Таблица соответствия зернистости | Хамер
Таблица соответствия зернистости
Хамер | СтатьиПриведённая ниже таблица соответствия зернистости позволит не только перевести зёрна из стандарта ГОСТ в наиболее употребительный сейчас европейский стандарт FEPA, но и примерно подобрать необходимую зернистость абразива в зависимости от операции и обрабатываемого материала.
Назначение | Маркировка по ГОСТ 3647-80 (старый) | Маркировка по ГОСТ Р 52381-2005 (новый) | Маркировка по FEPA | Размер зерна, мкм | |
Металл | Дерево | ||||
Снятие шва, снятие фаски, большой съём металла | Очень грубые работы | 80-Н | Р24 | Р22 | 800-1000 |
63-Н | Р30 | Р24 | 630-800 | ||
50-Н | Р36 | Р36 | 500-630 | ||
Грубое шлифование, снятие металла, подготовка чёрного металла под покраску | Грубые работы | 40-Н | Р40 | Р40 | 400-500 |
32-Н | Р50-Р54 | Р50 | 315-400 | ||
25-Н | Р60 | Р60 | 250-315 | ||
20-Н | Р80 | Р80 | |||
Финишное шлифование | Первичная шлифовка | 16-Н | Р100 | Р100 | 160-200 |
12-Н | Р120 | Р120 | 125-160 | ||
10-Н | Р150 | Р150 | 100-125 | ||
Подготовка под полировку, сатинирование | Окончательная шлифовка мягких пород дерева, старой краски под покраску | 8-Н | Р180 | Р180 | 80-100 |
6-Н | Р220 | Р220 | 63-80 | ||
Окончательная шлифовка твердых пород дерева, шлифовка между покрытиями | 5-Н, М63 | Р240 – Р280 | Р240-Р280 | 50-63 | |
4-Н, М50 | Р320-Р360 | Р320-Р360 | 40-50 | ||
Подготовка под полировку, тонкое шлифование | Полировка финальных покрытий, шлифовка между покрасками, мокрая шлифовка | М40/Н-3 | Р400-Р500 | Р400-Р500 | 28-40 |
М28/Н-2 | М28 | Р600-Р800 | 20-28 | ||
Тонкое шлифование | Шлифовка пластиков, керамики, мокрая шлифовка | М20/Н-1 | М20 | Р1000 | 14-20 |
Ещё более тонкая шлифовка, полировка | М14 | М14 | Р1200 | 10-14 | |
М10/Н-0 | М10 | Р1500 | 7-10 | ||
М7/Н-01 | М7 | Р2000 | |||
М5/Н-00 | М5 | Р2500 | 3-5 | ||
*маркировка микропорошков в ГОСТ Р 52381-2005 не менялась *некоторые значения являются приблизительными |
Мы надеемся, что изложенная в статье информация была Вам полезна, однако для точного подбора абразивных инструментов под Ваши задачи в зависимости от материалов и серийности изделий мы рекомендуем обратиться за консультацией к нашим технологам.
При использовании материалов сайта ссылка на источник обязательна.
Таблица соответствия зернистости Fepa и ГОСТ
Таблица соответствия зернистости Fepa и ГОСТFEPA | ANSI | ГОСТ 3647-80 | 3M Trizact | Scotch-Brite | Размер, мкм |
Р24 | 24 | 80 | |||
Р36 | 36 | 50 | |||
Р40 | 40 | 40 | XCRS | ||
Р50 | 50 | 32 | XCRS | ||
Р60 | 60 | 25 | XCRS | 250 | |
Р80 | 80 | 16 | A300 | 180 | |
Р100 | 100 | 150 | |||
Р120 | 120 | 12 | A160 | CRS | 120 |
Р150 | 150 | 10 | A130 | CRS | 100 |
Р180 | 180 | 8 | A110 | 80 | |
A100 | MED | 70 | |||
Р220 | 6 | A90 | MED | ||
5 | MED | ||||
Р240 | 220 | M63 | 60 | ||
A85 | |||||
A75 | |||||
Р280 | 240 | M50 | A65 | FIN | 50 |
A60 | FIN | 45 | |||
Р320 | 280 | FIN / VFN | |||
Р360 | 320 | A45 | VFN | 40 | |
Р400 | M40 | A40 | SFN | ||
Р500 | 360 | SFN / UFN | |||
Р600 | M28 | A35 | 35 | ||
400 | A30 | XFN | 30 | ||
Р800 | A25 | XFN | |||
Р1000 | 500 | M20 | A20 | 20 | |
600 | A16 | 15 | |||
Р1200 | 800 | M14 | |||
P1500 | 1000 | M10 | 12 | ||
P2000 | 1200 | M7 | 9 | ||
P2500 | M5 | A6 | 5 |
| Адрес этой страницы (вложенность) в справочнике dpva.ru: главная страница / / Техническая информация / / Материалы / / Абразивы — зернистость, мелкость, шлифовальное оборудование. Шкурка, шлифовальная наждачная бумага, шлифовальные пасты, шлифовальные круги, мелкость абразива. / / Обозначения зернистости абразива по международному ИСО (ISO8486-1,2 ISO 6344-1,2) и российскому стандарту ГОСТ 3647, кроме алмаза и нитрида бора. Таблица соответствия абразивов, мелкости шкурки, кругов, паст. Поделиться:
|
Соответствие размера абразивного зерна ГОСТ и FEPA
- Главная
- Информация
- Соответствие размера абразивного зерна в ГОСТ и FEPA
В таблице приведены размеры абразивного зерна в стандарте ГОСТ и FEPA, а так же рекомендованная скорость шлифования материалов абразивными инструментами из шлифовальной шкурки. Обращаем Ваше внимание, что размер зерна в стандарте FEPA для абразивных материалов и инструментов на гибкой основе маркируется буквой P.
Таблица соответствия размера абразивного зерна в стандарте ГОСТ и FEPA
В РФ в настоящее время действует ГОСТ Р 52381-2005 вступивший 01.07.2006 г., который распространяется на шлифовальные порошки из искусственных или природных абразивных материалов для изготовления абразивного инструмента, в том числе абразивного инструмента на гибкой основе, а так же для использования шлифовальных порошков при обработке свободным абразивным зерном.
Размеры абразивного зерна
Соответствие стандартов размеров абразивного зерна шлифовальной шкурки | ||||
Размер зерна FEPA | Размер зерна ГОСТ P52381-2005 | Размер зерна ГОСТ 3647-80 | Средний размер зерна в Мкн | Примечание |
---|---|---|---|---|
P12 | P12 | 160 | 1815 | |
P16 | P16 | 125 | 1324 | |
P20 | P20 | 100 | 1000 | |
P22 | P24 | 80 | 800 | |
P24 | P30 | 63 | 764 | |
P30 | — | 642 | ||
P36 | P36 | 50 | 538 | |
P40 | 40 | 425 | ||
P50 | P50 | 32 | 336 | |
P60 | P60 | 25 | 269 | |
P80 | P80 (примерно) | 20 | 201 | |
P100 | P100 | 16 | 162 | |
P120 | P120 | 12 | 125 | |
P150 | P150 | 10 | 100 | |
P180 | P180 | 8 | 82 | |
P220 | P220 | 6 | 68 | |
P240 | М63 | 58,2 | ||
P280 | 52,2 | |||
P320 | М50 | 46,2 | ||
P360 | 40,5 | |||
P400 | P400 | М40 | 35 | |
P500 | P500 | 30,2 | ||
P600 | М28 | 25,8 | ||
P800 | 21,8 | |||
P1000 | М20 | 18,3 | ||
P1200 | 15,3 | |||
P1500 | М14 | 12,6 | ||
P2000 | 10,3 | |||
P2500 | М10 | 8,4 |
Переводные данные являются по некоторым позициям приблизительными.
Рекомендуемая скорость шлифования в м/с для абразивных инструментов из шлифовальной шкурки
Обрабатываемый материал | Миним. м/с | Макс. м/с |
---|---|---|
Титан | 5 | 15 |
Твердые металлы | 8 | 14 |
Нержавеющая сталь | 20 | 30 |
Углеродистое железо | 30 | 38 |
Чугун | 34 | 36 |
Алюминий | 35 | 45 |
Латунь | 35 | 45 |
Медь | 35 | 40 |
Сухая твердая древесина | 15 | 20 |
МДФ | 15 | 20 |
Мягкая смолистая древесина | 12 | 18 |
Лаки | 10 | 15 |
Композиты | 8 | 20 |
Резина | 15 | 25 |
Кожа | 10 | 15 |
Стекло | 12 | 18 |
Фарфор | 12 | 20 |
Для того, чтобы подобрать абразивные инструменты из шлифовальной шкурки нужного размера зерна обратитесь в офис компании Абразивкомплект.
Перевод зернистости абразивного материала из русской системы в международную
Перевод зернистости абразивного материала из русской системы в международную
ГОСТ 3647-80 |
FEPA F |
FEPA P ГОСТ 52381-2005 |
100 | F20 | P20 |
80 | F22, F24 | P24 |
63 | F30 | P30 |
50 | F36 | P36 |
40 | F40, F46 | P40 |
32 | F54 | P50 |
25 | F60 | P60 |
20 | F70 | — |
16 | F80, F90 | P80 |
12 | F100 | P100 |
10 | F120 | P120 |
8 | F150 | P150 |
6 | F180 | P180 |
5 | F220 | P220 |
4 | F240, F280 | P320, P360 |
M63 | F230 | P240, P280 |
M50 | F240 | P320, P360 |
M40 | F320 | P400, P500 |
M28 | P600, P800 | |
M20 | P1000, P1200 | |
M14 | P1500 | |
M10 | P2000 | |
M7 | P2500 |
FEPA | ANSI | ГОСТ 3647-80 | ЗМ Trizact | Scotch-Brite | Размер, мкм |
P24 | 24 | 80 | |||
P36 | 36 | 50 | XCRS | ||
P40 | 40 | 40 | XCRS | ||
P50 | 50 | 32 | XCRS | ||
P60 | 60 | 25 | XCRS | 250 | |
P80 | 80 | 16 | A300 | 180 | |
P100 | 100 | A200 | 150 | ||
P120 | 120 | 12 | A160 | CRS | 120 |
P150 | 150 | 10 | A130 | CRS | 100 |
P180 | 180 | 8 | A110 | 80 | |
A100 | MED | 70 | |||
P220 | 6 | A90 | MED | ||
5 | MED | ||||
P240 | 220 | M63 | 60 | ||
A85 | |||||
A75 | |||||
P280 | 240 | M50 | A65 | FIN | 50 |
A60 | FIN | 45 | |||
P320 | 280 | FIN/VFN | |||
P360 | 320 | A45 | VFN | 40 | |
P400 | M40 | A40 | SFN | ||
P500 | 360 | SFN/UFN | |||
P600 | M28 | A35 | 35 | ||
400 | A30 | XFN | 30 | ||
P800 | A25 | XFN | |||
P1000 | 500 | M20 | A20 | 20 | |
600 | A16 | 15 | |||
P1200 | 800 | M14 | |||
P1500 | 1000 | M10 | 12 | ||
P2000 | 1200 | M7 | 9 | ||
P2500 | M5 | A6 | 5 |
Таблица зернистости шлифматериалов
Таблица зернистости шлифматериалов
Стандарт ГОСТ 52381-2005 | Стандарт FEPA 42Д | ||
зернистость | Размер зерен основной фракции, мкм | зернистость | Размер зерен основной фракции, мкм |
шлифзерно | |||
№200 | 2500-2000 | F10 | 2400-2000 |
№160 | 2000-1600 | F12 | 2000-1700 |
№125 | 1600-1250 | F14 | 1700-1400 |
— | — | F16 | 1400-1180 |
№100 | 1250-1000 | F20 | 1180-1000 |
№80 | 1000-800 | F24 | 850-710 |
№63 | 800-630 | F30 | 710-600 |
№50 | 630-500 | F36 | 600-500 |
— | — | F40 | 500-425 |
№40 | 500-400 | F46 | 425-325 |
№32 | 400-315 | F54 | 355-300 |
№25 | 315-250 | F60 | 300-250 |
№20 | 250-200 | F70 | 250-212 |
№16 | 200-160 | F80 | 212-180 |
— | — | F90 | 180-150 |
шлифпорошки | |||
№12 | 160-125 | F100 | 150-125 |
№10 | 125-100 | F120 | 125-106 |
№8 | 100-80 | F150 | 106-75 |
№6 | 80-63 | F180 | 90-75 |
№5 | 63-50 | F220 | 75-63 |
микрошлифпорошки | |||
М63 | 63-50 | F230 | 63-53 |
М50 | 50-40 | F240 | 53-44.![]() |
— | — | F280 | 44.5-36.5 |
М40 | 40-28 | F320 | 36.5-29.2 |
— | — | F360 | 29.2-22.8 |
М28 | 28-20 | F400 | 22.8-17.3 |
М20 | 20-14 | F500 | 17.3-12.8 |
М14 | 14-10 | F600 | 12.8-9.3 |
М10 | 10-7 | F800 | 9.3-6.5 |
М7 | 7-5 | F1000 | 6.5-4.5 |
М5 | 5-3 | F1200 | 4.5-3 |
М3 | 3-2 | — | — |
М2 | 2-1 | — | — |
М1 | 1-0 | — | — |
<< Назад в раздел
Зернистость шлифовальных кругов таблица
Шлифовальные и отрезные круги широко применяются для различных подготовительных работ как на производстве, так и в домашних условиях.
Важнейшей характеристикой при выборе инструмента является зернистость, правильно выбрать которую поможет специальная таблица зернистости кругов. Она позволяет точно расшифровать обозначение в соответствии с группой абразива.
Зернистость абразивных кругов
В зависимости от группы используемого материала, зернистость обозначается по разному:
- Шлифзерно, шлифпорошки – число означает наименьший размер зерен взятого в сотых долях мм.
- Группа «Микрошлифпорошки». Зернистость абразивных кругов этой группы состоит из литеры М с добавлением максимального размера зёрен в мкм.
- Шлифпорошки из алмаза – число представлено дробью, где числитель означает размер ячейки верхнего сита, а знаменатель – соответственно нижнего, взятого в мкм.
- Микропорошки из алмаза – обозначение зернистости в виде дроби, где в числителе указан максимальный размер зёрен, в знаменателе – минимальный.
- Группа глифзерно и шлифпорошки эльбора – обозначаются в зависимости от методов контроля.
Зернистость отрезных кругов
Выбирая зернистость отрезных кругов, следует учитывать, что чем крупнее зерно, тем выше режущая способность инструмента. При выборе инструмента следует оценивать соответствие толщины инструмента и размера зёрен. Более мелкие придают кругу стойкость, но снижают его режущую способность.
Зернистость отрезных кругов имеет свою классификацию:
- Крупная (F12-F16-F20-F22),
- Средняя (F30-F36-F40-F60),
- Мелкая (F70-F80-F100-F120).
Ниже представлены обобщённые данные обозначающие различную. Зернистость шлифовальных кругов. Таблица представляет собой информацию о зернистости групп материала по ГОСТ 3647-80 и стандарту ИСО 8486.
Зернистость шлифовальных кругов таблица
Группа абразивного материала | Обозначение зернистости(ГОСТ 3647-80) | Размер зерен, мкм | Обозначение постандарту ISO 8486 |
Шлифзерно | 200 | 2500.![]() |
10 |
160 | 2000…1600 | 12 | |
125 | 1600…1250 | 16(14) | |
100 | 1250…1000 | 20 | |
80 | 1000…800 | 22 | |
63 | 800…630 | 30 | |
50 | 630…500 | 36 | |
40 | 500…400 | 40 | |
32 | 400…315 | 54(46) | |
25 | 315…250 | 60 | |
20 | 250….200 | 70 | |
16 | 200…160 | 80 | |
Шлифпорошки | 12 | 160…125 | 100 |
10 | 125…100 | 120 | |
8 | 100…80 | 150(180) | |
6 | 80.![]() |
220 | |
5 | 63…50 | ||
4 | 50…40 | ||
Микрошлифпорошки | М63 | 63…50 | 230 |
М50 | 50…40 | 240 | |
М40 | 40…28 | 280 | |
М28 | 28…20 | 360 | |
М20 | 20…14 | 400 | |
М14 | 14…10 | 500 | |
Тонкие микрошлифпорошки | М10 | 10….7 | 600 |
M7 | 7….5 | 800 | |
М5 | 5….3 | 1000 | |
М3 | 3….2 | 1200 |
(PDF) Последние разработки в области измельчения передовых материалов
ізация скрытых слоев силицида на подложках SOI для приложений BICMOS-
. Microelectron Eng 82 (3–4): 454–459
27. Pietsch GJ, Kerstan M (2005) Понимание одновременного
Двухдисковое шлифование: принцип работы и удаление материала
кинематика планаризации кремниевых пластин. Precis Eng 29 (2): 189–196
28. Schoenfelder S, Ebert M, Landesberger C, Bock K, Bagdahn J
(2007) Исследования влияния техники нарезки кубиками на прочностные свойства тонкого кремния
.Microelectron Reliab 47
(2–3): 168–178
29. Венкатеш В.К., Изман С. (2007) Разработка нового алмазного шлифовального круга без связки
для обработки микросхем на отказ
анализ. J Mater Process Technol 185 (1–3): 31–37
30. Tani Y, Okuyama T, Murai S, Kamimura Y, Sato H (2007)
Разработка кругов из кремнеземного поливинилового спирта для мокрого зеркала
Шлифовка Кремниевая пластина. CIRP Annals — Manufacturing
Technology 56 (1): 361–364
31.Touge M, Watanabe J (2006) Ультратонкая обработка диэлектрических подложек
путем прецизионной абразивной обработки. CIRP
Annals — Manufacturing Technology 55 (1): 317–320
32. Джексон MJ, Khangar A, Chen X, Robinson GM, Venkatesh VC,
Dahotre NB (2007) Лазерная очистка и правка застеклованного шлифовального материала
колеса. J Mater Process Technol 185 (1–3): 17–23
33. Хосокава А., Уэда Т., Юноки Т. (2006) Лазерная правка металла
Алмазный круг на связке.CIRP Annals — Manufacturing Technology
55 (1): 329–332
34. Wang XY, Wu YB, Wang J, Xu WJ, Kato M (2005) Поглощенная энергия
при лазерной обработке небольшого шлифовального круга из керамического CBN . J
Mater Process Technol 164–165: 1128–1133
35. Харимкар С.П., Дахотре Н.Б. (2006) Эволюция морфологии поверхности
в материалах шлифовальных кругов из оксида алюминия, обработанных лазером. Международный
Журнал прикладной керамической технологии 3 (5): 375–381
36.Хангар А.А., Кеник Е.А., Дахотре Н.Б. (2005) Микроструктура и микроструктура
в материале шлифовального круга из оксида алюминия, обработанного лазером.
Ceram Int 31 (4): 621–629
37. Чен В.К., Куриягава Т., Хуанг Х., Йосихара Н. (2005)
Обработка микросферических вставок форм. Precis Eng 29
(3): 315–323
38. Hwang Y, Kuriyagawa T., Lee SK (2006) Создание кривой круга
Ошибкаасферического микрошлифования при параллельном методе шлифования. Int J
Mach Tools Manuf 46 (15): 1929–1933
39.Алвес С.М., де Оливейра Дж.Ф.Г. (2006) Разработка новой смазочно-охлаждающей жидкости
для регулирования механических характеристик процесса шлифования и воздействия на окружающую среду
. J Mater Process Technol 179 (1–3): 185–189
40. Oliveira JFG, Alves SM (2006) Разработка экологически безопасной жидкости
для измельчения CBN. CIRP Annals — Manufacturing
Technology 55 (1): 343–346
41. Gao Y, Lai H (2007) Влияние активно охлаждаемой охлаждающей жидкости на шлифование пластичных материалов
.Key Eng Mater 339: 427–433
42. Gao Y, Lai H (2008) Использование активно охлаждаемой и активированной СОЖ
для улучшения качества поверхности при шлифовании пластичных материалов. Int J
Mater Prod Technol 31 (1): 14–26
43. Irani RA, Bauer RJ, Warkentin A (2007) Разработка новой системы подачи смазочно-охлаждающей жидкости
для глубинного шлифования. Int J Manuf
Technol Manag 12 (1–3): 108–126
44. Catai RE, Bianchi EC, Zilio FM, De Valarelli ID, Alves MCDS,
Silva LR, De Aguiar PR (2006) Глобальный анализ аэродинамики
Эффективность дефлекторов в процессе шлифования.Журнал
Бразильское общество механических наук и инженерии 28
(2): 140–145
45. Salonitis K, Chryssolouris G (2007) Охлаждение при затвердевании
операций. Int J Adv Manuf Technol 33 (3–4): 285–297
46. Li J, Li JCM (2005) Распределение температуры в заготовке во время
царапания и шлифования. Материаловедение и инженерия A 409
(1–2): 108–119
47. Cheng HB, Feng ZJ, Cheng K, Wang YW (2005) Дизайн высокоточного станка с шестью осями
и его применение в обработке
асферических оптических зеркал. Int J Mach Tools Manuf 45 (9): 1085–
1094
48. Инь Л., Пикеринг Дж. П., Рамеш К., Хуанг Х., Spowage AC,
Vancoille EYJ (2005) Плоское наношлифование мелкозернистого материала
WC -Co композит для оптической обработки поверхности. Int J Adv Manuf
Technol 26 (7–8): 766–773
49. Zhong ZW, Peng ZF (2007) Структуры фрактальной шероховатости
стальных стержней с прецизионным покрытием из WC-Co и Inconel 625.
Int J Adv Manuf Technol 33 (9–10): 885–890
50.Wu Y, Fan Y, Kato M (2006) Технико-экономическое обоснование микромасштабного изготовления
с помощью бесцентрового шлифования с помощью ультразвукового башмака. Precis Eng 30
(2): 201–210
51. Чжун З.В., Жуй З.Й. (2005) Измельчение монокристаллического кремния
с использованием микровибрационного устройства. Mater Manuf Process 20 (4): 687–
696
52. Egana I, Mendikute A, Urionaguena X, Alberdi R (2006) На пути к
умной одежде. IEEE Instrum Meas Mag 9 (3): 38–43
53. Brinksmeier E, Heinzel C, Meyer L (2005) Разработка и применение
системы мониторинга процесса шлифования на основе круга.
CIRP Annals — Manufacturing Technology 54 (1): 301–304
54. Su JC, Tarng YS (2006) Измерение износа шлифовального круга
с помощью машинного зрения. Int J Adv Manuf Technol 31 (1–2): 50–60
55. Zhang X, Krewet C, Kuhlenkötter B (2006) Автоматическая классификация
Катион дефектов на поверхности продукта при шлифовании и полировке.
Int J Mach Tools Manuf 46 (1): 59–69
56. Xie J, Tamaki J (2006) Оценка выступа зерен
в процессе обработки алмазного шлифовального круга с помощью электроконтакта
разрядная повязка.J Mater Process Technol 180 (1–3): 83–90
57. Tian YL, Zhang DW, Yan B (2007) Анализ статических характеристик
стола с микропозиционированием с 3 степенями свободы для шлифования. Key Eng Mater
339: 177–182
58. Tian YL, Zhang DW, Chen HW (2006) Динамическое моделирование нового стола с микропозиционированием
с 3 степенями свободы для контроля плоского шлифования.
Key Eng Mater 304–305: 507–511
59. Zhang D, Chetwynd DG, Liu X, Tian Y (2006) Исследование стола с микропозиционированием
3-DOF для плоского шлифования.Int J Mech
Sci 48 (12): 1401–1408
60. Tian YL, Zhang DW, Yan B (2007) Исследование производительности
стола с микропозиционированием. Данные о диффузии и дефектах Pt.B: Solid
State Phencies 121–123: 1285–1288
61. Tian Y, Zhang D, Chen H, Huang T (2005) Моделирование прецизионного процесса шлифования
на основе микропозиционирования таблица и ошибка
технология компенсации. Цзиси Гунчэн Сюэбао / китайский
Журнал машиностроения 41 (4): 168–173
62.Тиан И, Чжан Д., Ян Б. (2006) Динамика и управление шлифовальным станком
с микропозиционным столом заготовки. Trans Tianjin
Univ 12 (3): 157–162
63. Tian YL, Zhang DW, Yan B (2006) Кинематические характеристики стола с микропозиционированием
с 3 степенями свободы для точного шлифования. Tianjin
Daxue Xuebao (Ziran Kexue yu Gongcheng Jishu Ban) / Journal of
Тяньцзиньский университет науки и технологий 39 (7): 777–782
64. Ли Т.С., Тин ТО, Линь Ю.Дж., Хтай Т. (2007) A рой частиц
подход к анализу оптимизации процесса измельчения.Int J Adv
Manuf Technol 33 (11–12): 1128–1135
65. Алагумурти Н., Паланираджа К., Саундарараджан В. (2007) Тепло
Генерация и теплопередача в процессе цилиндрического шлифования — численное исследование
. Int J Adv Manuf Technol 34 (5–6): 474–482
66. Кришна А.Г., Рао К.М. (2006) Многоцелевая оптимизация операций плоского шлифования
с использованием метода точечного поиска. Int J
Adv Manuf Technol 29 (5): 475–480
67. Kruszynski BW, Lajmert P (2005) Интеллектуальная система контроля
для шлифования с поперечным шлифованием. CIRP Annals — Manufacturing
Technology 54 (1): 305–308
68. Лю Кью, Чен Х, Джинди Н. (2007) Оценка суперабразивных кругов Al2O3 и
при шлифовании сплавов на основе никеля. Int J Adv
Manuf Technol 33 (9–10): 940–951
Int J Adv Manuf Technol (2009) 41: 468–480 479
(PDF) Многоцелевая оптимизация для шлифования стали AISI D2 с Al2O3 колесо под MQL
Материалы 2018,11, 2269 19 из 20
33.
Эмами, М.; Садеги, M.H .; Сархан, A.A.D. Исследование влияния распыления и подачи жидкости
параметров минимального количества смазки на процесс измельчения Al
2
O
3
инженерной керамики.
J. Manuf. Процесс. 2013, 15, 374–388. [CrossRef]
34.
Emami, M .; Садеги, M.H .; Сархан, A.A.D .; Хасани, Ф. Исследование минимального количества смазки при измельчении
инженерной керамики Al2O3.J. Clean. Prod. 2014,66, 632–643. [CrossRef]
35.
Chen, J .; Shen, J . ; Huang, H .; Xu, X. Характеристики шлифования при высокоскоростном шлифовании инженерной керамики
с паяными алмазными кругами. J. Mater. Процесс. Technol. 2010, 210, 899–906. [CrossRef]
36.
Prabhu, S .; Винаягам, Б. АСМ-исследование в процессе измельчения с использованием наножидкостей с использованием анализа Тагучи.
Внутр. J. Adv. Manuf. Technol. 2012,60, 149–160. [CrossRef]
37.
Sanchez, J.A .; Помбо, I .; Альберди, Р .; Искьердо, В .; Ортега, Н .; Plaza, S .; Martinez-Toledano, J. Machining
оценка гибридной технологии измельчения MQL-CO2. J. Clean. Prod. 2010, 18, 1840–1849. [CrossRef]
38.
Zhang, D .; Li, C .; Jia, D .; Zhang, Y .; Чжан, X. Удельная энергия шлифования и шероховатость поверхности наночастиц
Смазка струей при шлифовании минимальным количеством струи. Подбородок. J. Aeronaut. 2015,28, 570–581. [CrossRef]
39.
Zhang, Y.; Li, C .; Jia, D .; Zhang, D .; Чжан, X. Экспериментальная оценка наночастиц MoS
2
в струйном измельчении MQL
с различными типами растительного масла в качестве базового масла. J. Clean. Prod. 2015, 87, 930–940. [CrossRef]
40.
Zhao, W .; Gong, L .; Ren, F .; Li, L .; Сюй, Q .; Хан, А. Экспериментальное исследование деформирования стружки титанового сплава Ti-6Al-4V
при криогенном резании. Int. J. Adv. Manuf. Technol. 2018,96, 4021–4027. [CrossRef]
41.
Sadeghi, M.H .; Haddad, M.J .; Tawakoli, T .; Эмами М. Минимальное количество смазки-MQL при шлифовании титанового сплава
Ti-6Al-4V. Int. J. Adv. Manuf. Technol. 2009, 44, 487–500. [CrossRef]
42.
Tawakoli, T .; Hadad, M.J .; Садеги, M.H .; Данеши, А .; Stöckert, S .; Rasifard, A. Экспериментальное исследование
влияния параметров заготовки и шлифования на минимальное количество смазки — шлифование MQL. Int. J.
Мах. Инструменты Manuf.2009, 49, 924–932. [CrossRef]
43.
Надольный, К .; Каплонек В. Влияние явлений износа шлифовальных кругов с золь-гель оксидом алюминия на образование стружки
при внутреннем цилиндрическом врезном шлифовании стали 100Cr6. Int. J. Adv. Manuf. Technol.
2016
, 87,
501–517. [CrossRef]
44.
Tawakoli, T .; Hadad, M.J .; Садеги, М. Исследование минимального количества смазки-MQL-шлифования закаленной стали
100Cr6 с использованием различных типов абразивных материалов и СОЖ.Int. J. Mach. Инструменты Manuf.
2010
,
50, 698–708. [CrossRef]
45.
Silva, L.R .; Bianchi, E.C .; Catai, R.E .; Fusse, R.Y .; França, T.V .; Агиар, П.Р. Исследование поведения минимальной оптовой смазки
— метод MQL в различных условиях смазки и охлаждения при шлифовании стали
ABNT 4340. J. Braz. Soc. Мех. Sci. Англ. 2005 г., 27, 192–199. [CrossRef]
46.
Alves, J.A.C .; Де Баррос Фернандес, У.; Да Силва, J.C.E .; Bianchi, E.C .; De Aguiar, P.R .; Да Силва, Э.Дж.
Применение метода минимального количества смазки (MQL) при врезном круглом шлифовании
. J. Braz. Soc. Мех. Sci. Англ. 2009,31, 1–4. [CrossRef]
47.
Oliveira, D.D.J .; Guermandi, L.G .; Bianchi, E.C .; Diniz, A.E .; De Aguiar, P.R .; Канарим, Р. Улучшение минимального количества смазки
при шлифовании CBN с использованием очистки круга сжатым воздухом. J. Mater.
Процесс.Technol. 2012, 212, 2559–2568. [CrossRef]
48.
Ne¸seli, S .; Asiltürk, I .; Челик, Л. Определение оптимального технологического параметра для шлифовальных операций с использованием робастного процесса
. J. Mech. Sci. Technol. 2012 г., 26, 3587–3595. [CrossRef]
49.
Pusavec, F .; Hamdi, H .; Kopac, J .; Джавахир, И. Целостность поверхности при криогенной обработке сплава
на основе никеля — Inconel 718. J. Mater. Процесс. Technol. 2011, 211, 773–783. [CrossRef]
50.
Rapeti, P .; Pasam, V.K .; Rao Gurram, K.M .; Ревуру, Р. Оценка эффективности смазочно-охлаждающих жидкостей на основе растительного масла
при механической обработке с использованием реляционного анализа серого — шаг к устойчивому производству.
J. Чистый. Prod. 2016, 172, 2862–2875. [CrossRef]
51.
Puri, A.B .; Банерджи, С. Оптимизация характеристик электрохимического измельчения с множественным откликом с помощью методологии
поверхности отклика. Int. J. Adv. Manuf. Technol.2013,64, 715–725. [CrossRef]
52.
Rabiei, F .; Rahimi, A.R .; Хадад, М.Дж. Повышение производительности экологически чистой техники MQL за счет использования гибридной наножидкости
и измельчения с ультразвуковой поддержкой. Int. J. Adv. Manuf. Technol.
2017
, 93, 1001–1015. [CrossRef]
53.
Монтгомери, округ Колумбия, Планирование и анализ экспериментов, 2-е изд .; Журнал Американской статистической ассоциации:
Феникс, Аризона, США, 2000; Том 16, стр.241–242.
54.
Ben Fathallah, B .; Бен Фредж, N .; Sidhom, H .; Braham, C .; Ичида, Ю. Влияние режима охлаждения абразивного типа и скорости периферийного шлифовального круга
на целостность шлифованной поверхности стали AISI D2. Int. J. Mach. Инструменты Manuf.
2009,49, 261–272. [CrossRef]
Определение характеристик поверхности аустенитной нержавеющей стали 304L после различных операций шлифования | Международный журнал машиностроения и материаловедения
Сила шлифования и измеренная температура поверхности
Влияние параметров шлифования на усилие шлифования и измеренную температуру поверхности сравнивается в таблице 2.Результаты показывают, что увеличение мощности станка увеличивает требуемое нормальное усилие шлифования. Было замечено, что применение смазки для шлифования снижает нормальное усилие шлифования со 100 до 40 Н, даже несмотря на то, что использовалась такая же мощность станка (60%). Подобный эффект также наблюдался в предыдущей работе нынешних авторов при шлифовании дуплексной нержавеющей стали 2304 (Zhou, Peng Ling, et al., 2016). Использование смазки во время операций шлифования может помочь сохранить остроту абразивного зерна, уменьшить трение между абразивным материалом и материалом детали и способствовать благоприятному режиму стружкообразования, тем самым уменьшив нормальное усилие (Paul and Chattopadhyay, 1996).
Как показано на рис. 3, температуры поверхности были измерены вблизи области контакта между материалом заготовки и шлифовальным кругом. Поскольку именно температура в зоне шлифования фактически влияет на свойства поверхности земли, а на измеренные значения температуры влияют условия поверхности, а также настройки инфракрасной камеры, приведенные здесь результаты используются только для указания тенденции изменение температуры для разных параметров измельчения.Шлифование на более высокой мощности станка значительно повысило температуру поверхности. Увеличение мощности станка напрямую увеличивало силу шлифования, и в результате более высокое трение между абразивом и материалом детали вызвало очевидное увеличение тепла шлифования. Несколько парадоксально было замечено, что шлифование с более тонкой конечной поверхностью (группа I) приводило к немного более высоким температурам поверхности. Наиболее правдоподобным объяснением этого является то, что более тонкая отделка добавляла больше этапов шлифовки и увеличивала общее время шлифования.Поскольку тепло, выделяемое на каждом этапе шлифования, накапливалось, наблюдалось небольшое повышение температуры поверхности. Однако мощность машины имеет гораздо большее влияние на температуру. Эффект охлаждения при смазке заметен, хотя температура, измеренная в условиях смазки, может быть температурой смазки, а не металлической поверхности; Смазка может эффективно уменьшить трение между абразивными зернами и заготовкой и помочь отвести тепло при шлифовании (Yao et al.2013). В целом, измеренная температура шлифовальной поверхности вблизи зоны шлифования в данном исследовании относительно низкая.
Измерение температуры во время операций шлифования с отображением измеренной площади, шлифовка 304L с размером абразивного зерна 180 #, 60% мощности станка и без использования шлифовальной смазки
Удаление металла
Расчетные результаты удаления металла при различных условиях шлифования, а также стандартные ошибки показаны на рис. 4. Удаление металла рассчитывается по следующему уравнению:
Сравнение съема металла при различных условиях шлифования. a Группа I, размерный эффект абразивного зерна. b Группа II, машинное силовое воздействие. c Группа III, эффект смазки при шлифовании
$$ {\ delta} _ {\ mathsf {metal} \ \ mathsf {remove}} = {\ delta} _ {\ mathsf {as} \ \ mathsf {доставлено} \ \ mathsf {material}} — {\ delta } _ {\ mathsf {после} \ \ mathsf {измельчение} \ \ mathsf {операция}} $$
(1)
где \ ({\ delta} _ {\ mathsf {metal} \ \ mathsf {remove}} \) — толщина снятого металла в результате различных операций шлифования.
$$ \ begin {array} {l} {\ дельта} _ {\ mathsf {как} \ \ mathsf {доставлен} \ \ mathsf {материал}} \ kern0.24em \ mathrm {is} \ \ mathrm {the} \ \ mathrm {толщина} \ \ mathrm {of} \ \ mathrm {as} \ \ mathrm {доставлен} \ \ mathrm {test} \ \ mathrm {coupon} \\ {} {\ delta} _ {\ mathsf {after} \ \ mathsf {измельчение} \ \ mathsf {operation}} \ kern0. 36em \ mathrm {is} \ \ mathrm {the} \ \ mathrm {толщина} \ \ mathrm {of} \ \ mathrm {test} \ \ mathrm {coupon} \ mathrm {s} \ \ mathrm {after} \ \ mathrm {разные} \ \ mathrm {измельчение} \ \ mathrm {operations} \ end {array} $ $
Здесь толщина тестовых образцов, как в состоянии поставки, так и в основном состоянии, представляет собой среднее значение из 24 измеренных значений толщины для каждой пластины; оценочные стандартные ошибки случайного пересечения рассчитываются с помощью модели смешанного эффекта (Cheng 2014), их можно интерпретировать как производственные ошибки, которые связаны только с изменением толщины листа, ошибка воспроизводимости была исключена.
Как показано на рис. 4а, абразивы с зернистостью 60 # и 180 # обладают хорошей способностью снимать металл. 28 мкм металла были зачищены с помощью абразива с зернистостью 60 #; и толщина еще 20 мкм была удалена путем добавления еще одной стадии процесса шлифования с использованием абразива с зернистостью 180 #. Однако абразивы с зернистостью 280 # и 400 # имеют относительно более низкую способность к удалению металла, они используются для обработки поверхности; Металл толщиной всего 8 мкм был отшлифован с использованием абразива с зернистостью 280 # в течение 5 минут плюс еще 5 минут шлифования абразивом с зернистостью 400 #.Мощность станка также оказывает большое влияние на качество съема металла. Как показано на рис. 4b, при использовании абразивов одного размера и одинаковых процедур шлифования максимальная скорость съема металла наблюдалась при промежуточной мощности (60%). Меньшая мощность машины (30%) давала удаление металла 25 мкм по сравнению с 48 мкм при 60%, при мощности 90% удаление металла упало до 34 мкм. Чем выше мощность станка, тем выше шлифовальное усилие. При шлифовании с меньшей мощностью станка (усилием шлифования) абразивные зерна скользят и трутся о поверхность материала вместо эффективной резки и вспашки.Использование более высокой мощности станка (шлифовального усилия) увеличивает трение между абразивом и поверхностью заготовки, а также износ абразивных зерен.
На рис. 4с показано значительное улучшение способности снимать металл за счет использования смазки для шлифования; удаленная толщина была увеличена более чем вдвое (с 48 мкм до 102 мкм) за счет использования смазки. Это можно объяснить тем фактом, что шлифовальная смазка может помочь уменьшить трение на контактных поверхностях, рассеивая тепло, сохраняя остроту абразивных зерен, тем самым обеспечивая благоприятный режим удаления металла (Manimaran et al.2014; Fredj et al. 2006 г.).
Шероховатость и топография шлифованной поверхности
В данном исследовании шероховатость поверхности была измерена с использованием обоих R a и R z значения. На рисунке 5 представлены результаты для различных размеров абразивного зерна (группа I), полосы ошибок на рисунке представляют собой стандартные отклонения, рассчитанные по пяти измерениям для каждого образца. Как показано на рисунке, оба R a и R z Значения уменьшаются за счет использования абразива с более мелкой зернистостью в качестве окончательной отделки поверхности. Для крупного (60 #) абразивного зерна размер R a значение 1,81 мкм и R z значение 18.4 мкм. Обе модели с более мелким зерном (180 #) R a и R z значения были уменьшены примерно до половины ( рэндов a = 0,77 мкм и R z = 10,66 мкм), а для мелкого зерна (400 #) — R a Значение уменьшилось до 0.
34 мкм и R z до 5,66 мкм.
Шероховатость поверхности по разной крупности абразива (группа I). a R a Фактор . б R z фактор
На рис. 6 представлены СЭМ-изображения, показывающие топографию поверхности и дефекты поверхности, возникшие в результате использования абразивного зерна разного размера (группа I).Глубокие канавки, смазывание, сколы и вмятины, показанные на рис. 6а, являются основными дефектами, наблюдаемыми на шлифованных поверхностях. Подобные дефекты также наблюдались при шлифовании дуплексной нержавеющей стали 2304 в предыдущей работе авторов (Zhou, Peng Ling, et al. , 2016). Образование таких дефектов связано с различным взаимодействием между шлифовальной зернистостью и поверхностью заготовки. Неравномерный процесс удаления металла, включая формирование стружки и вспашку, привел к образованию глубоких бороздок на шлифованных поверхностях.В зоне контакта между верхними частями абразивного зерна и поверхностью заготовки материал выталкивается и перемещается по поверхности, что приводит к размазыванию участков (Totten et al. 2002) в дополнение к образованию стружки. Процесс повторного осаждения (Терли и Дойл, 1975) привел к образованию сколов клея; материал был перенесен на зерно за счет адгезии, а затем был перенесен обратно на шлифованную поверхность сваркой трением. Трение между абразивным зерном или стружкой и поверхностью заготовки приводило к образованию вмятин.Как показано на рисунке, чистота поверхности была явно улучшена за счет использования абразивов с более мелким зерном. По сравнению с использованием абразива с зернистостью 60 # было ясно, что при использовании абразива с зернистостью 180 # были уменьшены глубокие канавки, большие пятна размазывания и сколы клея.
Дефекты поверхности были уменьшены еще больше за счет использования самого мелкого (400 #) зерна. Для всех трех образцов наблюдались вмятины на поверхности.
Рельеф поверхности и дефекты поверхности из-за разной крупности абразива (группа I). a 60 #. b 180 #. с 400 #
Размер абразивного зерна имеет большое влияние на шероховатость и чистоту поверхности, улучшение за счет использования абразива с меньшим размером зерна является значительным. Во время шлифования только небольшая верхняя область абразивных зерен эффективна для удаления металла, оставшаяся часть скользит и трется о материал заготовки (Sin et al. 1979). Абразивы с более крупной зернистостью имеют более крупные абразивные частицы, что приводит к появлению больших площадей трения во время шлифования; в то же время размер и распределение зерен абразивного зерна более неравномерное в абразивах с более крупными зернами; таким образом, при использовании абразивов с более крупными зернами было вызвано больше дефектов и худшее качество поверхности.
На рисунках 7 и 8 показано влияние мощности машины (группа II) на шероховатость поверхности земли и рельеф поверхности соответственно. По сравнению со шлифованием абразивами с разным размером зерна мощность станка гораздо меньше влияет на шероховатость шлифованной поверхности. Модель R a Значения , показанные на рис. 7, различались очень мало, хотя мощность машины была удвоена и утроена, в то время как R z Значения показывают некоторые вариации.Воздействие на топографию поверхности и дефекты поверхности различно; СЭМ-изображения (рис. 8) демонстрируют явное улучшение качества поверхности за счет увеличения мощности станка. Отшлифованная поверхность выглядела намного более гладкой, с меньшим количеством дефектов поверхности, когда мощность машины была увеличена до 90% (рис. 8c), хотя все еще наблюдалось множество небольших размытых участков. Нержавеющая сталь 304L обладает высокой прочностью и пластичностью (Outokumpu, 2013) и характеризовалась как «липкая», то есть каучуковая или клейкая во время обработки (Jang et al.1996). Более низкая мощность станка означает более низкое (нормальное) усилие шлифования, что привело к большему трению вместо эффективных процессов удаления металла, стружкодробления, резки или вспашки, как показано на рис. 4. Вместе с высокой адгезией материала на шлифовальной ленте образовывались большие пятна смазывания, а также сколы клея. Между тем, более высокая мощность станка означает более высокую направленную вниз силу, поэтому вместо того, чтобы разрезать, материал поверхности прижимался и скользил вдоль направления шлифования.В результате более высокая степень деформационного упрочнения шлифованной поверхности снижает эластичность или адгезию и улучшает чистоту поверхности после шлифования, хотя остается большое количество смазывающихся участков. Однако следует отметить, что влияние изменения мощности станка также зависит от свойств материала заготовки.
Например, в работе Чжоу и др. (Zhou, Peng Ling и др., 2016) по шлифованию дуплексной нержавеющей стали 2304 существует оптимальная мощность станка для шлифования, выше и ниже которой качество обработки поверхности ухудшается.
Шероховатость поверхности при разной мощности станка (группа II). a R a Фактор . б R z фактор
Рис. 8Рельеф поверхности и дефекты поверхности от различной мощности станка (группа II). a 30%. b 60%. с 90%
На рисунках 9 и 10 показано влияние шлифования со смазкой и без смазки (группа III) на шероховатость и топографию поверхности соответственно. Использование смазки во время шлифования позволяет значительно улучшить шероховатость и чистоту поверхности, как показано на рисунках. Оба R a и R z Значения снизились почти вдвое, при этом уменьшение дефектов шлифованной поверхности очень заметно.Это можно объяснить уменьшением трения при хорошей смазке, которая, в свою очередь, сохранила абразивную резкость и повысила более равномерное эффективное удаление металла. Между тем, снижение температуры поверхности во время шлифования со смазкой также снижает эластичность или адгезионные свойства материала и уменьшает повторное осаждение.
Шероховатость поверхности с / без использования шлифовальной смазки (группа III). a R a Фактор . б R z фактор
Рельеф поверхности и дефекты поверхности ( a ) без и ( b ) с использованием шлифовальной смазки (группа III)
Микроструктура поперечного сечения
Электронно-микроскопические изображения с обратным рассеянием, показывающие типичные микроструктуры поперечного сечения вблизи шлифовальных поверхностей при использовании абразивов с разным размером зерна (группа I), различной мощности станка (группа II) и мокрого / сухого шлифования (группа III). показанные на фиг.11, 12 и 13 соответственно. Для исследования развития микроструктуры использовались различные увеличения. На всех представленных изображениях направление шлифования перпендикулярно поперечному сечению образца. Подобные особенности наблюдались для всех образцов грунта, которые показаны на рис. 11а1, а2. В зависимости от используемых параметров шлифования вдоль шлифованных поверхностей наблюдались размазывания разного размера и количества, сколы клея или стружки холодной сварки с неразрешимой микроструктурой.Образуется сильно деформированный поверхностный слой, простирающийся до нескольких микрон от поверхности земли, за которым следует гораздо более толстый подповерхностный слой, демонстрирующий меньшую пластическую деформацию. Сильно деформированный поверхностный слой состоял из фрагментированных зерен и дислокационных субячеек. Такой поверхностный слой также наблюдался в других грунтовых материалах, например, в шлифованной дуплексной нержавеющей стали 2304 в работе нынешних авторов (Zhou, Peng Ling, et al., 2016). Подповерхностная область характеризуется полосами скольжения и контрастом деформации (разные оттенки серого) от пластической деформации.Рядом с поверхностным слоем наблюдались густонаселенные и деформированные полосы скольжения разной ориентации, а дальше полосы скольжения становились меньше и более прямыми по мере уменьшения степени пластической деформации.
Для всех исследованных образцов зона деформации, вызванная шлифованием, была намного меньше используемой абразивной зернистости.
Микроструктура поперечного сечения после использования абразивного зерна разной крупности (группа I). a 60 #. b 180 #. с 400 #
Фиг.12Микроструктура поперечного сечения, полученная в результате использования машин различной мощности (группа II). a 30%. b 60%. с 90%
Рис.13Микроструктура поперечного сечения ( a ) без и ( b ) с шлифовальной смазкой (группа III)
В соответствии с наблюдениями топографии поверхности в поперечном сечении с использованием абразива с зернистостью 60 # наблюдалось большое количество больших смазывающихся участков или сколов клея (рис. 11a1).Кроме того, были видны сколы холодной сварки с образованием микротрещин (рис. 11а2). Как количество, так и размер таких дефектов уменьшались при использовании абразивов с более мелким зерном (180 # и 400 #). Изображения на рис. 11 показывают, что размер абразивного зерна имеет большое влияние как на степень деформации, так и на глубину деформации. Шлифование абразивом зернистостью 60 # привело к появлению сильно деформированного поверхностного слоя толщиной 3–4 мкм с четкой фрагментированной зернистой структурой. Толщина сильно деформированного слоя была уменьшена почти вдвое при использовании 180 # и примерно до одной трети на 400 #.Между тем, грубое абразивное зерно (60 #) вызвало деформированный подповерхностный слой толщиной более 20 мкм. Толщина слоя, подверженного деформации, уменьшилась с 15 до 10 мкм при использовании абразивных зерен 180 # и 400 # соответственно. Как плотность полос скольжения, так и количество деформационных систем скольжения были уменьшены за счет использования абразивов с более мелким зерном, что опять же указывало на меньшую деформацию.
Низкая мощность станка (30%) привела к появлению большого количества небольших размазанных участков или сколов клея вдоль шлифовальной поверхности, что согласуется с результатами исследования топографии поверхности, в то время как образовалось очень мало сколов, полученных при холодной сварке.Как показано ранее, нормальное усилие шлифования было низким. В результате удаление металла стало менее эффективным; абразивные зерна скользили по поверхности материала, оставляя на шлифованной поверхности множество смазывающихся участков, а также сколов клея. С другой стороны, поскольку трение между абразивным материалом и материалом детали было низким, температура шлифования была низкой, и, таким образом, могло образоваться небольшое количество стружки при холодной сварке. В случае шлифования на 90% мощности станка выделялось больше тепла при шлифовании из-за повышенного трения при шлифовании, что способствовало образованию стружки при холодной сварке.Как показано на рис. 12, на котором представлены типичные микроструктуры поперечного сечения для различных мощностей обработки, толщины сильно деформированных поверхностных слоев одинаковы. В приповерхностной области образование полос скольжения показало, что интенсивность деформации и глубина деформации также аналогичны. Однако было обнаружено, что деформация очень неравномерна при шлифовании с использованием 30% мощности обработки. Как показано на рис. 12a1, a2, которые относятся к одному и тому же образцу, некоторые участки поверхности были сильно деформированы, в то время как на других деформация была очень небольшой.
Использование смазки для шлифования в значительной степени уменьшило образование смазывания, клейкой стружки и стружки при холодной сварке на шлифованной поверхности, что можно просто объяснить измеренным более низким нормальным усилием шлифования и более низкой температурой. Из изображений электронного каналирования, представленных на рис. 13, также очевидно уменьшение деформации; хотя толщина деформированного поверхностного слоя аналогична, деформация в подповерхностной области намного меньше. Как показано на рис. 13b, наблюдались полосы непрерывной деформации с несколькими полосами скольжения, образованными только в диапазоне нескольких микрон. Между тем, деформация оказалась более равномерной при использовании шлифовальной смазки.
Остаточные напряжения на поверхности земли
Метод полной ширины на половине высоты (FWHM) показывает уширение дифракционного пика, которое может быть связано с повышенной плотностью кристаллических дефектов в материале (Chen et al.2014). Здесь считается, что наблюдаемая разница в FWHM связана с различными деформациями поверхности в процессе шлифования. На рис. 14 показаны дифракционные пики, измеренные на поставляемой поверхности и на шлифованной поверхности с размером абразивного зерна 180 #, мощностью машины 60%, без использования смазки, соответственно.FHWM модели K 1 пик составляет 0,332 o для поверхности в состоянии поставки и 0,68 o для поверхности земли. Результаты FWHM для всех шлифованных поверхностей с различными параметрами шлифования, а также для материала в состоянии поставки представлены и сравниваются на рис. 15. Наблюдалось более низкое значение FWHM за счет использования более мелкозернистых абразивов или шлифовальной смазки (рис. 15a и c), что указывает на меньшую деформацию поверхности, вызванную этими операциями шлифования.С другой стороны, как показано на фиг. 15b, влияние мощности машины на деформацию поверхности относительно невелико, в то время как влияние размера абразивного зерна является более доминирующим. Результаты FWHM согласуются с наблюдаемыми микроструктурными изменениями поверхности земли.
Пики дифракции измерены ( в черном цвете ) от ( a ) поверхности в состоянии поставки, ( b ) шлифованной поверхности при размере абразивного зерна 180 #, мощности машины 60% и без использования смазки.Соответствующие пики также показаны в синем с красном для K A1 и голубой для K A2 пиков
Рис.
Полная ширина на полувысоте после различных условий шлифования. a Группа I, размерный эффект абразивного зерна. b Группа II, машинное силовое воздействие. c Группа III, эффект смазки при шлифовании
Поверхностные остаточные напряжения параллельны ( σ ∥ ) и перпендикулярно ( σ ⊥ ) к направлениям шлифования при различных условиях шлифования представлены на рис. 16. Неопределенности полученных остаточных напряжений, представленные в виде полос погрешностей на рисунках, получены из стандартных отклонений при аппроксимации дифракционных пиков, а также для отклонений измеряли положения дифракционных пиков из ожидаемых распределений с направлениями измерения в соответствии с теорией упругости для квазиизотропного материала.
Рис. 16 Поверхностные остаточные напряжения, вызванные различными режимами шлифования. a Группа I, размерный эффект абразивного зерна. b Группа II, машинное силовое воздействие. c Группа III, смазывающий эффект при шлифовании. Положительные напряжения — это растягивающие, а отрицательные — сжимающие
Как показано на рисунке, операции шлифования в этом исследовании привели к растяжению σ ∥ и сжатие σ ⊥ напряжения в шлифованных поверхностях.Наибольшее поверхностное остаточное напряжение при растяжении, до 374 ± 44 МПа, было вызвано использованием абразива с крупной зернистостью (60 #), как показано на рис. 16а. Растяжение σ ∥ было уменьшено почти на треть, до 228 ± 25 МПа, за счет использования более мелкого (180 #) абразива, в то время как сжатый σ Напряжение ⊥ было аналогичным. Однако при использовании еще более мелкого абразива (400 #) поверхностное растяжение σ ∥ напряжение увеличивается, но при сжатии σ ⊥ напряжение уменьшается. Тенденция влияния мощности станка на поверхностные остаточные напряжения хорошо видна из рис. 16b, т. Е. Чем выше мощность обработки, тем выше растяжение σ ∥ напряжение, но более низкое сжатие σ ⊥ напряжение в шлифованных поверхностях. Эффект от использования шлифовальной смазки также очевиден, как показано на рис. 16c: использование шлифовальной смазки снижает остаточные напряжения, как σ ∥ и σ ⊥ , в поверхностном слое.
Для образца, отшлифованного абразивом зернистостью 60 #, профиль остаточных напряжений по глубине параллелен ( σ ∥ ) и перпендикулярно ( σ ⊥ ) в направлении шлифования, а также профиль FWHM. Как показано на рис.17, шлифование вызвало растяжение σ Напряжение ∥ резко снизилось с 374 до 44 МПа на поверхности до сжатия на глубине около 15 мкм под поверхностью земли. Компрессионный σ Напряжение ⊥ увеличилось с 91,1 до 18 МПа на поверхности до более 200 МПа в подповерхностной области, а затем постепенно упало до нуля в массивном материале. Результаты показали тенденцию к тому, что остаточные напряжения как вдоль, так и поперек направления шлифования в значительной степени смещаются в сторону сжатия под шлифованными поверхностями. Высокие остаточные напряжения растяжения существуют только в очень тонком поверхностном слое вдоль направления шлифования. Такие большие градиенты остаточных напряжений в приповерхностной области типичны для обрабатываемых деталей (Zhou, Peng Ling, et al.2016). Между тем, также наблюдалось уменьшение FWHM с увеличением глубины, которое выявляет градиент пластической деформации под поверхностью земли.
Глубинные остаточные напряжения и полная ширина на половине максимума профилей после шлифовки 60 # в качестве окончательной отделки поверхности (Zhou, Pettersson, et al. , 2016)
Во время шлифования преобладают механические и термические остаточные напряжения, которые существуют одновременно (Davim 2010). Механическое взаимодействие между абразивным материалом и материалом детали приводит к возникновению анизотропных остаточных напряжений на шлифованной поверхности.Поверхностный слой материала заготовки, параллельный направлению шлифования, испытывает пластическую деформацию сжатия; в то время как перпендикулярно направлению шлифования преобладает деформация растяжения (Guo et al. 2010; Noyan and Cohen 1987). В результате взаимодействие между поверхностным слоем и сыпучим материалом оставляет шлифованную поверхность в состоянии натяжения в направлении шлифования, но сжатия в поперечном направлении. Это также видно в настоящей работе.
В зоне контакта между абразивом и материалом заготовки во время операций шлифования образовывалось тепло, поскольку из-за низкой теплопроводности нержавеющей стали 304L образовался температурный градиент от поверхности к массивному материалу. Это приводит к растягивающим напряжениям в обоих направлениях в течение периода охлаждения после удаления зоны измельчения (Fredj et al. 2006; Davim 2010). В этом исследовании измеренная сильно анизотропная природа поля поверхностных остаточных напряжений, а также относительно низкая температура поверхности во всех грунтовых образцах показывают, что механически индуцированные остаточные напряжения преобладают над термически индуцированными остаточными напряжениями.
При шлифовании абразивом с зернистостью 60 # высокая пластическая деформация поверхности, а также высокая температура шлифования вызывали высокий предел растяжения ( σ ∥ ), которое было уменьшено за счет использования абразива с зернистостью 180 # из-за меньшего механического воздействия.Однако, по сравнению с 180 #, использование абразива с зернистостью 400 # создавало более высокие остаточные напряжения при растяжении, оба ( σ ∥ ) и σ ⊥ . Вероятно, это связано с большим количеством этапов шлифования при шлифовании более мелкими (280 # и 400 #) абразивами, что приводит к большему накоплению тепла на поверхности, таким образом, повышенный тепловой эффект плюс пониженное механическое воздействие привели к более высокому остаточному растяжению. напряжения в поверхности.Тенденция изменения поверхностных остаточных напряжений при различных мощностях обработки очень очевидна. Более высокая мощность обработки увеличивала температуру шлифования; но как исследование микроструктуры, так и результаты FWHM показали, что деформации поверхности и подповерхностного слоя аналогичны при различных используемых мощностях обработки. Таким образом, увеличение теплового эффекта можно рассматривать как основной фактор, который приводит к более высоким остаточным напряжениям при растяжении, как параллельно, так и перпендикулярно направлениям шлифования при шлифовании с более высокой мощностью обработки.Использование шлифовальной смазки уменьшило как деформации поверхности, так и тепло от операции шлифования; однако пониженное поверхностное растяжение ( σ ∥ ) напряжение и сжатие σ Результаты напряжений ⊥ показывают, что уменьшение механических воздействий было более значительным, чем уменьшение тепловых воздействий в этом исследовании.
Часть 2, Раздел II — Материалы и спецификации | Интерактивное сопроводительное руководство по кодам ASME для котлов и сосудов высокого давления: критерии и комментарии по отдельным аспектам кодов для котлов и сосудов высокого давления | Электронные книги Gateway
В этой главе представлены различные спецификации материалов, из которых изготовлены котлы.В первом разделе этой главы прослеживается хронологическая эволюция материалов и связанных с ними технологий, от потребности в материалах для изготовления клепаных конструкций до признания сварки плавлением в качестве процесса изготовления. В это обсуждение включено применение современных материалов, пересмотр основы для установки допустимых значений напряжения и принятие Спецификаций на материалы, отличных от тех, которые одобрены ASTM. В следующих двух разделах обсуждаются Раздел II Кодекса, Часть A– , Спецификации на черные металлы и Часть B– , Спецификации на цветные металлы .Обсуждается следующее: Руководство по утверждению новых материалов в соответствии с Кодексом ASME по котлам и сосудам высокого давления (BPV); Подача технических запросов в комитет по котлам и сосудам под давлением; и Руководство по множественной маркировке материалов. Четвертый раздел обеспечивает основу для спецификаций и стандартов, охватываемых разделом II, часть C– «Спецификация сварочных стержней, электродов и присадочных материалов », и их связи со спецификациями ANSI / AWS. В обсуждение включены система классификации электродов, описания материалов, области применения сварочных материалов, закупка сварочных материалов и сертификация присадочного металла.В пятом разделе рассматриваются важные аспекты раздела II, часть D– Properties . Обсуждаются свойства черных и цветных сплавов, используемых при проектировании компонентов для норм BPV и ядерных строительных норм. В последнем разделе обсуждаются Раздел II, Часть A и Часть B — Международные спецификации материалов . Раздел II ASME включает правила принятия спецификаций материалов признанных национальных или международных организаций, кроме ASTM. В этом разделе также обсуждается процесс принятия спецификаций Комитета по стандартизации в Европе с последствиями для соответствующих спецификаций ASME.
История
Деннис Рахой, Марвин Л. Карпентер и Доменик А. Канонико были первоначальными авторами этой главы. Второе и третье издания были обновлены Марвином Л. Карпентером, Эльмаром Упитисом и Ричардом А. Моеном. Четвертое издание обновили Эльмар Упитис, Марвин Л. Карпентер, Джон Ф. Грабб, Ричард С. Сазерлин, Джеффри Генри, К. В. Роули и Энн Шодуле. Пятое издание было обновлено Ричардом С. Сазерлином, Джеффри Генри и Анн Шодуле. Текущее онлайн-издание было обновлено Анн Шодуэ, Эльмаром Упитисом и Джоном Граббом.
Простая процедура измельчения образцов растений и почвы на валковой мельнице
% PDF-1.7 % 1 0 obj > / Metadata 2 0 R / Outlines 6 0 R / Pages 3 0 R / StructTreeRoot 7 0 R / Type / Catalog / Viewer Preferences >>> эндобдж 5 0 obj > / Шрифт >>> / Поля [11 0 R] >> эндобдж 2 0 obj > поток application / pdf

Шлифовка хрупких материалов — Aggressive Grinding Service, Inc.

Компания Aggressive Grinding Service, Inc.
В промышленном мире к хрупким материалам относятся ряд марок цементированного карбида вольфрама, все семейство передовой керамики, включая карбид кремния, нитрид кремния, оксид алюминия, диоксид циркония и оксид алюминия, закаленный цирконием, карбид бора и другие, а также поликристаллический алмаз. С инженерной точки зрения хрупкий материал — это материал, который не демонстрирует пластической деформации
, предшествующей зарождению трещины.
Когда хрупкий материал необходимо довести до окончательных размеров путем твердого шлифования, он не будет демонстрировать пластической деформации, поскольку алмазная крошка проникает сквозь него для удаления материала; он также не будет демонстрировать профиль остаточного напряжения пластичного материала. Вместо этого материал потрескается, оставив микротрещины, которые останутся подповерхностными повреждениями. Ключом к измельчению хрупких материалов является минимизация подземных повреждений за счет соблюдения заданных параметров измельчения, которые позволят достичь желаемых скоростей съема материала и конечной точности размеров.
Удаление материала
Обычно стружка не считается частью процесса шлифования, но именно это происходит при шлифовании пластичных или хрупких материалов. В хрупком материале «стружки» просто меньше. Механизм удаления хрупкого материала достигается за счет микротрещин и последующего удаления стружки следующим проходящим зерном (см. Рисунок 1).
Профиль нормального распределения напряжений, связанный со шлифованием пластичного материала, не применим к шлифованию хрупкого материала, такого как современная керамика.Любое индуцированное растягивающее напряжение, которое обычно вызывается ограниченным тепловым расширением при высоких температурах, уже привело к микротрещинам под поверхностью, как в хрупком материале (см. Рисунок 2).
Параметры шлифования
При использовании шлифовального круга важными факторами являются связка круга, форма абразива, концентрация зерна, глубина резания (DOC) и поток охлаждающей жидкости. Правильный выбор каждого из этих параметров имеет решающее значение при шлифовании хрупкого материала.Неправильный выбор может привести к серьезному повреждению заготовки, алмазного круга или того и другого. Повреждение усовершенствованной керамической заготовки может быть невидимо невооруженным глазом, но может привести к преждевременному выходу из строя в работе, поскольку микротрещины распространяются под действием рабочего напряжения.
Крепление колеса
Связка круга определяет «твердость» или «мягкость» шлифовального круга и указывает на способность круга удерживать абразивную зернистость. «Более мягкий» круг, как правило, легче разрывает свое сцепление с абразивными зернами, тем самым подвергая шлифованию новые зерна.Напротив, «более твердый» круг дольше сохраняет зерна неповрежденными, тем самым обнажая более затупившийся абразив и сильно влияя на режущую способность.
Успешное шлифование хрупкого материала, такого как современная керамика, традиционно заключалось в использовании круга на полимерной связке, который позволяет снизить давление инструмента и обеспечивает более качественную поверхность. Такой круг приводит к более частому обновлению зерна и режущему действию, которое вызывает минимальное повреждение подповерхности.
Затупившееся абразивное зерно, многократно ударяющее по керамике, вызывает еще больший ущерб, выделяя больше тепла и увеличивая потребление энергии.Последние достижения производителей колес в разработке новых гибридных металлических связок с наведенной пористостью позволили кругу с более жесткой связкой действовать больше как круг с более мягкой связкой, с более длительным сроком службы и равными или лучшими габаритными характеристиками.
Форма и концентрация зерна
Форма абразивного зерна обычно не является спецификацией закупки, когда шлифовальный цех заказывает алмазный круг. Изготовитель круга обычно предоставляет зерно «блочной» или «угловатой» формы на основе данных шлифовального цеха о том, какой материал шлифуется с определенной скоростью (см. Рисунок 3).
В шлифовальном цехе указываются связка, размер и концентрация алмазного зерна, но форма уточняется редко, полагаясь исключительно на решение производителя колес. Отклонение от этого общего подхода и указание вместо этого угловой формы при шлифовании современной керамики может гарантировать минимальное повреждение поверхности. Зерно с большей вероятностью сломается, а не изнашивается, что позволяет обнажить новые частицы и создавать эффект самозатачивания, который предотвращает серьезные эксплуатационные повреждения тусклого или изношенного зерна.
Концентрация зерна определяет количество алмазных частиц в круге для определенного размера зерна. Для кругов, используемых при шлифовании хрупких материалов, характерна концентрация 75-100. Эта концентрация идеальна для поддержания минимального повреждения поверхности и оптимальной производительности колеса.
Таблица 1 показывает типичное число концентрации и эквивалентный объемный процент, который представляет концентрация. Производители колес имеют разные рецепты концентраций для разного размера зерен, и концентрации выше 100 коммерчески доступны.Если желательны более высокие концентрации, желательно проконсультироваться с производителем колеса.
Глубина резания
Чем крупнее (больше) размер алмазного зерна в круге, тем больше открытые зерна выступают из круга. Глубина резания круга должна составлять примерно 60-80% высоты обнаженного зерна (см. Рисунок 4).
Если круг загружается в материал, имеющий DOC, равный высоте обнаженного зерна, то будет выделяться значительное количество тепла, что приведет к большему повреждению подповерхностного слоя.Кроме того, оптимальный поток охлаждающей жидкости к шлифовальной поверхности будет нарушен из-за сжатия пространства между кругом и материалом заготовки. DOC, превышающий высоту открытых зерен, вызывает чрезмерное нагревание. Это приведет к повреждению материала или колеса.
Таблица 2 показывает размер зерна в микронах и дюймах, а также ожидаемую чистоту поверхности, которую должен придавать конкретный размер зерна. В правильно обработанном круге не менее 35% обнаженных алмазных частиц должны выступать из поверхности связки.Следовательно, исходя из данных в таблице 2, алмазный круг с зернистостью 220, имеющий типичный размер зерна 66 микрон (0,0026 дюйма), должен иметь 35% открытой высоты, или 23 микрона (0,0009 дюйма). Тогда DOC должен составлять 60-80% открытой высоты зерна, или приблизительно 15 микрон (0,0006 дюйма).
Расход охлаждающей жидкости
Целью охлаждающей жидкости является отвод тепла от заготовки путем смазывания поверхности раздела заготовка-колесо, чтобы возникло меньшее трение и, как следствие, меньше выделяемого тепла. Охлаждающая жидкость также помогает снизить износ колес и улучшить качество поверхности, а также смыть стружку и минимизировать повреждение поверхности.Принято считать, что более высокий расход охлаждающей жидкости приводит к лучшему отводу тепла.
Фактически, лучший отвод тепла является результатом скорости потока, а не расхода. Следовательно, повышение скорости охлаждающей жидкости до соответствия скорости вращения круга необходимо для того, чтобы охлаждающая жидкость могла переноситься на поверхность шлифования через поры в круге. В идеале скорость охлаждающей жидкости должна соответствовать 80-110% скорости колеса:
V
охлаждающая жидкость = (от 80 до 110%) x V колесо Это соотношение может быть достигнуто за счет давления насоса и общей площади используемого сопла при условии, что насос может подавать поток галлонов в минуту, необходимый для достижения требуемой скорости. Было сказано, что, если бы можно было выполнить операцию полностью погруженного измельчения, высокоскоростной поток все же лучше отводил бы тепло от поверхности измельчения.
Свести к минимуму урон
Следующие известные параметры измельчения могут минимизировать эффект подповерхностного повреждения хрупкого материала. Опытный шлифовальный станок может отклоняться от некоторых из этих параметров, но при этом должен соблюдать осторожность. Такая осторожность необходима, потому что хрупкий материал не прощает ошибок, когда шлифовальные нагрузки превышают прочность материала: возникнут трещины.Однако серьезность таких трещин можно ограничить только с помощью правильной техники шлифования.
Список литературы
- Фотографии и иллюстрации использованы с разрешения The Grinding Doc, Джеффри А. Бэджер, доктор философии, эксперт по шлифованию, независимый консультант, Остин, Техас, «Книга шлифования» и «Живописная одиссея, части I и II. , ”Режущее инструментальное машиностроение.
- Ширер, Томас Р., «Алмазный круг
, шлифование 101», журнал Ceramic Industry
, июнь 2006 г., стр.17-20.
← Вернуться к новости
Технология обработки материалов для производства мягких ферритов
Дипак Бхалла 1 , DK. Сингх 2 , Свати Сингх 1 , Дипти Сет 3
1 Инженерный колледж ACME, Мураднагар, Газиабад, Индия
2 Отделение машиностроения, Инженерный колледж МММ, Горакхпур, Индия
3 Отделение прикладных наук, Радж Кумар Гоэль, Инженерный колледж Гхакху, Индия
Для корреспонденции: Дипак Бхалла, Инженерный колледж ACME, Мураднагар, Газиабад, Индия.
Электронная почта: |
Авторские права © 2012 Научно-академическое издательство. Все права защищены.
Аннотация
В этой статье были предприняты попытки подробно объяснить метод производства марганцево-цинковых (Mn-Zn) мягких ферритов, а также способы их использования и применения.Тот же метод применим и к никель-цинковым (Ni-Zn) и литий-титановым (Li-Ti или микроволновым) ферритам. Показана блок-схема процесса. Были объяснены производственные этапы, такие как смешивание порошков, прокаливание порошка, измельчение порошка, изготовление гранул, прессование компонентов, спекание в туннельной печи или коробчатой печи и обработка на шлифовальном станке с вращающимся столом. Обсуждается влияние атмосферы (кислорода) при спекании компонентов при высокой температуре. Также обсуждались температурные профили муфельной печи и туннельной печи.Изменение температуры внутри муфельной печи (900 × 900 × 800 мм) исследовалось с помощью скользящей термопары. Градиент температуры в объеме печи нанесен на график. Математическая связь была найдена с использованием уравнения аппроксимации кривой. Сопоставлены фактические и математические результаты.
Ключевые слова: Мягкие ферриты, Обработка, Температура, Печь, Спекание
Цитируйте эту статью: Дипак Бхалла, ДК.Сингх, Свати Сингх, Дипти Сет, «Технология обработки материалов для производства мягких ферритов», Американский журнал материаловедения , Vol. 2 № 6, 2012, с. 165-170. DOI: 10.5923 / j.materials.20120206.01.
1. Введение
- Ферриты — это плотные однородные керамические материалы, используемые в качестве сердечника в трансформаторах для электронных устройств.


Рис. ure 1 . Ферритовые компоненты |
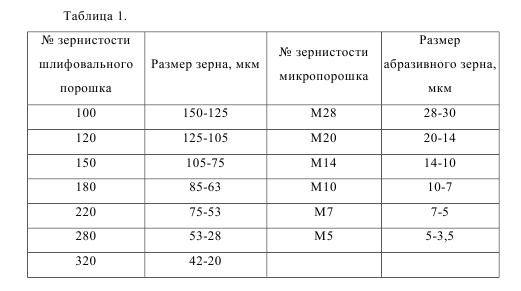
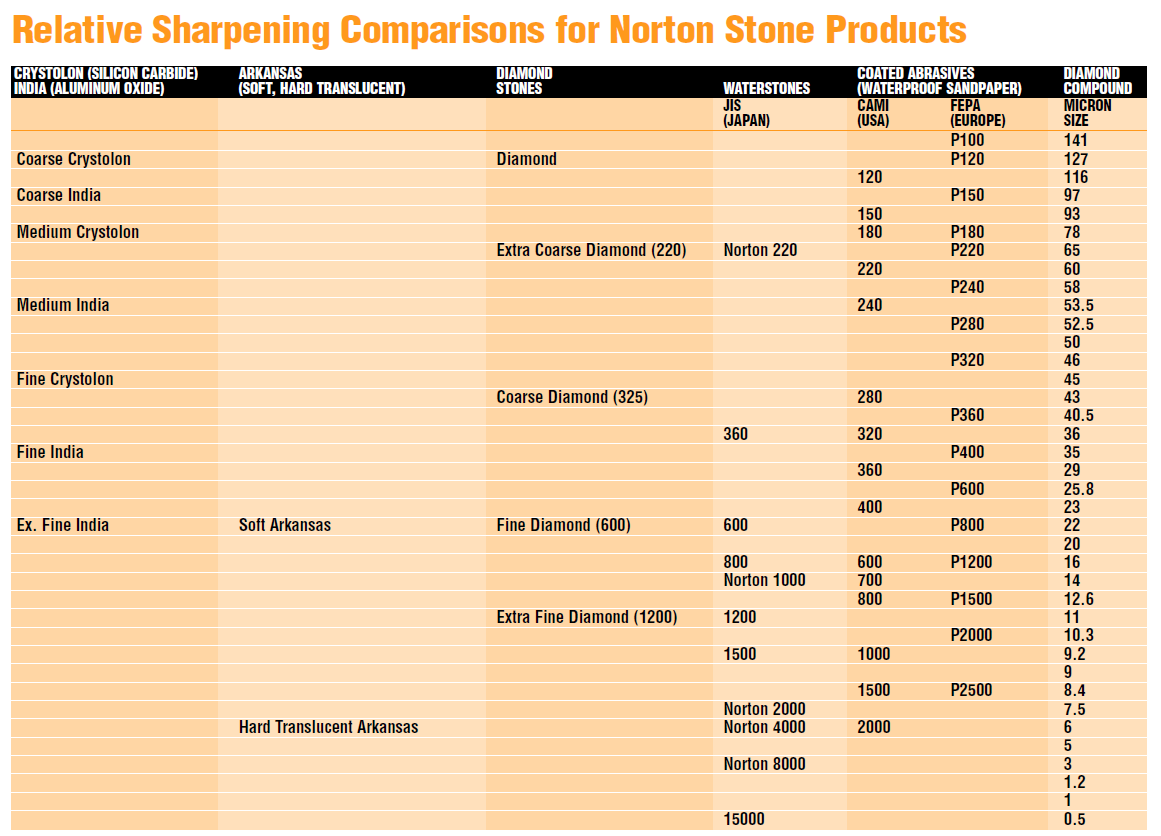
2. Эксперименты
- Ниже приведены основные этапы производства мягких ферритовых компонентов: Смешивание порошков Предварительное спекание Мокрое измельчение порошков Распылительная сушка Прессование гомогенной смеси для получения желаемой форма Спекание в печах туннельного типа (температура 1400 ℃) Обработка спеченного продукта для получения конечного продукта. Типичная технологическая схема производства мягкого феррита показана ниже:
Рис. ure 2 . Этапы процесса производства мягкого феррита |
2.1. Смешивание порошков
- В процессе смешивания соли металлов (в форме оксидов или карбонатов) проверяются на чистоту (в миллионных долях) с помощью химического анализа.

Рис ure 3 . Шаровая мельница для мокрого (на основе деионизированной воды) смешивания порошков и измельчения |
2.2. Прокаливание порошков
- После смешивания порошок прокаливают (предварительно нагревают) при температуре около 75% от конечной температуры спекания.

Рисунок 4 . Прокаливание (предварительное спекание) во вращающейся печи |
2.3. Измельчение
- Мокрое измельчение выполняется в шаровой мельнице, как показано на рисунке.
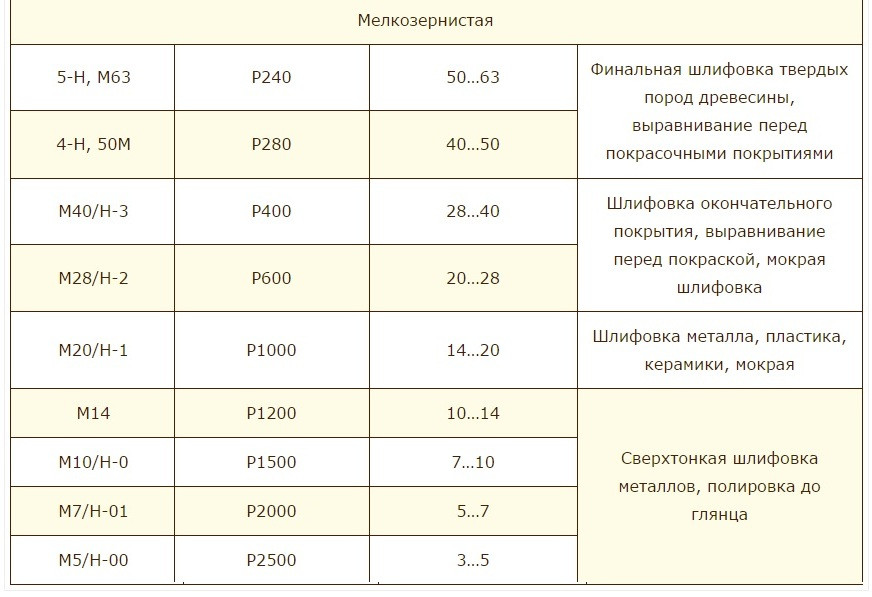
2.4. Изготовление гранул
- Из этого мелкодисперсного, смешанного и высушенного ферритного порошка гранулы получают вручную или с помощью распылительной сушилки.Для партии 200 кг гранулы производятся с использованием распылительной сушилки, а для небольших партий гранулы производятся вручную.
Рисунок 5 . Распылительная сушка для приготовления гранул |
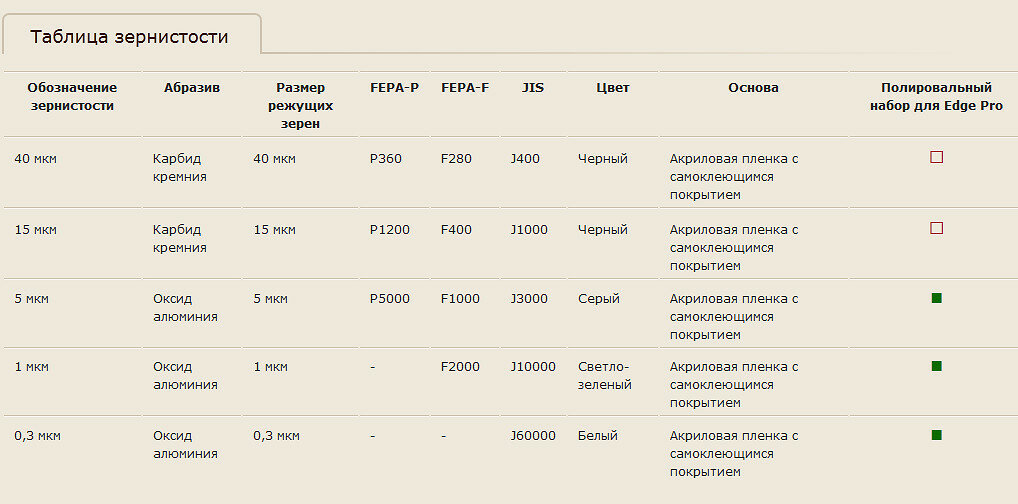
Рисунок 6. Пресс для прессования порошков |
2.5. Прессование
- Следующий этап — формирование детали. Формование или прессование производится на механическом, гидравлическом или изостатическом прессе.
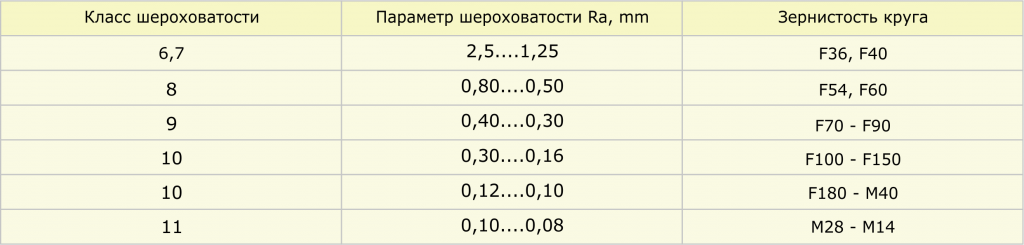
2.6. Спекание
- Это очень важный этап производства ферритов. На этом этапе продукт приобретает свои окончательные магнитные и механические свойства.


Рисунок 7 . Туннельная печь для спекания ферритовых компонентов |
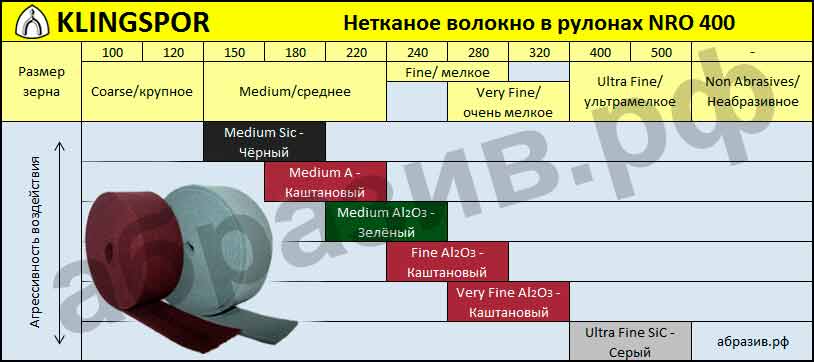
Рисунок 8 . Профиль температуры и атмосферы |

2.7. Обработка и доводка
- Механическая обработка выполняется для получения заданных размеров путем шлифовки этих стержней алмазным кругом. Эта операция не является обязательной. Ферритовые сердечники шлифуются с помощью алмазных шлифовальных кругов, которые обычно имеют чашеобразную форму. Используемые станки представляют собой шлифовальные станки с вертикальным шпинделем и вращающимся столом, как показано на рисунке. 9. Хотя основные магнитные свойства достигаются во время спекания и не могут быть изменены, лучшая обработка поверхности сопрягаемых поверхностей обеспечивает лучшие магнитные характеристики ферритовых сердечников.Таким образом, притирка сопрягаемых поверхностей важна для надлежащего контроля плоскостности и степени чистовой обработки сопрягаемых поверхностей. Для обработки ферритовых сердечников используются следующие типы шлифовальных кругов: Шлифовальный круг из карбида кремния Шлифовальный круг на металлической связке с алмазной пропиткой Шлифовальный круг на полимерной связке с алмазной пропиткой Смола и металл (резмет) Алмазный шлифовальный круг на связке Алмазный шлифовальный круг на гальванической связке Шлифовальный круг с кубическим нитридом бора (CBN) В качестве охлаждающей жидкости используется в основном вода.
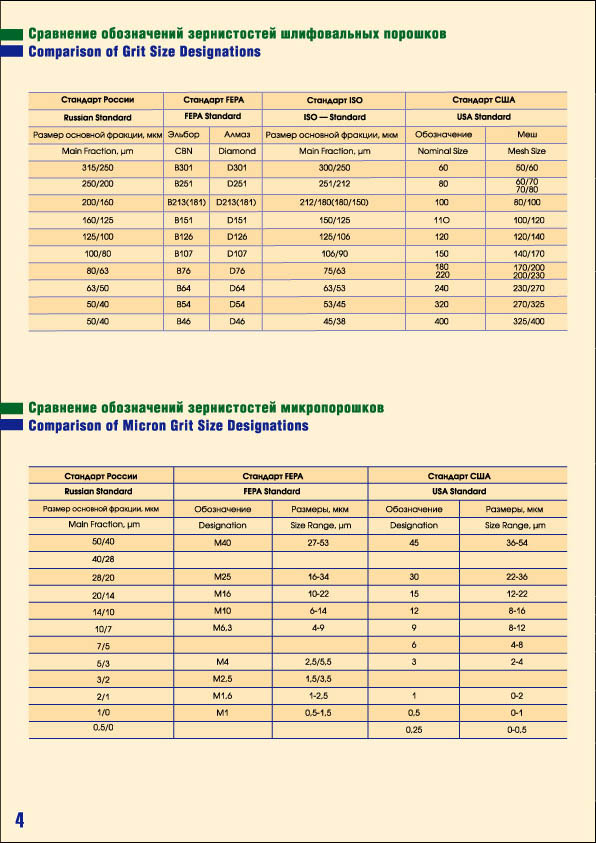
Рисунок 9 . Обработка на шлифовальном станке с вращающимся столом |
2.8. Проверка качества
- Физический осмотр выполняется для проверки компонентов на отсутствие трещин. В то же время гарантируется, что компоненты не имеют коробления, которое может появиться во время спекания или механической обработки. Затем размеры проверяются по чертежу с помощью штангенциркуля, микрометра, высотомера или глубиномера и т. Д.Проверяются электрические свойства, такие как удельное сопротивление, проницаемость, значение A L , параметры петли B-H (кривая гистерезиса), намагниченность насыщения, температура Кюри.
3. Результаты и обсуждение
- Жесткие и мягкие ферриты играют доминирующую роль в магнитных материалах и производятся в значительных количествах.
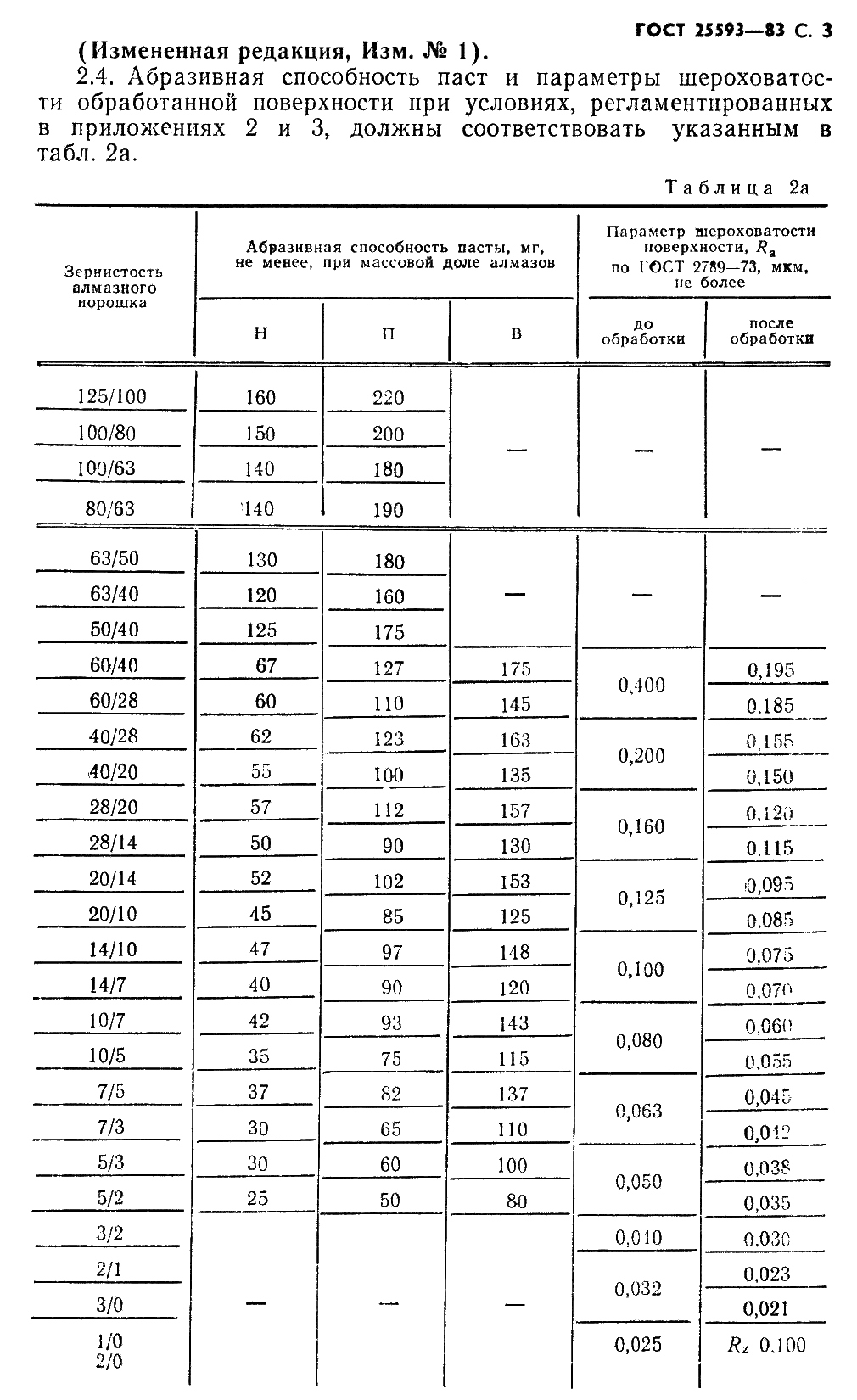
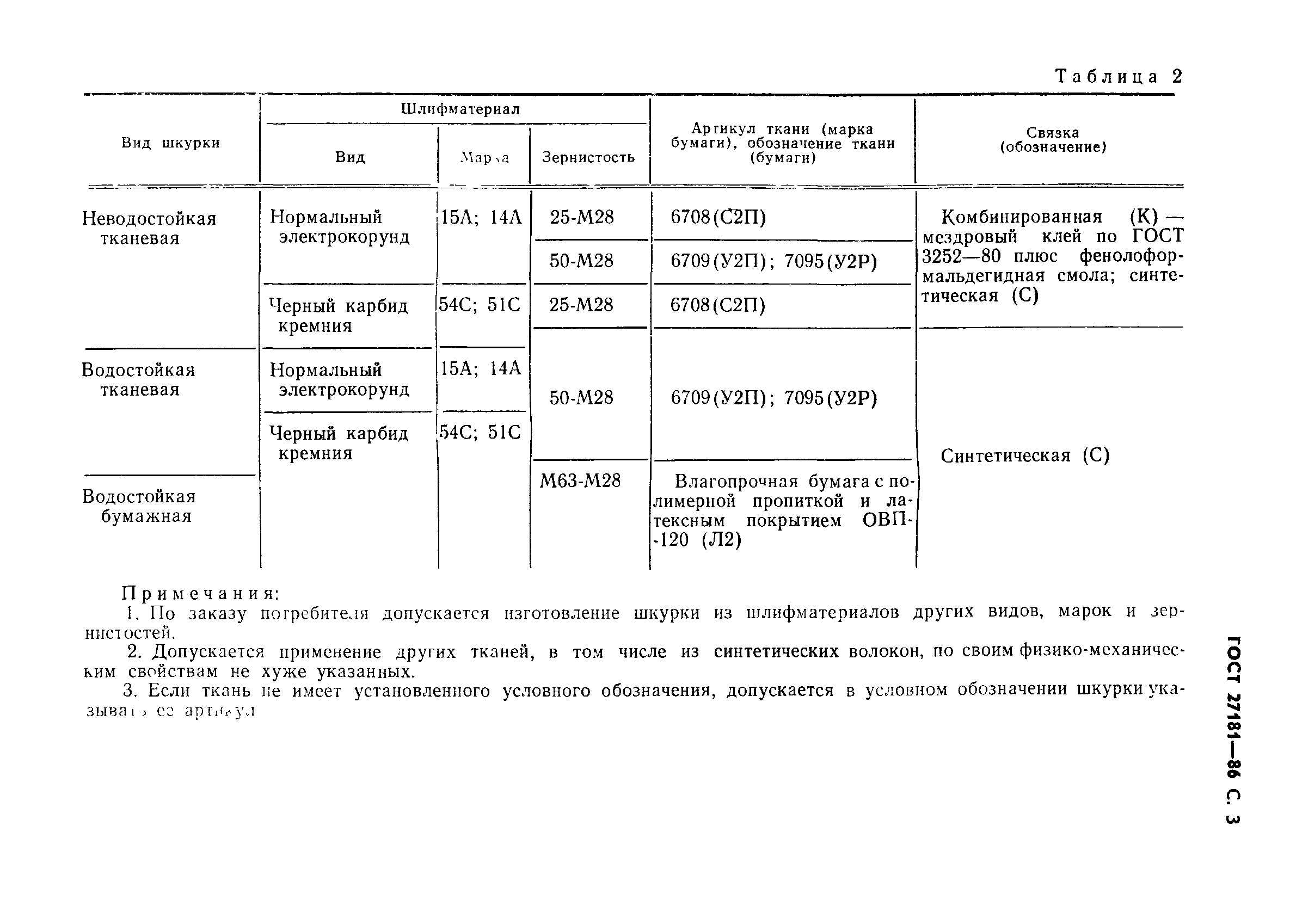
Рисунок 10 . Температурный градиент в муфельной (коробчатой) печи |
|
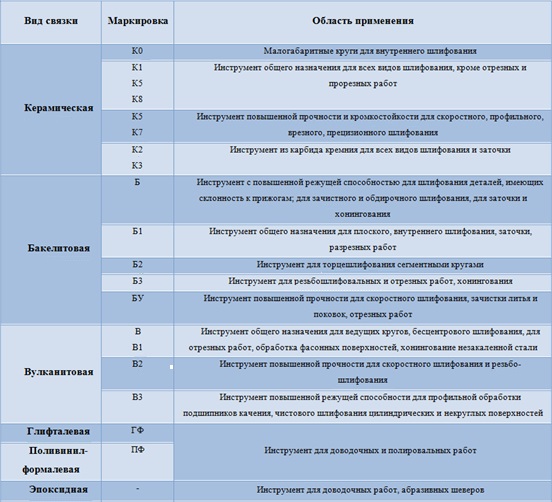
4. Выводы
- В современной электронике ферриты пользуются огромным спросом. Инженеру-проектировщику электронных схем очень важно знать технологию производства этих ферритов. Области применения: прикладная электроника, преобразование энергии, связь, компьютеры, приборостроение и физика высоких энергий. Состав сырья, его источник и этапы процесса сильно влияют на магнитные свойства этих ферритов и их формы.Чтобы выбрать правильный материал и форму, понимая вышеупомянутый процесс и детали производства, инженер-конструктор будет учитывать ограничения, с которыми сталкиваются производители, и будет выбрана правильная форма и размер сердечника. Эти производственные детали также пригодятся начинающему предпринимателю при создании завода по производству мягкого феррита. Кроме того, это очень полезно для ученых-исследователей в области прикладной электроники и изучения новых возможных областей исследований.Это также улучшит качество существующих производителей феррита.

Каталожные номера
[1] | Hitoshi Saita, Tomofumi Kuroda, Naoyoshi Sato (2002), «Магнитный ферритовый материал и метод его производства», Патент США 6402979 |
[2] | Bhalla Deepak, SK Aggarwal et al. (2010), «Производство марганцево-цинкового мягкого феррита методом порошковой металлургии».![]() |
[3] | Flavin E, F. Boust, Onera OM, 1996, «Экспериментальное исследование высокочастотной проницаемости в ферритовых композитных материалах», Труды Седьмой Международной конференции по ферритам, Конференц-центр Бордо, Франция , стр. 453 |
[4] | Дитмар Хольц и др., 2007, «Промышленный количественный контроль характеристик прессования высушенных распылением гранул MnZn-феррита» Журнал Американского керамического общества, том 90, выпуск 6 июня 2007 страницы 1780-1786 |
[5] | Topfer J, Schops W, Nauber P et al (1999) «Современные тенденции развития производства и применения магнитомягких ферритовых материалов», Международный форум керамики, том 76 с. 49-55 |
[6] | Miclea C, Tanasoiu C, CF Miclea, et al (2005), «Мягкие ферритовые материалы для магнитных датчиков температуры и приложений» Journal of Magnetism and Magnetic Materials, volume 290-291, па RT 2, апрель 2005 г.![]() |
[7] | Бхалла Д., Кайкер С.К., Аггарвал С.К. (2008 г.), «Технологии производства литий-титановых ферритов», Труды 10-й Международной конференции по ферриты, Чэнду, Китай, стр. 321-324 |
[8] | Маучок Р. и В.Т. Заспалис (2000), «Взаимодействие процесса выгорания связующего материала во время спекания ферритов Mn-Zn», Журнал Европейского керамического общества, том 20, выпуск 12, ноябрь 2000 г., страницы 2121-2127 |
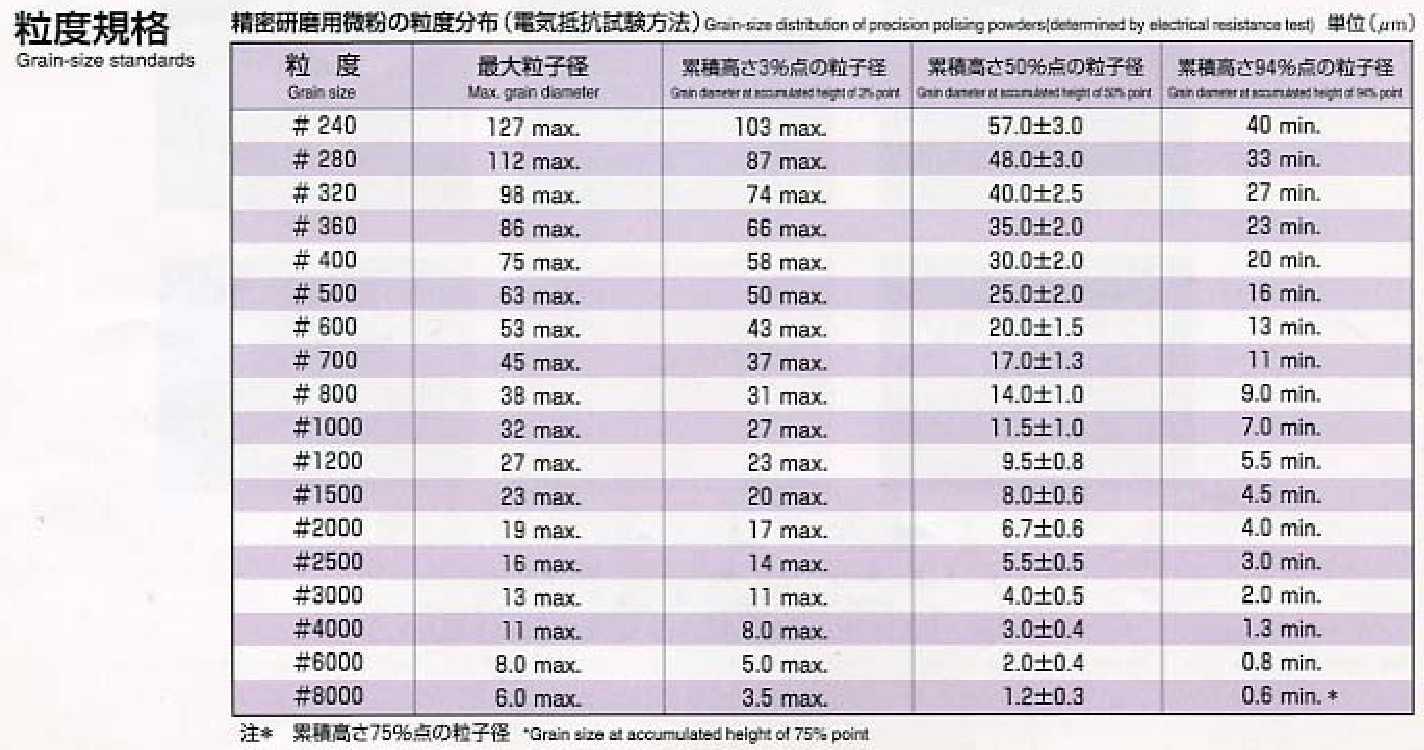