Принцип плазменной резки. Работа на плазменной резке.
2.1 Нечто большее, чем просто одно из состояний вещества?
Как правильно понимать источники плазменной резки? Плазма представляет собой нагретый до высокой температуры газ, обладающий электропроводимостью, который состоит из положительно и отрицательно заряженных частиц, а также возбужденных и нейтральных атомов и молекул. Между процессами диссоциации, ионизации и рекомбинации, присущими плазменному состоянию, устанавливается динамический баланс. В результате плазма электрически нейтральна. В физике плазму часто называют четвёртым состоянием вещества. В природе плазменное состояние вещества, обусловленное высокими температурами, имеет место внутри солнца и других звёзд. Молния также является примером перехода вещества в плазменное состояние, происходящий под действием сил электрического поля большой величины.
Рисунок 1: Плазма — четвертое состояние вещества |
Для того чтобы создать плазму для технических потребностей, газ либо сильно разогревается с помощью источника тепла, либо подвергается действию сильного электрического поля, так чтобы перевести его в ионизированное состояние.
2.2 Принцип плазменной резки
Плазменная резка – это процесс термической резки, при котором плазменная дуга обжимается, проходя через сопло. Дуга прямого действия, которая возникает, когда электрический ток протекает от неплавящегося электрода (катода) на изделие (анод), используется для резки материалов, обладающих электрической проводимостью. Эта форма плазменной резки является наиболее часто используемой. В случае дуги косвенного действия, она создаётся между электродом и соплом. Даже если используется режущий газ, в состав которого входит кислород, тепловой эффект плазменной дуги преобладает. Таким образом, данный метод не рассматривается как процесс кислородной резки, а скорее как резка путём плавки.
Плазменные газы в дуге частично подвергаются диссоциации и ионизации, что делает их электропроводящими. Благодаря высокой плотности энергии и температуре плазма расширяется и движется по направлению к изделию со скоростью, которая в три раза превышает скорость звука.
Благодаря рекомбинации атомов и молекул на поверхности изделия потреблённая энергия сразу же высвобождается и усиливает тепловой эффект воздействия плазменной дуги на изделие. В плазменной дуге температура доходит до 30 000 К. В сочетании с высокой кинетической энергией плазменного газа такая температура обеспечивает чрезвычайно высокую скорость резки всех материалов, обладающих электрической проводимостью, которая зависит от толщины материала.
Для начала процесса резки в первую очередь зажигается пилотная дуга между соплом и электродом путём подачи высокого напряжения. Эта низкоэнергетическая пилотная дуга подготавливает пространство между плазменным резаком и изделием, вызывая частичную ионизацию. Когда пилотная дуга контактирует с изделием (резка с лёта), благодаря автоматическому увеличению мощности зажигается основная плазменная дуга.
Рисунок 2: Принцип плазменной резки с помощью дуги прямого действия |
Металлический материал плавится и частично испаряется благодаря тепловой энергии дуги и плазменного газа. Расплавленный металл выдувается из реза под действием кинетической энергии плазменного газа. В отличие от кислородной резки, при которой около 70% тепловой энергии вырабатывается благодаря сгоранию железа, в процессе плазменной резки энергия, требующаяся, для того чтобы расплавить материал в резе создаётся только под действием электричества.
Выбор используемого плазменного газа зависит от того, какой материал требуется разрезать. Например, одноатомный газ аргон и/или двухатомные газы, такие как водород, азот, кислород и смеси этих газов, а также очищенный воздух, используются в качестве плазменного газа и режущего газа.
Резаки могут иметь как водяное, так и газовое охлаждение. В зависимости от того, где используются процессы плазменной резки, различают процессы, выполняемые над водой и на ней, а также такие, которые производятся под поверхностью воды.
2.3 Оборудование для плазменной резки
2.3.1 Источник питания для плазменной резки
Источник питания для плазменной резки подаёт рабочее напряжение и ток резки для основной и вспомогательной дуги. Напряжение источника питания для плазменной резки без нагрузки находится в диапазоне между 240 и 400 В. В состав источника питания входит система зажигания пилотной дуги (вспомогательной плазменной дуги), назначение которой состоит в возбуждении основной плазменной дуги. Для того чтобы это выполнить сначала зажигают плазменную дугу косвенного действия, используя импульсы высокого напряжения. Назначение данной дуги состоит в ионизации пространства между соплом и изделием, что позволяет возбудить основную плазменную дугу.
Рисунок 3: Пример установки для плазменной резки |
Источники питания для плазменной резки либо имеют круто падающую кривую вольтамперной характеристики (рис. 6), либо постоянную токовую характеристику (рис. 7), в связи с чем при удлинении дуги мощность резки изменяется незначительно или остаётся неизменной.
Рис.![]() для плазменной резки с крутоубывающей (крутопадающей характеристикой) кривой напряжения и тока | Рис.7: Источник питания для плазменной резки с постояноой токовой характеристикой (вертикальнок падение) |
2.3.2 Электрод и сопло плазменного резака
Повышение эффективности плазменной резки в большой степени зависит от конструкции плазменного резака. Чем плотнее плазменная дуга обжимается, тем выше скорость резки и качество кромки реза.
Важнейшими деталями плазменного резака являются плазменное сопло и электрод. Как плазменное сопло, так и электрод являются быстроизнашивающимися деталями. Неправильный подбор, либо неверное использование сопла или электрода могут значительно сократить срок их службы и повредить резак.
Срок службы электрода в значительной степени определяется силой тока резки, количеством зажиганий, а также типом используемого плазменного газа. Кроме того, управление газом и мощностью вначале и в конце резки, а также рассеяние тепла от электрода также играет ключевую роль. Обычно используются электроды стержневой формы из вольфрама, а также имеющие форму пальца из циркония или гафния, которые можно сделать заострёнными или плоскими. Ввиду того, что они подвержены эрозии, электроды из вольфрама могут применяться только с инертными плазменными газами и их смесями, а также с газами с низкой реакционной способностью и восстановительными плазменными газами. При использовании чистого кислорода, либо плазменных газов, в состав которых входит кислород, электроды будут служить значительно дольше, если они будут изготовлены из циркония или гафния. Эти материалы естественным образом формируют защитный слой, плавящийся при более высокой температуре (табл. 1), и, к тому же, они заключены в основную оболочку, обладающую очень большой теплопроводностью, которая интенсивно охлаждается. Если в плазменной резке используется кислород, увеличения срока службы электрода можно добиться, подавая два газа: процесс зажигания проводится с использованием газа с низкой окислительной способностью, а сам процесс резки с использованием кислорода.
Ключевые факторы, влияющие на срок службы сопла:
- диаметр на выходе сопла
- масса и теплопроводность материала сопла
- выход (произведение силы тока резания на напряжение резания)
- время действия плазменной дуги
- количество зажиганий
- последовательность прожигания отверстий
- и интенсивность охлаждения.
Водяное охлаждение является более интенсивным. Воздушное охлаждение требует большего количества газа.
Таблица 1: Типовые величины для расходных деталей, применяемых с плазменными резаками
Материал | Усл. | плавл. [°C] | Используемый | Теплопроводность |
Вольфрам | W | ≈ 3400 | Ar | ≈ 174 |
Оксид вольфрама | WO3 | ≈ 1473 | Ar/H2 | |
Цирконий | Zr | ≈ 1852 | O2 | ≈ 22 |
Оксид циркония | ZrO2 | ≈ 2700 | Воздух | ≈ 2,5 |
Нитрид циркония | ZrN | ≈ 2982 | ||
Гафний | Hf | ≈ 2227 | ||
Оксид гафния | HfO2 | 1700 | O2 | |
Нитрид гафния | HfN | 3305 | Воздух | ≈ 29 |
Медь | Cu | 1083 | ||
Оксид меди | Cu2O | 1235 | Все | ≈ 400 |
Серебро | Ag | 961 | Все | ≈ 429 |
(Источник: информационный листок DVS 2107)
2.
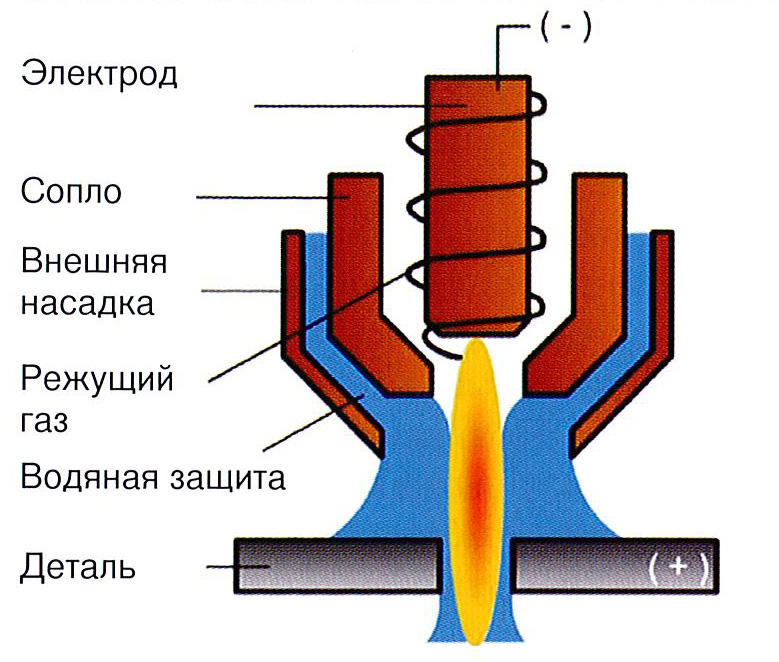
При плазменной резке с помощью плазменной дуги прямого действия разрезаемый материал должен обладать электрической проводимостью, так как изделие является частью электрической цепи. Заземление подсоединённого изделия должно проектироваться таким образом, чтобы обеспечивалось непрерывное прохождение тока.
2.3.4 Подаваемый газ
Системы плазменной резки работают с инертными, восстановительными газами или с газами с низкой реакционной способностью, а также с химически активными газами и их смесями. Подробное описание систем подачи газа и информация по выбору газов, а также рекомендации по качеству применяемого газа приведены в главе 4.
2.3.5 Системы циркуляции охладителя
Поскольку плазменная резка сопряжена с большими тепловыми нагрузками, необходимо эффективное охлаждение. Различают интегрированные и внешние контуры циркуляции водяного охлаждения и газового охлаждения. Резаки, работающие с током около 100 ампер и более, обычно охлаждаются водой.
2.3.6 Система воспроизведения
Требования, относящиеся к точности воспроизведения, а также эксплуатационные характеристики систем воспроизведения устанавливаются стандартом ISO 8206.
2.3.7 Стол для резки и система вытяжки
Столы для плазменной резки служат стабильной основой для расположения металлического листа, который требуется разрезать. Размеры стола зависят от размера, толщины и массы листа металла. Выделения, которые сопровождают процесс резки можно значительно уменьшить, используя плазменный резак в сочетании с вытяжной системой для удаления дыма и пыли, либо с водяным бассейном.
устройство, принцип действия, выбор, какой лучше
Содержание страницы
Что такое плазморез, как работает он? Если говорить об этом инструменте, то необходимо отметить, что он является прибором, который использует достаточно узкий круг сварщиков. Для одноразового применения плазменный резак нигде и никогда не применяется. Потому что существуют инструменты, с помощью которых можно провести отрезные операции, не прибегая к дорогому варианту, к примеру, болгаркой.
Но если требования к скорости и объему проводимых процессов достаточно жесткие, то без плазмореза не обойтись. Поэтому его используют в машиностроительной промышленности, в изготовлении больших металлических конструкций, при резке труб и прочего.
Виды плазменных резаков и их назначение
На вопрос, как выбрать плазморез, необходимо ответить так, все будет зависеть от того, в какой области вы его собираетесь использовать. Потому что конструктивные особенности у разных видов сильно отличаются, у всех у них разный тип зажигания дуги и различная мощность системы охлаждения.
- Инструменты, работающие в среде защитных газов: аргон, водород, азот, гелий и так далее. Эти газы обладают восстановительными свойствами.
- Резаки, работающие в среде окислительных газов. Газы обычно насыщаются кислородом.
- Приборы, работающие со смесями.
- Плазменные резаки, работающие в стабилизаторах газожидкостного типа.
- Плазморезы, работающие со стабилизацией водной и магнитной. Специфичный инструмент, который редко используется, поэтому в свободной продаже трудно найти.
Существует еще одна классификация, которая делит плазморезы по виду используемого оборудования.
- Инверторные. Экономичный вариант, который может резать металлические детали толщиною до 30 мм.
- Трансформаторные. Производит резку металлов толщиною до 80 мм, менее экономичный вариант.
По типу контакта плазморезы делятся на контактные и бесконтактные. Из названий можно понять метод использования плазменного резака. В первом случае для него необходим контакт с обрабатываемым металлом, поэтому с его помощью можно отрезать изделия толщиною не более 18 мм. Во втором такого контакта не должно быть, зато толщина отрезаемой металлической заготовки может быть максимально возможной.
И еще один вид разделения – это по типу использования и возможностях потребления электроэнергии. Здесь две позиции: бытовой, работающий от сети переменного тока под напряжением 220 вольт, и промышленные (профессиональные), подключаемые к трехфазной питающей сети напряжением 380 вольт.
Внимание! Даже самый маломощный бытовой резак плазменного типа обладает мощностью 4 кВт. Поэтому при подключении его в бытовую электрическую сеть, необходимо удостовериться, что она сможет выдержать такую нагрузку.
Но данная нагрузка не единственная. В системе плазменной резки используется охлаждение, для чего в комплект к основному оборудованию прилагается компрессор, который также работает от электросети. И его мощность нужно учитывать, подключаясь к бытовой питающей сети.
Устройство плазмореза
Само название уже информирует о том, что резка металлов производится с помощью плазмы. А плазма – это ионизированный газ, который обладает высокой проводимостью электрического тока. И чем выше температура этого газа, тем выше проводимость, а значит, сила резки увеличивается.
Для процессов резки металлов используют воздушно-плазменную дугу. При этом электрический ток имеет непосредственное воздействие на металлические поверхности. То есть, принцип работы плазмореза такой:
- Плавление металла.
- Выдувание его жидкого состояния из зоны среза.
Состоит плазменный резак из:
- источника питания – это может быть сварочный трансформатор или инвертор;
- самого резака, который иногда называют плазмотроном;
- компрессора;
- шлангов.
Важно понять конструктивные особенности самого резака. Внутри него вставлен электрод, изготовленный из редких металлов, таких как бериллий, гафний, цирконий и так далее. Почему именно они? Потому что в процессе нагревания на поверхности такого электрода образуются тугоплавкие оксиды. Они своеобразная защита самого электрода, которая обеспечивает целостность материала, то есть, не разрушается. Но чаще всего в плазменных резаках устанавливаются электроды из гафния, потому что он не токсичен, как торий, и нерадиоактивен, как бериллий.
Немаловажное значение в конструкции резака играет и сопло, через который подается плазма на резку. Именно от него и зависят основные характеристики оборудования. А точнее сказать, от его диаметра и длины. От диаметра зависит мощность плазменного потока, а соответственно и быстрота среза и ширины срезанной канавки. Конечно, от этого зависит и скорость охлаждения заготовки. Чаще всего на резаках плазменной резки устанавливается сопло диаметром 3 мм. Длина сопла влияет на качество среза. Чем оно длиннее, тем качество выше. Хотя очень длинное сопло быстро выходит из строя.
Схема работы плазменной резки
При нажатии на кнопку розжига автоматически включается источник электроэнергии, который подает в резак ток высокой частоты. Появляется так называемая дежурная дуга между наконечником сопла и электродом. Температура дуги – 6000-8000С. Необходимо обратить внимание, что сразу дуга между электродом и разрезаемым металлом не образуется, на это надо время.
После чего в камеру резака начинает поступать воздух из компрессора, он сжатый. При прохождении через камеру, где располагается дежурная дуга, воздух нагревается и увеличивается в сто раз. К тому же он начинает ионизироваться, то есть, превращается в токопроводящую среду, хотя сам по себе воздух – это диэлектрик.
Суженное до 3 мм сопло создает поток плазмы, который с большой скоростью вылетает из резака. Скорость – 2-3 м/с. Температура ионизированного воздуха достигает огромной величины – до 30000С. При такой температуре воздух по проводимости электрического тока приближается к проводимости металла.
Как только плазма касается обрабатываемой металлической поверхности, дежурная дуга выключается, а рабочая включается. Производится плавление металлической заготовки в месте среза, откуда жидкий металл сдувается подающим в зону среза воздухом. Вот такая элементарная схема принципа работы плазменной резки.
Как правильно выбрать инструмент для плазменной резки
Любой работавший с плазменной резкой сварщик отметит, что чем выше сила подающего на электрод тока, тем быстрее проходит процесс. Но есть определенные условия, на которые влияют и другие параметры оборудования.
Тип металла и толщина среза. От этих параметров будет зависеть выбор оборудования, с которым придется работать. А именно такой параметр, как сила тока. Внизу таблица соотношений.
Вид металла | Сила тока для резки металлического листа толщиною 1 мм, А |
---|---|
Цветные металлы | 6 |
Черные металлы и нержавейка | 4 |
Чтобы разрезать медный лист толщиною 2 мм, потребуется резак плазменный с силой тока 12 А. И так далее.
Внимание! Рекомендуется приобретать оборудование с запасом силы тока. Потому что указанные параметры в таблице являются максимальными, а с ними работать можно лишь незначительное время.
Достоинства и недостатки
Перед тем как принять решение о приобретение плазменного резака, нужно ознакомиться со всеми положительными и отрицательными сторонами этого оборудования. Ведь, к примеру, в домашних условиях его может заменить обычная болгарка.
Итак, плюсы использования резака для плазменной резки металлов.
- Большая скорость резки, соответственно уменьшение времени на этот процесс. По сравнению с другими режущими инструментами (кислородная горелка, например) скорость выше в шесть раз. Уступает только лазерной резке.
- С помощью плазменного инструмента можно резать толстые заготовки, что иногда не под силу болгарке.
- Режет любые виды металлов. Главное – правильно выставить режим работы.
- Минимальный подготовительный этап. Зачищать поверхности деталей от ржавчины, грязи, масляных пятен нет никакого смысла. Они для резки не помеха.
- Высочайшая точность среза и высокое его качество. Для ручных агрегатов для точности среза используются специальные упоры, которые не дают резаку смещаться в плоскости.
Срез получается без наплывов, ровным и тонким.
- Невысокая температура нагрева, кроме зоны среза, поэтому заготовки не деформируются.
- Возможность фигурного среза. И хотя этим могут похвастаться и другие режущие инструменты, но, к примеру, после кислородной горелки придется края среза шлифовать и убирать подтеки металла.
- Стопроцентная безопасность проводимых операций, ведь никаких газовых баллонов в комплекте оборудования нет.
Минусы:
- Высокая цена оборудования.
- Возможность работать только одним резаком.
- Необходимо направление плазмы выдерживать строго перпендикулярно плоскости обрабатываемой детали. Правда, сегодня можно приобрести аппараты, которые режут изделия под разными углами: 15-50°.
- Толщина разрезаемого изделия ограничена, потому что самые мощные плазморезы могут разрезать металл толщиною 100 мм. С помощью кислородной горелки можно резать толщину 500 мм.
И все же плазморезы сегодня достаточно востребованы. Ручные часто используются в небольших цехах, где требуется провести большой объем резки металлов, и где к качеству разреза предъявляются жесткие требования. Обязательно посмотрите видео, которое специально размещено на этой странице сайта.
https://www.youtube.com/watch?v=rg4PvBBr1CU
Плазменно-дуговая резка. Рассмотрение процесса и оборудования
Плазменно-дуговой процесс всегда рассматривался как альтернатива кислородно-топливному процессу. В этой части серии описываются основы процесса с акцентом на рабочие характеристики и преимущества многих вариантов процесса.
Щелкните здесь , чтобы посмотреть наши последние технические подкасты на YouTube .
Основы процесса
Процесс плазменной резки показан на Рис. 1 . Основной принцип заключается в том, что дуга, образующаяся между электродом и заготовкой, сужается медным соплом с мелким отверстием. Это увеличивает температуру и скорость плазмы, выходящей из сопла. Температура плазмы превышает 20 000°C, а скорость может приближаться к скорости звука. При резке поток плазмообразующего газа увеличивается так, что глубоко проникающая плазменная струя прорезает материал, а расплавленный материал удаляется в вытекающей плазме.
Этот процесс отличается от кислородно-топливного процесса тем, что в плазменном процессе используется дуга для плавления металла, тогда как в кислородно-топливном процессе кислород окисляет металл, а тепло экзотермической реакции плавит металл. . Таким образом, в отличие от кислородно-топливного процесса, плазменный процесс можно применять для резки металлов, образующих тугоплавкие оксиды, таких как нержавеющая сталь, алюминий, чугун и сплавы цветных металлов.
Источник питания
Источник питания, необходимый для плазменно-дугового процесса, должен иметь падающую характеристику и высокое напряжение. Хотя рабочее напряжение для поддержания плазмы обычно составляет от 50 до 60 В, напряжение холостого хода, необходимое для зажигания дуги, может достигать 400 В постоянного тока.
При инициировании вспомогательная дуга формируется внутри корпуса горелки между электродом и соплом. Для резки дуга должна быть перенесена на заготовку в так называемом «перенесенном» режиме дуги. Электрод имеет отрицательную полярность, а заготовка — положительную, так что большая часть энергии дуги (приблизительно две трети) используется для резки.
Состав газа
В традиционной системе с использованием вольфрамового электрода плазма является инертной, образованной с использованием либо аргона, либо аргона-H 2 или азот. Однако, как описано в Варианты процесса , можно использовать окисляющие газы, такие как воздух или кислород, но электрод должен быть из меди с гафнием.
Поток плазмообразующего газа имеет решающее значение и должен быть установлен в соответствии с текущим уровнем и диаметром отверстия сопла. Если расход газа слишком мал для текущего уровня или уровень тока слишком высок для диаметра отверстия сопла, дуга гаснет, образуя две последовательные дуги: электрод к соплу и сопло к заготовке. Эффект «двойной дуги» обычно катастрофичен при плавлении сопла.
Качество резки
Качество кромки плазменной резки такое же, как и при кислородно-топливном процессе. Однако, поскольку плазменный процесс режет плавлением, характерной чертой является более высокая степень плавления по направлению к верхней части металла, что приводит к закруглению верхней кромки, плохой прямоугольности кромки или скосу кромки реза. Поскольку эти ограничения связаны со степенью сужения дуги, доступно несколько конструкций горелок, улучшающих сужение дуги и обеспечивающих более равномерный нагрев в верхней и нижней части реза.
Варианты процесса
Варианты процесса, Рис. 2а-2е , в основном были разработаны для улучшения качества резки и стабильности дуги, снижения шума и образования дыма или увеличения скорости резки.
Двойной газ
Процесс работает в основном так же, как и обычная система, но вокруг сопла вводится вторичный газовый экран, Рис. 2a . Положительные эффекты вторичного газа заключаются в усилении сужения дуги и более эффективном «выдувании» окалины. Плазмообразующий газ обычно представляет собой аргон, аргон-H 2 или азот, а вторичный газ выбирается в зависимости от разрезаемого металла.
Сталь
воздух, кислород, азот
Нержавеющая сталь
азот, аргон-H 2 , CO 2
- Алюминий
аргон-H 2 , азот/CO 2
Преимущества по сравнению с обычной плазмой:
- Снижение риска «двойного искрения»
- Более высокие скорости резания
- Уменьшение закругления верхней кромки
Впрыск воды
В качестве плазмообразующего газа обычно используется азот. Вода впрыскивается радиально в плазменную дугу, Рис. 2b , чтобы вызвать большую степень сжатия. Температура также значительно повышается, достигая 30 000°C.
Преимущества по сравнению с обычной плазмой:
- Улучшение качества и прямоугольности резки
- Повышенная скорость резания
- Меньший риск «двойного искрения»
- Уменьшение эрозии сопла
Водяной кожух
Плазма может работать либо с водяным кожухом, Рис. 2c , либо даже с заготовкой, погруженной на глубину от 50 до 75 мм ниже поверхности воды. По сравнению с обычной плазмой вода действует как барьер, обеспечивая следующие преимущества:
Удаление дыма
- Снижение уровня шума
- Увеличенный срок службы сопла
В типичном примере уровня шума при высоком токе 115 дБ для обычной плазмы водяной экран эффективно снижает уровень шума примерно до 96 дБ, а под водой — до 52–85 дБ.
Поскольку водяной экран не увеличивает степень сужения, прямоугольность режущей кромки и скорость резания заметно не улучшаются.
Воздушная плазма
Инертный или нереакционноспособный плазмообразующий газ (аргон или азот) можно заменить воздухом, но для этого требуется специальный электрод из гафния или циркония, закрепленный в медном держателе, Рис. 2d . Воздух также может заменить воду для охлаждения горелки. Преимущество воздушно-плазменной горелки в том, что в ней вместо дорогостоящих газов используется воздух.
Следует отметить, что хотя электрод и сопло являются единственными расходными материалами, электроды с гафниевым наконечником могут быть дороже по сравнению с вольфрамовыми электродами.
Плазменная резка с высоким допуском
В попытке улучшить качество резки и конкурировать с превосходным качеством резки лазерных систем, доступны системы плазменно-дуговой резки с высоким допуском (HTPAC), которые работают с сильно сжатой плазмой. Фокусировка плазмы осуществляется за счет закручивания плазмы, генерируемой кислородом, при ее входе в отверстие для плазмы, а вторичный поток газа вводится после плазменного сопла 9.0007 Рис. 2e . Некоторые системы имеют отдельное магнитное поле, окружающее дугу. Это стабилизирует струю плазмы за счет поддержания вращения, вызванного закрученным газом. Преимущества систем HTPAC:
- Качество резки находится между обычной плазменной дугой и лазерной резкой
- Узкий пропил
- Меньшая деформация благодаря меньшей зоне термического влияния
HTPAC — это механизированная техника, требующая точного и высокоскоростного оборудования. Основные недостатки заключаются в том, что максимальная толщина ограничена примерно 6 мм, а скорость резки обычно ниже, чем у обычных плазменных процессов, и составляет примерно 60-80% скорости лазерной резки.
Эта статья была подготовлена Биллом Лукасом в сотрудничестве с Дерриком Хилтоном, BOC
Что такое плазменная резка? Принцип работы и его преимущества
Существует несколько преимуществ плазменной резки как метода изготовления металла по сравнению с другими. Эти преимущества включают экономическую эффективность, более широкий диапазон резки металла, высокую точность и повторяемость.
Что такое плазменная резка? Как работает этот процесс? Какой газ идеально подходит для использования в этом процессе? С какими материалами работают плазменные резаки? Мы подробно ответим на эти вопросы и предоставим вам другую важную информацию о плазменной резке.
Обзор плазменной резки Плазменная резка — это процесс изготовления металла, в котором используются ионизированные газы, нагретые до температуры выше 20 000 0 C, для плавления металлических материалов. Этот газ, выбрасываемый под высоким давлением, расплавляет материал и удаляет его из разреза.
Важно отметить, что этот процесс работает только с электропроводящими материалами, такими как нержавеющая сталь, медь, алюминий и другие металлы. Другими словами, плазменная резка не может резать камень, бумагу, стекло и другие плохие проводники электричества.
Этот метод не имеет себе равных по экономичности, когда речь идет о резке толстых металлов. Кроме того, он универсален и требует низких затрат на обслуживание инструмента. Он также обладает высокой точностью резки, что делает его идеальным для резки деталей со сложной геометрией.
Кратко познакомившись с тем, что такое плазменная резка, давайте узнаем немного об ее истории.
История плазменной резки Процесс плазменной резки существует с 1957 года. Он начался как расширение процесса GTAW (дуговая сварка вольфрамовым электродом). Первоначально его основным применением была резка стальных и алюминиевых пластин толщиной от половины дюйма до шести дюймов.
Плазменные резаки, использовавшиеся в ту эпоху, были непредсказуемы и не обладали точностью, присущей современным резакам. Кроме того, используемые электроды и сопла быстро выходили из строя из-за воздействия тепла во время процесса. Замена сопла и электродов часто делала плазменную резку в то время дорогой.
Конец 1960-хОднако в конце 1960-х и начале 1970-х годов в этой технике произошел прорыв, когда инженеры создали двухпоточную горелку. Этот резак помог увеличить срок службы электродов и сопел, а также повысить качество и точность резки.
1970-е годыИнженеры использовали 1970-е годы для контроля паров и дыма, первоначально возникающих в процессе резки, с помощью водяного глушителя и стола. Они также разработали более совершенные сопла, которые помогли повысить точность дуги, предоставив операторам и машинистам возможность тонкой настройки.
1980-е 1980-е годы были периодом экспериментов для инженеров, когда они разработали и внедрили несколько новых функций. Эти функции включают плазменные резаки на основе кислорода и обеспечивают лучший контроль резки за счет различных уровней мощности. Они также сосредоточились на портативности блока плазменной резки, сделав его более эргономичным.
К 1990-м годам плазменные резаки высокого разрешения появились на рынке благодаря использованию долговечных кислородных процессов. Эти долговечные кислородные процессы в сочетании с новой системой сопел дали плазменным резакам той эпохи возможность в четыре раза увеличить плотность энергии по сравнению с предыдущими периодами.
С 1990-х годов по сегодняшний день в центре внимания инженеров находятся варианты питания и управления, а также повышение эффективности. Они также повысили точность плазменных резаков: сегодня модели предлагают более острые края и точные разрезы. Портативность и автоматизация — другие аспекты плазменного резака, которые инженеры значительно улучшили по мере того, как в обращении появилось больше портативных устройств.
Теперь, когда мы знаем, как развивалась плазменная резка, как она работает?
Как работает плазменная резкаВ процессе плазменной резки используется тепло для плавления металла вместо механической резки. Плазменные резаки работают, посылая электрическую дугу через газ. Затем этот газ проходит через суженное отверстие (сопло). Ограниченное отверстие заставляет газы проталкиваться через него с высокой скоростью, образуя плазму. Резка заготовки влечет за собой контакт режущего наконечника плазменного резака с заготовкой. Также обратите внимание, что из-за проводимости плазмы необходимо соединить заготовку с землей через режущий стол.
Не все системы плазменной резки работают одинаково. Однако существует три типа процессов резки.
Три типа процесса резки- Высокочастотный контакт : Это малобюджетная форма. Также из-за риска помех современному оборудованию из-за его высокой частоты этот процесс недоступен для плазменных резаков с ЧПУ.
Высокочастотная контактная резка включает использование высокочастотной искры и высокого напряжения — искра образуется, когда плазменная горелка соприкасается с разрезаемым металлом. Контакт замыкает цепь, инициирует искру и создает плазму, используемую для резки.
- Пилотная дуга: В этом процессе резки искра возникает внутри резака за счет комбинации слаботочной цепи и высокого напряжения. Эта искра способствует созданию вспомогательной дуги, небольшого количества плазмы. При соприкосновении с заготовкой плазменный резак создает режущую дугу, которая позволяет машинисту или оператору начать процесс резки.
- Подпружиненная головка плазменной горелки: Чтобы создать короткое замыкание, операторы прижимают резак к заготовке. При возникновении короткого замыкания начинает течь ток. Для создания вспомогательной дуги операторы сбрасывают давление.
Тип газа, используемого в процессе, зависит от метода резки, режущего материала и толщины. Помимо обеспечения формирования плазменной струи, используемый газ также должен способствовать удалению расплавленного материала и оксида из реза. Наиболее распространенные газы, используемые для плазменной резки, включают:
Аргон — инертный газ, и его плазменная дуга стабильна. Стабильность означает, что этот газ почти не реагирует с любым металлом при высоких температурах. Электроды и сопла, используемые для резки аргоном, часто имеют более длительный срок службы, чем те, которые используются с другими газами.
Газ аргон имеет ограничения при резке из-за его низкой плазменной дуги и энтальпии. Кроме того, при резке с использованием аргона в среде с защитой от аргона неизбежно возникнут проблемы со шлаком. Это в первую очередь связано с тем, что поверхностное натяжение расплавленного металла примерно на 30% выше, чем в азотной среде. Эти проблемы являются одной из причин, по которой аргон редко используется для плазменной резки.
Азот имеет лучшую стабильность плазменной дуги и более высокую энергию струи, чем аргон, особенно при более высоком напряжении питания. Кроме того, он образует минимальное количество шлака на нижних краях разреза даже при резке таких металлов, как сплавы на основе никеля и нержавеющая сталь с высокой вязкостью.
Газообразный азот работает как самостоятельный газ или в сочетании с другими газами. Это также облегчает высокоскоростную резку углеродистой стали.
ВоздухВоздух содержит 78 % азота и 21 % кислорода по объему, что делает его подходящим газом для плазменной резки. Кислородная составляющая воздуха делает его одним из самых быстрых газов, используемых при резке низкоуглеродистой стали. Кроме того, поскольку воздух повсюду, это экономичный газ для работы.
С другой стороны, электрод и сопло, используемые для этого процесса, обычно имеют короткий срок службы, что увеличивает затраты на резку и снижает эффективность. Кроме того, использование воздуха в качестве автономного газа проблематично, так как это приводит к зависанию шлака и снижению окисления.
Как и воздух, кислород увеличивает скорость резки низкоуглеродистой стали. Использование высокоэнергетической плазменной дуговой резки и высокой температуры кислорода увеличивает ее скорость. Однако для использования кислорода лучше всего сочетать его с электродами, устойчивыми к высоким температурам и окислению.
ВодородВодород часто используется в качестве вспомогательного газа для смешивания с другими газами для плазменной резки. Одной из наиболее распространенных комбинаций является водород и аргон, который производит один из самых мощных газов при плазменной резке.
Смешивание аргона с водородом значительно увеличивает напряжение дуги, энтальпию и режущую способность струи аргоновой плазмы. Режущая эффективность этой комбинации также увеличивается при сжатии струей воды.
При плазменной резке обычно используются несколько газов. В таблице ниже показаны эти газы, разрезаемые материалы и преимущества газа по отношению к материалу.
Толщина материала | Плазменный газ | Вторичный газ | Remark |
Structural Steel 0.5 to 8mm | Oxygen | Oxygen or oxygen/ nitrogen or nitrogen | Burr-free edges can tolerate square-ness, with smoothness akin to laser cutting |
Structural Steel 4 to 50 мм | Кислород | Кислород/азот или азот или воздух | Без заусенцев до 20 мм, поверхность разреза выглядит гладкой, допуск на прямоугольность до 25 мм, аналогично лазерной резке |
Высоколегированная сталь от 5 до 45 мм | Аргон/водород/азот | Азот или азот/водород | Без заусенцев до 20 мм, гладкие резы, плохая устойчивость к прямоугольности | Сжатый воздух | Азот или азот/водород | Резка без заусенцев, поверхность может быть шероховатой или зернистой, что позволяет выполнять почти вертикальную резку |
Алюминий от 5 до 40 мм | Аргон/водород/азот | Азот или азот/водород | Без заусенцев до 20 мм, зернистая или шероховатая поверхность, позволяет резать почти вертикально |
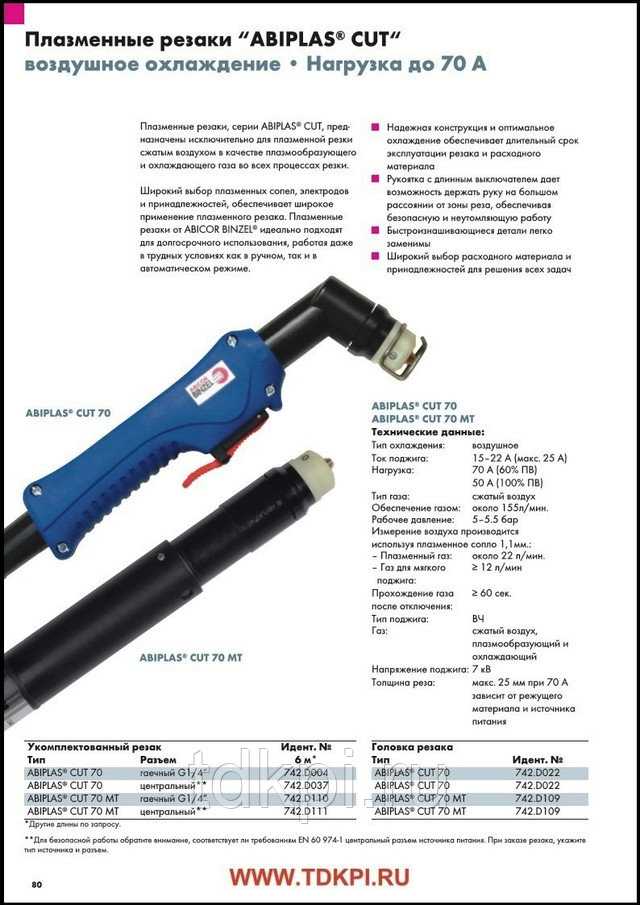
Алюминий обладает электропроводностью, что делает плазменную резку идеальным процессом для его изготовления. Кроме того, этот процесс дает преимущества при работе с более толстыми металлами по сравнению с другими методами изготовления алюминия, такими как лазерная резка. Он может резать алюминий толщиной до 160 мм.
Кроме того, производство алюминия с помощью плазменной резки более рентабельно из-за более низких эксплуатационных расходов и затрат на оборудование.
Мягкая стальМягкая сталь — это тип стали с низким содержанием углерода, обычно не более 2,1%. Это одна из наиболее часто используемых форм стали из-за ее свойств, которые подходят для многих целей. Кроме того, мягкая сталь недорога в приобретении, и ее свойства, такие как высокая ударная вязкость, свариваемость и пластичность.
Нержавеющая сталь Нержавеющая сталь представляет собой сплав железа, устойчивый к коррозии и ржавчине. Плазменная резка является одним из наиболее эффективных способов изготовления этого металла, так как позволяет получить толщину реза до 30 мм. Марки нержавеющей стали, идеально подходящие для резки, включают: 304, 304L, 316, 316L, 321, 310S, 317 и т. д.
Латунь — еще один металл, который легко изготавливается с помощью плазменной резки. Это связано с его высокой проводимостью. Однако при изготовлении латуни этим методом лучше всего это делать в хорошо проветриваемых помещениях. Это связано с тем, что латунь содержит цинк, а вдыхание паров, содержащих горящий цинк, вредно для здоровья.
Медь Медь обладает тепло- и электропроводностью всех материалов, кроме драгоценных металлов. Важные качества этого металла включают в себя; коррозионная стойкость, высокая пластичность и свариваемость. Эти свойства, в том числе высокая проводимость, делают медь идеальным металлом для плазменной резки. Однако, как и латунь, этот металл важно резать в местах с хорошей вентиляцией.
Этот металл популярен благодаря своей низкой стоимости и пластичности. В незначительных количествах он содержит такие элементы, как марганец, сера, фосфор и кремний. Чугун обладает высокой электропроводностью, высокой прочностью на сжатие и низкой температурой плавления, что делает его идеальным для плазменной резки.
Преимущества плазменной резкиСуществует несколько преимуществ использования плазменной резки для изготовления металлов по сравнению с другими методами, начиная от экономической эффективности и заканчивая более высокой производительностью и лучшим качеством резки. Вот некоторые другие преимущества.
Высокое качество резки По сравнению с другими процессами обработки металлов, такими как газовая резка или гидроабразивная резка , резка плазменными резаками обеспечивает более высокое качество резки металлов. Это связано с отсутствием остаточной накипи на кромке реза металла и меньшей площадью околошовной зоны.
Этот процесс позволяет резать любой металл, проводящий электричество, что делает его очень универсальным. Он может легко резать такие металлы, как алюминий и высоколегированную сталь средней и большой толщины. Он отлично подходит для нарезания канавок, строгания или маркировки металлов. Кроме того, этот процесс позволяет резать металлы в воде с пониженным уровнем шума.
Высокая скоростьПлазменная резка в 100 раз быстрее, чем лазерная резка, и примерно в 10 раз быстрее, чем газокислородная резка. Другими словами, он повышает производительность и сокращает время, затрачиваемое на изготовление металла, по сравнению с другими методами.
Более высокая точность и воспроизводимость Вырезанные детали имеют более высокую точность и качество поверхности благодаря нагреву в процессе. Кроме того, скорость изготовления улучшает воспроизводимость при одновременном сокращении времени, затрачиваемого на механическую обработку металлов.
Вы хотите производить металл с помощью плазменной резки? Зачем подвергать себя риску, связанному с процессом, если вы можете передать его более умелым рукам, таким как RapidDirect? RapidDirect — одна из лучших компаний по плазменной резке в мире, предлагающая широкий спектр услуги плазменной резки . Наши передовые плазменные резаки могут резать широкий спектр металлов толщиной до 15 мм.
Компания RapidDirect гордится тем, что производит детали для плазменной резки с высокой точностью и постоянством, используемые в различных отраслях промышленности. Итак, зачем ждать? Свяжитесь с RapidDirect, чтобы получить детали для плазменной резки уже сегодня.
Попробуйте RapidDirect прямо сейчас!
Вся информация и загрузки защищены и конфиденциальны.
Недостатки плазменной резкиХотя обработка металлов с помощью плазменной резки имеет множество преимуществ, существуют и недостатки.
- Режет только токопроводящие материалы
- Не идеально подходит для толщины более 150 мм
- Яркие вспышки, возникающие во время процесса, могут отрицательно повлиять на глаза человека с расходными материалами с малым сроком службы, такими как сопло и электрод
Плазменная резка — это процесс, который включает использование четвертой стадии материала для резки проводящих металлов.