выстраиваются в непрерывные трехмерные группы, в которых каждый атом кислорода принадлежит одновременно к двум тетраэдрам. В их структуре атомы кремния нередко заменяют алюминием, что привлекает в состав катионы других веществ. Этим обеспечивается их разнообразие.
К каркасным силикатам относят две большие группы минералов: кварцы и полевые шпаты. К первым причисляют агат, кошачий глаз, соколиный глаз, авантюрин, розовый кварц, халцедон, горный хрусталь, аметист, оникс. К полевым шпатам относятся лунный камень, ортоклаз, альбит, лабрадор, битовнит, анортит.

Многие из них являются полудрагоценными камнями, из которых делают украшения и сувениры. В промышленности их используют для изготовления оптически приборов, различных стекол и керамики. Шпаты применяют при сварке, а также добавляют в зубные пасты в качестве абразивов.
www.syl.ru
Силикатные материалы и изделия
Силикатные, гипсовые и асбоцементные материалы относятся к безобжиговым изделиям и составляют значительную группу строительных материалов из искусственного камня.
Силикатный кирпич. Материалами для изготовления силикатного кирпича являются чистый кварцевый песок (92 — 95%), воздушная известь (5 — 8%) и вода (около 7%) . Кварцевый песок в производстве силикатного кирпича применяют немолотый или в виде смеси немолотого и молотого. Допускаются равномерно распределённые глинистые примеси в количестве не более 10%. При таком содержании они несколько повышают удобоукладываемость смеси. Крупные включения глины в песке не допускаются.
Силикатный
кирпич изготавливают путем прессования
смеси под давлением 15-20МПа с последующим
пропариванием в автоклаве под давлением
0,8МПа и температуре 174
Этот строительный материал по своей форме, размерам и основному назначению не отличаются от глиняного кирпича. Теплоизоляционные качества стен из силикатного и керамического кирпича практически равны, водо-, морозо- и огнестойкость меньше. Морозостойкость М рз -15циклов. Его нельзя использовать для кладки фундаментов, цоколей, наружных стен, помещений с высокой влажностью воздуха, а также для кладки печей. Себестоимость силикатного кирпича на 25…35% ниже, чем керамического.
Кроме силикатного кирпича таким же способом изготовляют золосиликатный (зольный) кирпич, в нём частично или целиком песок заменён золой топлива. Этот кирпич легче силикатного и имеет более низкую теплопроводность. По прочности и стойкости зольный кирпич уступает силикатному. Применяют зольный кирпич для возведения кладки стен зданий малой этажности (до трёх этажей), а также для стен верхних этажей многоэтажных зданий.
Крупноразмерные изделия из силикатного бетона. Силикатным бетоном называют затвердевшую в автоклаве уплотнённую смесь, состоящую из кварцевого песка (70 — 80%), молотого песка (8-15%) и молотой негашеной извести (6 — 10%). Из силикатного бетона маркой не ниже М-150, с применением тепловлажностной обработки в автоклаве, изготовляют крупные стеновые блоки внутренних несущих стен, панели перекрытий и несущих перегородок, ступени, плиты, балки. Элементы, работающие на изгиб, армируют стержнями и сетками.
Не рекомендуется применять плотные силикатобетонные изделия для фундаментов и других конструкций, работающих в условиях высокой влажности.
Минеральные вяжущие вещества
Минеральные вяжущие вещества получают путем обжига в печах природных каменных материалов (известняка гипса, ангидрита, доломита, магнезита). Куски полученные после обжига , путем помола превращаются в тонкий порошок. Чем меньше размер зерен после помола, тем выше активность вяжущего. Вяжущие вещества при смешивании с водой способны переходить из жидкого (тестообразного) в камневидное состояние.
Вяжущие вещества делятся на две группы:
Воздушные вяжущие вещества, способные твердеть и длительно сохранять свою прочность только на воздухе, во влажных условиях они снижают или теряют прочность .
Гидравлические вяжущие вещества, твердеют и длительно сохраняют свою прочность не только на воздухе, но и в воде. В отличии от воздушных они имеют более высокую прочность , поэтому шире применяются в строительстве.
К воздушным вяжущим веществам относятся: воздушная известь, гипсовые вяжущие, магнезиальные вяжущие и жидкое (растворимое) стекло. К гидравлическим вяжущим относятся: гидравлическая известь, романцемент, портландцемент и его разновидности.
Вяжущие вещества широко применяются в строительстве для изготовления строительных растворов, бетонов, бетонных и железобетонных изделий.
Кирпичная и каменная кладки, бетон были известны человечеству ещё в доисторические времена, до изобретения им вяжущих веществ. Взамен вяжущих применялось пластическое глиняное тесто, которое, высыхая, превращалось в камнеподобный материал. Так как между глиной и водой никаких химических реакций не протекает, то высохшая и окаменевшая глина под действием воды может снова размокнуть и потерять прочность и связанность. В сухом климате или в условиях, исключающих увлажнение, глиняное тесто и в настоящее время используется как заменитель вяжущих. В наше время глиняные растворы применяются при кладке печей и возведения стен зданий в сухом климате.
Воздушная известь. Строительную воздушную известь получают путем обжига при температуре 1000-1200оС известняков или других горных пород, содержащих углекислый кальций. На строительство известь поступает в виде кусков белого или серого цвета(комовая известь или кипелка). Негашеная известь химически соединяется с водой и образует гашеную (гидратную) известь. При гашении ограниченным количеством воды известь распадается, образуя тонкий порошок, называемый пушонкой. При большом количестве воды образуется известковое тесто. Известь применяют для приготовления строительных растворов, в производстве известково-пуццолановых вяжущих, для изготовления силикатного кирпича, силикатных и пеносиликатных изделий, шлакобетонных блоков, а также в качестве покрасочных составов. Существенный недостаток воздушной извести – невысокая прочность и малая стойкость во влажных условиях.
Строительный гипс (алебастр) получают путем обжига природного гипсового камня с последующим размолом в тонкий порошок. В зависимости от тонкости помола и прочности строительный гипс делится на три сорта марок 35, 45, 55. Строительный гипс применяют для изготовления стеновых панелей, плит и камней для внутренних перегородок зданий, сухой штукатурки, архитектурно-отделочных деталей. Гипсовые вяжущие вещества применяются в виде гипсового теста в кладочных и штукатурных растворах, бетонах, производстве теплоизоляционных материалов, искусственного мрамора и других декоративных изделий. По пределу прочности на сжатие гипсовые вяжущие вещества делятся на четыре марки: 50,100, 150,200 . При воздействии влаги прочность затвердевшего гипса значительно снижается , поэтому его применяют в помещениях с влажностью до 60%.
Maгнезиальные вяжущие. Различают два вида магнезиальных вяжущих — каустический магнезит и каустический доломит. Применяют магнезиальные вяжущие для изготовления бесшовных ксилолитовых полов, перегородочных плит, плит для облицовки стен, а также ступеней и теплоизоляционных изделий и т. п.
Растворимое (жидкое) стекло.
Портландцемент. Является важнейшим гидравлическим вяжущим веществом. Его выпуск составляет около 80% от выпуска всех вяжущих. Высокая прочность, способность быстро твердеть на воздухе и в воде, относительно низкая стоимость сделали портландцемент самым распространённым вяжущим. Его применяют для изготовления бетонных и железобетонных конструкций, для строительных растворов высокой прочности. Сырьем для портландцемента служат природные ископаемые – мергеля или смесь из 73% известняка, 25% глины, 2% гипса. Размолотое сырье обжигают и производят помол спекшейся смеси – клинкера в тонкий порошок. Порошок, затворенный водой, образует тесто, которое быстро твердеет в течение первых трех суток и твердение в основном заканчивается на 28 сутки, достигая марочной прочности. При благоприятных условиях прочность бетона на портландцементе продолжает возрастать и может в 2-3 раза превысить марочную (28-суточную). Нормальные условия твердения – это 15 оС и влажная атмосфера. При 0 оС и ниже тесто замерзает, и прочность не увеличивается. Прочность характеризуется маркой. Марку устанавливают по пределу прочности при изгибе и сжатии образцов в виде брусков из цементного раствора состава 1:3 с водой через 28 суток после изготовления. Выпускают портландцемент марок 300, 400, 500 и 600. Хранить цемент в сухом месте не более 6 месяцев. Портландцемент не рекомендуется применять для конструкций, которые будут подвергаться действию напора морской, минеральной или пресной воды.
studfile.net
Силикатные материалы | Новости в строительстве
Силикатные материалы на основе строительной извести при нормальных условиях твердения имеют малую прочность. Поэтому, в целях повышения их прочности проводят обработку насыщенным водяным паром при 70…100°С при атмосферном давлении (пропаривание) или искусственную карбонизацию.
Состав статьи:
1. Силикатные материалы автоклавного твердения.
2. Силикатный кирпич.
3. Известково-зольный и известково-шлаковый кирпичи.
4. Силикатный бетон
5. Крупноразмерные изделия из силикатного бетона.
Показатели прочности и долговечности силикатных материалов приобретают максимальные значения в условиях гидротермальной обработки в автоклавах в среде насыщенного водяного пара. Гидротермальную обработку (запаривание ) проводят под давлением насыщенного водяного пара : 0,8; 1,2 и 1,6 МПа, что соответствует температурам указанной среды 174,5; 190,7 и 203,3°С.
Читать далее на http://stroivagon.ru строительная известь
Автоклавные строительные материалы выпускают в виде кирпича, блоков и панелей для наружных и внутренних стен, панелей перекрытий, колонн, лестничных маршей и площадок, балок и других изделий. Их свойства близки к свойствам цементных бетонов, но они отличаются меньшим расходом вяжущих, широким использованием дешевых местных заполнителей и следовательно меньшей стоимостью.
Однако для их производства необходимы автоклавы.
♣ Силикатный кирпич
Силикатный кирпич является одним из наиболее экономичных и распространенных в стране стеновых материалов, из него возводят более 16% всех каменных зданий.Основными видами сырья для производства силикатного кирпича являются песок, известь и вода. Кроме того, применяют суглинки, трепелы, золы, шлаки и другие горные породы и промышленные отходы.
В качестве известкового компонента для производства автоклавных изделий можно применять молотую не гашенную известь, пушонку, частично гашенную известь, а также известково зольное и известково-пуццолановое вяжущее. Производство силикатного кирпича включает следующие стадии:
добычу и просев песка, обжиг извести и ее размол совместно с частью песка, смешение полученного вяжущего с немолотым песком и водой. А также гашение извести в смеси с песком, повторное перемешивание и до увлажнение полученной массы, прессование кирпичей, их укладку на вагонетки, загрузку в автоклав и обработку насыщенным водяным паром при температуре 174,5°С (давлении 0,8 МПа).
Автоклавная обработка (запаривание ) силикатного кирпича производится по следующему режиму: Подъем температуры до 174,5°С-1,5 ч; изотермическая выдержка при 174,5°С-8 ч; снижение температуры до 100 °С и давления до атмосферного -2 ч.
Согласно ГОСТ 379-79, силикатный кирпич подразделяется на марки, которым соответствуют показатели предела прочности при сжатии : 30; 25; 20; 15; 12.5; 10 и 7.5 МПа ( последняя цифра только для пустотелых камней). Морозостойкость рядового силикатного кирпича должна составлять не менее 15 циклов попеременного замораживания ( при -13 °С ) и оттаивания ( в воде при 15…20 °С), а лицевого -25, 35, 50 циклов в зависимости от марки.
Водопоглощение рядового силикатного кирпича не должно превышать 16%, а лицевого -14%. Средняя плотность составляет 1800…1850 кг/м³. заводы выпускают рядовой и лицевой силикатный кирпичи, пустотелый и полнотелый, модульный (утолщенный) одинарный. Одинарный силикатный кирпич имеет ту же форму и размеры , что и красный керамический кирпич ( 250 х 120 х 65 мм). Модульный силикатный кирпич является пустотелым и имеет размер 250 х 120 х 88 мм.
Выпускаются также мелкоштучные силикатные изделия в виде пустотелых камней размером 250 х 120 х 138 мм. Такие изделия имеют массу не более 4,3 кг.
♣ Известково шлаковый и известково-зольный кирпичи.
Известково-шлаковый и известково-зольный кирпич является одним из разновидностью силикатного кирпича,который отличается лучшими теплоизоляционными показателями а также меньшей плотностью. Это достигается заменой тяжелого кварцевого песка на более легкий и пористым материалом на основе шлаков или золой.
Для того чтобы приготовить известково-шлаковый кирпич берут от 3 до 12 процентов извести и от 88 до 97 процентов шлака. Для производства известково- зольного кирпича используют от 75 до 80 процентов золы и от 20-25% извести. Зола как и шлак является дешевым сырьевым материалом и образуется при сжигании каменного или бурого угля в печах или при добывании электрической энергии путем сжигания топлива в котельных ТЭЦ и ГРЭС.
Экономически очень выгодно использование шлаков и зол, потому что таким образом расширяется сырьевая база используемых строительных материалов на основе силиката и при этом существенно снижается их стоимость. Производство известково-шлаковых кирпичей и соответственно известково-зольных не отличается от производства силикатного кирпича.
Шлаковый и зольный кирпич выпускаются предприятиями размерами 250 х 120 х 140 миллиметров и больше.Такой кирпич имеет марку прочности при сжатии М-75, 50, 25, плотностью от 1400-1600 кг/м3. Морозостойкость кирпича на уровне силикатного, теплопроводность должна быть в пределах 0.5-до 0.6 Вт/(м· °С).
Используют известково-шлаковый и известково-зольный кирпич преимущественно в качестве стенового материала в строительстве домов разного назначения, высотой до трех этажей.На основе извести также выпускают и силикатный бетон который получил также широкое использование в строительстве.
♣ Силикатный бетон
Силикатный бетон представляет собой бесцементный бетон автоклавного твердения. Вяжущим в нем является смесь извести с тонкомолотым песком. Наибольшее распространение получили мелкозернистые силикатные бетоны, заполнителем в которых является обычный кварцевый песок. Песок обладает более высокой удельной поверхностью, отсюда лучшая реакционная способность а также меньшая стоимость, чем крупного заполнителя.
Поэтому мелкозернистые силикатные бетоны наряду с хорошими техническими свойствами имеют низкую стоимость.Формуют силикатный бетон вибрированием, прессованием, прокатом, центрифугированием, литьем и так далее. Для крупноразмерных изделий чаще всего применяют вибрационное формование на виброплощадках и виброустановках.
Таблица-1. Требуемая жесткость силикатобетонной смеси
Вибрационное воздействие как правило характеризуется амплитудой колебаний 0,5…0,8 мм и частотой 2800…3000 кол/мин. Жесткость смеси необходимая для ее качественного уплотнения при различных способах формования, приведена в таблицу-1. При использование не гашенной извести ориентировочные значения прочности плотного силикатного бетона можно определить по формуле:
Rб=40,5[S м.п./1000+1,6/(Ц/В-1)]+180,где
S м.п.-удельная поверхность молотого песка, см²/г.
Изготовление силикатобетонных автоклавных изделий характеризуется сравнительно низким расходом извести: 175…250 кг на 1 м³ плотного бетона.Это объясняется тем, что вяжущим в условиях автоклавной обработки является не только известь, но и часть песка( в первую очередь молотого), входящего в состав цементирующих материалов -гидросиликатов кальция.
При гидротермальной обработке крупноразмерных изделий целесообразно применять автоклавы большего диаметра (2,6 и 3,6 метра), которые позволяют повысить коэффициент их заполнения. Крупноразмерные изделия из плотного силикатобетона имеют прочность на сжатие 15…40 МПа, среднюю плотность 1800…2100 кг/м³ и морозостойкость более 50 циклов попеременного замораживания и оттаивания.
Они могут применяться наряду с цементобетонными во всех случаях, кроме контакта с грунтовыми и сточными водами, содержащие углекислоту( вследствие образования растворимого бикарбоната кальция). На 20 предприятиях страны ежегодно выпускается более 500 тыс. м³ изделий из плотного силикатного бетона (ПСБ).
Основная номенклатура продукции из ПСБ: панели внутренних стен и сенажных траншей; плиты перекрытий; крупные стеновые блоки и блоки стен подвалов, тротуарные, дорожные и облицовочные плиты.
Читать далее на http://stroivagon.ru продолжение статьи-ячеистые бетоны
Крупноразмерные изделия из силикатного бетона
Силикатным бетоном называют затвердевшую в автоклаве уплотненную смесь, состоящую из кварцевого песка (70…80%),
молотого песка (8..15%) и молотой негашеной извести (6… 10%).Плотный силикатный бетон является разновидностью тяжелого бетона.
Силикатные бетоны, как и цементные, могут быть тяжелыми (заполнители плотные — песок и щебень или песчано-гравийная смесь),легкими (заполнители пористые — керамзит, вспученный перлит, аглопорит и
stroivagon.ru
Состав и свойства и Использование материала для строительства и облицовки фасада зданий +Фото и Видео
Силикатный кирпич в последнее время набирает все больших оборотов по популярности и востребованности на рынке строительных материалов.
Для его изготовления используют самые простые компоненты, а технология производства не отличается особой сложностью.
В связи с этим стоимость готовой продукции довольно приемлема, и это, скорее всего, и является залогом популярности материала.
Современный жилфонд, если брать за ориентир крайние 50 лет, практически на 4/5 всех построен из силикатного кирпича.
Общие сведения
Состав силикатного кирпича
Со времен начала производства данного строительного материала, его компонентный состав претерпел ничтожно мало изменений.
Итак, для его изготовления применяют:
- Шлам белитовый;
- Зола;
- Шлаковый песок;
- Смесь золы и шлака мелкофракционная;
- Окись хрома;
- Песок кварцевый – 80 – 90% от общей массы;
- Гашеная известь гидратированная 10 – 15%;
- Чистая вода – используется для придания смеси пластичности и ее увлажнения.
Классификация силикатного кирпича
Песчано-известковый – стандартный вид материала, состоит из 7 – 10% извести и 90 – 93% кварцевого песка;
- Шлаково-известковый – изготавливают при помощи замены кварца пористым шлаком в количестве 88 – 97% и 3 – 12% извести;
- Зольно-известковый имеет в составе 75 – 80% золы и 20 — 25% извести.
Размеры силикатного кирпича
Длина х ширина х толщина в мм:
- одинарный (О) 250 × 120 × 65 имеет массу 3,5 – 3,8 кг;
- уплотненный (У) 250 × 120 × 88 именуется также полуторным или модульным, обладает рифленой поверхностью, имеет массу до 4,3 кг.
С учетом сферы применения
Силикатный кирпич делится на:
- «Л» Лицевой используется для облицовки силикатным кирпичом стен строения, должен иметь идеальную поверхность без дефектов. Такой материал производят гладким, декоративным, с имитацией сколов, рельефным.
- «Р» Рядовой силикатный кирпич используется для кладки стен, после чего будет спрятан под облицовочными материалами, в связи с этим допустимо наличие сколов, трещин и шероховатостей на поверхности.
Преимущества силикатного кирпича
- Высокий уровень поглощения шума;
- Неподверженность образованию высолов;
- Морозоустойчивость;
- Вес готового здания на выходе получается небольшим, таким образом снижается нагрузка на основание дома;
- Долговечность и надежность;
- Экологичность;
- Широкий выбор разновидностей.
Недостатки силикатного кирпича
- Малые размеры кирпича требуют увеличения трудозатрат;
- По сравнению с керамическим кирпичом, устойчивость к низким температурам, влаге и открытому огню ниже.
- Материал нельзя применять для кладки печей, каминов, дымоходов, поскольку предельная температура использования составляет 500°C;
- Не походит для применения в помещениях с высоким уровнем важности.
Производство
Процесс изготовления силикатного кирпича подразумевает тщательное очищение компонентов смеси от различных примесей. Затем массу спрессовывают и формируют заготовку блока. Следующим этапом идет процесс обработки сырца в автоклаве, где к нему применяют повышенное давление и высокие температуры.
Эти действия направлены на образование в растворе силикатокальциевых соединений, делающих материал устойчивым к растворению в воде. Кроме того, повышается уровень прочности и понижается коэффициент теплового расширения. В течение суток силикатные блоки застывают полностью, и стают пригодными для использования.
Для того чтобы придать раствору пластичности и текучести, производители добавляют различные компоненты. Их действие направлено на вытеснение воздуха из пор, предотвращение расслоение раствора при обработке в автоклаве.
Технические характеристики состава и свойств силикатного кирпича
С учетом популярности силикатного кирпича в наших климатических зона, которые не отличаются теплотой в холодное время года, а тем более в северных регионах, остро стоит вопрос о придании материалу большей морозоустойчивости. Стоит отметить, что классический состав кирпича подразумевает выдержку циклов замораживания/размораживания – до 30. Добавления в состав полимерных компонентов дает возможность увеличит их до 50.
Использование особых растворов красителей на минеральной основе, которые отличаются устойчивостью к наличию щелочи в окружающей среде, дает возможность значительно расширить ассортимент силикатных блоков для строительства домов. Краситель применяют также при производстве белого силикатного кирпича.
Содержание в смеси белого кварца и извести, позволяет получить на выходе именно белые блоки. Но в процессе эксплуатации построенных домов из силикатного кирпича, материал поглощает пыль, а известь вымывается дождевыми водами и блоков. В результате кирпич приобретает сероватый неприглядный оттенок.
Поэтому, для того чтобы этого не случилось, производители подмешивают в состав окись титана. Именно это компонент позволяет силикатному кирпичу оставаться белым продолжительное время.
Дорогостоящие сорта силикатного кирпича от известных европейских производителей наделены абсолютной устойчивостью к ультрафиолету.
Связано это с тем, что в состав пластичной массы добавляют такие компоненты как:
- На 1 м3 смеси – максимум 5 кг портландцемента;
- На 1 м3 смеси – максимум 5 кг белого цемента из глинозема;
- 0,5 – 10 кг полимеров в виде порошка на основе винилароматического спирта и метакрилатов.
Данный состав кирпича белого силикатного полнотелого позволяет на протяжении нескольких десятилетий не терять изначального цвета и насыщенности оттенков.
Способность силикатных блоков сохранять тепло делают их весьма привлекательным материалом для строительства жилья. Самый простой по составу кирпич имеет довольно высокий процент теплопроводности. Примечательно, что с более высоким уровнем плотности материала, этот коэффициент понижается. Показатели КТ для стандартного силикатного кирпича составляют 0,55 Вт/ М х Со. Кладка силикатного кирпича обладает тенденцией к снижению этих показателей до 22 – 29%, в связи с повышенным содержанием цементного раствора в швах.
Благоприятный климат в домах из силикатного кирпича напрямую зависит от уровня паропроницаемости. Средний показатель находится на уровне 10 – 12 мг/м х ч х Па. Именно эти значения обеспечивают способность стен дышать, создавая условия проживания близкие к строениям из древесины.
Увеличить теплопроводимость силикатного кирпича можно при помощи некоторых способов:
- Добавление в состав компонентов, увеличивающих пористость материала, и уменьшающих тем самым его плотность;
- Формовка в блоках специально созданных пустот, которые понижают показатели проводимости тепла;
- Добавление гидрофобных компонентов и теплоизолирующее покрытие внешней поверхности силикатного кирпича.
Как видите, прочность силикатного блока напрямую зависит от его плотности, веса и устойчивости к воздействию внешней среды. Чем плотнее материал, тем выше показатели устойчивости к морозам, и ниже к поглощению влаги. Стандартный силикатный кирпич, имеющий класс плотности 1,6 – 1,8 способен абсорбировать от 10 до 14% воды, а свойства сохранять тепло снижаются на 30%.
Примечание. Некоторые виды силикатного кирпича производят из перекаленного керамзитного песка, который сам по себе имеет высокий уровень теплоизоляции, и кроме того, окрашивает материал в чудесный кофейный цвет.
Прочность и показатели поглощения воды у такого кирпича более низкие, нежели у стандартных видов, но для облицовочного материала это не играет особой роли.
Особенности состава для изготовления силикатного кирпича
Размер фракций кварцевого песка в значительной степени влияет на показатели прочности силикатного кирпича. Таким образом, мелкофракционный песок дает возможность получить на выходе плотный и прочный материал, который, к сожалению, не может похвастаться особой паропроницаемость, и не подойдет для строительства жилья, поскольку он не обладает способностью поглощать вяжущий раствор. Крупнофракционный песок просто необходимо добавлять в состав смеси в определённом количестве, для получения качественного продукта.
Примечание. Перед применением песок очищают от слюды и глины, вкраплений серы и органики.
Отдельно пунктом контроля над качеством смеси для производства силикатного кирпича является чистота извести. Допускается применение частично гашеной или негашеной извести. Но, зачастую применяют гидратную гашеную форму. Содержание окиси магния в смеси должно быть на уровне не больше 5 кг на 1/2 м3 извести.
Морозоустойчивость смеси повышают добавлением продуктов переработки отходов алюмощелочи. Показатели устойчивости к низким температурам повышается на 30 – 35%. Также, появляется возможность повысить уровень сохранения тепла на 10 – 12%.
Вес силикатного кирпича
Современный стандарт определяет семь классов плотности силикатного кирпича, от которой и зависит его вес. Легкие виды материала весят до 1000 кг/м3, самые тяжелые –2200 кг/м3. Кроме того, плотность материала определяет марку силикатного блока. Кирпич силикатный утолщенный применяют для строительства несущих конструкций многоэтажек, легкий блок походит для возведения стен. Силикатный пустотелый кирпич используют для теплоизоляции, а также в качестве облицовки стен.
Эксперты строительной сферы прогнозируют, что силикатный кирпич еще долгое время будет оставаться на пике популярности, поскольку аналогов пока не существует. Кроме того, развитие производственных технологий не стоит на месте, с каждым годом появляются улучшенные виды материала, более качественные и по сниженной цене.
ТОП 9 магазинов, где я выгодно закупаюсь
ТОП 7 по товарам и мебели для дома:
7 лучших строительных и мебельных магазинов!
- Akson.ru- это интернет-гипермаркет строительных и отделочных материалов!
- homex.ru- HomeX.ru предлагает большой выбор качественных отделочных, материалов, света и сантехники от лучших производителей с быстрой доставкой по Москве и России.
- Instrumtorg.ru – это интернет – магазин строительного, автомобильного, крепежного, режущего и другого инструмента, необходимого каждому мастеру.
- Qpstol.ru — «Купистол» стремится предоставить лучший сервис своим клиентам. 5 звёзд на ЯндексМаркет.
- Lifemebel.ru- гипермаркет мебели с оборотом более 50 000 000 в месяц!
- Ezakaz.ru- Представленная на сайте мебель изготавливается на собственной фабрике в Москве, а так же проверенными производителями из Китая, Индонезии, Малайзии и Тайваня.»
- Mebelion.ru- – крупнейший интернет-магазин по продаже мебели, светильников, интерьерного декора и других товаров для красивого и уютного дома.
domsdelat.ru
СИЛИКАТНЫЙ — это… Что такое СИЛИКАТНЫЙ?
Силикатный — Город: Липецк Административный округ города: Левобережный Координаты: Координаты … Википедия
силикатный — силикатовый Словарь русских синонимов. силикатный прил., кол во синонимов: 2 • армосиликатный (1) • … Словарь синонимов
силикатный — ая, ое. silicate m. Отн. к силикатам; связанный с производством силикатов. Силикатная промышленность. Силикатный завод. БАС 1. Под каменным силикатным поясом, наиболее глубоко залегающим членом является перидотовая или эклогиновая постель,… … Исторический словарь галлицизмов русского языка
силикатный — СИЛИКАТЫ, ов, ед. силикат, а, м. (спец.). Минералы, составляющие основную массу земной коры; промышленные материалы для изготовления цемента, стекла, огнеупоров, кирпича, керамики. Толковый словарь Ожегова. С.И. Ожегов, Н.Ю. Шведова. 1949 1992 … Толковый словарь Ожегова
Силикатный — прил. 1. соотн. с сущ. силикаты, связанный с ним 2. Свойственный силикатам, характерный для них. 3. Изготовленный из силикатов. Толковый словарь Ефремовой. Т. Ф. Ефремова. 2000 … Современный толковый словарь русского языка Ефремовой
силикатный — силикатный, силикатная, силикатное, силикатные, силикатного, силикатной, силикатного, силикатных, силикатному, силикатной, силикатному, силикатным, силикатный, силикатную, силикатное, силикатные, силикатного, силикатную, силикатное, силикатных,… … Формы слов
силикатный — силик атный … Русский орфографический словарь
силикатный — см. Силикаты … Энциклопедический словарь
Силикатный — 424910, Марий Эл Республики, г.Йошкар Ола … Населённые пункты и индексы России
Силикатный (2) — 431308, Мордовия Республики, Ковылкинского … Населённые пункты и индексы России
dic.academic.ru
Современный силикатный блок в качестве стенового материала
Поиски надёжного и эффективного, при этом удобного в работе и не отпугивающего своей ценой материала для строительства с переменным успехом велись всегда. Результат налицо — достижения современной строительной науки вдохнули новую жизнь в давно известный материал.
Новый взгляд на силикат
Строительство дома — серьёзный этап, требующий тщательного подхода в выборе надёжного и эффективного строительного материала. Поиски удобного и при этом доступного материала велись всегда. На сегодняшний день достижения современной строительной науки вдохнули новую жизнь в давно известный материал.
Продолжительное соперничество на строительном поприще двух классических конкурентов керамики и силиката до сих пор так и не выявило явного лидера. Силикатные блоки приобрели солидное преимущество за счет более доступной цены и высокой прочности.
Необходимо заметить, что не стоит путать силикатные блоки с газосиликатными. Это два строительных материала с абсолютно несравнимыми характеристиками. Газосиликат представляет собой пористый ячеистый бетон с достаточно низкими прочностными характеристиками.
Силикатный блок — материал с высокой прочностью, в состав которого входят природные компоненты: известь, песок и вода. Силикатный блок по праву можно назвать природным камнем. Высокая марка прочности (М150-200) позволяет использовать силикатный блок для строительства высотных жилых зданий, а так же для сооружения промышленных объектов, выдерживая при этом серьезную нагрузку.
Силикатный кирпич имеет такую же долгую историю создания, как и керамический. Но гораздо более драматическую. Известно, что в поисках более дешёвого и удобного, но столь же надёжного строительного материала, как природный камень, прошли столетия. Из глины в итоге получился керамический кирпич, а из песка и извести при добавлении связующего — силикатный. Первые силикатные кирпичи, хоть и уступали в прочности керамическим, были более дешёвыми в производстве. А потому их считали перспективными, и работа над улучшением характеристик силикатных материалов продолжалась весь XX век.
В малоэтажном строительстве силикатный блок завоевал лидирующие позиции и это вполне обоснованно. При строительстве коттеджей из силикатного блока отпадает необходимость в армопоясе, колоннах и балках, а это существенно экономит средства и время. Идеальная геометрия позволяет обойтись без дополнительного оштукатуривания, а стены из силикатного блока являются несущими. Из этого следует, что рассмотрение строительного материала детально, позволит сделать правильный выбор в строительной индустрии.
Силикатный блок — мировой строительный тренд
На сегодняшний день силикатный блок является одним из самых продаваемых строительных материалов в Европе. Залог такой популярности заключается в экономических, технических и экологических преимуществах. Силикатный блок включает бесспорное преимущество в идеально ровной поверхности, высокой прочности, безусадочности а так же высокой тепло и звукоизоляции.
Обращая внимание на ценовую политику строительных материалов, силикатный блок является доступным для массового потребления. Экономический фактор отвечает новому формату силикатных изделий. Силикатный блок является среднеформатным, весом в 18 кг каждый с системой паз-гребень позволяют резко снизить количество швов, минуя «мостики холода» и серьезно упростив процесс самой кладки.
Безупречные геометрические размеры позволяют производить кладку на специальную клеевую смесь, а не на кладочный раствор. Современная торцовочная система паз-гребень обеспечивает плотное прилегание торцевых поверхностей блоков. Возможные перекосы при строительстве полностью исключаются- стена будет ровная. Без особых усилий с кладкой справится даже начинающий мастер.
Отсутствие необходимости закладки силовых поясов сокращает трудоёмкость работ и экономит время строительства, а значит вносит свою не малую лепту в снижении затрат. Идеальная геометрия как основа строительного материала обеспечивает экономию времени на дополнительное выравнивание стен и экономит затраты о общем бюджете строительства дома.
Всё вышеперечисленное не только экономит затраты на рабочие руки и вспомогательные материалы, но и за счёт размера блоков и толщины клеевого слоя доля кладочных швов в общей площади стен оказывается в пять раз ниже. Из этого следует, что теплопотери такой стены будут существенно ниже. Кладка попросту будет «теплее».
В разряд экономических достоинств необходимо добавить и то, что за счет хороших энергосберегающих характеристик, а значит, и меньшей толщины блока, площадь дома на том же фундаменте будет больше. С фундамента площадью в 100 м2 можно сэкономить порядка 6 м2, а это целая котельная или санузел. За счёт уменьшения толщины стен потребуется и существенно меньший объём блока для строительства.
С экологической стороны блоки преуспевают в своем развитии. При производстве силикатных блоков используются только природные, экологически чистые компоненты. Одна из составляющих силикатного блока — известь придаёт материалу бактерицидные свойства. Такие стены не подвержены губительному воздействию грибков и плесени.
Высокая удельная теплоемкость силикатного блока говорит о том, что стены хорошо аккумулируют тепло и компенсируют резкие перепады температур в помещениях, из-за чего в доме легче настроить оптимальный микроклимат. Иными словами в доме из силикатного блока летом прохладно, а зимой тепло.
Очень важно касательно характеристик, следует добавить, что стены из силикатного блока не дают усадки, чем не могут похвастаться другие строительные материалы. Высокая прочность на врыв анкера позволяет навешивать на стены тяжелые конструкции без всяких сомнений.
Развенчивание мифов о силикатном кирпиче
Силикатные строительные материалы в малоэтажном домостроении давно и успешно применяют во многих странах Западной Европы (Германии, Австрии, Швейцарии, Нидерландах) даже при возведении фундаментов, цоколей, подвалов и санузлов.
Ранее в ряде нормативных документов определялись ограничения на использование силикатного кирпича для кладки наружных стен подвалов или помещений с мокрым режимом эксплуатации. Данные положения отчасти были справедливы в отношении продукции 50-70 годов прошлого века. Сегодня силикатные технологии шагнули далеко вперёд. Усовершенствование технологий производства вызвало столь значительное повышение качества выпускаемых силикатных изделий, что на сегодняшний день такие кирпичи и блоки по своим эксплуатационным свойствам не уступают никакому другому строительному материалу.
Причём для снятия негативного отношения к силикатному кирпичу есть научное подтверждение. Опубликованные и находящиеся в общем доступе результаты испытаний силикатных материалов по стандартной методике исследования строительных материалов показывают, что автоклавный силикатный блок можно назвать водостойким материалом, способным длительное время сохранять при этом важнейшие качества (прочность и внешний вид).
При воздействии попеременных циклов увлажнения-высушивания (по крайней мере до 100 циклов). Из силикатного камня не только не вымывается основной связывающий компонент, гидросиликат кальция, но и происходит усиление взаимодействия песка и извести. Прочность таких блоков практически не меняется.
Проведённые исследования наглядно доказали и достаточную стойкость современных силикатных строительных материалов в горячей воде. Все без исключения испытываемые изделия после длительного (6-месячного) воздействия горячей воды по всем показателям соответствовали ГОСТ 379-2015. Таким образом, опасения по поводу воздействия горячей, ровно как и кипящей воды, абсолютно напрасны. Также подтверждены высокие результаты стойкости материалов к минерализованным грунтовым водам (в агрессивных средах солевых растворов).
Всё это обосновывает применение силикатных блоков при кладке наружных и внутренних стен подвалов, цоколей и фундаментов, в помещениях с влажным и мокрым режимом эксплуатации. Приведённые доводы показывают, что блок из силиката обрёл популярность у застройщиков вполне заслуженно. Настоящий «каменный дом» из такого строительного материала прослужит своим хозяевам многие десятки лет.
domidei.ru
Лекции / Силикатные изделия. Технология производства силикатных изделий автоклавного твердения
Технология пр-ва силикатных изделий автоклавного твердения
При смешивании возд извести с кварцевым песком и водой получают стр-ный р-р, который твердеет при обычных условиях очень медленно. Так как песок в обычных условиях химически инертен.
Силикатные бетоны, как и цементные, могут быть тяжелыми (заполнители плотные — песок и щебень или песчано-гравийная смесь), легкими (заполнители пористые — керамзит, вспученный перлит, аглопорит и др.) и ячеистыми (заполнителем служат пузырьки воздуха, равномерно распределенные в объеме изделия).
Вяжущим в силикатном бетоне является тонкомолотая известково-кремнеземистая смесь — известково-кремнеземистое вяжущее, способное при затворении водой в процессе тепловлаж-ностной обработки в автоклаве образовывать высокопрочный искусственный камень.
В качестве кремнеземистого компонента применяют молотый кварцевый песок, металлургические (главным образом доменные) шлаки, золы ТЭЦ. Кремнеземистый компонент (тонкомолотый песок) оказывает большое влияние на формирование свойств силикатных бетонов. Так, с возрастанием дисперсности частиц молотого песка повышаются прочность, морозостойкость и другие свойства силикатных материалов.
С увеличением тонкости помола песка повышается относительное содержание СаО в смеси вяжущего до тех пор, пока содержание активной СаО обеспечивает возможность связывания ее во время автоклавной обработки имеющимся песком в ннзкооснбвные гидросиликаты кальция.
Автоклавная обработка — последняя и самая важная стадИя производства силикатных изделий. В автоклаве происходи сложные процессы превращения исходной, уложенной и уплотненной силикатобетонной смеси в прочные изделия разной плотности,- формы и назначения. В настоящее время выпускаются автоклавы диаметром 2,6 и 3,6 м, длиной 20…30 и 40 м. Как изложено выше, автоклав представляет собой цилиндрический горизонтальный сварной сосуд (котел) с герметически закрывающимися с торцов сферическими крышками. Котел имеет манометр, показывающий давление пара, и предохранительный клапан, автоматически открывающийся при повышении в котле давления выше предельного. В нижней части автоклава уложены рельсы, по которым передвигаются загружаемые в автоклав вагонетки с изделиями. Автоклавы оборудованы траверсными путями с передаточными тележками — электромостами для загрузки и выгрузки вагонеток и устройствами для автоматического контроля и управления режимом автоклавной обработки. Для уменьшения теплопотерь в окружающее пространство поверхность автоклава и всех паропроводов покрывают слоем теплоизоляции. Применяют тупиковые или проходные автоклавы. Автоклавы оборудованы магистралями для выпуска насыщенного пара, перепуска отработавшего пара в другой автоклав, в атмосферу, утилизатор и для конденсатоотвода.
После загрузки автоклава крышку закрывают и в него медленно и равномерно впускают насыщенный пар. Автоклавная обработка является наиболее эффективным средством ускорения твердения бетона. Высокие температуры при наличии в обрабатываемом бетоне воды в капельно-жидком состоянии создают благоприятные условия для химического взаимодействия между гидратом оксида кальция и кремнеземом с образованием основного цементирующего вещества — гидросиликатов кальция.
Весь цикл автоклавной обработки (по данным проф. П. И. Бо-женова) условно делится на пять этапов: 1 —от начала впуска пара до установления в автоклаве температуры 100 °С; 2 — повышение температуры среды и давления пара до назначенного минимума; 3 — изотермическая выдержка при максимальном давлении и температуре; 4 — снижение давления до атмосферного, температуры до 100 °С; 5 — период постепенного остывания изделий от 100 до 18…20 °С либо в автоклаве, либо после выгрузки их из автоклава.
Прочность силикатного бетона при сжатии, изгибе и растяжении, деформативные свойства, сцепление с арматурой обеспечивают одинаковую несущую способность конструкций из силикатного и цементного бетона при одинаковых их размерах и степени армирования. Поэтому силикатный бетон можно использовать для армированных и предварительно напряженных конструкций, что ставит его в один ряд с цементным бетоном.
Из плотных силикатных бетонов изготовляют несущие конструкции для жилищного, промышленного и сельского строительства: панели внутренних стен и перекрытий, лестничные марши и площадки, балки, прогоны и колонны, карнизные плиты и т. д. В последнее время тяжелые силикатные бетоны применяют для изготовления таких высокопрочных изделий, как прессованный безасбестовый шифер, напряженно-армированные силикатобе-тонные железнодорожные шпалы, армированные силикатобетон-ные тюбинги для отделки туннелей метро и для шахтного строительства (бетон прочностью 60 МПа и более).
Коррозия арматуры в силикатном бетоне зависит от плотности бетона и условий службы конструкций; при нормальном режиме эксплуатации сооружений арматура в плотном силикатном бетоне не корродирует. При влажном и переменном режимах эксплуатации в конструкциях из плотного силикатного бетона арматуру необходимо защищать антикоррозионными обмазками.
Силикатный бетон на пористых заполнителях — новый вид легкого бетона. Твердение его происходит в автоклавах. Вяжу-Щие для этих бетонов применяют те же, что и для плотных силикатных бетонов, а заполнителями служат пористые заполнители: керамзит, вспученный перлит, аглопорит, шлаковая пемза
Силикатный кирпич
Силикатный кирпич по своей форме, размерам и основному назначению не отличается от керамического кирпича (см. гл. 3). Материалами для изготовления силикатного кирпича являются воздушная известь и кварцевый песок. Известь применяют в виде молотой негашеной, частично загашенной или гашеной гид-ратной. Известь должна характеризоваться быстрым гашением и не должна содержать более 5% MgO. Пережог замедляет скорость гашения извести и даже вызывает появление в изделиях трещин, вспучиваний и других дефектов, поэтому для производства автоклавных силикатных изделий известь не должна содержать пережога
. Кварцевый песок в производстве силикатных изделий применяют немолотый или в виде смеси немолотого и тонкомолотого, а также грубомолотого с содержанием кремнезема не менее 70%. Наличие примесей в песке отрицательно влияет на качество изделий: слюда понижает прочность, и ее содержание в песке не должно превышать 0,5%; органические примеси вызывают вспучивание и также понижают прочность; содержание в песке сернистых примесей ограничивается до 1 % в пересчете на SO3. Равномерно распределенные глинистые примеси допускаются в количестве не более 10%; они даже несколько повышают удобоукладываемость смеси. Крупные включения глины в песке не допускаются, так как снижают качество изделий. Состав известково-песчаной-смеси для изготовления силикатного Кирпича следующий: 92…95% чистого кварцевого песка, 5…8% воздушной извести и примерно 7% воды.
Производство силикатного кирпича ведут двумя способами: барабанным и силосным, — отличающимися приготовлением известково-песчаной смеси.
При барабанном способе (рис. 8. 6) песок и тонкомолотая Негашеная известь, получаемая измельчением в шаровой мельнице комовой извести, поступают в отдельные бункера над гасильным барабаном. Из бункеров песок, дозируемый по объему, а известь — по массе, периодически загружаются в гасильный барабан. Последний герметически закрывают и в течение 3…5 мин производят перемешивание сухих материалов. При подаче острого пара под давлением 0,15…0,2 МПа происходит гашение извести при непрерывно вращающемся барабане. Процесс гашения извести длится до 40 мин.
При силосном способе предварительно перемешанную и увлажненную массу направляют для гашения в силосы. Гашение в силосах происходит 7…12 ч, т.е. в 10…15 раз больше, чем в барабанах, что является существенным недостатком силосного способа. Хорошо загашенную в барабане или силосе известково-песчаную массу подают в лопастный смеситель или на бегуны для дополнительного увлажнения и перемешивания и далее на прессование. Прессование кирпича производят на механических прессах под давлением до 15…20 МПа, обеспечивающим получение плотного и прочного кирпича. Отформованный сырец укладывают на вагонетку, которую направляют в автоклав для твердения.
Автоклав представляет собой стальной цилиндр диаметром 2 м и более, длиной до 20 м, с торцов герметически закрывающийся крышками (рис. 8. 7). С повышением температуры ускоряется реакция между известью и песком, и при температуре 174 °С она протекает в течение 8… 10 ч. Быстрое твердение происходит не только при высокой температуре, до и высокой влажности, для этого в автоклав пускают пар давлением до 0,8 МПа и это давление выдерживают 6…8 ч. Давление пара поднимают и снижают в течение 1,5 ч. Цикл запаривания продолжает* 10… 14 ч. Я
Под действием высокой температуры и влажности происходи химическая реакция между известью и кремнеземом. Образующиеся в результате реакции гидросиликаты срастаются с зернами песка в прочный камень. Однако твердение силикатного кип. пича на этом не прекращается, а продолжается после запаривания. Часть извести, вступившей в химическое взаимодействие с кремнеземом песка, реагирует с углекислотой воздуха, образуя прочный углекислый кальций по уравнению
Са (ОН)2 + СО2 = СаСОз + Н2О
Силикатный кирпич выпускают размером 250 X 120Х 65 мм, марок 75, 100, 125, 150, 200, 250 и 300, водопоглощением 8… 16%,’ теплопроводностью 0,70…0,75 Вт/(м-°С), плотностью свыше 1650 кг/м3 — несколько выше, чем плотность керамического кирпича; морозостойкостью F15. Теплоизоляционные качества стен из силикатного кирпича и керамического практически равны.
Применяют силикатный кирпич так же, где и керамический, но с некоторыми ограничениями. Нельзя применять силикатный кирпич для кладки фундаментов и цоколей, так как ои менее водостоек, а также для кладки печей и дымовый труб, так как при длительном воздействии высокой температуры происходит дегидратация гидросиликата кальция и гидрата оксида, кальция, которые связывают зерна песка, и кирпич разрушается.
По технико-экономическим показателям силикатный кирпич превосходит керамический. На его производство требуется в 2 раза меньше топлива, в 3 раза меньше электроэнергии, в 2,5 раза меньше трудоемкости производства; в конечном итоге себестоимость силикатного кирпича оказывается на 25…35% ниже, чем керамического.
studfile.net